-
{"cz":"Info EDUARD"}
{"cz":"Měsíčník o historii a plastikovém modelářství.","en":"Monthly magazine about history and scale plastic modeling."}
03/2023
Good day, Ladies and Gentlemen, We’re closed. Although you are certainly able to view and study our March release listing within these pages or at our e-shop, any purchases will have to be postponed. I understand that this sounds a little nuts, but it is not the result of some underhanded marketing ploy. It is a function of the fact that we are moving our entire retail department. It is also the reason why no sales will be going through our e-shop for the next seven days. As you will have probably already noted, the new items were available for early purchase from last Friday, and they will be available from our retail partners as well.
Page 1
INFO Eduard# 157e-magazine FREE Vol 22 March 2023Page 2
INFO Eduard# 157e-magazine FREE Vol 22 March 2023© Eduard - Model Accessories, 2023FREE FOR DOWNLOAD, FREE FOR DISTRIBUTION!This material may only be used for personal use. No part of the textor graphic presentations can be used in another publication in any other mediaform or otherwise distributed without the prior writtenpermission of Eduard - Model Accessories and authors involved.Editorial and Graphics - Marketing department, Eduard - Model Accessories, Ltd.Page 3
eduardeduardMARCH 2023CONTENTSEDITORIALKITSBRASSINPHOTO-ETCHED SETSBIG EDBUILTON APPROACH–April 2023TAIL END CHARLIEHISTORYEVENTBOXART STORYSpitfire Mk.Vc TROP 1/48Bf 109E-4 1/72GUADALCANAL DUAL COMBO 1/48Bf 110G-2 1/72MiG-21bis 1/48 Re-releaseAvia B.534 IV. serie 1/48 Re-releaseFw 190 A-8/R2 1/48Bf 109G-6 1/48Buccaneer S.2C/D 1/48Fw 190A-4 1/48Fw 190D-9 1/48The Cavalry Arrives - VMF-223 at GuadalcanalThe air war over UkraineBack to NurembergThe Maltese FalconStukas under fighter commandWasps over the bayVirtue out of necessityThe Calm Before the StormGuardians482026405674808694111Published by Eduard-Model Accessories, spol. s.r.o.Mírová 170, Obrnice 435 21support@eduard.com www.eduard.comPage 4
EDITORIALGood day, Ladies and Gentlemen,We’re closed. Although you are certainlyable to view and study our March releaselisting within these pages or at our e-shop,any purchases will have to be postponed.I understand that this sounds a little nuts,but it is not the result of some underhandedmarketing ploy. It is a function of the fact thatwe are moving our entire retail department. Itis also the reason why no sales will be goingthrough our e-shop for the next seven days.As you will have probably already noted, thenew items were available for early purchasefrom last Friday, and they will be availablefrom our retail partners as well.The move is being made from within the cityof Most, where we suffered our fire claiminga lot of our plastic some two years and threemonths back, to a facility which we purchasedjust outside of the city last year and havebeen renovating for our needs. The village iscalled Sedlec, and borders an industrial parkthat houses, for example, a former brewery.That has long since been relocated. Our newfacility is located about 4km from our headoffice in Obrnice. Our renovation is beingdone in steps. In January, immediately aheadof our departure for Nuremberg, we movedall of our plastic to the new facility which wecall ‘the Barn’, but is officially labeled as ‘HallNo.2’. The relocation of the retail departmentis the second phase, and the third will be themove of the tool and press shops. This willinclude our design offices that fall underkit production. If everything goes as it hasbeen up to now, that third phase should becomplete by the end of the year. On the onehand, it complicates our life quite a bit, thethird phase being the most complicated. Themove of the heavy equipment will be the mostlogistically ambitious activity Eduard has everembarked upon. It will also likely have animpact on the meeting of release schedulesfor the beginning of the year. This will mostlycentre around the 48th scale S-199, but therewill be a negative push against other projectssuch as the MiG-21F. But, there is the otherhand, too, that will open up a more effectiveworkspace for us, and not just with respectto the production of kits. The move will beto the benefit of the Brassin departmentas well, because the space freed up on themain floor of the main building in Obrnicewill be allocated to them. This will give themsomewhere between 6400 and 6500 squarefeet, and that will house their printers andother pieces of equipment very nicely!This is all still in the relatively distant future.And you know how plans are. They havean awe-inspiring ability to not go the waythey’re supposed to, they have an ability tofail, and so on. At the moment, it’s the retaildepartment’s turn to move on up, and webegan this today. We moved all the furnitureand the IT equipment and tomorrow we’llpick up with packing up stock items fromthe shelves and the latter’s disassembly. So,keep your fingers crossed and please, bepatient. If everything goes according to thoseaforementioned plans, we should be open forbusiness again next Wednesday. If you needanything from us, you can still write. We willbe on-line and answering questions. Justbear in mind that we will be rather busy andthere may be a delay in our responses fora short while.NurembergThe Nuremberg Toy Fair was different thisyear. From the point of view of our industry,it’s pretty simple to describe. It was small.All in all, there were six manufacturersrepresented: us, Special Hobby, Italeri,Airfix, Revell and Tamiya. There were somecolleagues that produce accessory itemspresent, AK Interactive, Vallejo, and Art Scale,which is also a retailer, but they do producesome masks and decals, along with somecutting saws. And that’s it. Beyond that…crickets. There was Zvezda, but they werein a bit of an undercover mode in an office inthe service centre. In proportion to the newconditions, our table space was reduced andshared with Special Hobby. Retailers andjournalists were fewer as well, and notableabsences were Asian and American. But, itwasn’t as bleak as I am perhaps making it outto sound. There were fewer of us, but therewas correspondingly more time for things.The discussions were not mechanicallygeared to business and there was a pleasant,friendly feel to it. There was also moregeneral ‘chatter’, if you like. All in all, it wasan interesting experience and I am happy forit. The atmosphere at this year’s NurembergToy Fair reminded me of the old Chicago showRICHTA because, among other reasons, ourexhibition hall at Nuremberg was, apparentlyfor the first time, open to kids, and kids came!There were no Scout troops in attendance likein Chicago, but it was nice to see, regardless ifit was because of the recent crisis or a simpleorganizational decision. It was a change andchange is good. It wasn’t a revolution, but itwas a step forward within the bounds ofreason, and that is, in my estimation, thebest way to move forward. Ultimately, whatbothered me the most was the cold in theexhibition venue, and the stall that soldsteaks on a bun that was closed. That wasprobably my greatest piece of enjoyment thatI looked forward to. I will need to find anotherlittle gem to look forward to, and I am worriedthat this one will be tough to replace!Don’t fret too much if these little philosophicalmusings don’t give you all that much.A dedicated, in depth look at Nurembergfollows in the pages of this newsletter edition.New Releases for March – KitsOf all of our new releases, which total 86 thismonth, modellers most gravitate to new kits.This month, there is nothing that is super new,there is no kit taking a bow for its premiere,but even so, it is an interesting mix of scalesand aircraft from various periods in history.INFO Eduard4March 2023Page 5
One is dedicated to the pivotal battle duringthe Second World War that was Guadalcanaland contains the F4F-4 in two developmentconfigurations from that period. At the time,naval fighters were not particularly striking inappearance on either of the opposing sides,but in my view, we were able to come out withan attractive mix of interesting aircraft thatare accompanied by, to the contrary, rivetingstories. Among them is a Wildcat that wasflown by ‘Pug’ Southerland in a legendaryfight with Saburo Sakai. This event wasalready once depicted on the boxart for one ofour A6M2 releases. Other scheme options areprovided for Wildcats that were brought to theforefront by pilots such as Joe Foss, StanleyVejtasa and Donald Runyon. There is a total oftwelve of these options, and the kit containstwo complete sets of plastic for versions ofthe Wildcat that marginally differed from oneanother. Truth be told, the differences onlyconcern the fuselages, but they are there andyou need to be aware of them. If these setsof plastic aren’t enough for you, we also havethe Overtrees options. And while still on theWildcats over Guadalcanal theme, we have anarticle penned by Tom Cleaver in this issue ofthe newsletter.The Second World War is our main focus ofattention when it comes to kit productionand our range reflects this. The 1:72 scale Bf109E-4 in the ProfiPACK line is generally, butnot exclusively, about the Battle of Britain,while the Spitfire Mk.Vc Trop deals with thelater battles over the Mediterranean, NorthAfrica and Southeast Asia. It representsaircraft equipped with the tropical filter,either the Vokes or Aboukir types, and themarkings are anything but boring. We haveBritish, South African, Australian, Americanand even a Yugoslavian Spitfire. We did makea subtle change to the design of this kit withthe addition of the wingtips that were typicalfor aircraft equipped with the Aboukir unit.I also consider the boxart for this kit ratherunique, and what is interesting about it, aswell as with our other boxarts this month, isdetailed in the Boxart Stories sections of thenewsletter.The Second World War theme is alsoexpressed in the only Weekend kit release forMarch. Following on the heels of November’sBf 110G-4, we have the Bf 110G-2 for March.In terms of camouflage schemes, this kit isno slouch either, but what sets this kit apartare the weapons options, and is different foreach of the four marking options offered. Wewaited just shy of two years for the returnto our range of the Bf 110 in the two mainscales of 1:48 and 1:72. It was even longerfor the Avia B.534. That one makes its returnin the form of the B.534 IV Series in theProfiPACK line. We should also manage toput out the B.534 III Series, and in the originalboxes. Also being reissued in March is theMiG-21bis, also in the ProfiPACK line.New Releases for March – AccessoryItemsOf the 86 aforementioned new releases forthe month, eighty of them fall under variousaccessory labels. Among them are some veryinteresting little items, often even unique, thatprovide a hint of the future. Among these, forexample, is the cockpit for the 1:48 Mi-24V/Mi-35 in black form, which carries in its namePRINT & SPACE. This means that it is made asa 3D print with a small number of cast items,complemented by an instrument panel andother details made using 3D technology of theSPACE line. In April, we will release a set forthe older and more traditional green version,common to Soviet era aircraft. I think that thiscombination is a fairly interesting concept,and with the advantages and features thatit offers, will pique the curiosity of manymodellers. For accessory items for modelaircraft, this really is a new age, offering newopportunities and possibilities for improvingyour models, and certainly deserves a testdrive at the very least. The colour sets includea small 3D printed item covering the ejectionseat handle for the F-16A from Kinetic, also in1:48 scale. The set is called ACES II EjectionSeat Lower Handles PRINT 1/48 and it reallyis as noteworthy as it is small. If it does getnoticed, and becomes popular, it will openthe door for further development of thetechnology. Printed engines are falling intothe realm of classic items, and are offered forthe F-4F-4 Wildcat, along with a wheel wellset for the same type and scale, and yes, forthe Eduard kit in general, and for the abovementioned Guadalcanal item in particular. Iwould also like to turn your attention to theset of guns for the Beaufort Mk.I, which arebeautifully and finely printed items as well.The collection also includes other interestingtypes of accessories. These cover, forexample, the HKM B-25J in 1:48, in the formof masks, photoetched brass and SPACEsets, and the same can be said of the setsfor the Revell B-24D Liberator and theF-16A MLU from Kinetic. A large collection ofphotoetched sets are designed for the ZvezdaC-130J Hercules. So far, we have masks and aSpace set for Zvezda’s Mi-8MT, while masks,photoetched and SPACE items are availablefor the 1:32 scale Hurricane from Revell andSpitfire Mk.IXc from Airfix. The latter, though,is in the bigger scale of 1:24. There is a mixof accessory items for Tamiya’s beautifulF-35A and, besides the wheels, I would pointout the extensive masks for the RAM panelson the surface of Japanese and Americanaircraft which the kit offers as part of its eightmarking options. Similar, but correspondinglysimpler versions of these masks for theremaining marking options of the kit havebeen available since last month. These masksare produced using a different material fromthe one used in our canopy sets. Besides theadvantages that this material offers for thistype of application, they also differ in theirblack colour. With these two sets, we makea return to masks designed for camouflageschemes, national insignias and markingdetails. It’s not a one-off project, and we willcontinue with these sets primarily for kits ofour own production. For the F-35A, we alsohave a BiGSin set of weapons.Of the increasingly popular SPACE line, wehave eight new items for March. I wouldalso like to point out two 3D printed sets for1:35 scale AFVs, and also the new LooK andLookPlus items.ArticlesBesides the articles already mentionedabove, we have the next installment of theWar Over Ukraine feature from Mira Maric.February 24th marked the first anniversaryof the Russian attack on Ukraine. It camewith a realization that we have ahead of usmany months, if not years, of bloody fighting,the horrors of war and general gloom anddoom. Regardless of how long it takes, it willend, and it must end if the world is to surviveand maintain the values on which it stands.That means the defeat of Russia. After all, theRussians are working at it through their owntenacity.With the use of four formerly Czech Hindsby Ukraine, we have a connection, albeita loose one, to Tomas Dvorak’s article coveringthe Mi-24/Mi-35 that takes a look at not justthe technical details of these aircraft, butalso examines the interesting circumstancessurrounding their acquisition byCzechoslovakia, and later deliveries to theCzech Air Force. This is an article that, althoughit is very detailed, it remains very easy to readand has a good continuity. It may not appearyet in the English translation of the newsletter.The last of today’s articles deals with thesad news of the passing of Petr Samal onJanuary 31, after a long illness. He led a ringof modellers that brought kids into the hobbyand was also the head of the builders’ sectionof the SMCzR. Memories are offered by FredyRiedel and Milan Mikulecký, and I think backon Petr fondly.Happy Modelling!Vladimir SulcINFO Eduard5March 2023Page 6
MemoriesPetr ŠámalofOn Tuesday, January 31, I was sitting with Jan Zdiarsky from Eduardin a restaurant near our hotel in Nuremberg. I was enjoying dinnerand relaxing after a busy day, full of preparations of the stand at thefair. However, this relaxed mood was swept away by the news thathit me hard. Petr Šámal has died. He hadn’t been in good health forsome time, but according to the reports I was getting, he had startedto improve. So, it came like a bolt from the blue. After Petr Dousekand Radek Pavlíček, another great friend of mine had passed away ...by Alfred RiedelI met Peter sometime in late 1990 or earlythe following year. We were introducedby a mutual friend, my classmate PetrŠobíšek, at a model exhibition organizedby the plastic model club Albatros. Wegot along in many things with “Šámi”,as we called him. Plastic modeling andinterest in history were of course twoof them. “Šámi” had knowledge as wellas copious archives and was, like us,kind of “patient”. We became members ofAlbatros club and “Šami” became a bit ofa mentor to us. After all, he was a bit older.Unlike me, a student at the time, and PetrŠobíšek, who was serving the alternativecivilian service, “Šámi” was alreadymaking money and owned a car. Two yearslater, I started working at one MPM modelshop in Prague while Petr Šobíšek wasworking at another MPM shop in a differentPrague location. Thanks to his work atPrague Energy company (PRE), “Šámi”kept moving around Prague and veryoften stopped by one or the other store.A group of colleagues and their friendsformed around both shops and “Šámi” wasan important member of this group. At thattime, he got a studio apartment in Písnice,so our group had a place to meet. TodayI wouldn’t probably survive such lavishparties as those held there back then …We travelled together not only to attendmodel competitions, but also to do varioustrips including mountaineering. “Šámi”with his guitar, which he played with greatskill, often took care of the entertainment.In fact, music was his other great hobby.Besides playing the instrument, he alsocollected records and his knowledgeof good music was astounding.But time passed, “Šámi” settled down,got married, had a daughter and latera son. His son was born just a few monthsbefore mine. So, we would occasionallymeet up with our families, usually ata modeling contest. Unlike “Šámi”, whowas still working at PRE, I left MPM toeventually return to Special Hobby. So,I was also seeing “Šámi” professionally,because in the meantime he had becomethe chairman of the plastic modelingsection of SMČR (Modelers associationof Czech Republic) and was dealingwith sponsorship issues. He took overthe plastic model section in quite a badshape, but thanks to his dedication,organizational skills and knowledge,the functioning of it has changed for themuch better. At the same time, he led thechildren model club in Písnice and raisedmany new modelers. He took care of thechildren like a little grumpy, but verycaring babysitter. Unfortunately, he didnot take similar care of his health, whichhad fatal consequences. “Šámi” left toosoon. I miss him.INFO Eduard6March 2023Page 7
Whenever someone passes away, every-body tends to remember them in a goodway. In the case of Petr Šámal, it’s easyfor me, I really experienced him only ina good way. And I think that everyone whoknew him in connection with his passion –plastic modelling – has it the same.by Milan MikuleckýI admit that I am not worth much asa modeler, the last time I finished a kitwas some thirty-five years ago. When mychildren got to the age when it was timeto start developing their fine motor skills,I had to admit self-critically that theywould acquire rather negative habitsunder my guidance. Therefore, I calledVladimír Šulc from Eduard, saying thatI would like to hire a modeler for mychildren who would introduce them tomodeling in the twenty-first century. AndVladimír gave me the phone number ofPetr Šámal, saying he runs a modelingclub in Písnice near Prague. That’s howI first met Peter.What surprised me there? First of all, thenumber of children attending the club.And then that even though today’s childrenhave a different attitude to authoritythan we had, Petr and his colleaguesmanaged to “discipline” them without anysevere means. And most importantly,that even for teenagers, Peter was anunquestionable authority. I understoodthat running a modeling club is not justabout building the kits, but also aboutweekends spent at modeling contests,looking for sponsors or negotiating withthe owners of the premises where theclub operates. Petr was the soul and theengine of it all. But it didn’t stop there,as Petr also organized trips to variousmuseums. Once I had an opportunity to gowith them, it was the trip from Točná tothe Military Technical Museum in Lešany.A driver for the historic Dodge WC 52,which was to take us to the museum andback, send us a last-minute apology. Well,it was Petr who got behind the wheel, andhe bravely tackled driving a car withouta synchronized gearbox and many otherconveniences of modern cars.Peter, besides aircraft built in variousscales, also liked the real ones. Hehimself used to fly in the Točná Aero Club,and when I offered him the opportunity togo flying, he did not refuse. Although a lotof time had passed since he himself hadbeen a student pilot of Blaník glider, it wasclear that he still had a feeling for flying.When he took over the controls, I did nothave the slightest urge to correct hispiloting in any way. We had the opportunityto fly together a Stearman, a Zlin C-305 ora Cessna C 180 in bush flying modification.Peter then surprised me, because he hadbought each of these aircraft as a model,with the intention of building them in theexact livery we flew together. I don’t knowwhether he managed to realize his plan,the illness he eventually lost the battle forhis life with came rather quickly (at leastfor me, as Peter didn’t talk much about histroubles) and in a form that caused himto be hospitalized in addition to the pain.I admit that we will all remember himas a tireless organizer with his typicalsmile. As a man who never refused helpto anyone who asked for it.I have three children myself and I knowhow challenging it is to take care of them,to teach them something and to anticipateeverything they might think of. That’s whyI have lot of respect and awe for peoplewho are spending time and lot of effortwith children who might be strangersto them in addition to their own. Peterwas one of them. He led them to a loveof history, to patience, and taught thema whole range of skills that neither schoolnor their family could provide. All this inhis spare time and with no expectationof remuneration. In today’s performance,money and success driven world, he wasalmost a person from another time. Peter,we’re gonna miss you here.INFO Eduard7March 2023Page 8
HISTORYThe sky over the Coral Sea was a deepblue with a few clouds on the morning ofAugust 20, 1942, when a 14th Air GroupH6K Mavis operating from the advancepatrol base in the Shortland Islands begantracking a cruiser and two destroyersat 1020 hours, transmitting news of thesighting. At 1130, the Mavis reported thethree warships were escorting an aircraftcarrier when it sighted the auxiliaryaircraft carrier USS Long Island (ACV-1),her deck loaded with aircraft. When themessage from the Mavis revealing thepresence of Long Island was receivedby Combined Fleet headquarters at Truk,Japanese commanders were elated, butthey missed the significance of the carrierthe Mavis had sighted, since they knewnothing of the existence of U.S. “auxiliarycarriers.” To Admiral Yamamoto’s staff,it appeared Long Island was stalkingAdmiral Tanaka’s slow ReinforcementGroup, which was steaming steadilytoward Guadalcanal since departingTruk in two forces on August 16 and17. Long Island was beyond the range ofany Japanese strike aircraft, but Tanaka’sfleet was in range of the unidentifiedAmerican carrier. Vice Admiral NishizōTsukahara ordered Tanaka to turn awayfrom Guadalcanal and turn directlytoward Rabaul. If the Americans knewwhere he was, they might chase him andin so doing come within range of the 5thAir Attack Force’s Bettys.At 1340 hours, Yamamoto’s headquartersreceived a message from the Mavis inthe next search sector over from first,reporting the presence of a secondaircraft carrier and several surfaceescorts; in fact, this was Long Islandand her escorts. The big flying boat wasThe Grumman F4F-4 Wildcat was the most significantfighter aircraft deployed in the fightings for Guadalca-nal. VMF-223 pilots were the first to land these aircraftat Henderson Field.Text: Thomas McKelvey CleaverThree prominent pilots of the first phase of aerial combat over Guadalcanal: Maj. John L. Smith, commander of VMF-223,Lt. Col. Richard Mangrum, commander of VMSB-232 and Capt. Marion E. Carl, XO of VMF-223.Photo: Naval History and Heritage CommandINFO Eduard8March 2023Page 9
unnoticed by any American radars andeased within 40 miles of the carrier as itcontinued tracking her course.At 1400 hours Long Island reached herlaunch point off the tip of San CristobalIsland, 200 miles south of Guadalcanal.The strange-looking ship had begun lifeon January 11, 1940, as the C-3 cargoliner Mormacmail. Taken over by theNavy March 6, 1941, she had emergedfrom the yards with her superstructureremoved and replaced by a 362-foot flightdeck, becoming the first of a new classof aircraft carrier – Auxiliary EscortCarriers – which would over the next fewyears become the most numerous classof aircraft carriers in the world, by thenknown as CVEs, which their crews wouldclaim stood for “combustible, vulnerableand expendable.” Long Island’s captain,Commander Donald Duncan, ordered fullspeed ahead. Black smoke poured fromthe horizontal funnels on her starboardside as Long Island’s single diesel enginestrained to bring the ship to her maximumspeed of 16.5 knots – half that of a fleetcarrier.For Long Island and her precious cargo ofF4F-4 Wildcats of VMF-223 and SBD-3s ofVMSB-232, this was their second attemptto get to Guadalcanal. After less thana month in preparation followingnotification on July 5 that they weredeploying to the South Pacific, the pilotsand gunners had packed themselvesaboard the little carrier in Pearl Harboron August 2 and Long Island set sailunescorted into the great unknown ofthe war-torn Pacific. Their ground crewsand other key personnel from MAG-23,and all the necessary ordnance, fuel, andsupplies needed to begin air operationsdeparted separately aboard the transportWilliam Ward Burroughs.On August 9, 1942, completely unaware ofconditions on Guadalcanal, Long Islandhad neared her launch point when CaptainDuncan learned of disaster suffered inthe Battle of Savo Island the night before.Duncan turned around and headed forthe American base at Suva, Fiji, to awaitclearance to launch his cargo of preciousaircraft and pilots. Upon arrival, heinformed Admiral Robert Ghormley thatmost of the pilots were too green to becommitted to combat. Ghormley buckedthe matter to Admiral McCain, who orderedeight more experienced pilots transferredto VMF-223 from the well-trained butunbloodied Vila-based VMF-212, whichwould take 223's least-experienced pilotsin trade and train them further. On August14, Long Island departed Suva for Efate tomake the swap, but the VMF-212 pilots didnot come aboard until the day before theship departed for Guadalcanal on August18.To Guadalcanal!On the way out from Pearl, the Marineshad worried about getting off the carrierwhile in the Pacific “doldrums” wherethere was no wind over the deck. DickMangrum recalled “we had no idea howfar south this equatorial condition wouldbe found, and considered ourselvesfortunate to discover our destinationwas far enough south to be well awayfrom this situation.” With the southeasttradewind adding another 10 knots to thebreeze over the flight deck, the crews inthe 12 new SBD-3 Dauntless dive bomberschecked the gear and equipment – sparkplugs, starter cartridges, tool kits, evenspare tires – they had stuffed in theircockpits the night before to supportthemselves for the two weeks they wouldbe on their own before their ground crewsarrived. The squadron was six airplanesshort of its authorized strength becausethese 12 had been the only Dauntlessesavailable in the Ford Island fleet poolwhen Mangrum learned of their comingdeployment. Each Dauntless carrieda 500-pound bomb to supplement thesmall supply on Guadalcanal. According toMangrum, “receiving orders to bomb-upour airplanes was an eye-opener tojust how difficult things were wherewe were going.” Second LieutenantEugene Trowbridge noted in his offically-illegal diary (that he kept regardless):“A lot of excitement today as there areenemy subs all around, and today we getthe new experience of being catapultedfrom the ship as the flight deck is too shortto fly off. We are all set to leave. Engineswarm and tested, baggage all secured,everything all set. Finally, we’re off.”T he f ligh t dec k crew p ush ed the f irs t bom berinto position. Bombing-232’s skipper,Major Richard. H. Mangrum’s 12 years asa fighter and bomber pilot and 3,000 flyinghours, made him the most experiencedof all 31 pilots in the two squadrons.Mangrum later recalled that “Our launchwas delayed to the afternoon since theJapanese visited Guadalcanal at mid-day,and thus, arriving later, we were less likelyto get an unfriendly reception from ourfellow Marines.”Two minutes later, 2nd LieutenantLawrence Baldinus, a Polish expatriateand former Marine enlisted pilot who hadbeen commissioned after Pearl HarborHISTORY“Receiving orders to bomb-up our airplanes was aneye-opener to just how difficult things were wherewe were going.”(LtCol Richard Mangrum; VMSB-232)Captain USS Long Island, Commander Donald B. Duncan, on the deck of his ship while at anchor in Norfolk,Virginia, October 26, 1941. Note the installation of a makeshift mast.Photo: Naval History and Heritage CommandINFO Eduard9March 2023Page 10
and was the most experienced pilot in thesquadron after Mangrum, stood on hisbrakes and ran up his engine, then soaredup to join his leader. Second LieutenantHenry “Hank” Hise, a 22-year-old Texanwho had graduated from flight school theprevious May with a shade over 200 hoursin his logbook, maneuvered his scoutbomber on the deck as the crew hookedthe airplane to the catapult. He and theother nine “nuggets” had never seena Dauntless before they reported to thesquadron in late June. A minute later, theforce of the catapult caused LieutenantHise to forcibly pull back on his joystick,pulling the Dauntless’s nose high enoughto nearly stall. He quickly jammed the stickforward and fought to keep the bomberout of the water. Regaining control, hejoined up on Mangrum and Baldinus.The first of the 19 blue-grey F4F-4Wildcat fighters was pushed into positionon the catapult. Squadron commanderMajor John L. Smith made a last-minute check of his engine and controls.Extremely intelligent and able, he had ademonstrated ability to adapt quickly tochanged conditions; most who knew himsaid he often appeared to be in a bad mood.He had only flown fighters since a monthbefore the attack on Pearl Harbor andhad worked his young replacements hardsince the squadron had been informed,they were headed for the South Pacific.He had never trained other aviators andnever been in combat. Fortunately, hewas a superb natural fighter tactician,a confident innovator who hadpainstakingly trained his men to surviveagainst the otherwise unbeatable Zero.He later recalled those weeks spentworking to prepare his novices for theunknown rigors of combat: “We all had toqualify on an aircraft carrier, which we did.We spent as much time as we could flyingon Saturdays and Sundays and everyother day, doing gunnery and dummyruns and anything that would help to givepeople quick experience or quick training.It was the first experience that I’d ever hadtrying to train anybody, but it seemed tome that gunnery was the most importantthing, so we concentrated on gunnerymore than anything else, which wasa good thing after we found out where wewere going.”The F4F-4 Smith flew was unlike itspredecessor, the F4F-3; this Wildcatsported folding wings, allowing more ofthem to operate from an aircraft carrier.Armament was increased from four tosix .50-caliber machine guns, increasingthe weight of fire, though the ammunitionload remained the same which reducedtotal firing time by 14 seconds, an eternityin air combat. Most Wildcat pilots didnot see this as an improvement. Theweight of the additional guns and thefolding wings reduced the already-sluggish performance of the fightereven more. At Guadalcanal, the pilotswould need every bit of warning timethe coastwatchers could provide tostruggle up to 20,000 feet in time to bein position for an attack on the incomingJapanese.Smith was followed in quick successionby Captain Marion Carl, newly-promotedto Executive Officer, and fellow Midwayveteran Division Leaders CaptainsClayton Canfield and Roy Corry and theiryoung charges, who had an average of250 flying hours in their logbooks andwere eight weeks out of flight school.At 1455 hours, Yamamoto’s staff receiveda report from the second Mavis that thecarrier and its escorts were retiringsouth. Neither of the big flying boats hadseen the launch of Marine Air Group 23 toGuadalcanal.With the Marine aircraft launched, thevulnerable carrier reversed course andheaded out of range at full speed. The 31blue-grey airplanes headed north into thecloudy unknown.Two hours later, Guadalcanal hove intoview. While Smith’s Wildcats flew cover,the SBDs landed. Mangrum followeda ground-control jeep to the dispersalarea and jumped to the ground as soonas his plane's engine stopped. He hadhis hand wrung profusely by GeneralVandegrift, while thousands of thankfulMarines shouted themselves hoarse andpounded one another black and blue ina thundering release of emotion. Thecavalry had arrived.Lieutenant Gene Trowbridge later wrote inhis diary: “[We] sight the [air]field at 1600.We are really welcomed by the troopsas the Japs have been taking their timebombing them and they figure we will helpthem quite a lot. We are all bedded downfor the night and get ready for a nice sleepwhen, bang, the whole world seems toexplode. The Japs are coming and some oftheir cruisers and destroyers are shellingus and the troops. It was a trying firstnight. We are nervous and jumpy as thereare snipers all around us, just waiting forsomeone to stick [his] nose out.”HISTORYBefore taking off from the deck of the USS Long Island ...“It was a trying first night. We are nervous andjumpy as there are snipers all around us, justwaiting for someone to stick [his] nose out.”(2/Lt Eugene Arthur Trowbridge; VMF-223)Photo: Naval History and Heritage CommandINFO Eduard10March 2023Page 11
Invasion on a ShoestringOnce the Allied fleet had retreated fromthe Guadalcanal area following the defeatat Savo Island, the primary objective forthe abandoned Marines was getting thecaptured Japanese airfield on the Lungaplain operational as quickly as possible.Without air support, they were completelyat the mercy of Japanese aerial and navalattacks, and highly vulnerable to groundassault.Almost as soon as the runway had falleninto the hands of the 3rd Battalion, 5thMarines on August 8, the division air andengineering officers sized things up. Theyreported they could put down 2,600 feetof usable runway by August 10, and thatanother 1,200-by-160-foot section couldbe completed in the week after that.Rear Admiral Turner promised on August8 that aircraft would arrive on August 11.Unfortunately, when the fleet was forcedto retire following Savo Island, they leftwith nearly all the 1st Engineer Battalion’sequipment that had yet to be unloaded.Construction of the airfield commencedAugust 9 when the 1st Engineer and 1stPioneer battalions managed to gathersufficient gear to get started. A miserable15 percent of their equipment and supplieshad been landed, with none of the heavyequipment making it ashore. Thus, theywere forced to manhandle 100,000 cubicfeet of earth fill to cover the depressionin the center of the field that had beenleft by the Japanese, who had begun theirconstruction at both ends and built towardthe center.The engineers used a huge steel girderas a drag, while a captured Japaneseroad roller was used to pack the fill.Japanese gear contributed heavily to thesmall store of engineering equipmentavailable to the Americans, though ingeneral, the captured equipment wasin poor condition; ingenious Americanmechanics kept it working hour afterbrutal hour in their race against time. Theonly earth-moving equipment was oneangle-dozer the pioneers had managedto land. Dump trucks were nonexistent.The engineers performed incrediblefeats of improvisation as they overcamemonumental difficulties.On August 18, eight Betty bombers arrivedover Henderson in the largest air strikesince August 9 as the 25th Air Flotillabegan the aerial assault leading up tothe first Japanese effort to land troopsand retake the island. Forced to remainabove 25,000 feet by antiaircraft fire,the bombers did little harm. But it wasclear to all that the enemy was resumingHISTORYThe hangar of the USS Long Island with the Wildcats and Seagulls on June 17, 1942. All aircraft are from VGS-1.A month later, this ship was carrying VMF-223 towards Guadalcanal.The Henderson Field area as it looked shortly after the Marines captured it.Marines building a defensive line on the perimeter around Henderson Field.Photo: Naval History and Heritage Command Photo: Naval History and Heritage Command Photo: Naval History and Heritage CommandINFO Eduard11March 2023Page 12
HISTORYwork and would be back. As yet nothingstood in their path. A three-ship convoyfrom Noumea arrived after the Japanesedparted. The ships brought five days offood, which, along with captured Japaneseprovisions, gave the Marines a two-weekfood supply. To stretch the supplies as faras possible, the Marines were limited totwo meals per day.Henderson is ReadyOn August 19, CUB-1 and the 1st EngineerBattalion reported Henderson was fitto support air operations. The airfieldwas now 3,800-foot strip 150 feet wide,covered with gravel, with a dirt taxiwayand parking area destined to becomefields of mud in the many rainstorms. Theairfield was surrounded by a tenuouslyheld defensive line extending from PointCruz on the west to the Ilu River on theeast, leaving the field only a quarter milefrom a mile-long piece of high groundthat would come to be known in Marinehistory as “Bloody Ridge.” There wereno protective revetments and aircraftmaintenance would test Americaningenuity throughout their time on theisland. The only structure on the fieldwas a wooden tower the Japanese hadconstructed which became known as“The Pagoda.” Time Magazine reporterRobert Sherrod, who landed with theMarines, described living conditions atthe field as “appalling” with sleepingchoices limited to mud-floor tents ordugouts, with slit trenches close by.Malarial mosquitos were numerous. Thefliers would be issued Japanese mosquitonetting, something the “mud marines”could only hope for. The facilities werecrude, but Henderson Field was ready.It was just in time.Despite all the effort, Henderson Fieldcould barely be described as an airfield.It was an irregularly shaped blob cut outof the island growth, half in and half outof a coconut grove, with a runway thatwas too short and too few revetmentsto protect the aircraft from shrapnel.In mid-September, several weeks aftertheir arrival on the island, MAG-23 groupexecutive officer Lt. Colonel Charles Fikefinally wrote the August 20, 1942, entryin the group’s War Diary: “Upon arrival itwas found that a servicing detachmentof approximately 140 men, commandedby Ensign Polk, of CUB-1, were availablefor fueling, rearming, and servicingof aircraft. All fueling was done by meansof hand pumps directly from drums.Rearming was done without the aidof bomb-handling trucks, bomb carts,or bomb hoists. The enlisted menof CUB-l, although willing and intelligent,had, for the most part, less than fourmonths’ service, as a result of whichthey required the closest supervision.Considering the attending difficulties,Ensign Polk handled this situationremarkably well. His attitude was at alltimes cooperative.”To be continued...A major innovation in the F4F-4 version was the "So-Wing" folding system, designed by Leroy Grumman himself.Here, mechanics demonstrate the system’s space-saving capabilities on an aircraft belonging to VF-3 at NASKaneohe, Oahu, May 29, 1942.“We spent as much time as we could flying on Saturdaysand Sundays and every other day, doing gunnery anddummy runs and anything that would help to give peoplequick experience or quick training.”(Maj. John L. Smith, VMF-223)Wildcats on Guadalcanal in the fall of 1942. A group of B-17s is overflying Henderson Field.Photo: Naval History and Heritage CommandPhoto: Naval History and Heritage CommandINFO Eduard12March 2023Page 13
HISTORIE12. ročník modelářské soutěžePANTHERS CUPHlavní téma: KDYŽ HVĚZDY TANČÍKdy: 25. 3. 2023Kde: Novoborská 2, Praha 9Další informace: www.pantherscup.czať je tou vaší hvìzda smrti,britney spears neboinsignie americkéholetectva...pøijïte nám dokázat,že ta vaše je ta nejzáøivìjší!téma letošníhoPantherscupu jekdyž hvìzdy tanèí.Page 14
The new year started with so far, thelargest one-time loss on the Russianside The Russian command demonstratedthe great negligence when hundreds ofdrafted soldiers were concentrated in theunprotected and unreinforced buildingof the former high school in Makiivka inDonetsk region. All this regardless thefact that for several months the buildingexactly like this have been targets of thehighly efficient missiles fired from theHIMARS rocket launchers. On the top ofit, there was an ammunition dump in thebuilding basement and uncamouflagedvehicles parked around the building. Therewas no secret that the building housedhundreds of soldiers. The result wasa disaster at an unheard-of scale, evenby Russian standards. On the New Yearthe building was hit by rockets and thecarnage was topped by the explosion ofthe stored ammunition. The former schoolcompletely collapsed which is confirmedby videos published on the Russianchannels. According to the Ukrainian andWestern estimates between 300 and 400soldiers were killed. Even the RussianDepartment of Defense had to admit to theMakiivka attack. Otherwise, it covers upthe Russian own losses. It was announcedthat 89 soldiers perished, the highest lossthe Russians have admitted to so far. Sucha Russian confirmation is unusual andindicates that the real losses were highin fact.A drive for an offensiveSince the fall rains started practicallyeverybody has waited for the weatherchange, for the ground to freeze, so asthe larger scale operations could beresumed. The Ukrainians were on alert forthe anticipated large Russian offensive.Unlike a year ago the massive attack didnot materialize. The Russians have lost toomany combat vehicles. Even though theyare being replenished from the reservesthe level of training of the drafted soldiersto operate this equipment is low andthe whole logistics is in the shambles.Instead of the massive concentrations ofits forces the Russian Army attemptedthe attacks executed by the smallergroups at the various sectors of the front,from the borders of the Kharkov regionin the north to the Zaporozhe region inthe south. After a half year long effortthe Russians achieved a breakthroughat Bakhmut. In the beginning of January,they took advantage of the failed rotationof the Ukrainian troops and captured thelittle town of Soledar north of Bakhmut.After that the Ukrainians deployed thereinforcements and blocked the Russianadvance. The pressure on the towncontinued from three different directionshowever and at this time Bakhmut wasstill holding on. The Russian attemptsat capturing the city of Vuhledar furthersouth of Bakhmut, failed spectacularly.The Russian troop were chaoticallyHISTORYText: Miro BaričThe air war over UkraineOld ways pass to the New YearA Ukrainian A1-SM Furia drone with the designation 610 and serial number ACM13072 was shot down near Kreminnaya, Luhansk area, on January 31.During the reported period, from January 1 to February 1,2023, the offensive operations were expected by either side.The large-scale maneuvers however did not take place. TheRussians stubbornly launched mass assaults against thewell-fortified positions, with the poor results that could beexpected.This Russian Ch-101 missile crashed after launch whilestill on its own territory near Ulan-Khola, 140 km fromAstrakhan.INFO Eduard14March 2023Page 15
HISTORYattacking across the huge, opened area,covered with land mines and under thecovering fire of the Ukrainian defenders.The result were tens of combat vehiclesdestroyed and the whole units decimated.The armored fighting vehicles and tanksTo stop these attacks and to prepare theirown counter-offensive, the Ukrainiansrequested the modern armored equipmentfrom their allies. The call was answeredin January. First, in the beginning of themonth. France committed to deliverAMX-10 RC wheeled combat vehiclesarmed with 105 mm cannon and after thatGermany and the USA made their move.Germany will deliver 40 infantry combatvehicles Marder. The USA have deliveredso far 109 proven M2 Bradley vehiclesand others should follow. Besidesthese vehicles however the Ukrainiansrequested the third-generation mainbattle tanks. The call was answered in theend of the months when the Great Britaincommitted to deliver 14 Challenger 2 tanksand shortly afterwards the USA agreed tosupply thirty Abrams tanks and severalcountries will deliver in total several tensof Leopard 3 German tanks. They will bedelivered after the Ukrainian tank crewstraining is completed, currently underway in Britain, Germany and Poland.Long rangeFor quite some time the Ukrainiansdemanded from the USA the supplies ofATACMS missiles with 300 km range fortheir HIMARS rocket launchers. It seemsthat the compromise was reached in theform of GLSDB ammunition with 150 kmrange. There is a problem though, thesebrand-new missiles are not yet in theUSA inventory and their deliveries willnot be possible sooner than in coupleof months. GLSDB stands for GroundLaunched Small Diameter Bomb. It wasdeveloped from GBU-39 SDB bomb whichweighs 113 kilos. These small diameterbombs were designed in a way that anaircraft can carry several of them insteadof one large bomb – and hit more targetsduring one mission. The bomb featuresthe precise guiding system and extendedrange thanks to its gliding ability.Boeing and Saab Group cooperated inthe development of the ground versionof this weapon. They attached the rocketengine to the bomb which will launch itto the altitude on the ballistic trajectory.At that point the rocket engine will bedropped, the bomb will extend its wingsand continue its gliding path. Its range isas long as 150 km. The weapon featuresseveral advantages. Thanks to its semi-active laser sight it can hit the movingtargets within 100 km on the ground andas far as 130 km at sea. And thanks to itsability to maneuver and turn around inThe crash of a Ukrainian Ministry of the interior H225 helicopter caused a major fire in the town of Brovaryon January 18.Ukraine bought 21 H225 helicopters before the war.The machine gun in the nose appeared on several Ukrainian Mi-8s.INFO Eduard15March 2023Page 16
HISTORYthe air it can hit the targets behind thehorizon, impossible for the traditionalgunnery.In case the Ukrainians receive theseweapons, they will be able to fire themfrom the M142 HIMARS and M270 MLRSrocket launchers already in their arsenal.Currently, they only have rockets with70 km range. Using the GLSDBammunition, based on the current frontlines, they will be able to hit the wholeoccupied region of Luhanks, Donetsk,Zaporozhye and Kherson regions andthe upper third of Crimea. The Russianswill be forced to relocate their bases,fuel, and ammunition dumps practicallyoutside of the Ukrainian territory. Noteven the moving trains and ships will besafe from these gliding bombs. At last,GLSDB is priced more favorably - it costs40,000 USD as opposed to 1 million USDfor an ATACMS rocket.Sea Sparrow fired from the groundSoon enough another AA defense systemwill reach Ukraine – and let’s admit,it is urgently needed due to the continuedRussian missile attacks on the Ukrainianinfrastructure. Following the systemssuch as Patriot, IRIS-T or NASAMS, partof those has been already delivered toUkraine, in January the USA announcedthat one of their military aid packageswill include Sea Sparrow rockets.This weapon, used for the ship’s AAdefense, were modified for the grounddeployment in Ukraine. RIM-7 missileswere developed in 1960s based on theair-to-air AIM-7 Sparrow rockets. Whilethose were later replaced by AIM-120AMRAAM missiles, Sea Sparrow rocketsdevelopment continued simultaneously.They are still used today resembling theoriginal Sparrow only by the name.Sea Sparrow rockets were modified tobe used in the modern vertical launchsystems. They weigh 230 kilos out ofwhich the warhead represents 41 kilos.Its airspeed is 4250 kph and range 19kilometers. Besides the aircraft, it candestroy the cruising missiles and certaintypes of rockets. They are radar guided.The Ukrainians will launch them fromBuk systems modified for this purpose.The transfer of three reconnaissanceNATO aircraft, known as AWACS, fromGermany to Romania can be consideredas an indirect form of support. It tookplace on January 1, and they are to remainnear Ukrainian border for at least severalweeks.AWACS is the designation of one of thesystems these aircraft carry on board.They are known to public under this namehowever the official designation is AEW&Cwhich means Airborne Early Warning andControl. For this purpose, NATO usesBoeing E-3 Sentry aircraft operatingfrom Geilenkirchen base in the WesternGermany. USA and NATO reconnaissanceaircraft were gathering the informationeven before the Russian attack on Ukraine.Since then, they have been flying outsideof the Ukrainian airspace over Romaniaand the Black Sea. They are capable tofind out when and how many rocketsand cruising missiles the Russiansfired. The operational space however isapproximately 2,000 kilometers from theGerman base, distance the aircraft haveto cover each way. After the transfer tothe Romanian airbase in Otopeni nearBurcharest, the flight to the Ukrainian-Romanian border is approximately 200kilometers long. The time they can spendon their mission expanded significantlyas well.Secretary of State perishedMost of the aircraft losses is linked tothe intense fighting in Bakhmut area. TheUkrainians reported several helicopters(especially Ka-52) and aircraft (Su-25)shot down however their wrecks havenot been visually confirmed. Only severallosses of the drones could be verified.Su-25SM wreck carrying the bort number“blue 15” and registration RF-95152 wasfound in the Kherson area. The aircrafthad been lost earlier but the images ofits wreck were published only on JanuaryA moody night shot of a Mi-8 under preparations at a forward-field base. A spectacular shot of an unguided missiles firing from a Ukrainian Mi-8 helicopter.Economics professor Oleh Fedirets Ph.D. became an anti-aircraft gunner near Bakhmut.INFO Eduard16March 2023Page 17
5. Obviously, a Su-34, which wreck wasshown in the video on January 25 hadbeen lost quite some time before. TheUkrainian forces lost several drones aswell. On January 6, the mercenaries fromthe so-called Wagner group publisheda video which shows how they, firing theportable rocket launchers, hit an airplane,probably a Ukrainian Su-25. The followingday, on January 7, the satellite imageswere published showing the crashedUkrainian Mig-29. When and under whichcircumstances the airplane was lostremains unknown. On January 18, in themorning, a tragedy took place in the townof Brovary east of Kiev where an AirbusH225 helicopter crashed. 14 people werekilled including the Ukrainian Secretaryof State, his deputy and the statecommissioner.Even before the conflict the UkrainianDepartment of State bought 21 H225helicopters (originally Eurocopter EC225Super Puma). Deliveries started in 2018.They were used by the GovernmentalRescue Service and the National Guard.The aircraft that crashed belonged tothe rescue service and there were ninepassengers on board – besides the crewmembers it was Secretary of State DenysMonastyrskyi, his first deputy YevheniiYenin, state commissioner Yuri Lubkovichand other department officials. Theaircraft was enroute to Kharkiv. Accordingto the eye witnesses the helicopter flewclose to the ground but straight and therewere no indications that it was havingany problems. It flew three circles abovethe town of Brovary east of Kiev andthen it suddenly started to descend, hita kindergarten, and crashed next to themulti-family residential building. It wasdark and foggy at the time of a crashwhich could have played a significant rolein the tragedy. The kindergarten buildingwas set on fire and had to be evacuated.Besides nine people in the helicopter fivemore people died on the ground, includinga child. 30 people were injured out ofwhich 12 were children.Till the end of January four more Ukrainianairplane losses were confirmed. OnJanuary 22, the mercenaries from theso-called Wagner group shot downa Mi-8 helicopter near Bakhmut.Its three-member crew was killed.On January 27, Captain Danylo Murashkowas killed near Kramatorsk during thecombat flight. He flew Su-25 from 299Brigade of Tactical Aviation. AnotherMi-8 was shot down on January 30 nearNovodarovka in Zaporozhiye region ona mission to supply the ammunition. Itsthree-member crew did not survive. Onthe last day of January, a Mi-2 helicoptercrashed near Poltava it is far from thefront line. Therefore, it can be considereda non-combat loss. Two-member crew47 years old pilot Vladyslav Stankevychand 46 years old commander GennadiiButenko, perished in the crash.HISTORYA Polish-made Krab self-propelled howitzer was saved from a Russian Lancet kamikaze drone by a metal mesh.Footage of a crashed MiG-29 with blue-yellow coloringon its wings appeared on January 7.The wreckage of a Su-25SM with the fuselage number "Blue 15" and registration RF-95152, images of which were released on January 5.INFO Eduard17March 2023Page 18
HISTORYCaptain Danylo Murasko was killed on January 27 during a combat flight near Kramatorsk.The crew of Captain Gennady Butenko and Lieutenant Vladyslav Stankevych didnot survive the Mi-2 crash during a training flight on 31 January.Originally Slovak Mi-17 in Ukrainian service.Footage of the wreckage of this Su-34 was released on 25 Jan.INFO Eduard18March 2023Page 19
Page 20
EVENTIt has to be said right at the beginning thatthis year fair was different from the previousones. There were significantly fewerexhibitors. In our market segment of plasticmodel kits, the fingers of just two handswould be enough to count the participants.However, count me in – Eduard/SpecialHobby, Italeri, Tamiya, Revell, Airfix. Whatelse? Let’s add to the credit the Art ScaleKit distributor and Zvezda, which hada stand in one of the tucked away boothsdue to the organizers’ restrictionsagainst Russian companies. Any others?No, nobody else. Other companies fromour business chose a more economicaloption and came only to have a look andgo round the stands. And more than weexpected stopped at our stand. Amongthem, even those we hadn’t counted onbeforehand. Others didn’t come at all.For example, representatives from China,USA and Ukraine were missing, and therepresentation from Poland was also quiteweak.But no wonder. The situation is not rosy,so many companies have opted forlow-profile and very economical formsof participation. We alsochose a more economicaloption than in the past, andas more attentive readersmay have noticed above, wejoined forces with a friendlycompany, Special Hobby,reducing our stand to onlytwo-thirds of its former size.Of course, this led to moreintensive communicationwith our colleagues from Special Hobby, sowe were able to discuss further possiblecooperation on future projects. However,when more visitors arrived at one point,the booth was a bit tight ... Nevertheless,we handled it without any problems. Wealso split our team into two parties androtated with our colleagues after threedays at the fair. Saving money is necessarynowadays!If you have not attended this fair in personin the past, I guarantee you would beimpressed anyway. It’s a huge event, with2,843 exhibitors from 70 countries takingpart this year, and over 62,000 visitors from136 countries visiting the fair over five days.But something in the mood was simplymissing. Talking to other people in theindustry, it was clear that they had mixedfeelings about attending. As the numberof exhibitors in the industry dwindles, theimportance of the event for us and othersis diminishing, and if the situation does notimprove, we would at least be very hesitantto decide on participation in future years.However, as usual, there was a silver lining.In this case, thanks to the low participationof the companies from our business,we were able to conduct more intensivenegotiations with visitors to our stand.Several very pleasant meetings took placein a friendly atmosphere with companiesBack to NurembergAfter a long two-year hiatus caused by the COVIDepidemic, the Eduard team was back to theNuremberg Toy Fair once again. The event tookplace from February 1 to 5 and was held in sixteenhalls of the local trade fair center.Alfred Riedel and Vladimír ŠulcJan Bobek and David Francis(Phoenix Scale Publications)Jan Zdiarský and Vladimír ŠulcText: Jakub NademlejnskýINFO Eduard20March 2023Page 21
EVENTfrom the industry, but also from outsidethe industry, which may have an impacton the future, for example on our futurereleases. For example, we arranged thereboxing of Su-25 Zvezda kit and sketchedout the negotiations on reboxing of Airfixkits. Representatives of Airfix, Italeri orRevell liked our 3D prints or SPACE fora change, and so possible windows ofcloser cooperation are opening up for usin the future. As far as the design of thestands of these companies is concerned,Airfix was part of the huge Hornbypresentation, where it had its own spaceamong about ten brands that fall underHornby. And you’ve got to get ready fortheir new Gannet in 1/48, they say it’s goingto be cool! The Italeri booth reminded meof an Italian coffeehouse. Lots of roundtables and chairs everywhere, a receptiondesk, and delicious Italian coffee or a shotof grappa, which gave the negotiationsthere a touch of Italian flair. The boothwas dominated by two large display caseswith built models featuring new releases,1/72 AMX and 1/32 Mc.202 graphics. Revelltraditionally had a stand in Hall 12, amongthe dominant companies in the wholetoy industry, such as Lego, Playmobiland Mattel. Revell revealed various newproducts for 2023, among which I wouldhighlight the Gloster Meteor in 1/32 scale.The only representatives of the exhibitingcompanies that we didn’t exchange toomany words with at the fair were fromTamiya. Their stand was by far the largestin our Hall 7A and was dominated by atrack for RC models. So maybe next year ...The award ceremony of the Modellfanmagazine with prizegiving of the Model ofthe Year awards is one of the traditionsof the fair. This year the award went toour Wildcat in 1/48th scale. We are ofcourse happy that our kit is among thechosen ones, but so many are awardedby Modellfan every year that it kind ofdegrades the whole thing. We already havea bowl full of medals and judging by thedisplay cases of other companies, almosteveryone regularly wins a medal for onePavel Gerhart, Vladimír Šulc and Zdeněk Peroutka (MPM s.r.o.)INFO Eduard21March 2023Page 22
Jan Bobek and Vladimír Šulcof its product. We chose to present theawards in the aforementioned bowl thisyear, as if we had placed them in the displaycases, there probably wouldn’t have beenmuch room left to present our products.To sum up, I would like to say that I waspersonally impressed by the magnificenceand high level of organization of the fair,as it was my first time at this event. Theysay organization is a common thing inGermany, and it was demonstrated on thespot by the German police, who completelypacked up the stand of a Chinese die-castmodel seller in short time, and the ownersof the stand then sat on a few boxes for therest of the fair. It all was done supposedlybecause of plagiarism. In contrast, wehad to pack our own things by ourselveson Sunday and arrived home safely. So,hopefully next year again!The Hornby stand which includes the Airfix stand.Presentation of new Tamiya products.EVENTINFO Eduard22March 2023Page 23
EVENTINFO Eduard23March 2023Page 24
EVENTINFO Eduard24March 2023Page 25
EVENTINFO Eduard25March 2023Page 26
The Spitfires Mk. Vb/Vc had their mostglorious time during the battles for the small,but strategically important, island of Malta.One of the most successful Spitfires to fightthere was the Mk.Vc serial number BR301.The aircraft came from a consignmentof Spitfires taking off on May 9, 1942,from the carrier USS Wasp (CV-7) duringOperation Bowery. Like most Spitfiresfrom the Bowery delivery, BR301 had DarkMediterranean Blue color applied to theupper surfaces while still on the aircraftcarrier’s deck. But the original desertcolor scheme was slightly visible underthis new paint. The lower surfaces wererepainted in Sky Blue. This aircraft had alsothe national roundels overpainted with thiscolor. The original four-cannon armamentwas reduced to two cannons, mounted ininner position in the armament bay andtwo inner machine guns. CodenamedUF-S, BR301 served first with No. 601 Sqn.,but its pilots achieved most of their successwith it in July 1942 after transferring to No.249 Sqn. There it became the “aircraft of theaces”.P/O John McElroy (10 victories plus threeshared in total) claimed one MC.202 withBR301 on July 7, one Ju 88 shared on July 9and one Bf 109 on July 13, damaging anotherone in the process. No. 249 SquadronLeader Richard Mitchell (5 + 3) shot downa Ju 88 on July 23, while F/Sgt JohnRae (11 + 2) shot down a Bf 109 probablyand a Ju 88, in addition to damaginga Re.2001 and a Ju 88 on July 27 and28. The greatest success with the BR301was achieved by Canadian pilot in theranks of the RAF Sgt. George Beurling,who destroyed four opponents during onemission (two MC.202 and two Bf 109) andadded one Bf 109 on July 27 two days later.For our boxart, created by PiotrForkasiewicz, we chose to depict Beurling’sfirst kill. His victim, a Macchi MC.202, is verywell documented both photographically(after the crash landing) and also by combatreports of the two combatants. Thanksto that, we know how it all went down:At 0855 hours on July 27, 1942, No. 249Sqn. sent out six Spitfires to join othersix patrolling Spitfires from Nos. 126 and185 Sqn. A formation of seven Ju 88s,accompanied by more than forty fighterswas approaching Malta, flying at 25,000feet (7,600 m). Beurling was the first tospot the enemy and radioed to warn theothers: “Enemy aircraft at four o’clock,slightly below us!” He immediatelylaunched an attack. The enemy fightersnoticed Beurling’s action and went intoa left climbing turn. Beurling then got on thestarboard side of one MC.202 and fired hischaracteristic short burst.Beurling later recalled: “I saw four Macchisflying in a row and I focused on number 4.I fired a short burst that went into its engineand radiator.” The pilot of MC.202 SergenteMagg Falerio Gelli of 378-11 Squadrigliaturned his aircraft towards home base,but immediately realized that the smokingengine would not last long enough. Hetherefore chose a place and belly-landedin a field outside Victoria on the island ofGozo. Later, when questioned, he said:“I saw a Spitfire firing at me, but I didn’tfeel any impacts. I was performing evasivemaneuvers and noticed that the enginetemperature was rising rapidly. In anattempt to reach my base, I turned north,but soon realized I couldn’t make it asthe oil tank and radiator had been hit. So,I turned back and landed at Gozo”.Some pilots and ground staff went to seeGelli’s Macchi. The aircraft was relativelyintact, and the battle damage was consistentwith Beurling’s report. The rudder wasremoved and the emblem of the 51° Stormounit was also cut out of the fuselage asa war trophy. Beurling later posed with thetrophies for photographs.During the five months of fighting in Malta,Sgt. George “Screwball” Beurling scoreda total of 28 kills (including one shared) ofAxis aircraft, becoming the most successfulAllied pilot of the Battle of Malta. Theseachievements earned him another unofficialnickname: “Falcon of Malta”. It was meant tocharacterize his straightforward predatoryinstinct in combat.Spitfire BR301 was irreparably damagedon July 29 and decommissioned with54 flying hours.BOXART STORY #82126Text: Michal KrechowskiIllustration: Piotr ForkasiewiczThe Maltese FalconINFO Eduard26March 2023Page 27
#7033BOXART STORYThe Ju 87 Stuka units from the Battle ofBritain period are mainly known for theheavy losses they suffered on August 18,1940. However, they returned to combat inearly November. Their targets were onceagain Allied vessels in the Channel.One of the units that made it through theentire western campaign was III./St.G.1.It was formed in July 1940 from I.(St)/Tr.Gr.186, which was originally intended to be on boardof the aircraft carrier Graf Zeppelin. Gruppe’scommander, Obstlt. Walter Hagen becameKommodore of Sturzkampfgeschwader 1 inmid-1940. His former Gruppe, under the newdesignation III./St.G.1, was taken over byHptm. Helmut Mahlke, who served in theLuftwaffe from 1935 after previous service inthe Navy.In early November 1940, well protected byfighters from III./JG 51 and from Galland'sJG 26, Mahlke's unit made three attacks onallied vessels within sight of the British coast.In mid-November, III./St.G. 1 found itself inan unexpected situation. For organizationalreasons, it was incorporated under thefighter command of Luftflotte 2, the so-calledJagdfliegerführer 2 (Jafü 2). Its commanderwas GenMaj Kurt-Bertram von Döring,a World War I fighter ace.Mahlke had legitimate doubts about howJafü 2 would handle leading a bomber unitin attacking vessels. His fears were realizedon the first deployment on November 14,1940. This is a transcript of a communicationbetween the two staffs that began at 1100.The document is part of the St.G. 1 Chroniclein the Bundesarchiv collections: Jafü 2:“III./St.G.1 will attack: enemy convoy reportedto have passed Dover in a north-easterlydirection towards the Thames estuary.Fighter escort to join at 1445 on the Channelcoast. Do not fly beyond Cape Margate due tolimited range of escort fighters.”III./St.G.1: “When and where was the convoysighted, how many ships and at what speed?”Jafü 2: “A formation of ships was sightedat 0900 off Dover, medium speed, easterlycourse.”III./St.G.1: “Then the convoy of ships will passCape Margate before we reach the targetarea. We request permission to deploybeyond Cape Margate in this case.”Jafü 2: “The Cape Margate restriction must berespected at all times.”III./St.G.1: “What is the alternate target if theship group is not in the restricted area?”Jafü 2: “Then attack the other ships in theDover-Margate section. If there are no shipsthere: the alternate target is the radio stationat Dover.”III/St.G.1: “If we get to Margate and then turntowards Dover, we'll have the entire Britishfighter fleet on our tail! - Which radio stationat Dover is to be the alternate target, we have3 radio stations here in the Dover files.”Jafü 2: “The one with the mirror” (“Spiegel”,German for mirror, a codename for radar)III./St.G.1: "Which one is it?”Jafü 2: “We don’t know that either. We willtry to find out and tell you before the take-off. Otherwise, just attack the largest radiostation in Dover.”Just as Mahlke predicted, they did notencounter a single ship on the flight toMargate. The formation of nineteen Stukasthen proceeded to Dover, where it wasattacked by five RAF squadrons. Some of theStukas had as many as five enemies on tail.Yet some of them managed to drop bombs onDover facilities. Stuka gunners claimed twovictories and RAF fighters reported 16-4-5Stuka victories. A number of Stukas werehit, but only two were shot down and threemore made emergency landings in France.Galland’s fighter escort arrived at the sceneof the engagement 10 to 15 minutes late.Kommodore Galland, CO of 7./JG 26 Oblt.Müncheberg and CO of 9./JG 26 Oblt. Rupperteach claimed one Spitfire. However, the RAFlost only one Spitfire from No. 74 Sqn. andtwo others from No. 66 Sqn. were damaged.After a few days, a meeting between thestaffs of Jafü 2 and St.G. 1 took place. In theprocess Mahlke and his commander learnedthat it was a mistake to disband the formationand try to escape from the Spitfires. Aftera subsequent exchange of views, Jafü 2no longer required the deployment of theStukas, explaining that there were no fighterunits available as escorts.Helmut Mahlke retired in 1970 at the rank ofGeneralleutnant and had not only 159 combatsorties in the Stuka but also a number offlights in the F-104 Starfighter in his flight log.He is the author of Stuka Angriff: Sturzflug,published in English as Memoirs of a StukaPilot.Text: Jan BobekIllustration: Marek RyśStukas under fighter commandINFO Eduard27March 2023Page 28
BOXART STORY #7468Early August 1943, the Bf 110 G-2s of II./ZG 1moved from Monte Corvino to Lanveoc-Poulmic. Command of II./ZG 1 passed to HptmKarl-Heinrich Matern, Staffelkapitän of 4./ZG 1.II./ZG 1 was to be used countering increasedAllied air traffic over the Bay of Biscay togetherwith Ju 88 C-6s of V./KG 40 and Fw 190sof III./JG 2 and 1./Seeaufklärungsgruppe 128.August 21, 1943, saw the first victory when theGruppe claimed a Liberator. This is believedto be from 311 Sqn. and was flown by Wg CdrJindřich Breitcetl – all eight crew perishedbut Uffz Georg Planer of 5./ZG 1 was lostin the combat.On September 11, 1943, Mosquitoes of 307Sqn. claimed to have destroyed a Bf 110,probably destroyed two and damaged one.Lt Dieter Bambauer of 5./ZG 1 was lost so wasprobably the victim of Flt Sgt Zbigniew Dunin-Rzuchowski. Five days later, II./ZG 1 interceptedB-17s attacking targets in western Franceclaiming three, credited to Fw Klaus Schreuerand Oblt Arnold Dorka of 4. Staffel andFw Emil Pfeiffer of 6. Staffel.A Liberator of 53 Sqn. flown by Flt Lt TonySpooner was then damaged by Bf 110s betweenthe Scillies and Lundy Island on September21, 1943 and three days later, the Gruppesuffered its heaviest losses to date. DespiteOfw Ruhland Zahn and Fw Hans Fuchs of 5./ZG 1 each claiming a Spitfire and Ofw HeinrichBörger and Uffz Peter Schölz of 6./ZG 1 claiminga Mitchell and a Spitfire, four Bf 110s, includingthose of Zahn, Fuchs and Oblt Arnold Dorka,were lost to Spitfires of Nos. 66, 313 and 610Sqn. No 98 Sqn. Mitchells were lost but 313 Sqn.lost three which included Sqn Ldr JaroslavHimr.II./ZG 1’s time over the Bay of Biscay wouldnow only last another three weeks. On themorning of September 27, 1943, Fw KlausSchreuer of 4. Staffel claimed a Wellingtonand 30 minutes later, 5./ZG 1 got a secondWellington. The Wellingtons came fromNo. 612 Sqn. flown by Flt Sgt Robert Hyndsonand No. 407 Sqn. flown by Wg Cdr JohnArcher, the latter having gone to search fora No. 407 Sqn. Wellington which had ditched offthe Scillies returning from the Bay.Six days later, the Gruppe apparently claimeda Sunderland and a Typhoon. The former waspossibly from No. 10 Sqn. RAAF captainedby Fg Off Fred Lee while the latter waspossibly a Hurricane of 1449 Flt flown by FltSgt Richard Adams which was reported shotdown 35 miles south-west of the Scilliesat 0900hrs.The end for II./ZG 1 came on October 8, 1943.At 0735hrs, seven Spitfires of No. 453 Sqn.took off on what was called an anti-Me110 patrol. At 0845 they came across eightBf 110s and in the ensuing battle, Fg Off HaroldParker was seen to be shot down and FltLt Russell Ewins, having shot down a Bf 110,suffered engine failure and ditched. Parkerwas reported missing, but Ewins was rescued.Another four Bf 110s were claimed destroyedby Fg Off Patrick McDade and Plt Off ColinLeith. At 1330hrs, eight Bf 110s got airbornefrom Lanveoc-Poulmic looking for twoaircraft lost that morning. No. 610 Sqn. wererelieving a Mosquito circling Russell Ewin’sdinghy and at 1415hrs bounced the Germans.Fg Off Vincent Moody and Flt Sgt Bob Husseyeach claimed a Bf 110 around 1415hrs. Finally,at 1445hrs, No. 66 Sqn. together with 453Sqn., got airborne to escort aircraft bombingII./ZG 1's home base. No. 66 Sqn. bounced eightto 10 Bf 110s off Brest claiming three Bf 110sdestroyed, one probable and one damaged.The timings for II./ZG 1’s losses are hardto determine. There were some claims by6. Staffel as Ofw Heinrich Börger claimeda Mitchell, Fw Franz Meissl a Spitfire andUffz Anders a P-47 around 1545hrs. Duringthe day they lost 11 fighters with three moresuffering varying degrees of damage. Thoselost included Hptm Karl-Heinrich Matern (whowould be awarded the Ritterkreuz the followingday – he was possibly lost in the morning asHptm Rudolf Wangner was leading the Gruppelater that day), Lt Hans-Bodo Busch (Adjutant)while Lt Hans Schmidtal, who was leading6. Staffel, was wounded. Lt Wolfgang Priebeand his radio operator from 4./ZG 1 werecaptured after being shot down by No. 610 Sqn.and their interrogation revealed much aboutthe Gruppe but by then it was too late. Havingsuffered such heavy losses, one more comingon October 14, 1943, when Uffz Max Wichertof 6./ZG 1 crashed due to engine failure offthe Ille D’Ouessant, in November, II./ZG 1, nowcommanded by Ritterkreuz winner Hptm EgonAlbrecht, former Staffelkapitän of 6. Staffel,withdrew to Wels where in July 1944 it wasdisbanded to become the Bf 109-equippedIII./JG 76.Text: Chris GossIllustration: Piotr ForkasiewiczWasps over the bayINFO Eduard28March 2023Page 29
BOXART STORY#8232In the spring of 1998, a significant eventoccurred in the Finnish Air Force. TheMiG-21BIS was retired from its arsenal andthe replacement, the F/A-18C/D Hornet,marked a significant shift for Ilmavoimat.However, the road to this turning point wasrather thorny.Finland was in a difficult situation after theSecond World War. Fighting with the RedArmy during the Winter War and then theContinuation War had significantly drainedits resources and thrown the country into analliance with Nazi Germany in its fighting forsurvival. Finland then fought against Germanyin the Lapland War after the armistice withthe USSR in 1944. The Paris Peace Talks in1947 limited the post-war development of theFinnish air force which was still using oldBf 109Gs in the early 1950s. The country didnot have the funds for modern aircraft, amongother things because of the reparations paidto the USSR. However, in 1952 the purchaseof six Vampire Mk.52s was agreed bygovernment and Ilmavoimat entered thejet era. But Vampires were obsolete, andthe USSR was concerned about the lackof protection of its neighbour’s airspace ina deteriorating international situation.Soviets feared that it could becomea “gateway” for a possible strike from theWest. Finland was thus threatened that theUSSR would use a provision in the 1948 PeaceTreaty (YYA) to take over the protection ofFinnish airspace, which would havenegatively affected Finland’s internationalposition. The result was the purchase of12 Folland Gnats in 1958.In the early 1960s, the Soviet Union attemptedto persuade Finns to buy the aging MiG-19Ss,but Finnish pilots were already familiar withthe Western machinery, including the J 35DDraken or Mirage IIIC thanks to test flights,and so the offer was declined. However, thefinancial capabilities of Finland did not allowthe purchase of these types. On the contrary,the acquisition of Soviet equipment wouldhave been advantageous due to the possibilityof repaying it with supplies of goods.In October 1961, the USSR sent another noteto Finland demanding increased protectionof Finnish airspace, again with a threat of useof the provisions of the YYA. After this crisiswas settled, the USSR offered Finland theMiG-21F-13 and on February 1, 1962, a contractwas signed for the delivery of twenty aircraft,the first of which were delivered on April 24,1963.Just a decade later it was obvious thatIlmavoimat would need another upgrade.The Saab J 35 Draken was selected asa replacement for the Gnats and in the spiritof the ongoing policy of diversification, itwas decided that the replacement for theMiG-21F-13 would be procured from theUSSR. The Finns requested a presentationof the available types and were offered MiG-23MS and MiG-21bis. The MiG-23 was moreexpensive and its maintenance requirementswere higher, while the MiG-21 was cheaperand already established in Finland. Andthat made the decision. In the autumn of1976, Captains Paavo Janhunen and TaistoMyöhänen were enabled to test-fly the typeat the Krasnodar base and a year latera contract for 20 aircraft was signed.The first two MiG-21BISs landed at Risalaon September 21, 1978. One of them, codedMB-114, was flown to the test center inHalli, the other, MB-111, was used for pilotconversion training at HävLLv 31 (31st FighterSquadron). Subsequently, the fuselagedesignation of the MiG-21BIS was changedfrom MB to MG, and the remaining 18 aircraftwere delivered in three batches during 1980.The MG-129, which is pictured on the boxartby Petr Štěpánek during a landing at KuopioAir Base was part of the second delivery onJuly 17, as was its wingman on the painting,coded MG-124. In 1984, it was decided topurchase six more aircraft, so in total theIlmavoimat operated 26 MiG-21BISs.All the delivered aircraft underwent avionicsand instrumentation modifications by Valmet.The stenciling was translated to Finnish,the aircraft received VHF/COM radios andaltimeters of Western origin, as well asVOR/ILS/DME systems and transponders.In January 1986, the MiG-21F-13s that hadserved with the Reconnaissance Squadron(TiedLLv) were retired and replaced byMiG-21BISs modified to carry reconnaissanceand electronic warfare containers. Thereconnaissance squadron was disbandedin 1996, and two years later all FinnishMiG-21BISs were gone…Text: Richard PlosIllustration: Petr ŠtěpánekVirtue out of necessityINFO Eduard29March 2023Page 30
BOXART STORY #8192The Avia B.534 is one of the symbols of thedetermination of Czechoslovakia to stand upagainst the threat of Nazism that had grippedGermany, and the threat of its spread to othernations in Europe. The attempts to rip away theborder regions of Czechoslovakia were obviousfrom the mid thirties and diplomatic rifts werethe order of the day. A strong fighter force wasthe only way to deter German aggression fromthe air and to make negotiating meaningful. TheCzechoslovak industry lacked the capacity todevelop and especially to produce a fast, singleengine fighter that could hold its own againstthe Bf 109 and the fast German bombers of theLuftwaffe. For this reason, the nation turned tothe more multi-functional Avia B.534 biplane.The aircraft’s prototype, designed byFrantisek Novotny, first flew in May 25,1933. It displayed a very good rate of climb,excellent maneuverability, and, for thattime, a good maximum speed, approaching250mph. Its performance exceeded thoseof its competition from Praga and Letov. Theinitial versions had an open cockpit which laterwas covered, and there was an evolution in theaircraft’s armament, engine cooling system,propeller and on-board equipment. Thecurrently available kit represents the epitomeof the B.534, not including the cannon armedBk.534 which never saw the installation of thecannon firing through the propeller hub, andso production versions were only armed withthree machine guns instead of four.The B.534 entered service at the beginningof 1935. AT the time of increasing tensionsprovoked by Germany, 27 aircraft were loanedby the army to border guard units. The mainacceptance of the type into service tookpart in the immediate pre-war years, seeinga growth in numbers from 326 at the beginningof September, 1938 to 443 in March, 1939.The family tree of the type in production canbe divided into four blocks, plus the plannedcannon armed Bk.534.The B.534s played their role during bothCzechoslovak mobilization periods in May andSeptember, 1938. Their pilots were ready andwilling to protect their freedom. As a resultof the complete betrayal by Czechoslovakia’slegally bound allies Great Britain and France,culminating in the Munich Agreement andthe dismemberment and occupation ofBohemia and Moravia, the B.534 never got theopportunity to put up a fight. In fact, the B.534became a welcomed prize for the Germans thatpressed them into service in their own unitsand in those of their allies. The type was usedby the Luftwaffe, primarily in the advancedtraining role, and was supplied to Slovakia andBulgaria, as well as to a lesser extent, Greece.The exception to this are three B.534s thatwere used during the Slovak National Uprisingagainst the Germans, an event that broughtabout the last air to air victory to be achievedby a biplane fighter in history.The painting by Martin Novotny takes us backto the summer of 1937, where the clear skyrepresents the fragile calm, but history tells usthat storm clouds were gathering on the otherside of the border. The aircraft bearing theserial number 534.208 was first flown on July1, 1937 by factory test pilot Oldrich Kosar, andtwo days later was handed over to Air Forcereps. On July 13, 1937, the aircraft was ferriedto Kbely, from where it made its way to the 2ndAviation Regiment at Olomouc, and was laterassigned to the 36th Flight.There, it served with this unit on September6, 1937, when during a formation flightover Hostynske Vrchy at 6,500m there wasa collision involving two B.534s. JaroslavSodek, later to become a Czechoslovakmember of the RAF, collided with aircraftserialed 208 while flying aircraft B.534.035as a result of being blinded by the sun. Hecollided with the second Avia from the leftand from behind. The Flight Leader, flying thatsecond plane, was Sgt. Julius Zaoral, who wasable to nurse his plane back to Olomouc andland, while Sodek had to take to his chute. Thedamage to the aircraft flown by the Sergeantwas restricted to both the upper and lowerleft wing and included the interwing struts.The aircraft was repaired and pressed backinto service, only to be later taken over by theGermans.Although the B.534 by 1938/39 would not havethe opportunity to stand up to the aggressor,the same could not be said of its pilots. Theywere, to varying degrees, involved in domesticresistance, and significantly left to opposethe Germans in foreign services of allies thattook them to Poland, France, Africa, the SovietUnion, the far east, and most notably, GreatBritain.That, though, leads to other events throughhistory, with which you can get acquaintedthrough other Eduard kits.Text: Jan ZdiarskýIllustration: Martin NovotnýThe Calm Before the StormINFO Eduard30March 2023Page 31
BOXART STORY#11170When Operation Watchtower was launchedon August 7, 1942, a “green hell” was waitingfor the men of the 1st Marine Divisionunder the command of Maj. Gen. AlexanderVandegrift on Guadalcanal. Though only 2,000Japanese stood against 6,000 Marines, theirfanatical determination did not waver evenafter fighting for 36 hours, when Americanforces had captured most of the island,including the airfield under construction. Thelanding was strongly supported by naval andair forces, with the USS Enterprise’s pilotsmaking 237 combat sorties that day, othersadded by the pilots from the USS Saratoga.After the Enterprise withdrew from the area,the aerial support weakened and the Marineson the island suffered intense bombing.No wonder they were eagerly awaiting thearrival of the fighters. Those arrived onAugust 20, when VMF-223 Wildcats landedat Henderson Field.Air combat and on-site accidents quicklyreduced the numbers of aircraft and justten days after arrival there were only fiveof the 19 Wildcats left. Even later, after thearrival of reinforcements, the numbers ofairworthy Wildcats were rapidly decreasing.The pilots had no choice and no Wildcat fromGuadalcanal can be attributed to a particularpilot. In the case of the GUADALCANALLimited kit, we solved this in a jokey way:Where possible, we assigned a specific pilotto the aircraft he flew in a known event.The third most successful fighter of thecampaign, Capt. Marion Carl, would certainlydeserve “his” marking in the kit. Butconcerning the Wildcat often attributed tohim, it’s complicated.The aircraft with the number 2 on thefuselage and nineteen kill marks under thecockpit (marking F) was most likely one heever flew with. According to the testimonyof historians who spoke with the famousace, Carl said that this aircraft in the well-known photographs was in fact an “hangarqueen” pulled out of the hangar at EspirituSanto to be photographed with the hero bythe media. For this purpose, the nineteen killmark stickers were applied. The media thenreportedly took a lot of pictures of MarionCarl at “his” Wildcat. But ...No matter how much you are searching,you won’t find a proof photo of Carl with thisaircraft. Which is strange. In one famousphotograph, a man is squatting on the wing,half undressed, wearing a crumpled cap.It’s said to be Marion Carl. But would a pilot,an officer, present himself to the media likethat? Hardly ... In several other photos, sittingin the cockpit or standing on the wing is TechSgt R. W. Greenwood. The photo of him in thecockpit was published in Stars and Stripesmagazine during the war. Firstly with thecaption “unknown soldier in the cockpit ofa Wildcat on Guadalcanal”. When the editorsfound out who it was through a letter from asergeant’s fellow, they published the photoagain, this time with his name. The mentionof Guadalcanal remained and according tothe sergeant’s son, his father never disputedthat fact. But historians say this Wildcatnever made it to Guadalcanal! But the picturewith Greenwood shows the kill marks wereworn out and the surroundings on the photoof the whole aircraft looks like Hendersonfield rather than Espiritu Santo airfield.What’s more, even the official US Navyarchive dates the photo to February 2, 1943.At this time Carl was gone from Guadalcanalfor some four months! So, there are manyquestions regarding this aircraft. It issometimes also attributed to the CO ofVMF-223, Maj. John L.Smith, because heachieved nineteen kills, which correspondsto the number of kill marks. But he was alsono longer on Guadalcanal in February.We may never know the full truth about theWildcat with number 2, but that uncertaintymakes it an attractive option as well. Wehave, however, chosen other Wildcats forthe boxart. The one in the background was“Swede” Vejtasa’s personal mount (markingA). For the foreground we have chosen anaircraft that was only marginally relatedto Guadalcanal, as it was used by 1/Lt. S.B. Folsom shortly after he left the island(marking H). But there are not many Wildcatswith such a nice nose art, so it was anobvious choice. The author of the Wildcats onthe boxart of the kit 11170 is Adam Tooby andhe did a great job, which is supported by thegraphics by Jan Zdiarsky. Twelve markingsand two complete kits are what is waiting forthe modeler inside the box ...Text: Richard PlosIllustration: Adam ToobyGraphic design: Jan ZdiarskyGuardiansINFO Eduard31March 2023Page 32
#82126Spitfire Mk.Vc TROP1/48ProfiPACK edition kit of British WWII fighter plane Spitfire Mk.Vc TROPin 1/48 scale. Kit presents tropical version of famous Spitfire Mk.Vcflying in the RAF, SAAF, USAAF and RAAF.plastic parts: Eduardmarking options: 6decals: EduardPE parts: yes, pre-paintedpainting mask: yesresin parts: noProduct pageKITS 03/2023INFO Eduard32March 2023Page 33
BR301, Sgt. George F. Beurling, No. 249 Squadron,RAF Hal Far, Malta, July 1942BR476, S/Ldr Jefferson H. Wedgwood, No. 92 Squadron,RAF LG. 173, Egypt, August–October 1942JG959, Lt. McClellan E. S. Robinson, No. 1 Squadron SAAF,Ben Gardane, Tunis, April 1943Spitfire Mk.Vc serial number BR301 was one of the mostsuccessful Spitfires fighting on Malta. The aircraft camefrom the batch of Spitfires flying off the aircraft carrier USSWasp (CV-7) on May 9, 1942, during the operation Bowery.Like a majority of Spitfires delivered for the operationBowery, BR301 had the blue shade of Dark MediterraneanBlue applied already on board of the carrier having theoriginal desert scheme (Dark Earth and Middle Stone)shown slightly through. The lower surfaces were re-painted in Sky Blue including the national markings. Theoriginal armament consisting of four cannons was reducedto two in the wing inner gun bays and two machine gunswere installed outwards. BR301 coded UF-S first servedwith No. 601 Squadron however its greatest glory awaitedit at No. 249 Squadron where it was transferred. Here itbecame an “aircraft of the Aces”. Between July 7 and July13 P/O John McElroy claimed four aerial victories flyingit and on July 27, a rising star, Sgt. George Beurling shotdown four enemy aircraft in one mission and two dayslater he claimed another kill with BR301. During the monthof July S/Ldr Richard Mitchell and F/Sgt John Rae claimedfurther kills. On July 29, BR301 was damaged beyondrepair and struck of charge having flown 54 hours.Jefferson Heywood Wedgwood was born on May 28, 1917,in London. He was educated at Holyrood School, Bognorand Lancing Colleges. In March 1936 he joined the RAFand a year later he became a staff pilot at No. 2 AirArmament School in North Coates. After a brief stint atNo. 65 Squadron, he was transferred as an instructor toNo. 12 Group Pool in Aston Down. On July 18, 1940, Wedgwoodwas assigned to No. 253 Squadron at Kirton-in-Lindseywith which he took part in the famous Battle of Britain.During the month of September, he destroyed a Bf 110 andcooperated in destroying five Ju 88s and three Do 17s.At the end of September, he was ordered to VickersSupermarine where he flew as a Production Test Pilot buton October 10 he was transferred to the RAF CzechoslovakDepot in Cosford as a flight instructor. In January 1942he assumed command of the No. 92 Squadron in Digby.In February the unit was transferred to the Near Eastand in April it arrived in Egyptian Fayid. For severalmonth the unit was without any airplanes and as ofJuly 2 the pilots were attached to the No. 80 Squadronin the Western Desert to gain the operational experience.Finally, in the end of August 1942, the tropicalized Spitfiresarrived. Between August 14 and October 29 Wedgwooddestroyed eight Bf 109s and damaged another eight. Forhis accomplishments he was awarded DFC. On December17, 1942 he was on board of a Halifax Mk.II from No. 138Squadron as a passenger flying back to the Great Britainbut the aircraft crashed near Żejtun on Malta. It is highlyprobable that it was shot down by a friendly AA fire andall on board perished. Jefferson Wedgwood is buried in theNavy cemetery in Capuccini on Malta.Pilot’s full name was McClellan Eric Sutton Robinson, andhis usual nickname was “Robbie”. He was born on February26, 1919, in Johannesburg. His first operational unit was No.1 Squadron SAAF flying Hurricanes. He was assigned to theunit in August 1942 and remained flying with it for a year. OnNovember 2, 1942, he achieved his first combat success whenhe shared victory over a Ju 87. After he converted to SpitfireMk.V, between January and April 1943, he added another fivevictories to his score. After that he had bad luck for the firsttime when on July 14, 1943, he was shot down by a friendly fireof a USAAF P-38 and had to bail out over the Mediterranean sea.He got lucky though as he was fished out by the crew of a Greekdestroyer. In September 1943, at the end of his tour of duty,Robinson was awarded DFC and sent back to the Great Britainwhere he assumed the post of a flight instructor at No. 11 OTU.On November 14, 1944, the bad luck struck again as he collidedmid-air with one of his students flying Kittyhawk, crashed andwas killed. All his personal Spitfires carried the inscriptionCireCooks on the port side which was the combination of hisfirst name and last name of his fiancé. Number VI indicatedit was the sixth airplane christened with this name. On April22, 1943, flying this aircraft, Robinson shot down two Bf 109Fs.During his combat career he shot down in total five enemyaircraft plus one probable and one aircraft damaged.KITS 03/2023INFO Eduard33March 2023Page 34
Lt. Luis T. Zendegui, 2nd FS, 52nd FG, 12th AF,La Sabala, Tunis, Winter 1942–1943MH592, S/Ldr Hinko Šoić, NOVJ No. 352 (Yugoslav)Squadron, Vis, Yugoslav, January–February 1945A58-137 (EE835), F/Lt David H. Hopton, No. 79 SquadronRAAF, Kiriwina, Trobriand Islands, October 1943One of the successful pilots flying with 2nd FS was Cpt.Luis Zendegui who scored his first victory on December 25,1942, during the dogfight with Mc.202. During his servicewith 2nd FS he was credited with three confirmed killsand he damaged another two enemy aircraft. Zendegui’sSpitfire carried the pilot’s name on the drop tank andthe American flag on the fuselage sides. The originalBritish cockades on wings and fin flash on the verticaltail surface remained intact. The squadron white codesQP were not yet applied on Spitfires during this period.Some sources assign serial number ER148 to this Spitfire,however it cannot be found in the database of the Spitfires’serial numbers.No. 352 (Yugoslav) Squadron was the first Yugoslav fighterunit established at Royal Air Force in Mediterraneanduring WWII. This unit is also known as the Prva EskadrilaNOVJ. In June it converted to Spitfires Mk.Vb/Vc andin August the unit was transferred to Italy to join RAFNo. 281 Wing and provide the escort for the fighter-bombersquadrons. As of January 25, 1945, it was deployed to theforward base on the island of Vis. Due to the absence ofthe Luftwaffe aircraft the Yugoslav Spitfires had very littleopportunities for the air combat and for the rest of warthey flew the ground attack missions. Šoić’s Spitfire MH592sported the type “B” desert camouflage scheme and asthe only Yugoslav Spitfire featured the Aboukir dust filter(the rest of the aircraft featured Vokes filters). Also, HinkoŠoić as one of very few Yugoslav pilots encountered theenemy aircraft and in the cooperation with another threepilots shot down a Henschel Hs 126 on March 20, 1945. Inthis Spitfire he flew 73 missions altogether, further sixmissions were flown by other No. 352 (Yugoslav) Squadronpilots.Spitfire serial number EE835 arrived in Australia onApril 13, 1943. Before it was delivered to the combat unitit had been repainted in Foliage Green/Earth Brown/SkyBlue. In May it was handed over to the No. 79 SquadronRAAF as A58-137 and the code letters UP-T were applied.It was assigned to F/Lt David Hopton who christened hisnew Spitfire by the phrase “Down with everything” andhad a naked girl painted on the port side of the fuselage.Hopton flew this Spitfire until November 28, 1943, whenthe fuselage drop tank was not released correctly anddamaged the aircraft’s tail. The repaired airplane wasreturned to the service in October 1944, assigned to No. 85Squadron and coded SH-W. The camouflage was stripped,and it flew in the natural metal color finish. On February26, 1945, during the landing at Guildford, the pilot F/OB. O’Connell collided with another Spitfire and A58-137was struck off charge.KITS 03/2023INFO Eduard34March 2023Page 35
Recommended:for Spitfire Mk.Vc TROP 1/48481065 Spitfire Mk.V landing flaps (PE-Set)FE1207 Spitfire Mk.V seatbelts STEEL (PE-Set)644113 Spitfire Mk.V LööK (Brassin)648098 Spitfire wheels - 5 spoke (Brassin)648119 Spitfire wheels - 5 spoke, smooth tire (Brassin)648663 Spitfire Mk.V cockpit (Brassin)648664 Spitfire Mk.V wheels (Brassin)648666 Spitfire Mk.Vc gun bays (Brassin)648667 Spitfire Mk.V three-stacks exhausts rounded (Brassin)648668 Spitfire Mk.V three-stacks exhausts fishtail (Brassin)648669 Spitfire Mk.V six-stacks exhausts fishtail (Brassin)648671 Spitfire Mk.Vc undercarriage legs BRONZE (Brassin)648738 Spitfire Mk.V landing flaps PRINT (Brassin)D48088 Spitfire Mk.V stencils (Decal Set)Cat. No. 648671Cat. No. 644113Cat. No. 648666Cat. No. 648119Cat. No. 648667Cat. No. 648663OVERTREES#82158XSpitfire Mk.Vc/Vc TROP1/48Product pageOVERLEPT#82126-LEPTSpitfire Mk.Vc TROP PE-Set1/48Product pageKITS 03/2023INFO Eduard35March 2023Page 36
GUADALCANALLimited edition kit of US carrier basedfighter F4F-4 Wildcat early and lateproduction in 1/48 scale. Kit presentsWildcats from United States Navy andMarine Corps participating in the fightingfor Guadalcanal.plastic parts: Eduardmarking options: 12decals: EduardPE parts: yes, pre-paintedpainting mask: yesresin parts: noProduct page#111701/48KITS 03/2023INFO Eduard36March 2023Page 37
Lt. Stanley W. Vejtasa, VF-10, USS Enterprise,April 1943BuNo. 5192, Ens. Mortimer Kleinmann jr.,VF-5, USS Saratoga, AugustCapt. Joseph J. Foss, VMF-121, Henderson Field,Guadalcanal, October–November 1942Unusual surname and blond hair were equally responsiblefor the nickname “Swede” for Stanley Winifield Vejtasa,a man with strong Czech roots as a grandson ofimmigrants from then part of the Austria-HungaryEmpire. He made himself famous when he managed toshoot down three Zeros while leading a formation ofeight SBD-3s tasked with the air cover of the US shipsduring the Battle of the Coral Sea. This achievementgave him opportunity to join VF-10 fighting squadronas its Operations Officer. There he scored seven morekills during the Guadalcanal campaign on board of theUSS Enterprise. After the war he enjoyed a great career,making him the Captain of USS Constellation and CO ofthe Miramar base. He retired in 1970 and died on January23, 2012, at the age of 98. The Wildcat No. 79 took overthe starboard side panel with eight kill marks from theNo. 19 (BuNo. 03417) Vejtasa used before. Ninth kill markwas added on November 13, when he shot down onehuge Kawanishi Type 97 Mavis flying boat. Some of theWildcats sported the kill marks on both sides, but onlystarboard of this Wildcat is known. This hangs questionmark on their port side presence. Also, the white verticalrudder strip is not sure for the period of the early 1943.This is a reconstruction of the aircraft, assigned to andusually flown by Ens. Mortimer “Junior” Kleinmann. Buton August 7, 1942, during the rush to take off againstJapanese bombers as soon as possible, Lt. James Julien“Pug” Southerland jumped the plane and took it off againstthe enemy. He managed to shoot down two bombers butduring the consecutive dogfight with Zero he learned hisguns would not fire, probably due to the damage from fireby the tail gunner of the bomber. To make the things evenworse, two more Zeros joined the fight. Pug was able tooutmaneuver them, but the melee was spotted by SaburoSakai. The Wildcat was hit by numerous shells frommachine guns and cannons, but kept flying, until a Zerogave him a burst into the left-wing root setting it afire.“Pug” bailed out over the enemy territory of western partof Guadalcanal. Wounded and weaponless he managedto escape the Japanese soldiers thanks to the help ofnatives and was evacuated from Henderson Field onAugust 20, 1942. Later he added three more victories withF6F-5 and died in flying accident on October 12, 1949.Mortimer Kleinmann achieved two kills during the timeUSS Saratoga was taking part in Guadalcanal campaign.This is one of the Wildcats of VMF-121 the highest-scoringace of the Guadalcanal campaign, Capt. Joseph JacobsFoss, used during the combat missions. The Bureau Numberis unknown, but we know Foss scored with nine differentWildcats. This speaks of itself as the Marine pilots onGuadalcanal did not have the luxury of assigned aircraft. Noteven the best ones. The fierce combats, harsh environmentand other factors made the Wildcats rather consumablegoods, and the pilots simply jumped the closest airworthyaircraft. Joe Foss, former flying instructor, joined VMF-121on August 11, 1942 and was promoted to Captain on the sameday. He arrived at Guadalcanal on October 9 and four dayslater scored his first victory, shooting down a Zero. His scorewas rising, as he shot down 16 enemies during October andprior to his farewell to the island his score raised to 23. Hehad to bail out himself on November 7 after shooting downone Rufe and two float biplanes and made it back to the basein three days. The VMF-121 left Guadalcanal on November19, but Joe returned to Guadalcanal for his final tour therefrom January 1 to January 26, 1943. Adding three more kills,he became the highest scoring USMC ace of WWII. Afterthe war, he served in the South Dakota Air National Guard,which he helped to organize. Later he turned to politics andwas elected to the South Dakota House of Representativesbut returned to the duty during Korean war. In 1954, Fosswas elected Governor of South Dakota. He passed away onJanuary 1, 2003.KITS 03/2023INFO Eduard37March 2023Page 38
BuNo.02062, Mach. Donald E. Runyon, VF-6,USS Enterprise, September 19421/Lt. Jefferson J. DeBlanc, VMF-112/121, Henderson Field,Guadalcanal, January 1943Guadalcanal, Henderson Field,early 1943Donald Eugene Runyon was a petty officer AviationMachinists Mate 1/c and he was so skilled he had officersfor wingmen. He scored six times with Wildcat. This oneserved him well to get two of his victories at the verystart of the Guadalcanal campaign on August 8, when heshot down Zero and Betty. A day before, he also shot downtwo enemies with aircraft BuNo. 02125. He joined VF-3 inDecember 1942 and stayed with the unit until April 1943.He did not achieve any aerial victories with the unit, butthe things changed when he joined VF-18 based on theUSS Bunker Hill in September 1943. There, already flyingHellcats, he added three more kills to finish the war with11 victories. He was promoted to Lieutenant (junior grade)rank in May 1943 and to Lieutenant on July 1, 1944. He wasa test pilot at Moffett Field from July 1945 to July 1946 andserved with several units until July 1964, when he retiredin the rank of Commander. The Wildcat BuNo. 02062 sportedthe unusual painting of the tombstone with 41 Japaneseroundels symbolizing total score of the VF-6 during theirfighting of Guadalcanal Campaign. Such a painting sportedonly nine Wildcats of the unit, the ones which stayed on thedeck of the USS Enterprise on her route from the Solomonsto Hawai. Other Wildcats were flown to USS Saratoga or toGuadalcanal.During his two tours of duty, Jefferson Joseph DeBlancscored nine kills in the combats during the Guadalcanal andOkinawa campaigns. That made him 11th highest scoringMarines ace. During his mission on January 31, 1943, whenescorting SBSs to attack Japanese ships, he detecteda serious fuel leak, which made his return to baseunlikely. He requested that rescue forces be altered andcontinued the mission, which resulted in a fierce combatwith Japanese Ki-43 Oscars. DeBlanc managed to shootdown five of them but was wounded and had to bail outhimself from his crippled and smoking Wildcat. After manymishaps he finally managed to get back to the base and tothe hospital on February 12. This Wildcat also received anenemy burst. It happened on November 12, 1942, with 1/Lt.Sam Folsom at the controls. He managed to get it home andthe Wildcat was repaired. Mechanics used white aircraft-fabric patches to cover the bullet holes, but the patcheslost their white color soon in harsh, dusty environment…DeBlanc was one of the pilots to use it, although it wasassigned to VMF-121, while he was a member of VMF-112.Although good photos of this Wildcat are available, there aremany questions regarding its identity. Usually, the aircraftis referred to 1/Lt. Marion Carl of VMF-223 or the CO ofthis unit, Maj. John L. Smith. Both were bright stars of theearly stage of the Guadalcanal campaign amongst USMCpilots. The VMF-223 was the first one to land on HendersonField together with VMSB-232. From August 20 they werefrantically fighting Japanese aircraft until late October.Carl got 16,5 of them, Smith 19. That’s one of the reasonsthis Wildcat is sometimes referred to latter, as it sports 19kill marks. But the photos are dated to February 1943 whenthe VMF-223 was gone from Guadalcanal. According tosome sources, Carl himself stated this aircraft was a non-airworthy aircraft he used for photo session with media atEspiritu Santo, following the end of the tour on Guadalcanal(i.e., in second half of October). Together with a mechanic,they reportedly put 19 kill mark stickers on. But there are nophotos of Carl with this aircraft or in the cockpit ... More toit, other photos show visibly stained kill marks, one of themdated to March 22, 1943. Conclusion? It might be operationalaircraft changing units and sporting the kills of all the pilotsflying it. Or it might be really used for some photo sessionon Espiritu Santo in late October, but repaired and sent toGuadalcanal, keeping these kill marks applied. There wererepairs on the right wing and on the fuselage, while roundelon the upper side of the left half of the wing showed somedamage.KITS 03/2023INFO Eduard38March 2023Page 39
Nose arts were rare on the Navy and Marines aircraft,especially during the Guadalcanal campaign, where wasno time or resources to “play” with drawings. The Wildcatwith the painting of Popeye on the port side of the enginecowling is one of rare exceptions, but it was not paintedon Guadalcanal. In fact, the aircraft was part of theVMF-111 inventory, the unit which was operating on Samoa.Sam Folsom had the Popeye painted on the engine cowlwhen he was assigned to the unit as an instructor afterhis combat tour at Guadalcanal. The aircraft is sometimesportrayed with “winged” roundels, which is not correct.At the time the photographs of the Popeye Wildcat wereshot, is still sported the original roundels. Folsom wasrather inexperienced pilot when he was thrown withothers of VFM-122 into the battle of the Solomon Islands,but he was progressing rapidly. He stayed there for threemonths and was wounded twice. He scored his first kill onNovember 11, when he shot down a Zero. Just a day later,he shot down a Mitsubishi Betty bomber and added anotherone to finish the war with three victories.Bill Leonard took part in the battles at Coral Sea andMidway, where he made himself an ace during his servicewith VF-42 and VF-3. In August 1942 he joined new VF-11squadron and became its Operations Officer. He servedat Guadalcanal in 1943 and added two more kills to histally. It happened on June 12, 1943, when he shot downtwo Zeros flying this aircraft and this achievement madehim the ace. After his three-month tour in Guadalcanal, hewas transferred to Samoa, ending his time with VMF-121.Leonard’s Wildcat sported the Sun Downers symbol paintedon both sides as well as four kill marks (six after June12). The panels with the VF-11 symbol and port side underthe cockpit were repainted, probably by fresh camouflagecolor. The same pays to the area of the fuselage code.BuNo. 12034, VMF-221, Henderson Field,Guadalcanal, February 19431/Lt Samuel B. Folsom, VMF-121,Samoa, spring 1943BuNo. 11985, Lt. (jg) William N. Leonard,VF-11, Guadalcanal, June 1943This aircraft is usually attributed to 1/Lt. James E. Swett,a member of VMF-221. The squadron was based at MarineCorps Base Ewa on Oahu, Hawai in early 1943, from wherethey moved to the island of Espiritu Santo aboard the USSNassau. Most probably during their stay at Espiritu Santo,various arts were painted on the vertical fins of some ofthe squadron’s Wildcats. In the case of No. 77, the paintingwas probably inspired by “Hairless Joe” from Al Capp’sstrips made for L’il Abner satiric strips (it was paintedon the port side only). The squadron was moving toGuadalcanal in stages from February 1943 and there the“tail arts” became a thorn in the side of the commandingofficers. So, probably not long after arrival, an orderwas issued to remove all the paintings. Lt. Swett wasa leader of one of flights of VMF-221. He took off for hisfirst combat flight on April 7 when the Japanese madea massive raid, sending approximately 70 bombersagainst Guadalcanal, covered by more than hundredZeros. More than a hundred of American naval and Armyfighters took off to defend the island, and the mostsuccessful among them was Swett, who managed toshoot down seven Val bombers before having to bail outhimself. This was his only encounter with enemy aircraftin the cockpit of a Wildcat, as he subsequently switchedto the Corsair and achieved 15.5 kills during his 103 totalcombat missions in WW II.KITS 03/2023INFO Eduard39March 2023Page 40
Lt. (jg) Francis R. Register, VF-11, VC-21,USS Nassau, May 1943VF-11, Guadalcanal, May 1943Lt. (jg), Charles R. Stimpson, VF-11,Guadalcanal, June 1943Francis Ronald Register enlisted to Navy on February 17,1941, and joined the VF-3 squadron on January 4, 1942.While still on USS Saratoga, he changed the unit for VF-6and saw combat in the Eastern Solomons. He managedto shoot down two aircraft on August 24, one of themidentified as Zero and the other strangely as “Me 109”.After the Saratoga was torpedoed on August 31, he joinedVF-5, based at the Guadalcanal, and added two morevictories on September 12 and 13. Two weeks later heentered the prominent club of fighter aces by shootingdown two Zeros and prior to leaving the “Death Island”,he added two more victories and one probable. On March23 “Cash”, as was his nickname joined his old VF-3 unitbut was detached to Composite Squadron 21 (VC-21) justfour days later. On board of USS Nassau, he was set toparticipate in the Aleutian Campaign, but perished there inthe flying accident. The aircraft he boarded the USS Nassausported seven kill marks from the Gauadalcanal, and thewhite stripes on the horizontal and vertical stabilizers,distinguishing the aircraft of the fights for Attu Island.Register’s diary describing in the raw manner the harshliving on Guadalcanal is available on Internet.As there were not too many possibilities and opportunitiesto adorn the aircraft with any personal paintings, theWildcats on Guadalcanal were uniform regardless theunit. But there were some attempts to make the aircraft atleast a little bit specific by easier means. This F4F-4 is anexample as the page from the 1943 Esquire calendar withthe January girl painted by the famous Alberto Vargas wasglued to the port side of the engine cowling. More to it,on starboard side the inscription “Nylorac” was painted(a slang word meaning somebody who gets close personally,then betrays and hurts you). The short movie showsLt. Gordon Cady standing by this Wildcat, but it is the onlyindication about any link between this Wildcat and him.The VF-11 was divided into flights of four aircraft and Cadywas leading the second one, which assigned his aircraftnumber 5, while No. 17 was the aircraft of the leader of the5th flight, Lt. Raymond “Sully” Vogel. But Vogel damagedhis Wildcat in the collision with the aircraft of Lt. (jg)Maxwell on May 2, 1943 and “the new No. 17” might bethe Nylorac … Cady shot down two Zeros and Vogel addedanother one kill in the same combat on June 7.Charles Russell Stimpson was 16-victory ace, rankinghim eighth in the Navy list of aces, sharing this positionwith Ira Kepford. Stimpson enlisted in the Navy on June17, 1941, the pilot training followed. He joined newly formedVF-11 in the summer of 1942 and served with the unit untilFebruary 1945. He served at Guadalcanal from May to July1943, achieving six victories there. His maiden fightersuccess came on June 16, when he shot down four Valsflying this aircraft. According to some sources, he wasflying Wildcat BuNo. 12163 at the time. Four kill markswere applied under the cockpit of the aircraft named“Missie” of the unknown BuNo. It might be the 12163 but itis not certain. Stimpson shot down two Zeros in July 1943in the cockpit of the same aircraft and added ten morekills in 1944, while still with VF-11 but flying Hellcats. Afterserving as a flight instructor from April to September1945, he was released from active duty on October 11, 1945.KITS 03/2023INFO Eduard40March 2023Page 41
Recommended:for GUADALCANAL 1/48481093 F4F-4 landing flaps (PE-Set)FE1290 F4F seatbelts STEEL (PE-Set)644164 F4F-4 LööK (Brassin)648756 F4F 42gal ventral drop tank PRINT (Brassin)648769 F4F gun barrels PRINT (Brassin)648779 F4F undercarriage legs BRONZE (Brassin)648803 F4F-4 cockpit PRINT (Brassin)648815 F4F-4 wheels early (Brassin)648816 F4F-4 wheels late (Brassin)648817 F4F-4 landing flaps PRINT (Brassin)648818 F4F-4 folding wings PRINT (Brassin)648820 F4F-4 exhausts PRINT (Brassin)648828 F4F-4 engine PRINT (Brassin)648829 F4F-4 wheel bay PRINT (Brassin)3DL48090 F4F-4 SPACE (3D Decal Set)EX904 F4F-4 TFace (Mask)OVERLEPT#11170-LEPTGUADALCANAL PE-set1/48Product pageCat. No. 644164Cat. No. 648756Cat. No. 648820Cat. No. 648828Cat. No. 648817Cat. No. 648815Cat. No. 648803Cat. No. 648769KITS 03/2023INFO Eduard41March 2023Page 42
Page 43
WNr. 5819, Obstlt. Adolf Galland, CO of JG 26,Audembert, France, October–December 1940WNr. 1559, Hptm. Wilhelm Balthasar,CO of 7./JG 27, Carquebut, France, July 1940WNr. 5587, Ofw. Fritz Beeck, 6./ JG 51,Wissant, France, August 1940Adolf Galland, the ace and future General, flew theportrayed Emil during through fall of 1940 up to thebeginning of 1941. He was CO of III. Gruppe at the time,later he took command of the entire JG 26. The tacticalmarkings on the aircraft kept pace with these promotions.The standard camouflage of RLM 02/71/65 was darkenedon the fuselage sides with RLM 02/71. The yellow cowlingwas complemented by the yellow rudder which alsosported kill marks. The surface area of the original RLM65 was not large enough for them, and so the yellowwas oversprayed with fresh RLM 65 for the next row ofkill marks. The most typical changes for WNr. 5819 at thistime came with the personal emblem of Mickey Mouseand most of all the installation of the ZFR-4 telescope(installed together with the regular Revi). It didn’t serveas an actual sight as it did for the identification of distantaircraft. After the death of Werner Mölders Gallandreplaced him as the German fighter force commander(General der Jagdflieger). Later he became famous forlocking horns with Hermann Göring. He established JV 44at the end of the war, the unit well known for its Me 262 jetfighters and colorful Fw 190Ds. Galland managed to shootdown 104 enemy airplanes and was awarded with KnightCross with Oak Leaves, Swords, and Diamonds.The future Knight Cross with Oak Leaves recipient WilhelmBalthasar was born on February 2, 1914, in Fulda. In 1933 hejoined Reichswehr, in 1935 he was transferred to Luftwaffeby his own request and underwent the pilot training. Duringthe Spanish Civil War, he initially served with bomber andreconnaissance units, since September 1937 with fighterdetachment of the Legion Condor. In March 1938 he returnedto Germany. At the outbreak of World War II Oblt. Balthasarserved as 1. Staffel JG 1 commander. This unit saw combat forthe first time during the offensive against The Netherlands,Belgium and France. It was the time when Balthasardemonstrated his marksman skills as he shot down 23enemies during the Western Europe campaign. As of June 5,1./JG 1 was re-designated as 7./JG 27. On September 1, 1940,he was promoted to command III./JG 3 and in the air battlesover the Southern England he achieved further seventeenkills. In the meantime, on February 16, 1941, he was appointedCommanding Officer of JG 2. Balthasar run out of his luckduring the combat with the RAF fighters over Aire on July 3,1941. In the dive, the wing of his Bf 109F-4 wing collapsed andBalthasar perished at the impact with the ground. Balthasar’saircraft, camouflaged in RLM 71/02/65 colors, carried thenon-standard marking on the engine cowling. There isa unit marking painted under the windshield, kill markingsare painted on the vertical tail surface and rudder.Simple but effective camouflage adorned this aircraft thatwas shot down with Ofw. Fritz Beeck at the controls in thevicinity of East Langdon shortly after noon on August 28,1940. It was during the second escort mission of the daythat culminated in combat with RAF fighters in which theengine of Yellow 10 was hit. After an unavoidable forcedlanding, the aircraft, in relatively good shape, was madeotherwise by civilian vandals and allied soldiers beforeit could be inspected by RAF experts. Light blue sides ofthe RLM 02/71/65 fuselage scheme were sprayed with theupper surface colors. Yellow identification colors, typical formid-August 1940, were applied to the wing tips, horizontaltail surfaces, and top portion of the fin. Because the aircraftin question belonged to 6. Staffel, tactical numbering andthe background II./JG 51 “Gott strafe England” emblem wereyellow. Three victory marks on the left side were in white.It is not out of the question that these also appeared on theright side, but documentation is lacking.KITS 03/2023INFO Eduard43March 2023Page 44
WNr. 5901, Oblt. Walter Fiel, CO of 8./JG 53,Le Touquet-Etaples, France,September 1940Lt. Josef Eberle, 9./JG 54, The Netherlands,August 1940WNr. 2060, Lt. Hans Guse, 2.(J)/LG 2, Tudora,Soviet Union (Republic of Moldova today),July 1941After the Luftwaffe tactics changed during the Battleof Britain, when the bombing of London and SouthernEngland was switched to night operation, the decisionwas made to use certain Staffels in the fighter-bomberroles and to lure RAF fighters into combat. One of theseunits was 8. Staffel JG 53 commanded by Oblt. Fiel. OnOctober 2, during his unit’s attack, he was attackedby superiority of Spitfires. His aircraft was damagedand made to force-land nearby the little town of EastPeckham in the Kent County. The pilot was takena prisoner of war. The camouflage in RLM 71/02/65colors was supplemented by the gaudy marking in theform of yellow engine cowling and rudder. The originalaircraft’s marking was probably oversprayed withRLM 70 color, the unit marking, originally located onthe engine cowling, was overpainted in the red stripewrapping around the whole engine cowling.A very interesting camouflage was created in thesummer of 1940 by the ground staff of JG 54 on manyof unit’s aircraft in an attempt to darken the light bluefuselage sides of their Bf 109Es. To achieve such aneffect, they sprayed vertical to diagonal stripes withRLM 71 paint. The standard scheme of RLM 02/71/65was applied along with the quick identificationelements. The period scheme was applied to Yellow13 with which Lt. Josef Eberle managed to cross theChannel and belly land in France despite personalinjury on August 12, 1940. The wingtips and fin ofEberle’s aircraft were painted RLM 27 Yellow, whichwas lighter than the color of the spinner, tacticalnumber and background of the III./JG 54 emblem. Thewhite color cannot be ruled out on the wingtips andfin as well. The bottom wing RLM 65 color extendedmarginally to the upper surface. Some sourceserroneously identify this aircraft as an E-3. Despitehaving tempted fate once over the Channel, Eberlewas not as successful on October 9, 1940, when he losthis life in combat with RAF fighters.Like JG 77, Lehrgeschwader 2 was withdrawn fromthe combat operations after the end of the Greekcampaign for rest and rearmament, which was to takeplace in Belgrade. This was followed in mid-July bya move to Romanian territory, where LG 2 equipped byMesserschmitts Bf 109E (some in the fighter-bomberconfiguration) was on alert to be deployed againstthe Soviet Union. It joined Operation Barbarossa in theearly hours of July 22. The Black 10, which retained itscamouflage from the battles over Greece and Creteand was equipped with a tropical filter, was shot downon July 10, 1941, by Soviet I-16s. The pilot is still listedas missing in action. The markings of the aircraft arecomplemented by the insignia of I.(J)/LG 2 under thewindshield and 2.(J)/LG 2 on the side behind the fuselagecross.Recommended:for Bf 109E-4 1/72D72030 Bf 109E stencils (Decal)OVERTREESOVERLEPT#7033XBf 109E-4/71/72#7033-LEPTBf 109E-4/71/72Product page Product pageKITS 03/2023INFO Eduard44March 2023Page 45
Bf 110G-2Weekend edition kit of German WWII twin-engine multi role aircraft Messer-schmitt Bf 110G-2 in 1/72 scale. This version of the Messerschmitt Bf 110 wasused in the role fighter-bomber, fast bomber and destroyer, often used again-st Allied heavy bombers, equiped with WGr. 21 rockets or BK 3,7 cannon.plastic parts: Eduardmarking options: 4decals: EduardPE parts: nopainting mask: noresin parts: no#74681/72Product pageKITS 03/2023INFO Eduard45March 2023Page 46
Bf 110G-2/R7/M2, 6./ZG 1, Brest, France, August 1943Bf 110G-2/R3/M1/M5, 7./ZG 26, Fels am Wagram, Austria, May 1944Bf 110G-2/M1/R7, 5./NJG 200, Nikolayev, Soviet Union, September 1943In August 1943, 6./ZG 1 moved from Sicily to Brest,France, where the unit was tasked with escorts ofGerman submarines on their way across the Bayof Biscay to the Atlantic. The standard camouflagescheme of RLM 74/75/76 colors was darkened on thefuselage sides with patches of the same colors. Theunit’s emblem was a drawing of a wasp on the nose,additionally supplemented on the left side of thefuselage under the cockpit by a drawing of a witch onthe S9+LP. The color of the 6. Staffel was yellow hencethe aircraft code is yellow and the same appliesto the color of the spinner. The aircraft had alsoa white stripe on the fuselage in front of the tailsurfaces, which was a remnant of the unit’s timeon the Southern Front in Italy.Due to the intensification of Allied air raids from Italyon the southern areas of the German Reich, 7./ZG 26was relocated to Fels am Wagram airfield in May1944. The unit’s aircraft had the tips of the spinnerand the third letter in the code painted white, whichwas the color of the 7. Staffel. The black code letterK was painted also on the bottom of the wingtips. The3U+KR sported a white fuselage stripe in front of thetail surfaces and white bottom of wing tips. Both werethe designation of aircraft operating on the southernfront. Two MK 108 guns of 30 mm caliber mounted inthe nose were the Rüstsätze 3 kit add ons. Additionalarmament were WGr. 42 rocket launchers under thewing.In September 1943, 5./NJG 200 was based on theairfield near the town of Nikolayev in Ukraine.The pilots were tasked with night interception ofVVS (Soviet Air Force) aircraft. This machine wascamouflaged with standard RLM 74/75/76 colors.The distinguishing color of 5. Staffel was red henceboth the codes and the tips of the propeller coneswere painted so. The aircraft had a yellow stripe onthe fuselage in front of the tail surfaces, which wasa distinguishing feature of machines operating onthe Eastern Front and in the USSR.KITS 03/2023INFO Eduard46March 2023Page 47
72729 Bf 110G-2 (PE-Set)SS798 Bf 110G-2 Weekend (PE-Set)672013 Bf 110G wheels (Brassin)672115 SC 50 German WWII bombs (Brassin)672292 Luftwaffe rudder pedals PRINT (Brassin)CX644 Bf 110G-2 (Mask)Bf 110G-2/R1, 4./ZG 76, Wertheim, Germany, October 1943Dispersed Zerstörer units were called up from all overEastern Europe and the Mediterranean to be incorporatedinto the defense of the Reich. ZG 76 was rebuilt in southernGermany with the use of the personnel of training andreconnaissance units and ZG 76 stayed there throughthe winter of late 1943/44. Its aircraft were armed witha 37 mm BK 3.7 cannon under the fuselage and WGr. 42rockets to scatter American bomber formations. OnOctober 4, 1943, the American Eighth Air Force attackedtargets in Frankfurt am Rhein. II./ZG 76 encountered thestream of bombers alone and shot down four Americanbombers. But they encountered the American 56thFighter Group afterwards and without their own fighterescort nine Bf 110s were shot down in the ensuing battle.Eleven of the downed crews were killed and sevenwounded. The introduction of the American long-rangefighter escort meant a large increase in losses for theZerstörgeschwader units. In November 1944, 4./ZG 76 wasdisbanded and its pilots were retrained on the Bf 109,subsequently transferred to the 9./JG 54 fighter unit.Recommended:for Bf 110G-2 1/72Cat. No. 672292Cat. No. 672115Cat. No. 672013KITS 03/2023INFO Eduard47March 2023Page 48
Page 49
MiG-21BIS, c/n 75084300, HävLLv 31, Kuopio airbase, Finland, 1980 – 1981MiG-21bis, c/n 75080880, 1 Pucki DLMW, Lotnictwo Marynarki Wojennej,Gdynia-Babie Doły, Poland, late 1997MiG-21bis, c/n 75061874, 47 Pápa Harcászati Repülő Ezred, Pápa airbase,Hungary, 1991This aircraft was accepted for service on July 17, 1980 andassigned to 31 Fighter Squadron (Hävittäjälentolaivue 31,abbreviated HävLLv 31). It became the last of six FinnishMiG-21BIS fighters to be modified for reconnaissance tasks.After the modification, the aircraft was assigned to TiedLLv(Reconnaissance Squadron) and following its end of service itwas used as a teaching aid at the Technical School located atthe Kuopio Air Base. The aircraft is shown as it appeared between1980 and 1981 before being upgraded by western avionics, whichincluded cockpit instrumentation. Unlike other users, Finlandused capital letters for designation of their MiGs, that’s why it iswritten as BIS here as well.This aircraft was delivered to Poland on March 22, 1980 and wasassigned to the 1 Pucki Dywizjon Lotniczy (Air Division) of thePolish Naval Forces. The emblem on the tail surface indicatesservice with the 2nd Eskadra (Squadron) of the Division. Thelook of the plane evolved over time, and in 2001 it flew witha sharkmouth and a tiger motif on the brake chute housing.MiG-21bis, serial number 75061874, served with the 47Combat Regiment (Harcászati Repülõezred). In 1991, it receiveda temporary white coloring on the rear of the fuselage anda portion of the bottom. In this guise, it took part in DACT(Dissimilar Air Combat Training) exercises, in which the opposingaircraft pitted againt each other were of differing types. Later, itwas assigned to the “Sky Hussars” demonstration team. In 2006,it was mothballed and put in storage at Papa, and in 2007, it wassold into the private collection of Gerhard Neumann Museum atNiederalteich in Germany.KITS 03/2023INFO Eduard49March 2023Page 50
MiG-21bis, Tactics & Air Combat Development Establishment,Jamnagar airbase, India, September 1986MiG-21bisD, c/n 75002075, 22 eskadrila lovačkih zrakoplova, Pula airbase, Croatia, 2008MiG-21bis, No. 3 Air Base, Graf Ignatevo, Bulgaria, from 2002The aircraft coded C2305 was assigned to the Center for thedevelopment of tactics for aerial combat and served there duringSeptember 1986. The front of the aircraft referred to its formeruser, No. 4 Squadron of the IAF. This unit was dubbed “Oorials”after the local type of mountain sheep. Together with the unit’smotto, “Honor over Death” this symbolizes stamina, strength, anda fighting spirit. The colorful paint scheme of Indian MiGs wasused during one of the military exercises.This aircraft was one of a number of MiG-21s purchased in thefirst half of the nineties despite a UN embargo from the Ukraine.The first unit to use the aircraft was the 22 eskadrila lovačkihzrakoplova (Fighter Squadron) based at Pula. In 2003, this wasone of eight MiG-21bis aircraft to be modernized in Romania byAerostar to MiG-21bisD standard. Later, the plane was observedat Zagreb, Tchakovec and Zadar. It carries a typical camouflagescheme for the modernized bisD aircraft.MiG-21bis serial number 75094114 was delivered to Bulgaria in1983. The first user of the aircraft was the 19 Fighter Regiment.From 2002, it served at Air Base No. 3 based at Graf Ignatevo,where the MiG-21s shared the base with the more modernMiG-29s. The last MiG-21bis delivered directly from the factorywas retired from the Bulgarian Air Force in 2015, while thesecond-hand aircraft from the Soviet Air Force delivered in 1990were retired in 2000.KITS 03/2023INFO Eduard50March 2023Page 51
OVERTREESOVERLEPT#8234XMiG-21bis1/48#8232-LEPTMiG-21bis PE-Set1/48Product pageProduct pageRecommended:for MiG-21bis 1/4848704 MiG-21 ladder (PE-Set)48994 MiG-21 surface panels (PE-Set)48999 MiG-21bis exterior (fotolept)491036 MiG-21bis interior (fotolept)644033 MiG-21bis LööK (Brassin)648026 MiG-21 wheels (Brassin)648030 MiG-21 seat late (Brassin)648050 MiG-21BIS interior (Brassin)648051 MiG-21BIS exhaust nozzle (Brassin)648082 R-60 / AA-8 Aphid (Brassin)648049 MiG-21 wheel wells (Brassin)648064 MiG-21 late airbrakes (Brassin)648080 MiG-21 undercarriage legs BRONZE (Brassin)648490 MiG-21 F.O.D. (Brassin)3DL48026 MiG-21bis SPACE (3D Decal Set)Cat. No. 644033Cat. No. 648050Cat. No. 648051Cat. No. 648490Cat. No. 648080KITS 03/2023INFO Eduard51March 2023Page 52
Page 53
B.534.208, 36th Fighter Squadron, Air Regiment 2, Olomouc Airfield,Czechoslovakia, Fall 1937B.534.186, 34th Fighter Squadron, Air Regiment 4, Hradec Králové Airfield,Czechoslovakia, Summer 1937B.534.239, 45th Fighter Squadron, Air Regiment 3, Piešťany Airfield,Czechoslovakia, July 1938This aircraft is representative of the camouflage schemeused by Avia at the end of the Thirties, prior to the MunichCrisis. Upper surfaces are khaki, lower are silver doped,typically a matted shade. The lower surface of the upperwing is also khaki. The blue and white Moravian eagleidentifies the aircraft as belonging to the Air Regiment 2,while the letter G identifies membership within the 36thSquadron, and the numeral 1 specifies the aircraft withinthe Squadron. The blue tipped spinner was also a squadronidentifier, although this was not an official marking.This aircraft is known to have crashed on September 6,1937, piloted by četař (Sergeant) Julius Zaoral, followinga collision with another Avia B.534.35, with svobodník(Private First Class) Jaroslav Šodek at the controls.B.534s of the Air Regiment 4 are among the more strikingwithin the pre-war Czechoslovak Air Force. The color detailsare not known for certain, and this arises from uncertaintiesregarding the remarking of squadrons at the end of theThirties. These could have been either blue and yellow orgreen and yellow. The colors on the wheel spats wouldbe consistent, and so would, likely, the lower prop bladebandaging. This aircraft is known from photographs likelytaken during the course of 1937, when attached to 34thFighter Squadron, which utilized blue and yellow trimming.In January 1938, she was re-designated as belonging to50th Fighter Squadron, with the fuselage code K. Coded D,she was then attached to 42nd Squadron, which used greenand yellow colors. The aircraft has a tail skid instead of a tailwheel. The lower surface of the upper wing is silver doped.This aircraft carries the standard Czechoslovakcamouflage scheme from the late Thirties. Thelower surface of the upper wing is in khaki, and thespinner is yellow. The aircraft was documented ona photograph dated July 14, 1938, when it sufferedlight damage while flown by desátník (corporal)Baláš. At the time, these aircraft carried no squadroncodes. The Air Regiment 3 was the only one that waslocated in Slovakia prior to the outbreak of the war.After the dissolution of Czechoslovakia, Air Regiment3 aircraft were incorporated into the services of thenewly formed Slovak Air Force. In this service, AviaB.534s took part in combat operations in Poland andlater in the Soviet Union. In August 1944, the SlovakNational Uprising saw the remaining Avias take partin anti-German operations.KITS 03/2023INFO Eduard53March 2023Page 54
B.534.217, Combined Squadron of Slovak National Uprising, Tri Duby Airfield, Slovakia, September 1944In the fall of 1944, the Slovak National Uprising sawthe use of several Avia B.534s. This specific aircraftis the only one photographically documented withthe national markings used during the uprising.These were composed of the original Czechoslovakroundels with the addition of the Slovak two-prongedcross. The markings on the right wing are orientedincorrectly with the red field on the right side,i.e. directed away from the fuselage. Also, blue fieldpointing upwards on the rudder is wrongly oriented.It has not been conclusively determined weatheror not the lower wing markings lacked the Slovakcrosses. The aircraft carries the typical camouflagescheme of khaki upper surfaces and silver dopedlower (gray respray of the lower surfaces for thisaircraft is unlikely) and with khaki undersurface ofthe top wing. The aircraft was noted to have beenrather heavily weathered. The tip of the spinner waseither khaki or possibly also heavily weathered.Propeller blades were black on both sides. The topof the nose was likely also khaki, and not yellow.All photographic evidence suggests that the slidingportion of the canopy was missing at the time of theSlovak National Uprising.OVERTREES OVERLEPT#8192XAvia B.534 IV. serie1/48#8192-LEPTAvia B.534 IV. série PE-Pet1/48Product page Product pageRecommended:for Avia B.534 IV. serie 1/483DL48108 B.534 IV. serie SPACE (3D Decal Set)KITS 03/2023INFO Eduard54March 2023Page 55
www.eduard.com/bfcBUNNY BUNNY FIGHTERFIGHTERCLUBEduard's special membership club for all modeling enthusiasts!15% Permanent Club discount at Eduard Store – you will receive permanent 15% discount on all Eduardproducts and also discount on various other non-Eduard products. Fixed, permanent, forever!Unique valuable Club kits and accessories – you will gain access to unique and nowhere else to be soldproducts, specially made for BFC members.Even better prices at Eduard events stand – do you know that Eduard usually has huge discounts ontheir products at fairs and events all over the world? BFC members will have even higher discount atthese events.Club T-shirt – you will receive fancy BFC T-shirt with unique design and special barcode(used for event discounts). This exclusive T-shirt will be only availableto the members of BFC.Free entry fee on E-day – you will not have to pay a penny to visit Eduard's E-day.That means lot of fun at E-day for two days and entry kit, absolutely free!* E-day - INTERNATIONAL SCALE KIT EXHIBITION - IPMS Czech Republic ChampionshipBOX CONTENT:Plastic parts, Marking options 6, Decal Set, PE parts, Maska, Brassinparts (two different types of wheels, landing flaps, dust filter witheyelid, intake ring and RP-3 60lb rockets), 3D decals for main and si-dewalk instrument and control panels with photo-etched details andseat belts.BOX CONTENT:Plastic parts, Marking options 4, Decal Set, PE parts, Maska, Brassinparts (undercarriage wheels, cockpit, exhaust nozzle, FOD).How to become a member of BFC?How to become a member of BFC?Simply by purchasing the Activation product. You will be given 15% discount on (almost) every Eduardproduct in your shopping cart. To apply this discount, the Activation product has to be in your shoppingcart. Activation product is excluded from this calculation.Activation products:Activation products:Tempest Mk. V + T-shirt 1/48MiG-21MF + T-shirt 1/72Page 56
634031Bf 109G-2 LööKplus1/32 RevellBRASSINCollection of 4 sets for Bf 109G-2 in 1/32 scale.Recommended kit: Revell- LööK set (pre-painted Brassin dashboards& Steelbelts)- TFace painting mask- exhaust stacks- undercarriage wheelsProduct pageCollection of 3 sets for Z-326 in 1/48 scale.Recommended kit: Eduard- LööK set (pre-painted Brassin dashboards & Steelbelts)- TFace painting mask- undercarriage wheels644197Z-326 LööKplus1/48 EduardProduct pageINFO Eduard56March 2023Page 57
635023WWII German NOTEK headlights PRINT1/35Product pageBrassin set - NOTEK headlights for German WWII AFVin 1/35 scale. The set consists of 12 pcs of NOTEKheadlights. Made by direct 3D printing.Set contains:- 3D print: 12 parts- decals: no- photo-etched details: yes- painting mask: noBRASSINBrassin set - showels for German WWII AFVin 1/35 scale. The set consists of 3 showels.Made by direct 3D printing.Set contains:- 3D print: 3 parts- decals: no- photo-etched details: yes- painting mask: no635025WWII German shovels PRINT1/35Product pageINFO Eduard57March 2023Page 58
BRASSINCollection of 4 sets for Buccaneer S.2C/D in 1/48 scale.Recommended kit: Airfix- LööK set (pre-painted Brassindashboards & Steelbelts)- TFace painting mask- ejection seats- undercarriage wheels644199Buccaneer S.2C/D LööKplus1/48 AirfixCollection of 3 sets for Beaufort Mk.I in 1/48 scale.Recommended kit: ICM- LööK set (pre-painted Brassin dashboards & Steelbelts)- TFace painting mask- undercarriage wheels644200Beaufort Mk.I LööKplus1/48 ICMProduct pageProduct pageINFO Eduard58March 2023Page 59
BRASSINLööK set - Brassin pre-painted dashboard and STEELseatbelts for Anson Mk.I in 1/48 scale. Easy to assemble,replaces plastic parts. Recommended kit: AirfixSet contains:- resin: 1 part- 3D print: 2 parts- decals: no- photo-etched details: yes, pre-painted- painting mask: no644202Anson Mk.I Löök1/48 AirfixLööK set - Brassin pre-painted dashboardsand STEEL seatbelts for Mi-24V w/ black-paintedinterior (Mi-35) in 1/48 scale. Easy to assemble,replaces plastic parts.Recommended kit: Eduard / ZvezdaSet contains:- resin: 2 parts- decals: no- photo-etched details: yes, pre-painted- painting mask: no644201Mi-24V black (Mi-35) LööK1/48 ZvezdaProduct pageProduct pageINFO Eduard59March 2023Page 60
644203F-35A LööK1/48 TamiyaBRASSINLööK set - Brassin pre-painted dashboard and STEELseatbelts for F-35A in 1/48 scale. Easy to assemble,replaces plastic parts. Recommended kit: TamiyaSet contains:- resin: 1 part- decals: no- photo-etched details:yes, pre-painted- painting mask: no.Brassin set - the engine for F4F-4 in 1/48 scale.The cowling are included. Made by direct 3D printing.Recommended kit: EduardSet contains:- 3D print: 35 parts- decals: no- photo-etched details: yes- painting mask: no648828F4F-4 engine PRINT1/48 EduardProduct pageProduct pageINFO Eduard60March 2023Page 61
BRASSINBrassin set - the undercarriage wheels for AnsonMk.I in 1/48 scale. The set consists of the mainwheels and a tailwheel. Easy to assemble, replacesplastic parts. Recommended kit: AirfixSet contains:- resin: 3 parts- decals: no- photo-etched details: no- painting mask: yes648835Anson Mk.I wheels1/48 AirfixBrassin set - the wheel bay for F4F-4 in 1/48 scale.Made by direct 3D printing.Recommended kit: EduardSet contains:- 3D print: 10 parts- decals: no- photo-etched details: no- painting mask: no648829F4F-4 wheel bay PRINT1/48 EduardProduct pageProduct pageINFO Eduard61March 2023Page 62
648836ACES II ejection seat lower handles PRINT1/48BRASSINBrassin set - ejection seat for F-16 in 1/48 scale.Made by direct 3D printing. Recommended kit: KineticSet contains:- 3D print: 5 parts- decals: yes- photo-etched details: yes, pre-painted- painting mask: no648837F-16 ejection seat PRINT1/48 KineticProduct pageProduct pageBrassin set - pre-painted lower handles for ACES II ejec-tion seats in 1/48 scale. The set consists of the 5 handles.Made by direct 3D printing.Set contains:- 3D print: 5 parts- decals: no- photo-etched details: no- painting mask: noINFO Eduard62March 2023Page 63
BRASSINBrassin set - the undercarriage wheels for F-35A in1/48 scale. The set consists of the main wheels anda nose wheel. Easy to assemble, replaces plasticparts. Recommended kit: TamiyaSet contains:- resin: 3 parts- decals: no- photo-etched details: no- painting mask: yes648839F-35A wheels1/48 TamiyaBrassin set - black-painted cockpit for Mi-24V (Mi-35)in 1/48 scale. Made by direct 3D printing.Recommended kit: Eduard / ZvezdaSet contains:- 3D print: 10 parts- resin: 46 parts- decals: no- photo-etched details: yes, pre-painted- painting mask: no- SPACE 3D decals: yes648838Mi-24V cockpit black (Mi-35) PRINT1/48 EDUARD/ZVEZDAProduct pageProduct pageINFO Eduard63March 2023Page 64
648840Beaufort Mk.I guns PRINT1/48 ICMBRASSINBrassin set - guns for Beaufort Mk.I in 1/48 scale.Made by direct 3D printing. Easy to assemble, replacesplastic parts. Recommended kit: ICMSet contains:- 3D print: 4 parts- decals: no- photo-etched details: no- painting mask: noBrassin set - radiators for Anson Mk.I in 1/48 scale.The set consists of two radiators. Made by direct 3D prin-ting. Easy to assemble, replaces plastic parts.Recommended kit: AirfixSet contains:- 3D print: 2 parts- decals: no- photo-etched details: no- painting mask: no648841Anson Mk.I radiators PRINT1/48 AirfixProduct pageProduct pageINFO Eduard64March 2023Page 65
Brassin set - 75gal drop tank and a rack for P-39Qin 1/72 scale. Made by direct 3D printing. Easy to assemble,replaces plastic parts. Recommended kit: Arma HobbySet contains:- 3D print: 3 parts- decals: no- photo-etched details: no- painting mask: no672309P-39Q 75gal drop tank PRINT1/72 Arma HobbyBRASSINBrassin set - the 500lb bomb and a bomb rackfor P-39Q in 1/72 scale. Made by direct 3D printing.Easy to assemble, replaces plastic parts.Recommended kit: Arma HobbySet contains:- 3D print: 2 parts- decals: eys- photo-etched details: yes- painting mask: no672308P-39Q 500lb bomb PRINT1/72 Arma HobbyProduct pageProduct pageINFO Eduard65March 2023Page 66
BRASSINCollection of 6 sets for F-35A in 1/48 scale.Recommended kit: Tamiya- AIM-120C AMRAAM (2 sets)- AIM-9X- AIM-132 ASRAAM- GBU-12 bomb- GBU-31(V)1/B JDAMAll sets included in this BIG SIN are available separately,but with every BIG SIN set you save up to 30 %.SIN648100F-35A armament1/48 TamiyaProduct page2x AIM-120C AMRAAMGBU-12 bombGBU-31(V)1/B JDAMAIM-132 ASRAAMAIM-9XINFO Eduard66March 2023Page 67
BRASSINCollection of 4 sets for Fw 190A-8 in 1/48 scale. Reco-mmended kit: Eduard- undercarriage wheels- undercarriage legs BRONZE- landing flaps PRINT- cockpit PRINTAll sets included in this BIG SIN are available separately,but with every BIG SIN set you save up to 30 %.SIN648101Fw 190A-8 ESSENTIAL1/48 EduardProduct pagewheelsundercarriage legs BRONZElanding flaps PRINTcockpit PRINTINFO Eduard67March 2023Page 68
Page 69
Page 70
Page 71
Page 72
Page 73
Page 74
Page 75
Page 76
Page 77
Page 78
Page 79
Page 80
BIG EDAll sets included in this BIG ED are available separately,but with every BIG ED set you save up to 30%.BIG33148 Bf 109G-2/4 1/32 RevellBIG33149Yak-9K 1/32 ICM321002 Bf 109G-2/433338 Bf 109G-2/4 seatbelts STEELJX299 Bf 109G-2/4321003 Yak-9K32479 Yak-9K landing flaps33340 Yak-9K seatbelts STEELJX301 Yak-9KProduct pageProduct pageINFO Eduard80March 2023Page 81
BIG49360 Beaufort Mk.I PART I 1/48 ICM491318 Beaufort Mk.IEX908 Beaufort Mk.IFE1319 Beaufort Mk.I seatbelts STEELProduct pageAll sets included in this BIG ED are available separately,but with every BIG ED set you save up to 30%.BIG EDBIG49359 Mi-4 1/48 Trumpeter491320 Mi-4EX910 Mi-4FE1321 Mi-4 seatbelts STEELProduct pageINFO Eduard81March 2023Page 82
MASKSIT FITS!CX643 C-130J1/72 ZvezdaCX644 Bf 110G-21/72 EduardEX925 B-25J glazed nose1/48 HKMEX926 B-25J glazed nose TFace1/48 HKMEX927 B-24D TFace1/48 RevellEX928 B.534 IV. serie TFace1/48 EduardEX929 F-16A MLU1/48 KineticEX930 F-16A MLU TFace1/48 KineticEX931 F-35A RAM coating early1/48 TamiyaEX932 Mi-8MT1/48 ZvezdaEX933 Mi-8MT TFace1/48 ZvezdaJX305 Hurricane Mk.IIb1/32 RevellJX306 Hurricane Mk.IIb TFace1/32 RevellLX007 Spitfire Mk.IXc1/24 AirfixLX008 Spitfire Mk.IXc TFace1/24 AirfixJX305 Hurricane Mk.IIb JX305 Hurricane Mk.IIbEX927B-24D TFaceEX927 B-24D TFaceEX927 B-24D TFaceEX928 B.534 IV.serie TFaceEX928 B.534 IV.serie TFaceEX928 B.534 IV.serie TFaceEX928 B.534 IV.serie TFaceJX306 Hurricane Mk.IIb TFaceJX306 Hurricane Mk.IIb TFaceINFO Eduard82March 2023Page 83
Page 84
RELEASESMARCH 2023KITSPE-SETSZOOMSMASKS82126 Spitfire Mk.Vc TROP 1/48 ProfiPACK7033 Bf 109E-4 1/72 ProfiPACK11170 GUADALCANAL DUAL COMBO 1/48 Limited7468 Bf 110G-2 1/72 Weekend8232 MiG-21bis Re-release 1/48 ProfiPACK8192 Avia B.534 IV. serie Re-release 1/48 ProfiPACK23036 Spitfire Mk.IXc 1/24 AIRFIX23037 Spitfire Mk.IXc seatbelts STEEL 1/24 AIRFIX32481 Hurricane Mk.IIb landing flaps 1/32 REVELL53291 USS Alaska CB-1 part 3 1/350 HOBBY BOSS72728 C-130J exterior 1/72 ZVEZDA72729 Bf 110G-2 1/72 EDUARD73794 C-130J interior 1/72 ZVEZDA73795 C-130J cargo floor 1/72 ZVEZDA73796 C-130J cargo seatbelts 1/72 ZVEZDA73797 C-130J cargo interior 1/72 ZVEZDA321006 Hurricane Mk.IIb 1/32 REVELL481101 B-25J bomb bay 1/48 HKM481102 B-24D exterior 1/48 REVELL481103 MiG-21bis exterior 1/48 EDUARD491332 F-35A 1/48 TAMIYA491334 F-16A MLU 1/48 KINETIC491336 B-25J glazed nose 1/48 HKM491338 B-24D cockpit 1/48 REVELL491339 B-24D nose interior 1/48 REVELL33343 Hurricane Mk.IIb 1/32 REVELL33344 Hurricane Mk.IIb seatbelts STEEL 1/32 REVELLFE1334 F-16A MLU 1/48 KINETICFE1335 F-16A MLU seatbelts STEEL 1/48 KINETICFE1336 B-25J glazed nose 1/48 HKMFE1337 B-25J glazed nose seatbelts STEEL 1/48 HKMFE1338 B-24D 1/48 REVELLFE1339 B-24D seatbelts STEEL 1/48 REVELLSS794 C-130J 1/72 ZVEZDASS798 Bf 110G-2 Weekend 1/72 EDUARDCX643 C-130J 1/72 ZVEZDACX644 Bf 110G-2 1/72 EDUARDEX925 B-25J glazed nose 1/48 HKMEX926 B-25J glazed nose TFace 1/48 HKMEX927 B-24D TFace 1/48 REVELLEX928 B.534 IV. serie TFace 1/48 EDUARDEX929 F-16A MLU 1/48 KINETICEX930 F-16A MLU TFace 1/48 KINETICEX931 F-35A RAM coating early 1/48 TAMIYAEX932 Mi-8MT 1/48 ZVEZDAEX933 Mi-8MT TFace 1/48 ZVEZDAJX305 Hurricane Mk.IIb 1/32 REVELLJX306 Hurricane Mk.IIb TFace 1/32 REVELLLX007 Spitfire Mk.IXc 1/24 AIRFIXLX008 Spitfire Mk.IXc TFace 1/24 AIRFIXINFO Eduard84March 2023Page 85
BIG-EDBIG-EDBIG EDBIG33148 Bf 109G-2/4 1/32 REVELLBIG33149 Yak-9K 1/32 ICMBIG49359 Mi-4 1/48 TRUMPETERBIG49360 Beaufort Mk.I PART I 1/48 ICMRELEASESBRASSINLöökPLUSBIG SINSPACEDECAL SET635023 WWII German NOTEK headlights PRINT 1/35635025 WWII German shovels PRINT 1/35644201 Mi-24V black (Mi-35) LööK 1/48 EDUARD/ZVEZDA644202 Anson Mk.I LööK 1/48 AIRFIX644203 F-35A LööK 1/48 TAMIYA648828 F4F-4 engine PRINT 1/48 EDUARD648829 F4F-4 wheel bay PRINT 1/48 EDUARD648835 Anson Mk.I wheels 1/48 AIRFIX648836 ACES II ejection seat lower handles PRINT 1/48648837 F-16 ejection seat PRINT 1/48 KINETIC648838Mi-24V cockpit black (Mi-35) PRINT & SPACE 1/4 8 E DUARD/ZVE ZDA648839 F-35A wheels 1/48 TAMIYA648840 Beaufort Mk.I guns PRINT 1/48 ICM648841 Anson Mk.I radiators PRINT 1/48 AIRFIX672308 P-39Q 500lb bomb PRINT 1/72 ARMA HOBBY672309 P-39Q 75gal drop tank PRINT 1/72 ARMA HOBBY634031 Bf 109G-2 LööKplus 1/32 REVELL644197 Z-326 LööKplus 1/48 EDUARD644199 Buccaneer S.2C/D LööKplus 1/48 AIRFIX644200 Beaufort Mk.I LööKplus 1/48 ICMSIN648100 F-35A armament 1/48 TAMIYASIN648101 Fw 190A-8 ESSENTIAL 1/48 EDUARD3DL32012 Hurricane Mk.IIb SPACE 1/32 REVELL3DL32013 Spitfire Mk.IXc SPACE 1/24 AIRFIX3DL48107 F-16A MLU SPACE 1/48 KINETIC3DL48108 B.534 IV. serie SPACE 1/48 EDUARD3DL48109 F-35A SPACE 1/48 TAMIYA3DL48110 B-24D SPACE 1/48 REVELL3DL48111 B-25J glazed nose SPACE 1/48 HKM3DL48112 Mi-8MT SPACE 1/48 ZVEZDAD48110 B-25J stencils 1/48 HKMD48111 Su-25 Russian stencils 1/48 ZVEZDAMARCH 2023INFO Eduard85March 2023Page 86
BUILTBf 109G-6 late series1/48Cat. No. 82111built by Ignat PomazkovINFO Eduard86March 2023Page 87
BUILTW.Nr.160303, Flown by Hptm. Friedrich Eberle, CO of III./JG 1, Volkel, November, 1943Friedrich Eberle, the commanding officer of III.Gruppe of JG 1, was downed in this Bf 109G-6 onJanuary 30, 1944. The man who recorded the killwas a P-47D Thunderbolt jockey, Lt. Robert Bo-oth, of the 369th FS / 359th FG, a fighter ace with atotal of eight kills to his credit. Booth himself wasdowned a few months later, on June 8, 1944 andbecame a POW. Eberle was injured but survivedthe encounter with Booth and led III. Gruppe untilApril 27, 1944. In July 1944, he was appointed theCO of III./JG 4. Eberle led his unit in Operation Bo-deplatte, the attack on Allied airfields on January1, 1945. He was court martialled for cowardice butfinally was acquitted of the charge and survivedthe war with 33 kills. Eberle´s aircraft had beenmarked with a double chevron but in accordancewith temporary orders, this marking was paintedover and the commander´s aircraft was markedwith a number. The JG 1 crest was painted on theleft side of the cowling only. The rear part of thefuselage was partially overpainted with RLM 76 totone it down.INFO Eduard87March 2023Page 88
BUILTFw 190A-8/R21/48Cat. No. 8175Built by Ignat PomazkovINFO Eduard88March 2023Page 89
BUILTAccessories used:48840 Fw 190A-8 landing flaps (PE-Set)EX505 Spinner spirals Fw 190A/F (Mask)Werner Gerth, II.(Sturm)/JG 3 “Udet”, July, 1944INFO Eduard89March 2023Page 90
BUILTBuccaneer S.2C/D1/48Built by Mathias BeckerAirfixINFO Eduard90March 2023Page 91
BUILT49051 Remove before flight UK (PE-Set)491316 Buccaneer S.2C/D (PE-Set)FE1317 Buccaneer S.2C/D seatbelts STEEL (PE-Set)648814 Buccaneer S.2C/D wheels (Brassin)3DL48093 Buccaneer S.2C/D SPACE (3D Decal Set)EX907 Buccaneer S.2C/D TFace (Mask)Accessories used:INFO Eduard91March 2023Page 92
BUILTBuilt by Paolo PortuesiFw 190A-41/48Eduard648152 Fw 190 wheels early (Brassin)648351 Fw 190A-4 cockpit (Brassin)648355 Fw 190A-4 engine & fuselage guns (Brassin)648366 Fw 190A propeller (Brassin)648367 Fw 190A-3/A-4 undercarriagelegs BRONZE (Brassin)Accessories used:INFO Eduard92March 2023Page 93
Built by Oliver PeisslFw 190D-91/48EduardAccessories used:BUILT48651 Fw 190D-9 (PE-Set)648633 Fw 190F-8 cockpit (Brassin)648688 Fw 190D exhaust stacks (Brassin)EX328 Fw 190D Weekend (Mask)INFO Eduard93March 2023Page 94
ON APPROACHAPRIL 2023632189Hurricane Mk.II exhaust fishtail PRINT1/32 Revell632190Hurricane Mk.II wheels1/32 Revell634032Bf 109G-4 LööKplus1/32 Revell632188Hurricane Mk.II exhaust rounded PRINT1/32 RevellBIG33150 Tornado IDS 1/32 ITALERIBIG49361 Beaufort Mk.I PART II 1/48 ICMBIG49362 A-10C 1/48 HOBBY BOSS632188 Hurricane Mk.II exhaust rounded PRINT 1/32 REVELL632189 Hurricane Mk.II exhaust fishtail PRINT 1/32 REVELL632190 Hurricane Mk.II wheels 1/32 REVELL635024 WWII German 10 ton jacks PRINT 1/35635026 WWII German wire cutters PRINT 1/35644205 A6M2-N Rufe LööK 1/48 EDUARD644206 B-25J LööK 1/48 HKM644207 F-16C Block 25 LööK 1/48 KINETIC648826 F4F-3 engine late PRINT 1/48 EDUARD648842 A-1J seat PRINT 1/48 TAMIYA648844 Anson Mk.I guns PRINT 1/48 AIRFIX648845 A6M2-N Rufe seat PRINT 1/48 EDUARD648846 A6M2-N Rufe exhaust PRINT 1/48 EDUARD648847 A6M2-N Rufe cannon barrels & cockpit guns PRINT1/48 EDUARD648848 A6M2-N Rufe folding wingtips PRINT 1/48 EDUARD648849 A6M2-N Rufe gun bays PRINT 1/48 EDUARD648854 F-16 exhaust nozzle P&W F100 PRINT 1/48 KINETIC648855 F-16 radar early PRINT 1/48 KINETIC648857 Mi-24V cockpit turquoise PRINT & SPACE 1/48 EDUARD/ZVEZDA672310 Bf 110E wheels 1/72 EDUARD672311 Bf 110E nose guns PRINT 1/72 EDUARD672312 Bf 110E cockpit 1/72 EDUARD644204 Anson Mk.I LööKplus 1/48 AIRFIX634032 Bf 109G-4 LööKplus 1/32 REVELL674003 P-39Q LööKplus 1/72 ARMA HOBBYSIN63216 Tornado IDS armament 1/32 ITALERISIN648102 F-14D 1/48 TAMIYABIG ED (April)BRASSIN (April)LöökPlus (April)BIGSIN (April)Brassin set - exhaust stacks for Hurricane Mk.II in 1/32scale. Made by direct 3D printing. Easy to assemble,replaces plastic parts. Recommended kit: RevellSet contains:- 3D print: 2 parts- decals: no- photo-etched details: no- painting mask: noBrassin set - the undercarriage wheels for Hurricane Mk.IIin 1/32 scale. The set consists of the main wheels anda tail wheel. Easy to assemble, replaces plastic parts.Recommended kit: RevellSet contains:- resin: 3 parts- 3D print: 2 parts- decals: no- photo-etched details: no- painting mask: yesCollection of 4 sets for Bf 109G-4 in 1/32 scale.Recommended kit: Revell- LööK set (pre-painted Brassin dashboards& Steelbelts),- TFace painting mask- exhaust stacks- undercarriage wheelsBrassin set - exhaust stacks for Hurricane Mk.II in 1/32scale. Made by direct 3D printing. Easy to assemble,replaces plastic parts. Recommended kit: RevellSet contains:- 3D print: 2 parts- decals: no- photo-etched details: no- painting mask: noINFO Eduard94March 2023Page 95
635024WWII German 10 ton jacks PRINT1/35ON APPROACHBrassin set - 10ton jacks for German WWII AFV in 1/35 scale.The set consists of 3 jacks. Made by direct 3D printing.Set contains:- 3D print: 15 parts- decals: no- photo-etched details: no- painting mask: no635026WWII German wire cutters PRINT1/35644204Anson Mk.I LööKplus1/48 AirfixBrassin set - wire cuters for German WWII AFV in 1/35 scale.The set consists of 5 wire cutters. Made by direct 3D printing.Set contains:- 3D print: 5 parts- decals: no- photo-etched details: yes- painting mask: noCollection of 4 sets for Anson Mk.I in 1/48 scale.Recommended kit: Airfix- LööK set (pre-painted Brassin dashboards & Steelbelts)- TFace painting mask- radiators- undercarriage wheelsINFO Eduard95March 2023Page 96
ON APPROACHAPRIL 2023644205A6M2-N Rufe LööK1/48 Eduard644206B-25J LööK1/48 HKM644207F-16C Block 25 LööK1/48 KineticLööK set - Brassin pre-painted dashboard and STEEL seatbelts for A6M2-NRufe in 1/48 scale. Easy to assemble, replaces plastic parts.Recommended kit: EduardSet contains:- resin: 2 parts- decals: no- photo-etched details: yes, pre-painted- painting mask: noLööK set - Brassin pre-painted dashboard and STEELseatbelts for B-25J in 1/48 scale. Easy to assemble, replacesplastic parts. Recommended kit: HKMSet contains:- resin: 3 parts- 3D print: 2 parts- decals: no- photo-etched details: yes, pre-painted- painting mask: noLööK set - Brassin pre-painted dashboardand STEEL seatbelts for F-16C Block 25 in 1/48 scale.Easy to assemble, replaces plastic parts.Recommended kit: KineticSet contains:- resin: 2 parts- decals: no- photo-etched details: yes, pre-painted- painting mask: noPRELIMINARY IMAGESPRELIMINARY IMAGESPRELIMINARY IMAGESINFO Eduard96March 2023Page 97
ON APPROACHAPRIL 2023648826F4F-3 engine late PRINT1/48 Eduard648842A-1J seat PRINT1/48 Tamiya648844Anson Mk.I guns PRINT1/48 AirfixBrassin set - the engine for F4F-3 in 1/48 scale.The cowling are included. Made by direct 3Dprinting. Recommended kit: EduardSet contains:- 3D print: 36 parts- decals: no- photo-etched details: yes- painting mask: noBrassin set - the seat for A-1J in 1/48 scale. Seatbeltsare printed together with the seat. Easy to assemble,replaces plastic parts. Recommended kit: TamiyaSet contains:- resin: 1 part- decals: no- photo-etched details: no- painting mask: noBrassin set - guns for Anson Mk.I in 1/48 scale. The setconsists of the 4 guns. Made by direct 3D printing.Recommended kit: AirfixSet contains:- 3D print: 10 parts- decals: no- photo-etched details: yes- painting mask: noINFO Eduard97March 2023Page 98
ON APPROACH648845A6M2-N Rufe seat PRINT1/48 Eduard648846A6M2-N Rufe exhaust PRINT1/48 Eduard648847A6M2-N Rufe cannon barrels & cockpit guns PRINT1/48 EduardBrassin set - seat for A6M2-N Rufe in 1/48 scale.Easy to assemble, replaces plastic parts.Made by direct 3D printing.Recommended kit: EduardSet contains:- 3D print: 1 part- decals: no- photo-etched details: yes, pre-painted- painting mask: noBrassin set - exhaust pipes for A6M2-N Rufein 1/48 scale. Easy to assemble, replaces plasticparts. Made by direct 3D printing.Recommended kit: EduardSet contains:- 3D print: 4 parts- decals: no- photo-etched details: no- painting mask: noBrassin set - gun barrels for A6M2-N Rufe in 1/48 scale.Easy to assemble, replaces plastic parts.Made by direct 3D printing. Recommended kit: EduardSet contains:- 3D print: 4 parts- decals: no- photo-etched details: yes- painting mask: noAPRIL 2023INFO Eduard98March 2023Page 99
648849A6M2-N Rufe gun bays PRINT1/48 Eduard648854F-16 exhaust nozzle P&W F100 PRINT1/48 Kinetic648848A6M2-N Rufe folding wingtips PRINT1/48 EduardBrassin set - gun bays for A6M2-N Rufe in 1/48scale. Made by direct 3D printing.Recommended kit: EduardSet contains:- 3D print: 16 parts- decals: no- photo-etched details: yes- painting mask: noBrassin set - exhaust nozzle for P&W F100 poweredF-16 in 1/48 scale. Made by direct 3D printing.Recommended kit: KineticSet contains:- 3D print: 4 parts- decals: no- photo-etched details: no- painting mask: noON APPROACHBrassin set - folding wingtips for A6M2-N Rufein 1/48 scale. Made by direct 3D printing.Recommended kit: EduardSet contains:- 3D print: 4 parts- decals: no- photo-etched details: yes- painting mask: noAPRIL 2023INFO Eduard99March 2023Page 100
ON APPROACHBrassin set - nose radar for F-16 in 1/48 scale.Made by direct 3D printing. Recommended kit: KineticSet contains:- 3D print: 5 parts- decals: no- photo-etched details: no- painting mask: noBrassin set - turquoise-painted cockpit for Mi-24Vin 1/48 scale. Made by direct 3D printing.Recommended kit: Eduard / ZvezdaSet contains:- 3D print: 10 parts- resin: 46 parts- decals: no- photo-etched details:yes, pre-painted- painting mask: no- SPACE 3D decals: yesBrassin set - the undercarriage wheels for Bf 110Ein 1/72 scale. The set consists of the main wheels anda tail wheel. Easy to assemble, replaces plastic parts.Recommended kit: EduardSet contains:- resin: 3 parts- decals: no- photo-etched details: no- painting mask: yes648855F-16 radar early PRINT1/48 Kinetic648857Mi-24V cockpit turquoise PRINT & SPACE1/48 Eduard/Zvezda672310Bf 110E wheels1/72 EduardAPRIL 2023INFO Eduard100March 2023Page 101
ON APPROACHBrassin set - nose guns for Bf 110E in 1/72 scale.Made by direct 3D printing. Recommended kit: EduardSet contains:- 3D print: 13 parts- decals: no- photo-etched details: yes- painting mask: noBrassin set - the cockpit for Bf 110E in 1/72 scale.Recommended kit: EduardSet contains:- 3D print: 4 parts- resin: 25 parts- decals: yes- photo-etched details: yes, pre-painted- painting mask: noCollection of 4 sets for P-39Q in 1/72 scale.Recommended kit: Arma Hobby- LööK set (pre-painted Brassindashboards & Steelbelts)- seat- exhaust stacks- gun barrells672311Bf 110E nose guns PRINT1/72 Eduard672312Bf 110E cockpit1/72 Eduard674003P-39Q LööKplus1/72 Arma HobbyAPRIL 2023INFO Eduard101March 2023Page 102
SIN648102F-14D1/48 TamiyaCollection of 4 sets for F-14D in 1/48 scale.Recommended kit: Tamiya- undercarriage wheels- cockpit- exhaust nozzles- Remove Before Flight tags SPACEAll sets included in this BIG SIN are available separately,but with every BIG SIN set you save up to 30 %.ON APPROACHAPRIL 2023INFO Eduard102March 2023Page 103
SIN63216Tornado IDS armament1/32 ItaleriCollection of 6 sets for Tornado IDS in 1/32 scale.Recommended kit: Italeri-AIM-9M/L Sidewinder- AGM-88 HARM- BOZ-107 pod (2 sets)- AN/AAQ-28(V) Litening pod- GBU-24 bombAll sets included in this BIG SIN are available separately,but with every BIG SIN set you save up to 30 %.2xBRASSIN 02/2022BRASSIN 02/2022ON APPROACHAPRIL 2023INFO Eduard103March 2023Page 104
PE-SETS23038 Spitfire Mk.IXc landing flaps 1/24 AIRFIX23039 Spitfire Mk.IXc engine & undercarriage 1/24 AIRFIX36498 M48A5 1/35 TAKOM36499 Sd.Kfz. 251/1 Ausf.C 1/35 ACADEMY36500 Sd.Kfz. 251/1 Ausf.C side stowage bins 1/35 ACADEMY481104 B-24D bomb bay 1/48 REVELL481105 A6M2b landing flaps 1/48 ACADEMY491340 Mi-8MT 1/48 ZVEZDA491342 F4U-1D 1/48 HOBBY BOSS491344 A6M2b 1/48 ACADEMY491346 F6F-3 1/48 EDUARD491347 F6F-5 1/48 EDUARD53292 USS Missouri BB-63 1/350 HOBBY BOSS72730 F-14B exterior 1/72 ACADEMY73799 U-2C 1/72 HOBBY BOSS73800 F-14B 1/72 ACADEMYZOOMSFE1340 Mi-8MT 1/48 ZVEZDAFE1341 Mi-8MT seatbelts STEEL 1/48 ZVEZDAFE1342 F4U-1D 1/48 HOBBY BOSSFE1343 F4U-1D seatbelts STEEL 1/48 HOBBY BOSSFE1344 A6M2b 1/48 ACADEMYFE1345 A6M2b seatbelts STEEL 1/48 ACADEMYFE1346 Fw 190A-4 Weekend 1/48 EDUARDSS800 F-14B 1/72 ACADEMYMASKSCX645 UTI MiG-15 1/72 EDUARDCX646 U-2C 1/72 HOBBY BOSSCX647 F-14B 1/72 ACADEMYEX934 A6M2-N Rufe TFace 1/48 EDUARDEX935 F4U-1D 1/48 HOBBY BOSSEX936 F4U-1D TFace 1/48 HOBBY BOSSEX937 A6M2b TFace 1/48 ACADEMYEX938 Mosquito B Mk.IV / PR Mk.IV TFace 1/48 TAMIYAEX939 Fw 190A-4 1/48 EDUARDSPACE3DL48113 F4U-1D SPACE 1/48 HOBBY BOSS3DL48114 A6M2-N Rufe SPACE 1/48 EDUARD3DL48115 A6M2b SPACE 1/48 ACADEMY3DL72013 U-2C SPACE 1/72 HOBBY BOSS3DL72014 UTI MiG-15 SPACE 1/72 EDUARDON APPROACHSpitfire Mk.IXc engine & undercarriageMi-8MTM48A5APRIL 2023INFO Eduard104March 2023Page 105
Spitfire Mk.IXc engine & undercarriageON APPROACHZ-326/C-305 Trenér Master#821831/48Z-326, No. 610, Kladno Aero Club, Kladno Airfield,Czechoslovakia, 1975Z-326MF, No. 918, Repülőiskola Nyíregyháza,Nyíregyháza Airport, Hungaria, 2020C-305, No. 604, Czechoslovak People’s Army,Czechoslovakia, 1965Z-326M, No. 609, private owners, Slaný Airfield, 2022Z-326, No. 902, private owner, Grossenhain,Germany, 2022Z-326, No. 894, Escadrille Orion, Marmande Virazeil,France 2013APRIL 2023INFO Eduard105March 2023Page 106
ON APPROACHRUFE 1/48#11171Dual ComboYokohama Kōkūtai, Tulagi Island, Solomon Islands,August 19425th Kōkūtai, Kiska island, Aleutians, August 1942c/n 15, Lt.(jg) Keizō Yamazaki, Kōkūtai 802,Shortland Island, February 1943Kōkūtai 802, Faisi-Poporang base,Shortland Islands, February 1943Kōkūtai 452, Bettobi Lake, Shumshu Islands,Kuriles, July 1943Kōkūtai 802, Emidj Island, Jaluit Atoll,Marshall Islands, October 1943Ensign Jin´ichirō Ozawa, Sasebo Kōkūtai,Sasebo Air Base, Japan, September 1944Kōkūtai 934, Ambon island, Moluku Islands, March 1944APRIL 2023INFO Eduard106March 2023Page 107
Tempest Mk.V Series 2#841871/48ON APPROACHEJ750, W/Cdr John B. Wray, CO of No. 122 Wing,B.80 Volkel, the Netherlands, December 1944EJ536, F/Lt Pierre H. Clostermann, No. 56 Squadron,B.80 Volkel, the Netherlands, beginning of April 1945EJ705, P/O Frank A. Lang, No. 80 Squadron,B.80 Volkel, the Netherlands, December 1944SN330, S/Ldr Colin H. Macfie, CO of No. 3 Squadron,Wunstorf, Germany, 2nd half of 1947APRIL 2023INFO Eduard107March 2023Page 108
ON APPROACHFw 190A-4 w/engine flaps& 2-gun wings1/48#84117WNr. 0142481, Fw. Otto Kittel, 2./JG 54, Krasnogvardeyjsk,Soviet Union, February 1943Lt. Leopold Wenger, 10./JG 2, Caen-Carpiquet, France, February 1943WNr. 142317, Fw. Ludwig Seif, 11./SKG 10, Sidi Ahmed, Tunisia,January 1943Jaboschwarm I./JG 54, Krasnogvardeysk, Soviet Union, Spring 1943APRIL 2023INFO Eduard108March 2023Page 109
Bf 110C-2, WNr. 3578, 9./ZG 26, Barly, France, August 1940Bf 110C-2, WNr. 3257, Hptm. Heinz Wagner/Stfw. Adolf Schmidt,CO of 4./ZG 76, Abbeville, France, August 1940Bf 110C-4, WNr. 2095, 4./ZG 1, Trier-Euren, Germany, June 1940Bf 110C-2, WNr. 3026, Lt. K. Koch, 1.(Z)/JG 77,Kirkenes, Norway, October 1941Bf 110C, 1./NJG 3, Benghazi, Libya, May 1941ON APPROACHBf 110C1/48#8209APRIL 2023INFO Eduard109March 2023Page 110
ON APPROACHUTI MiG-15Re-release1/72#70556 Fighter-Bomber Air Regiment, Přerov Air Base,Czechoslovakia, summer 1974Soviet Union, 1960s through the 1970s Algerian Air Force, 1960s through the 1980sc/n 922226, Hävittäjälentolaivue 31, Rissala Air Base, Finland, late 1960sIndonesian Air Force, Jakarta-Kemajoran Air Base,Indonesia, 1960sAPRIL 2023INFO Eduard110March 2023Page 111
Can you recall the first accessory setyou bought for a kit? Frankly, I don’t. Ithas been quite some time… I only knowI noticed the existence of photo-etchedsets sometime in 1992, I would say, andalso noted the nice, camouflaged smallboxes stuffed with resin parts – detail setsby Verlinden, on the market. As far as I canrecall, this producer was really “in” at thattime. Amazed by the detail, the supplies ofthese sets, as well as of the typical flatpackages with Eduard photoetch sets,kept growing in my private collection.I never kept any summary of whatI spent my money on, leading to somefunny moments when, on opening a kitbox on which I planned to use my newlyacquired accessories, I was met with theexact same pieces already staring backat me from within! Once I even managedto triple one accessory! By the way: whowants some nice Eduard Brassin wheelsfor the HK Models´ Meteor in 32nd ata very good price?The wheels are a good example of the“no-problemo” resin accessory, becauseif one doesn't make any fundamentalmistake during the mastering and molding,than all should be OK. In this case, eventypical resin shrinkage presents noserious problems. But it is a very differentstory when it comes to the parts whichmust be precisely combined with theplastic parts. I think everyone who hasever built a kit with resin accessoriesknows that: thinning, scribing, placingand, sometimes, shouting … Many of usalso experienced a disappointment afteropening the box only to find out thereare just original plastic parts re-moldedwith several “easy-to-do-myself” detailsadded. It is even worse when the price ofsuch an “accessory” reaches the price ofthe kit and the installation of these resinparts requires more effort than to do thedetailing using the original kit parts.And then, after years spent with castresin sets, 3D printing emerged and thecontinual progress of this technologyled the first enthusiasts to start trying toproduce their own home-made parts (themore skilled and daring even made entiremodels of desired types). Manufacturers,well aware of what was happening, waitedfor the technology to mature enough toallow for sensible serial production andjumped at the opportunity when it did.Eduard did not stay aloof of this trend,of course, despite its well-establishedresin casting department. I rememberthe first attempts about two years ago,when colleagues were testing differentmaterials for printing in search for theright one to use, the one giving the bestpossible results and was stable enough.And even then, I was impressed with thefinesse of the printed parts. Today wehave a herd of printers humming merrilyalong, running at full speed. And the smallbeauties produced by them make me wantto start some super-detailed projectsagain, after quite a long time. For example,the Wildcat, where the wheel bay, engineand wing folding mechanism sets arereally encouraging me to do it!Anyone who knows something about resincasting knows that a rubber mold doesnot survive forever and the last part tocome out of it will not be exactly the sameas the first one quality-wise. And alsohe knows, there are a number of factorsthat can affect the result, whether it’s thequality of the air bubble removal in thevacuum chamber, the mix of the materialused, the temperature at which it is cast,and so on and so forth ... 3D productionis quite a different world! Yes, even theprinter can make a mistake occasionally,but it’s visible and the part is discardedduring quality control. Otherwise, they’rejust like each other, first and last. Andsince these parts do not shrink, one canalso rely on their accuracy. In fact, someof the printed parts seem to fit better thanthe original plastic parts! And I think it’sa terrible shame that this manufacturingprocess isn’t fast and cost-effectiveenough to produce complete kits. It wouldeliminate the many constraints that limitthe detail and sometimes also shapeaccuracy of parts produced using moldsand injection molding machines.By the way, nowadays even metal partscan be printed with great precision, andperhaps the time is not so far away forprinting molds. Such a technology mighteliminate at least the milling, maybe evenelectrode discharging of the molds. Sinceit is possible to print, for example, H13 toolsteel, it may only be a matter of time. Evenin this case, 3D printing technology wouldbring a number of advantages apart fromthose mentioned.In any case, 3D printing is a revolution forour hobby, and in combination with othertechnologies, such as Mimaki printers inour case, it opens up a whole new world ofpossibilities for the production of perfectaccessories. Many modelers keep sayingwe are in the golden age of modellingthanks to the constant flurry of new kits.But I think the real golden era is comingwith the rise of 3D technology.Richard PlosTHE GOLDEN ERA PRINTEDINFO Eduard111March 2023Editorial
Good day, Ladies and Gentlemen,
We’re closed. Although you are certainly able to view and study our March release listing within these pages or at our e-shop, any purchases will have to be postponed. I understand that this sounds a little nuts, but it is not the result of some underhanded marketing ploy. It is a function of the fact that we are moving our entire retail department. It is also the reason why no sales will be going through our e-shop for the next seven days. As you will have probably already noted, the new items were available for early purchase from last Friday, and they will be available from our retail partners as well.
The move is being made from within the city of Most, where we suffered our fire claiming a lot of our plastic some two years and three months back, to a facility which we purchased just outside of the city last year and have been renovating for our needs. The village is called Sedlec, and borders an industrial park that houses, for example, a former brewery. That has long since been relocated. Our new facility is located about 4km from our head office in Obrnice. Our renovation is being done in steps. In January, immediately ahead of our departure for Nuremberg, we moved all of our plastic to the new facility which we call ‘the Barn’, but is officially labeled as ‘Hall No.2’. The relocation of the retail department is the second phase, and the third will be the move of the tool and press shops. This will include our design offices that fall under kit production. If everything goes as it has been up to now, that third phase should be complete by the end of the year. On the one hand, it complicates our life quite a bit, the third phase being the most complicated. The move of the heavy equipment will be the most logistically ambitious activity Eduard has ever embarked upon. It will also likely have an impact on the meeting of release schedules for the beginning of the year. This will mostly centre around the 48th scale S-199, but there will be a negative push against other projects such as the MiG-21F. But, there is the other hand, too, that will open up a more effective workspace for us, and not just with respect to the production of kits. The move will be to the benefit of the Brassin department as well, because the space freed up on the main floor of the main building in Obrnice will be allocated to them. This will give them somewhere between 6400 and 6500 square feet, and that will house their printers and other pieces of equipment very nicely!
This is all still in the relatively distant future. And you know how plans are. They have an awe-inspiring ability to not go the way they’re supposed to, they have an ability to fail, and so on. At the moment, it’s the retail department’s turn to move on up, and we began this today. We moved all the furniture and the IT equipment and tomorrow we’ll pick up with packing up stock items from the shelves and the latter’s disassembly. So, keep your fingers crossed and please, be patient. If everything goes according to those aforementioned plans, we should be open for business again next Wednesday. If you need anything from us, you can still write. We will be on-line and answering questions. Just bear in mind that we will be rather busy and there may be a delay in our responses for a short while.
Nuremberg
The Nuremberg Toy Fair was different this year. From the point of view of our industry, it’s pretty simple to describe. It was small. All in all, there were six manufacturers represented: us, Special Hobby, Italeri, Airfix, Revell and Tamiya. There were some colleagues that produce accessory items present, AK Interactive, Vallejo, and Art Scale, which is also a retailer, but they do produce some masks and decals, along with some cutting saws. And that’s it. Beyond that…crickets. There was Zvezda, but they were in a bit of an undercover mode in an office in the service centre. In proportion to the new conditions, our table space was reduced and shared with Special Hobby. Retailers and journalists were fewer as well, and notable absences were Asian and American. But, it wasn’t as bleak as I am perhaps making it out to sound. There were fewer of us, but there was correspondingly more time for things. The discussions were not mechanically geared to business and there was a pleasant, friendly feel to it. There was also more general ‘chatter’, if you like. All in all, it was an interesting experience and I am happy for it. The atmosphere at this year’s Nuremberg Toy Fair reminded me of the old Chicago show RICHTA because, among other reasons, our exhibition hall at Nuremberg was, apparently for the first time, open to kids, and kids came! There were no Scout troops in attendance like in Chicago, but it was nice to see, regardless if it was because of the recent crisis or a simple organizational decision. It was a change and change is good. It wasn’t a revolution, but it was a step forward within the bounds of reason, and that is, in my estimation, the best way to move forward. Ultimately, what bothered me the most was the cold in the exhibition venue, and the stall that sold steaks on a bun that was closed. That was probably my greatest piece of enjoyment that I looked forward to. I will need to find another little gem to look forward to, and I am worried that this one will be tough to replace!
Don’t fret too much if these little philosophical musings don’t give you all that much. A dedicated, in depth look at Nuremberg follows in the pages of this newsletter edition.
New Releases for March – Kits
Of all of our new releases, which total 86 this month, modellers most gravitate to new kits. This month, there is nothing that is super new, there is no kit taking a bow for its premiere, but even so, it is an interesting mix of scales and aircraft from various periods in history. One is dedicated to the pivotal battle during the Second World War that was Guadalcanal and contains the F4F-4 in two development configurations from that period. At the time, naval fighters were not particularly striking in appearance on either of the opposing sides, but in my view, we were able to come out with an attractive mix of interesting aircraft that are accompanied by, to the contrary, riveting stories. Among them is a Wildcat that was flown by ‘Pug’ Southerland in a legendary fight with Saburo Sakai. This event was already once depicted on the boxart for one of our A6M2 releases. Other scheme options are provided for Wildcats that were brought to the forefront by pilots such as Joe Foss, Stanley Vejtasa and Donald Runyon. There is a total of twelve of these options, and the kit contains two complete sets of plastic for versions of the Wildcat that marginally differed from one another. Truth be told, the differences only concern the fuselages, but they are there and you need to be aware of them. If these sets of plastic aren’t enough for you, we also have the Overtrees options. And while still on the Wildcats over Guadalcanal theme, we have an article penned by Tom Cleaver in this issue of the newsletter.
The Second World War is our main focus of attention when it comes to kit production and our range reflects this. The 1:72 scale Bf 109E-4 in the ProfiPACK line is generally, but not exclusively, about the Battle of Britain, while the Spitfire Mk.Vc Trop deals with the later battles over the Mediterranean, North Africa and Southeast Asia. It represents aircraft equipped with the tropical filter, either the Vokes or Aboukir types, and the markings are anything but boring. We have British, South African, Australian, American and even a Yugoslavian Spitfire. We did make a subtle change to the design of this kit with the addition of the wingtips that were typical for aircraft equipped with the Aboukir unit. I also consider the boxart for this kit rather unique, and what is interesting about it, as well as with our other boxarts this month, is detailed in the Boxart Stories sections of the newsletter.
The Second World War theme is also expressed in the only Weekend kit release for March. Following on the heels of November’s Bf 110G-4, we have the Bf 110G-2 for March. In terms of camouflage schemes, this kit is no slouch either, but what sets this kit apart are the weapons options, and is different for each of the four marking options offered. We waited just shy of two years for the return to our range of the Bf 110 in the two main scales of 1:48 and 1:72. It was even longer for the Avia B.534. That one makes its return in the form of the B.534 IV Series in the ProfiPACK line. We should also manage to put out the B.534 III Series, and in the original boxes. Also being reissued in March is the MiG-21bis, also in the ProfiPACK line.
New Releases for March – Accessory Items
Of the 86 aforementioned new releases for the month, eighty of them fall under various accessory labels. Among them are some very interesting little items, often even unique, that provide a hint of the future. Among these, for example, is the cockpit for the 1:48 Mi-24V/Mi-35 in black form, which carries in its name PRINT & SPACE. This means that it is made as a 3D print with a small number of cast items, complemented by an instrument panel and other details made using 3D technology of the SPACE line. In April, we will release a set for the older and more traditional green version, common to Soviet era aircraft. I think that this combination is a fairly interesting concept, and with the advantages and features that it offers, will pique the curiosity of many modellers. For accessory items for model aircraft, this really is a new age, offering new opportunities and possibilities for improving your models, and certainly deserves a test drive at the very least. The colour sets include a small 3D printed item covering the ejection seat handle for the F-16A from Kinetic, also in 1:48 scale. The set is called ACES II Ejection Seat Lower Handles PRINT 1/48 and it really is as noteworthy as it is small. If it does get noticed, and becomes popular, it will open the door for further development of the technology. Printed engines are falling into the realm of classic items, and are offered for the F-4F-4 Wildcat, along with a wheel well set for the same type and scale, and yes, for the Eduard kit in general, and for the above mentioned Guadalcanal item in particular. I would also like to turn your attention to the set of guns for the Beaufort Mk.I, which are beautifully and finely printed items as well.
The collection also includes other interesting types of accessories. These cover, for example, the HKM B-25J in 1:48, in the form of masks, photoetched brass and SPACE sets, and the same can be said of the sets for the Revell B-24D Liberator and the F-16A MLU from Kinetic. A large collection of photoetched sets are designed for the Zvezda C-130J Hercules. So far, we have masks and a Space set for Zvezda’s Mi-8MT, while masks, photoetched and SPACE items are available for the 1:32 scale Hurricane from Revell and Spitfire Mk.IXc from Airfix. The latter, though, is in the bigger scale of 1:24. There is a mix of accessory items for Tamiya’s beautiful F-35A and, besides the wheels, I would point out the extensive masks for the RAM panels on the surface of Japanese and American aircraft which the kit offers as part of its eight marking options. Similar, but correspondingly simpler versions of these masks for the remaining marking options of the kit have been available since last month. These masks are produced using a different material from the one used in our canopy sets. Besides the advantages that this material offers for this type of application, they also differ in their black colour. With these two sets, we make a return to masks designed for camouflage schemes, national insignias and marking details. It’s not a one-off project, and we will continue with these sets primarily for kits of our own production. For the F-35A, we also have a BiGSin set of weapons.
Of the increasingly popular SPACE line, we have eight new items for March. I would also like to point out two 3D printed sets for 1:35 scale AFVs, and also the new LooK and LookPlus items.
Articles
Besides the articles already mentioned above, we have the next installment of the War Over Ukraine feature from Mira Maric. February 24th marked the first anniversary of the Russian attack on Ukraine. It came with a realization that we have ahead of us many months, if not years, of bloody fighting, the horrors of war and general gloom and doom. Regardless of how long it takes, it will end, and it must end if the world is to survive and maintain the values on which it stands. That means the defeat of Russia. After all, the Russians are working at it through their own tenacity.
With the use of four formerly Czech Hinds by Ukraine, we have a connection, albeit a loose one, to Tomas Dvorak’s article covering the Mi-24/Mi-35 that takes a look at not just the technical details of these aircraft, but also examines the interesting circumstances surrounding their acquisition by Czechoslovakia, and later deliveries to the Czech Air Force. This is an article that, although it is very detailed, it remains very easy to read and has a good continuity. It may not appear yet in the English translation of the newsletter.
The last of today’s articles deals with the sad news of the passing of Petr Samal on January 31, after a long illness. He led a ring of modellers that brought kids into the hobby and was also the head of the builders’ section of the SMCzR. Memories are offered by Fredy Riedel and Milan Mikulecky, and I think back on Petr fondly.
Happy Modelling!
Vladimir Sulc
Memories of Petr Šámal
by Alfred Riedel
On Tuesday, January 31, I was sitting with Jan Zdiarsky from Eduard in a restaurant near our hotel in Nuremberg. I was enjoying dinner and relaxing after a busy day, full of preparations of the stand at the fair. However, this relaxed mood was swept away by the news that hit me hard. Petr Šámal has died. He hadn’t been in good health for some time, but according to the reports I was getting, he had started to improve. So, it came like a bolt from the blue. After Petr Dousek and Radek Pavlíček, another great friend of mine had passed away ...
I met Peter sometime in late 1990 or early the following year. We were introduced by a mutual friend, my classmate Petr Šobíšek, at a model exhibition organized by the plastic model club Albatros. We got along in many things with “Šámi”, as we called him. Plastic modeling and interest in history were of course two of them. “Šámi” had knowledge as well as copious archives and was, like us, kind of “patient”. We became members of Albatros club and “Šami” became a bit of a mentor to us. After all, he was a bit older. Unlike me, a student at the time, and Petr Šobíšek, who was serving the alternative civilian service, “Šámi” was already making money and owned a car. Two years later, I started working at one MPM model shop in Prague while Petr Šobíšek was working at another MPM shop in a different Prague location. Thanks to his work at Prague Energy company (PRE), “Šámi” kept moving around Prague and very often stopped by one or the other store. A group of colleagues and their friends formed around both shops and “Šámi” was an important member of this group. At that time, he got a studio apartment in Písnice, so our group had a place to meet. Today I wouldn’t probably survive such lavish parties as those held there back then … We travelled together not only to attend model competitions, but also to do various trips including mountaineering. “Šámi” with his guitar, which he played with great skill, often took care of the entertainment. In fact, music was his other great hobby. Besides playing the instrument, he also collected records and his knowledge of good music was astounding.
But time passed, “Šámi” settled down, got married, had a daughter and later a son. His son was born just a few months before mine. So, we would occasionally meet up with our families, usually at a modeling contest. Unlike “Šámi”, who was still working at PRE, I left MPM to eventually return to Special Hobby. So, I was also seeing “Šámi” professionally, because in the meantime he had become the chairman of the plastic modeling section of SMČR (Modelers association of Czech Republic) and was dealing with sponsorship issues. He took over the plastic model section in quite a bad shape, but thanks to his dedication, organizational skills and knowledge, the functioning of it has changed for the much better. At the same time, he led the children model club in Písnice and raised many new modelers. He took care of the children like a little grumpy, but very caring babysitter. Unfortunately, he did not take similar care of his health, which had fatal consequences. “Šámi” left too soon. I miss him.
by Milan Mikulecký
Whenever someone passes away, everybody tends to remember them in a good way. In the case of Petr Šámal, it’s easy for me, I really experienced him only in a good way. And I think that everyone who knew him in connection with his passion – plastic modelling – has it the same.
I admit that I am not worth much as a modeler, the last time I finished a kit was some thirty-five years ago. When my children got to the age when it was time to start developing their fine motor skills, I had to admit self-critically that they would acquire rather negative habits under my guidance. Therefore, I called Vladimír Šulc from Eduard, saying that I would like to hire a modeler for my children who would introduce them to modeling in the twenty-first century. And Vladimír gave me the phone number of Petr Šámal, saying he runs a modeling club in Písnice near Prague. That’s how I first met Peter.
What surprised me there? First of all, the number of children attending the club. And then that even though today’s children have a different attitude to authority than we had, Petr and his colleagues managed to “discipline” them without any severe means. And most importantly, that even for teenagers, Peter was an unquestionable authority. I understood that running a modeling club is not just about building the kits, but also about weekends spent at modeling contests, looking for sponsors or negotiating with the owners of the premises where the club operates. Petr was the soul and the engine of it all. But it didn’t stop there, as Petr also organized trips to various museums. Once I had an opportunity to go with them, it was the trip from Točná to the Military Technical Museum in Lešany. A driver for the historic Dodge WC 52, which was to take us to the museum and back, send us a last-minute apology. Well, it was Petr who got behind the wheel, and he bravely tackled driving a car without a synchronized gearbox and many other conveniences of modern cars.
Peter, besides aircraft built in various scales, also liked the real ones. He himself used to fly in the Točná Aero Club, and when I offered him the opportunity to go flying, he did not refuse. Although a lot of time had passed since he himself had been a student pilot of Blaník glider, it was clear that he still had a feeling for flying. When he took over the controls, I did not have the slightest urge to correct his piloting in any way. We had the opportunity to fly together a Stearman, a Zlin C-305 or a Cessna C 180 in bush flying modification. Peter then surprised me, because he had bought each of these aircraft as a model, with the intention of building them in the exact livery we flew together. I don’t know whether he managed to realize his plan, the illness he eventually lost the battle for his life with came rather quickly (at least for me, as Peter didn’t talk much about his troubles) and in a form that caused him to be hospitalized in addition to the pain. I admit that we will all remember him as a tireless organizer with his typical smile. As a man who never refused help to anyone who asked for it.
I have three children myself and I know how challenging it is to take care of them, to teach them something and to anticipate everything they might think of. That’s why I have lot of respect and awe for people who are spending time and lot of effort with children who might be strangers to them in addition to their own. Peter was one of them. He led them to a love of history, to patience, and taught them a whole range of skills that neither school nor their family could provide. All this in his spare time and with no expectation of remuneration. In today’s performance, money and success driven world, he was almost a person from another time. Peter, we’re gonna miss you here.
The Cavalry Arrives
The Grumman F4F-4 Wildcat was the most significant fighter aircraft deployed in the fightings for Guadalcanal. VMF-223 pilots were the first to land these aircraft at Henderson Field.
Three prominent pilots of the first phase of aerial combat over Guadalcanal: Maj. John L. Smith, commander of VMF-223, Lt. Col. Richard Mangrum, commander of VMSB-232 and Capt. Marion E. Carl, XO of VMF-223.
VMF-223 at Guadalcanal
Pt. 1
Text: Thomas McKelvey Cleaver
Photo: Naval History and Heritage Command
The Grumman F4F-4 Wildcat was the most significant fighter aircraft deployed in the fightings for Guadalcanal. VMF-223 pilots were the first to land these aircraft at Henderson Field.
The sky over the Coral Sea was a deep blue with a few clouds on the morning of August 20, 1942, when a 14th Air Group H6K Mavis operating from the advance patrol base in the Shortland Islands began tracking a cruiser and two destroyers at 1020 hours, transmitting news of the sighting. At 1130, the Mavis reported the three warships were escorting an aircraft carrier when it sighted the auxiliary aircraft carrier USS Long Island (ACV-1), her deck loaded with aircraft. When the message from the Mavis revealing the presence of Long Island was received by Combined Fleet headquarters at Truk, Japanese commanders were elated, but they missed the significance of the carrier the Mavis had sighted, since they knew nothing of the existence of U.S. “auxiliary carriers.” To Admiral Yamamoto’s staff, it appeared Long Island was stalking Admiral Tanaka’s slow Reinforcement Group, which was steaming steadily toward Guadalcanal since departing Truk in two forces on August 16 and 17. Long Island was beyond the range of any Japanese strike aircraft, but Tanaka’s fleet was in range of the unidentified American carrier. Vice Admiral Nishizō Tsukahara ordered Tanaka to turn away from Guadalcanal and turn directly toward Rabaul. If the Americans knew where he was, they might chase him and in so doing come within range of the 5th Air Attack Force’s Bettys.
At 1340 hours, Yamamoto’s headquarters received a message from the Mavis in the next search sector over from first, reporting the presence of a second aircraft carrier and several surface escorts; in fact, this was Long Island and her escorts. The big flying boat was unnoticed by any American radars and eased within 40 miles of the carrier as it continued tracking her course.
Captain USS Long Island, Commander Donald B. Duncan, on the deck of his ship while at anchor in Norfolk, Virginia, October 26, 1941. Note the installation of a makeshift mast.
At 1400 hours Long Island reached her launch point off the tip of San Cristobal Island, 200 miles south of Guadalcanal. The strange-looking ship had begun life on January 11, 1940, as the C-3 cargo liner Mormacmail. Taken over by the Navy March 6, 1941, she had emerged from the yards with her superstructure removed and replaced by a 362-foot flight deck, becoming the first of a new class of aircraft carrier – Auxiliary Escort Carriers – which would over the next few years become the most numerous class of aircraft carriers in the world, by then known as CVEs, which their crews would claim stood for “combustible, vulnerable and expendable.” Long Island’s captain, Commander Donald Duncan, ordered full speed ahead. Black smoke poured from the horizontal funnels on her starboard side as Long Island’s single diesel engine strained to bring the ship to her maximum speed of 16.5 knots – half that of a fleet carrier.
For Long Island and her precious cargo of F4F-4 Wildcats of VMF-223 and SBD-3s of VMSB-232, this was their second attempt to get to Guadalcanal. After less than a month in preparation following notification on July 5 that they were deploying to the South Pacific, the pilots and gunners had packed themselves aboard the little carrier in Pearl Harbor on August 2 and Long Island set sail unescorted into the great unknown of the war-torn Pacific. Their ground crews and other key personnel from MAG-23, and all the necessary ordnance, fuel, and supplies needed to begin air operations departed separately aboard the transport William Ward Burroughs.
On August 9, 1942, completely unaware of conditions on Guadalcanal, Long Island had neared her launch point when Captain Duncan learned of disaster suffered in the Battle of Savo Island the night before. Duncan turned around and headed for the American base at Suva, Fiji, to await clearance to launch his cargo of precious aircraft and pilots. Upon arrival, he informed Admiral Robert Ghormley that most of the pilots were too green to be committed to combat. Ghormley bucked the matter to Admiral McCain, who ordered eight more experienced pilots transferred to VMF-223 from the well-trained but unbloodied Vila-based VMF-212, which would take 223's least-experienced pilots in trade and train them further. On August 14, Long Island departed Suva for Efate to make the swap, but the VMF-212 pilots did not come aboard until the day before the ship departed for Guadalcanal on August 18.
The hangar of the USS Long Island with the Wildcats and Seagulls on June 17, 1942. All aircraft are from VGS-1. A month later, this ship was carrying VMF-223 towards Guadalcanal.
Before taking off from the deck of the USS Long Island ...
The Henderson Field area as it looked shortly after the Marines captured it.
Marines building a defensive line on the perimeter around Henderson Field.
To Guadalcanal!
On the way out from Pearl, the Marines had worried about getting off the carrier while in the Pacific “doldrums” where there was no wind over the deck. Dick Mangrum recalled “we had no idea how far south this equatorial condition would be found, and considered ourselves fortunate to discover our destination was far enough south to be well away from this situation.” With the southeast tradewind adding another 10 knots to the breeze over the flight deck, the crews in the 12 new SBD-3 Dauntless dive bombers checked the gear and equipment – spark plugs, starter cartridges, tool kits, even spare tires – they had stuffed in their cockpits the night before to support themselves for the two weeks they would be on their own before their ground crews arrived. The squadron was six airplanes short of its authorized strength because these 12 had been the only Dauntlesses available in the Ford Island fleet pool when Mangrum learned of their coming deployment. Each Dauntless carried a 500-pound bomb to supplement the small supply on Guadalcanal. According to Mangrum, “receiving orders to bomb-up our airplanes was an eye-opener to just how difficult things were where we were going.” Second Lieutenant Eugene Trowbridge noted in his offically-illegal diary (that he kept regardless): “A lot of excitement today as there are enemy subs all around, and today we get the new experience of being catapulted from the ship as the flight deck is too short to fly off. We are all set to leave. Engines warm and tested, baggage all secured, everything all set. Finally, we’re off.”
The flight deck crew pushed the first bomber into position. Bombing-232’s skipper, Major Richard. H. Mangrum’s 12 years as a fighter and bomber pilot and 3,000 flying hours, made him the most experienced of all 31 pilots in the two squadrons. Mangrum later recalled that “Our launch was delayed to the afternoon since the Japanese visited Guadalcanal at mid-day, and thus, arriving later, we were less likely to get an unfriendly reception from our fellow Marines.”
Two minutes later, 2nd Lieutenant Lawrence Baldinus, a Polish expatriate and former Marine enlisted pilot who had been commissioned after Pearl Harbor and was the most experienced pilot in the squadron after Mangrum, stood on his brakes and ran up his engine, then soared up to join his leader. Second Lieutenant Henry “Hank” Hise, a 22-year-old Texan who had graduated from flight school the previous May with a shade over 200 hours in his logbook, maneuvered his scout bomber on the deck as the crew hooked the airplane to the catapult. He and the other nine “nuggets” had never seen a Dauntless before they reported to the squadron in late June. A minute later, the force of the catapult caused Lieutenant Hise to forcibly pull back on his joystick, pulling the Dauntless’s nose high enough to nearly stall. He quickly jammed the stick forward and fought to keep the bomber out of the water. Regaining control, he joined up on Mangrum and Baldinus.
The first of the 19 blue-grey F4F-4 Wildcat fighters was pushed into position on the catapult. Squadron commander Major John L. Smith made a last-minute check of his engine and controls. Extremely intelligent and able, he had a demonstrated ability to adapt quickly to changed conditions; most who knew him said he often appeared to be in a bad mood. He had only flown fighters since a month before the attack on Pearl Harbor and had worked his young replacements hard since the squadron had been informed, they were headed for the South Pacific. He had never trained other aviators and never been in combat. Fortunately, he was a superb natural fighter tactician, a confident innovator who had painstakingly trained his men to survive against the otherwise unbeatable Zero. He later recalled those weeks spent working to prepare his novices for the unknown rigors of combat: “We all had to qualify on an aircraft carrier, which we did. We spent as much time as we could flying on Saturdays and Sundays and every other day, doing gunnery and dummy runs and anything that would help to give people quick experience or quick training. It was the first experience that I’d ever had trying to train anybody, but it seemed to me that gunnery was the most important thing, so we concentrated on gunnery more than anything else, which was a good thing after we found out where we were going.”
The F4F-4 Smith flew was unlike its predecessor, the F4F-3; this Wildcat sported folding wings, allowing more of them to operate from an aircraft carrier. Armament was increased from four to six .50-caliber machine guns, increasing the weight of fire, though the ammunition load remained the same which reduced total firing time by 14 seconds, an eternity in air combat. Most Wildcat pilots did not see this as an improvement. The weight of the additional guns and the folding wings reduced the already-sluggish performance of the fighter even more. At Guadalcanal, the pilots would need every bit of warning time the coastwatchers could provide to struggle up to 20,000 feet in time to be in position for an attack on the incoming Japanese.
Smith was followed in quick succession by Captain Marion Carl, newly-promoted to Executive Officer, and fellow Midway veteran Division Leaders Captains Clayton Canfield and Roy Corry and their young charges, who had an average of 250 flying hours in their logbooks and were eight weeks out of flight school.
At 1455 hours, Yamamoto’s staff received a report from the second Mavis that the carrier and its escorts were retiring south. Neither of the big flying boats had seen the launch of Marine Air Group 23 to Guadalcanal.
With the Marine aircraft launched, the vulnerable carrier reversed course and headed out of range at full speed. The 31 blue-grey airplanes headed north into the cloudy unknown.
Two hours later, Guadalcanal hove into view. While Smith’s Wildcats flew cover, the SBDs landed. Mangrum followed a ground-control jeep to the dispersal area and jumped to the ground as soon as his plane's engine stopped. He had his hand wrung profusely by General Vandegrift, while thousands of thankful Marines shouted themselves hoarse and pounded one another black and blue in a thundering release of emotion. The cavalry had arrived.
Lieutenant Gene Trowbridge later wrote in his diary: “[We] sight the [air]field at 1600. We are really welcomed by the troops as the Japs have been taking their time bombing them and they figure we will help them quite a lot. We are all bedded down for the night and get ready for a nice sleep when, bang, the whole world seems to explode. The Japs are coming and some of their cruisers and destroyers are shelling us and the troops. It was a trying first night. We are nervous and jumpy as there are snipers all around us, just waiting for someone to stick [his] nose out.”
Invasion on a Shoestring
Once the Allied fleet had retreated from the Guadalcanal area following the defeat at Savo Island, the primary objective for the abandoned Marines was getting the captured Japanese airfield on the Lunga plain operational as quickly as possible. Without air support, they were completely at the mercy of Japanese aerial and naval attacks, and highly vulnerable to ground assault.
Almost as soon as the runway had fallen into the hands of the 3rd Battalion, 5th Marines on August 8, the division air and engineering officers sized things up. They reported they could put down 2,600 feet of usable runway by August 10, and that another 1,200-by-160-foot section could be completed in the week after that. Rear Admiral Turner promised on August 8 that aircraft would arrive on August 11. Unfortunately, when the fleet was forced to retire following Savo Island, they left with nearly all the 1st Engineer Battalion’s equipment that had yet to be unloaded. Construction of the airfield commenced August 9 when the 1st Engineer and 1st Pioneer battalions managed to gather sufficient gear to get started. A miserable 15 percent of their equipment and supplies had been landed, with none of the heavy equipment making it ashore. Thus, they were forced to manhandle 100,000 cubic feet of earth fill to cover the depression in the center of the field that had been left by the Japanese, who had begun their construction at both ends and built toward the center.
The engineers used a huge steel girder as a drag, while a captured Japanese road roller was used to pack the fill. Japanese gear contributed heavily to the small store of engineering equipment available to the Americans, though in general, the captured equipment was in poor condition; ingenious American mechanics kept it working hour after brutal hour in their race against time. The only earth-moving equipment was one angle-dozer the pioneers had managed to land. Dump trucks were nonexistent. The engineers performed incredible feats of improvisation as they overcame monumental difficulties.
On August 18, eight Betty bombers arrived over Henderson in the largest air strike since August 9 as the 25th Air Flotilla began the aerial assault leading up to the first Japanese effort to land troops and retake the island. Forced to remain above 25,000 feet by antiaircraft fire, the bombers did little harm. But it was clear to all that the enemy was resuming work and would be back. As yet nothing stood in their path. A three-ship convoy from Noumea arrived after the Japanese dparted. The ships brought five days of food, which, along with captured Japanese provisions, gave the Marines a two-week food supply. To stretch the supplies as far as possible, the Marines were limited to two meals per day.
Henderson is Ready
On August 19, CUB-1 and the 1st Engineer Battalion reported Henderson was fit to support air operations. The airfield was now 3,800-foot strip 150 feet wide, covered with gravel, with a dirt taxiway and parking area destined to become fields of mud in the many rainstorms. The airfield was surrounded by a tenuously held defensive line extending from Point Cruz on the west to the Ilu River on the east, leaving the field only a quarter mile from a mile-long piece of high ground that would come to be known in Marine history as “Bloody Ridge.” There were no protective revetments and aircraft maintenance would test American ingenuity throughout their time on the island. The only structure on the field was a wooden tower the Japanese had constructed which became known as “The Pagoda.” Time Magazine reporter Robert Sherrod, who landed with the Marines, described living conditions at the field as “appalling” with sleeping choices limited to mud-floor tents or dugouts, with slit trenches close by. Malarial mosquitos were numerous. The fliers would be issued Japanese mosquito netting, something the “mud marines” could only hope for. The facilities were crude, but Henderson Field was ready. It was just in time.
Despite all the effort, Henderson Field could barely be described as an airfield. It was an irregularly shaped blob cut out of the island growth, half in and half out of a coconut grove, with a runway that was too short and too few revetments to protect the aircraft from shrapnel. In mid-September, several weeks after their arrival on the island, MAG-23 group executive officer Lt. Colonel Charles Fike finally wrote the August 20, 1942, entry in the group’s War Diary: “Upon arrival it was found that a servicing detachment of approximately 140 men, commanded by Ensign Polk, of CUB-1, were available for fueling, rearming, and servicing of aircraft. All fueling was done by means of hand pumps directly from drums. Rearming was done without the aid of bomb-handling trucks, bomb carts, or bomb hoists. The enlisted men of CUB-l, although willing and intelligent, had, for the most part, less than four months’ service, as a result of which they required the closest supervision. Considering the attending difficulties, Ensign Polk handled this situation remarkably well. His attitude was at all times cooperative.”
To be continued
A major innovation in the F4F-4 version was the "So-Wing" folding system, designed by Leroy Grumman himself. Here, mechanics demonstrate the system’s space-saving capabilities on an aircraft belonging to VF-3 at NAS Kaneohe, Oahu, May 29, 1942.
Wildcats on Guadalcanal in the fall of 1942. A group of B-17s is overflying Henderson Field.
The air war over Ukraine
During the reported period, from January 1 to February 1, 2023, the offensive operations were expected by either side. The large-scale maneuvers however did not take place. The Russians stubbornly launched mass assaults against the well-fortified positions, with the poor results that could be expected.
A Ukrainian A1-SM Furia drone with the designation 610 and serial number ACM13072 was shot down near Kreminnaya, Luhansk area, on January 31.
Old ways pass to the New Year
Text: Miro Barič
During the reported period, from January 1 to February 1, 2023, the offensive operations were expected by either side. The large-scale maneuvers however did not take place. The Russians stubbornly launched mass assaults against the well-fortified positions, with the poor results that could be expected.
The new year started with so far, the largest one-time loss on the Russian side The Russian command demonstrated the great negligence when hundreds of drafted soldiers were concentrated in the unprotected and unreinforced building of the former high school in Makiivka in Donetsk region. All this regardless the fact that for several months the building exactly like this have been targets of the highly efficient missiles fired from the HIMARS rocket launchers. On the top of it, there was an ammunition dump in the building basement and uncamouflaged vehicles parked around the building. There was no secret that the building housed hundreds of soldiers. The result was a disaster at an unheard-of scale, even by Russian standards. On the New Year the building was hit by rockets and the carnage was topped by the explosion of the stored ammunition. The former school completely collapsed which is confirmed by videos published on the Russian channels. According to the Ukrainian and Western estimates between 300 and 400 soldiers were killed. Even the Russian Department of Defense had to admit to the Makiivka attack. Otherwise, it covers up the Russian own losses. It was announced that 89 soldiers perished, the highest loss the Russians have admitted to so far. Such a Russian confirmation is unusual and indicates that the real losses were high in fact.
This Russian Ch-101 missile crashed after launch while still on its own territory near Ulan-Khola, 140 km from Astrakhan.
A drive for an offensive
Since the fall rains started practically everybody has waited for the weather change, for the ground to freeze, so as the larger scale operations could be resumed. The Ukrainians were on alert for the anticipated large Russian offensive. Unlike a year ago the massive attack did not materialize. The Russians have lost too many combat vehicles. Even though they are being replenished from the reserves the level of training of the drafted soldiers to operate this equipment is low and the whole logistics is in the shambles. Instead of the massive concentrations of its forces the Russian Army attempted the attacks executed by the smaller groups at the various sectors of the front, from the borders of the Kharkov region in the north to the Zaporozhe region in the south. After a half year long effort the Russians achieved a breakthrough at Bakhmut. In the beginning of January, they took advantage of the failed rotation of the Ukrainian troops and captured the little town of Soledar north of Bakhmut. After that the Ukrainians deployed the reinforcements and blocked the Russian advance. The pressure on the town continued from three different directions however and at this time Bakhmut was still holding on. The Russian attempts at capturing the city of Vuhledar further south of Bakhmut, failed spectacularly. The Russian troop were chaotically attacking across the huge, opened area, covered with land mines and under the covering fire of the Ukrainian defenders. The result were tens of combat vehicles destroyed and the whole units decimated.
The crash of a Ukrainian Ministry of the interior H225 helicopter caused a major fire in the town of Brovary on January 18.
Ukraine bought 21 H225 helicopters before the war. Photo: Airbus
The armored fighting vehicles and tanks
To stop these attacks and to prepare their own counter-offensive, the Ukrainians requested the modern armored equipment from their allies. The call was answered in January. First, in the beginning of the month. France committed to deliver AMX-10 RC wheeled combat vehicles armed with 105 mm cannon and after that Germany and the USA made their move. Germany will deliver 40 infantry combat vehicles Marder. The USA have delivered so far 109 proven M2 Bradley vehicles and others should follow. Besides these vehicles however the Ukrainians requested the third-generation main battle tanks. The call was answered in the end of the months when the Great Britain committed to deliver 14 Challenger 2 tanks and shortly afterwards the USA agreed to supply thirty Abrams tanks and several countries will deliver in total several tens of Leopard 3 German tanks. They will be delivered after the Ukrainian tank crews training is completed, currently under way in Britain, Germany and Poland.
Economics professor Oleh Fedirets Ph.D. became an anti-aircraft gunner near Bakhmut.
Long range
For quite some time the Ukrainians demanded from the USA the supplies of ATACMS missiles with 300 km range for their HIMARS rocket launchers. It seems that the compromise was reached in the form of GLSDB ammunition with 150 km range. There is a problem though, these brand-new missiles are not yet in the USA inventory and their deliveries will not be possible sooner than in couple of months. GLSDB stands for Ground Launched Small Diameter Bomb. It was developed from GBU-39 SDB bomb which weighs 113 kilos. These small diameter bombs were designed in a way that an aircraft can carry several of them instead of one large bomb – and hit more targets during one mission. The bomb features the precise guiding system and extended range thanks to its gliding ability.
Boeing and Saab Group cooperated in the development of the ground version of this weapon. They attached the rocket engine to the bomb which will launch it to the altitude on the ballistic trajectory. At that point the rocket engine will be dropped, the bomb will extend its wings and continue its gliding path. Its range is as long as 150 km. The weapon features several advantages. Thanks to its semi-active laser sight it can hit the moving targets- within 100 km on the ground and as far as 130 km at sea. And thanks to its ability to maneuver and turn around in the air it can hit the targets behind the horizon, impossible for the traditional gunnery.
In case the Ukrainians receive these weapons, they will be able to fire them from the M142 HIMARS and M270 MLRS rocket launchers already in their arsenal. Currently, they only have rockets with 70 km range. Using the GLSDB ammunition, based on the current front lines, they will be able to hit the whole occupied region of Luhanks, Donetsk, Zaporozhye and Kherson regions and the upper third of Crimea. The Russians will be forced to relocate their bases, fuel, and ammunition dumps practically outside of the Ukrainian territory. Not even the moving trains and ships will be safe from these gliding bombs. At last, GLSDB is priced more favorably - it costs 40,000 USD as opposed to 1 million USD for an ATACMS rocket.
The machine gun in the nose appeared on several Ukrainian Mi-8s.
A moody night shot of a Mi-8 under preparations at a forward-field base.
A spectacular shot of an unguided missiles firing from a Ukrainian Mi-8 helicopter.
Sea Sparrow fired from the ground
Soon enough another AA defense system will reach Ukraine – and let’s admit, it is urgently needed due to the continued Russian missile attacks on the Ukrainian infrastructure. Following the systems such as Patriot, IRIS-T or NASAMS, part of those has been already delivered to Ukraine, in January the USA announced that one of their military aid packages will include Sea Sparrow rockets. This weapon, used for the ship’s AA defense, were modified for the ground deployment in Ukraine. RIM-7 missiles were developed in 1960s based on the air-to-air AIM-7 Sparrow rockets. While those were later replaced by AIM-120 AMRAAM missiles, Sea Sparrow rockets development continued simultaneously. They are still used today resembling the original Sparrow only by the name.
Sea Sparrow rockets were modified to be used in the modern vertical launch systems. They weigh 230 kilos out of which the warhead represents 41 kilos. Its airspeed is 4250 kph and range 19 kilometers. Besides the aircraft, it can destroy the cruising missiles and certain types of rockets. They are radar guided. The Ukrainians will launch them from Buk systems modified for this purpose. The transfer of three reconnaissance NATO aircraft, known as AWACS, from Germany to Romania can be considered as an indirect form of support. It took place on January 1, and they are to remain near Ukrainian border for at least several weeks.
AWACS is the designation of one of the systems these aircraft carry on board. They are known to public under this name however the official designation is AEW&C which means Airborne Early Warning and Control. For this purpose, NATO uses Boeing E-3 Sentry aircraft operating from Geilenkirchen base in the Western Germany. USA and NATO reconnaissance aircraft were gathering the information even before the Russian attack on Ukraine. Since then, they have been flying outside of the Ukrainian airspace over Romania and the Black Sea. They are capable to find out when and how many rockets and cruising missiles the Russians fired. The operational space however is approximately 2,000 kilometers from the German base, distance the aircraft have to cover each way. After the transfer to the Romanian airbase in Otopeni near Burcharest, the flight to the Ukrainian-Romanian border is approximately 200 kilometers long. The time they can spend on their mission expanded significantly as well.
A Polish-made Krab self-propelled howitzer was saved from a Russian Lancet kamikaze drone by a metal mesh.
The wreckage of a Su-25SM with the fuselage number "Blue 15" and registration RF-95152, images of which were released on January 5.
Secretary of State perished
Most of the aircraft losses is linked to the intense fighting in Bakhmut area. The Ukrainians reported several helicopters (especially Ka-52) and aircraft (Su-25) shot down however their wrecks have not been visually confirmed. Only several losses of the drones could be verified. Su-25SM wreck carrying the bort number “blue 15” and registration RF-95152 was found in the Kherson area. The aircraft had been lost earlier but the images of its wreck were published only on January 5. Obviously, a Su-34, which wreck was shown in the video on January 25 had been lost quite some time before. The Ukrainian forces lost several drones as well. On January 6, the mercenaries from the so-called Wagner group published a video which shows how they, firing the portable rocket launchers, hit an airplane, probably a Ukrainian Su-25. The following day, on January 7, the satellite images were published showing the crashed Ukrainian Mig-29. When and under which circumstances the airplane was lost remains unknown. On January 18, in the morning, a tragedy took place in the town of Brovary east of Kiev where an Airbus H225 helicopter crashed. 14 people were killed including the Ukrainian Secretary of State, his deputy and the state commissioner.
Even before the conflict the Ukrainian Department of State bought 21 H225 helicopters (originally Eurocopter EC225 Super Puma). Deliveries started in 2018. They were used by the Governmental Rescue Service and the National Guard. The aircraft that crashed belonged to the rescue service and there were nine passengers on board – besides the crew members it was Secretary of State Denys Monastyrskyi, his first deputy Yevhenii Yenin, state commissioner Yuri Lubkovich and other department officials. The aircraft was enroute to Kharkiv. According to the eye witnesses the helicopter flew close to the ground but straight and there were no indications that it was having any problems. It flew three circles above the town of Brovary east of Kiev and then it suddenly started to descend, hit a kindergarten, and crashed next to the multi-family residential building. It was dark and foggy at the time of a crash which could have played a significant role in the tragedy. The kindergarten building was set on fire and had to be evacuated. Besides nine people in the helicopter five more people died on the ground, including a child. 30 people were injured out of which 12 were children.
Till the end of January four more Ukrainian airplane losses were confirmed. On January 22, the mercenaries from the so-called Wagner group shot down a Mi-8 helicopter near Bakhmut. Its three-member crew was killed. On January 27, Captain Danylo Murashko was killed near Kramatorsk during the combat flight. He flew Su-25 from 299 Brigade of Tactical Aviation. Another Mi-8 was shot down on January 30 near Novodarovka in Zaporozhiye region on a mission to supply the ammunition. Its three-member crew did not survive. On the last day of January, a Mi-2 helicopter crashed near Poltava it is far from the front line. Therefore, it can be considered a non-combat loss. Two-member crew – 47 years old pilot Vladyslav Stankevych and 46 years old commander Gennadii Butenko, perished in the crash.
Captain Danylo Murasko was killed on January 27 during a combat flight near Kramatorsk.
The crew of Captain Gennady Butenko and Lieutenant Vladyslav Stankevych did not survive the Mi-2 crash during a training flight on 31 January.
Back to Nuremberg
Text: Jakub Nademlejnský
Photo: author
After a long two-year hiatus caused by the COVID epidemic, the Eduard team was back to the Nuremberg Toy Fair once again. The event took place from February 1 to 5 and was held in sixteen halls of the local trade fair center.
It has to be said right at the beginning that this year fair was different from the previous ones. There were significantly fewer exhibitors. In our market segment of plastic model kits, the fingers of just two hands would be enough to count the participants. However, count me in – Eduard/Special Hobby, Italeri, Tamiya, Revell, Airfix. What else? Let’s add to the credit the Art Scale Kit distributor and Zvezda, which had a stand in one of the tucked away booths due to the organizers’ restrictions against Russian companies. Any others? No, nobody else. Other companies from our business chose a more economical option and came only to have a look and go round the stands. And more than we expected stopped at our stand. Among them, even those we hadn’t counted on beforehand. Others didn’t come at all. For example, representatives from China, USA and Ukraine were missing, and the representation from Poland was also quite weak.
But no wonder. The situation is not rosy, so many companies have opted for low-profile and very economical forms of participation. We also chose a more economical option than in the past, and as more attentive readers may have noticed above, we joined forces with a friendly company, Special Hobby, reducing our stand to only two-thirds of its former size. Of course, this led to more intensive communication with our colleagues from Special Hobby, so we were able to discuss further possible cooperation on future projects. However, when more visitors arrived at one point, the booth was a bit tight ... Nevertheless, we handled it without any problems. We also split our team into two parties and rotated with our colleagues after three days at the fair. Saving money is necessary nowadays!
If you have not attended this fair in person in the past, I guarantee you would be impressed anyway. It’s a huge event, with 2,843 exhibitors from 70 countries taking part this year, and over 62,000 visitors from 136 countries visiting the fair over five days. But something in the mood was simply missing. Talking to other people in the industry, it was clear that they had mixed feelings about attending. As the number of exhibitors in the industry dwindles, the importance of the event for us and others is diminishing, and if the situation does not improve, we would at least be very hesitant to decide on participation in future years.
However, as usual, there was a silver lining. In this case, thanks to the low participation of the companies from our business, we were able to conduct more intensive negotiations with visitors to our stand. Several very pleasant meetings took place in a friendly atmosphere with companies from the industry, but also from outside the industry, which may have an impact on the future, for example on our future releases. For example, we arranged the reboxing of Su-25 Zvezda kit and sketched out the negotiations on reboxing of Airfix kits. Representatives of Airfix, Italeri or Revell liked our 3D prints or SPACE for a change, and so possible windows of closer cooperation are opening up for us in the future. As far as the design of the stands of these companies is concerned, Airfix was part of the huge Hornby presentation, where it had its own space among about ten brands that fall under Hornby. And you’ve got to get ready for their new Gannet in 1/48, they say it’s going to be cool! The Italeri booth reminded me of an Italian coffeehouse. Lots of round tables and chairs everywhere, a reception desk, and delicious Italian coffee or a shot of grappa, which gave the negotiations there a touch of Italian flair. The booth was dominated by two large display cases with built models featuring new releases, 1/72 AMX and 1/32 Mc.202 graphics. Revell traditionally had a stand in Hall 12, among the dominant companies in the whole toy industry, such as Lego, Playmobil and Mattel. Revell revealed various new products for 2023, among which I would highlight the Gloster Meteor in 1/32 scale. The only representatives of the exhibiting companies that we didn’t exchange too many words with at the fair were from Tamiya. Their stand was by far the largest in our Hall 7A and was dominated by a track for RC models. So maybe next year ...
The award ceremony of the Modellfan magazine with prizegiving of the Model of the Year awards is one of the traditions of the fair. This year the award went to our Wildcat in 1/48th scale. We are of course happy that our kit is among the chosen ones, but so many are awarded by Modellfan every year that it kind of degrades the whole thing. We already have a bowl full of medals and judging by the display cases of other companies, almost everyone regularly wins a medal for one of its product. We chose to present the awards in the aforementioned bowl this year, as if we had placed them in the display cases, there probably wouldn’t have been much room left to present our products.
To sum up, I would like to say that I was personally impressed by the magnificence and high level of organization of the fair, as it was my first time at this event. They say organization is a common thing in Germany, and it was demonstrated on the spot by the German police, who completely packed up the stand of a Chinese die-cast model seller in short time, and the owners of the stand then sat on a few boxes for the rest of the fair. It all was done supposedly because of plagiarism. In contrast, we had to pack our own things by ourselves on Sunday and arrived home safely. So, hopefully next year again!
The Maltese Falcon
Text: Michal Krechowski
Illustration: Piotr Forkasiewicz
Cat. No. 82126
The Spitfires Mk. Vb/Vc had their most glorious time during the battles for the small, but strategically important, island of Malta. One of the most successful Spitfires to fight there was the Mk.Vc serial number BR301. The aircraft came from a consignment of Spitfires taking off on May 9, 1942, from the carrier USS Wasp (CV-7) during Operation Bowery. Like most Spitfires from the Bowery delivery, BR301 had Dark Mediterranean Blue color applied to the upper surfaces while still on the aircraft carrier’s deck. But the original desert color scheme was slightly visible under this new paint. The lower surfaces were repainted in Sky Blue. This aircraft had also the national roundels overpainted with this color. The original four-cannon armament was reduced to two cannons, mounted in inner position in the armament bay and two inner machine guns. Codenamed UF-S, BR301 served first with No. 601 Sqn., but its pilots achieved most of their success with it in July 1942 after transferring to No. 249 Sqn. There it became the “aircraft of the aces”.
P/O John McElroy (10 victories plus three shared in total) claimed one MC.202 with BR301 on July 7, one Ju 88 shared on July 9 and one Bf 109 on July 13, damaging another one in the process. No. 249 Squadron Leader Richard Mitchell (5 + 3) shot down a Ju 88 on July 23, while F/Sgt John Rae (11 + 2) shot down a Bf 109 probably and a Ju 88, in addition to damaging a Re.2001 and a Ju 88 on July 27 and 28.
The greatest success with the BR301 was achieved by Canadian pilot in the ranks of the RAF Sgt. George Beurling, who destroyed four opponents during one mission (two MC.202 and two Bf 109) and added one Bf 109 on July 27 two days later.
For our boxart, created by Piotr Forkasiewicz, we chose to depict Beurling’s first kill. His victim, a Macchi MC.202, is very well documented both photographically (after the crash landing) and also by combat reports of the two combatants. Thanks to that, we know how it all went down: At 0855 hours on July 27, 1942, No. 249 Sqn. sent out six Spitfires to join other six patrolling Spitfires from Nos. 126 and 185 Sqn. A formation of seven Ju 88s, accompanied by more than forty fighters was approaching Malta, flying at 25,000 feet (7,600 m). Beurling was the first to spot the enemy and radioed to warn the others: “Enemy aircraft at four o’clock, slightly below us!” He immediately launched an attack. The enemy fighters noticed Beurling’s action and went into a left climbing turn. Beurling then got on the starboard side of one MC.202 and fired his characteristic short burst.
Beurling later recalled: “I saw four Macchis flying in a row and I focused on number 4. I fired a short burst that went into its engine and radiator.” The pilot of MC.202 Sergente Magg Falerio Gelli of 378-11 Squadriglia turned his aircraft towards home base, but immediately realized that the smoking engine would not last long enough. He therefore chose a place and belly-landed in a field outside Victoria on the island of Gozo. Later, when questioned, he said: “I saw a Spitfire firing at me, but I didn’t feel any impacts. I was performing evasive maneuvers and noticed that the engine temperature was rising rapidly. In an attempt to reach my base, I turned north, but soon realized I couldn’t make it as the oil tank and radiator had been hit. So, I turned back and landed at Gozo”.
Some pilots and ground staff went to see Gelli’s Macchi. The aircraft was relatively intact, and the battle damage was consistent with Beurling’s report. The rudder was removed and the emblem of the 51° Stormo unit was also cut out of the fuselage as a war trophy. Beurling later posed with the trophies for photographs.
During the five months of fighting in Malta, Sgt. George “Screwball” Beurling scored a total of 28 kills (including one shared) of Axis aircraft, becoming the most successful Allied pilot of the Battle of Malta. These achievements earned him another unofficial nickname: “Falcon of Malta”. It was meant to characterize his straightforward predatory instinct in combat.
Spitfire BR301 was irreparably damaged on July 29 and decommissioned with 54 flying hours.
Stukas under fighter command
Text: Jan Bobek
Illustration: Marek Ryś
Cat. No. 7033
The Ju 87 Stuka units from the Battle of Britain period are mainly known for the heavy losses they suffered on August 18, 1940. However, they returned to combat in early November. Their targets were once again Allied vessels in the Channel.
One of the units that made it through the entire western campaign was III./St.G.1. It was formed in July 1940 from I.(St)/Tr.Gr. 186, which was originally intended to be on board of the aircraft carrier Graf Zeppelin. Gruppe’s commander, Obstlt. Walter Hagen became Kommodore of Sturzkampfgeschwader 1 in mid-1940. His former Gruppe, under the new designation III./St.G.1, was taken over by Hptm. Helmut Mahlke, who served in the Luftwaffe from 1935 after previous service in the Navy.
In early November 1940, well protected by fighters from III./JG 51 and from Galland's JG 26, Mahlke's unit made three attacks on allied vessels within sight of the British coast. . In mid-November, III./St.G. 1 found itself in an unexpected situation. For organizational reasons, it was incorporated under the fighter command of Luftflotte 2, the so-called Jagdfliegerführer 2 (Jafü 2). Its commander was GenMaj Kurt-Bertram von Döring, a World War I fighter ace.
Mahlke had legitimate doubts about how Jafü 2 would handle leading a bomber unit in attacking vessels. His fears were realized on the first deployment on November 14, 1940. This is a transcript of a communication between the two staffs that began at 1100. The document is part of the St.G. 1 Chronicle in the Bundesarchiv collections:
Jafü 2: “III./St.G.1 will attack: enemy convoy reported to have passed Dover in a north-easterly direction towards the Thames estuary. Fighter escort to join at 1445 on the Channel coast. Do not fly beyond Cape Margate due to limited range of escort fighters.”
III./St.G.1: “When and where was the convoy sighted, how many ships and at what speed?”
Jafü 2: “A formation of ships was sighted at 0900 off Dover, medium speed, easterly course.”
III./St.G.1: “Then the convoy of ships will pass Cape Margate before we reach the target area. We request permission to deploy beyond Cape Margate in this case.”
Jafü 2: “The Cape Margate restriction must be respected at all times.”
III./St.G.1: “What is the alternate target if the ship group is not in the restricted area?”
Jaffa 2: “Then attack the other ships in the Dover-Margate section. If there are no ships there: the alternate target is the radio station at Dover.”
III/St.G.1: “If we get to Margate and then turn towards Dover, we'll have the entire British fighter fleet on our tail! - Which radio station at Dover is to be the alternate target, we have 3 radio stations here in the Dover files.”
Jafü 2: “The one with the mirror” (“Spiegel”, German for mirror, a codename for radar)
III./St.G.1: "Which one is it?”
Jafü 2: “We don’t know that either. We will try to find out and tell you before the take-off. Otherwise, just attack the largest radio station in Dover.”
Just as Mahlke predicted, they did not encounter a single ship on the flight to Margate. The formation of nineteen Stukas then proceeded to Dover, where it was attacked by five RAF squadrons. Some of the Stukas had as many as five enemies on tail. Yet some of them managed to drop bombs on Dover facilities. Stuka gunners claimed two victories and RAF fighters reported 16-4-5 Stuka victories. A number of Stukas were hit, but only two were shot down and three more made emergency landings in France. Galland’s fighter escort arrived at the scene of the engagement 10 to 15 minutes late. Kommodore Galland, CO of 7./JG 26 Oblt. Müncheberg and CO of 9./JG 26 Oblt. Ruppert each claimed one Spitfire. However, the RAF lost only one Spitfire from No. 74 Sqn. and two others from No. 66 Sqn. were damaged.
After a few days, a meeting between the staffs of Jafü 2 and St.G. 1 took place. In the process Mahlke and his commander learned that it was a mistake to disband the formation and try to escape from the Spitfires. After a subsequent exchange of views, Jafü 2 no longer required the deployment of the Stukas, explaining that there were no fighter units available as escorts.
Helmut Mahlke retired in 1970 at the rank of Generalleutnant and had not only 159 combat sorties in the Stuka but also a number of flights in the F-104 Starfighter in his flight log. He is the author of Stuka Angriff: Sturzflug, published in English as Memoirs of a Stuka Pilot.
Wasps over the bay
Text: Chris Goss
Illustration: Piotr Forkasiewicz
Cat. No. 7468
Early August 1943, the Bf 110 G-2s of II./ZG 1 moved from Monte Corvino to Lanveoc-Poulmic. Command of II./ZG 1 passed to Hptm Karl-Heinrich Matern, Staffelkapitän of 4./ZG 1. II./ZG 1 was to be used countering increased Allied air traffic over the Bay of Biscay together with Ju 88 C-6s of V./KG 40 and Fw 190s of III./JG 2 and 1./Seeaufklärungsgruppe 128.
August 21, 1943, saw the first victory when the Gruppe claimed a Liberator. This is believed to be from 311 Sqn. and was flown by Wg Cdr Jindřich Breitcetl – all eight crew perished but Uffz Georg Planer of 5./ZG 1 was lost in the combat.
On September 11, 1943, Mosquitoes of 307 Sqn. claimed to have destroyed a Bf 110, probably destroyed two and damaged one. Lt Dieter Bambauer of 5./ZG 1 was lost so was probably the victim of Flt Sgt Zbigniew Dunin-Rzuchowski. Five days later, II./ZG 1 intercepted B-17s attacking targets in western France claiming three, credited to Fw Klaus Schreuer and Oblt Arnold Dorka of 4. Staffel and Fw Emil Pfeiffer of 6. Staffel.
A Liberator of 53 Sqn. flown by Flt Lt Tony Spooner was then damaged by Bf 110s between the Scillies and Lundy Island on September 21, 1943 and three days later, the Gruppe suffered its heaviest losses to date. Despite Ofw Ruhland Zahn and Fw Hans Fuchs of 5./ZG 1 each claiming a Spitfire and Ofw Heinrich Börger and Uffz Peter Schölz of 6./ZG 1 claiming a Mitchell and a Spitfire, four Bf 110s, including those of Zahn, Fuchs and Oblt Arnold Dorka, were lost to Spitfires of Nos. 66, 313 and 610 Sqn. No 98 Sqn. Mitchells were lost but 313 Sqn. lost three which included Sqn Ldr Jaroslav Himr.
II./ZG 1’s time over the Bay of Biscay would now only last another three weeks. On the morning of September 27, 1943, Fw Klaus Schreuer of 4. Staffel claimed a Wellington and 30 minutes later, 5./ZG 1 got a second Wellington. The Wellingtons came from No. 612 Sqn. flown by Flt Sgt Robert Hyndson and No. 407 Sqn. flown by Wg Cdr John Archer, the latter having gone to search for a No. 407 Sqn. Wellington which had ditched off the Scillies returning from the Bay.
Six days later, the Gruppe apparently claimed a Sunderland and a Typhoon. The former was possibly from No. 10 Sqn. RAAF captained by Fg Off Fred Lee while the latter was possibly a Hurricane of 1449 Flt flown by Flt Sgt Richard Adams which was reported shot down 35 miles south-west of the Scillies at 0900hrs.
The end for II./ZG 1 came on October 8, 1943. At 0735hrs, seven Spitfires of No. 453 Sqn. took off on what was called an anti-Me 110 patrol. At 0845 they came across eight Bf 110s and in the ensuing battle, Fg Off Harold Parker was seen to be shot down and Flt Lt Russell Ewins, having shot down a Bf 110, suffered engine failure and ditched. Parker was reported missing, but Ewins was rescued. Another four Bf 110s were claimed destroyed by Fg Off Patrick McDade and Plt Off Colin Leith. At 1330hrs, eight Bf 110s got airborne from Lanveoc-Poulmic looking for two aircraft lost that morning. No. 610 Sqn. were relieving a Mosquito circling Russell Ewin’s dinghy and at 1415hrs bounced the Germans. Fg Off Vincent Moody and Flt Sgt Bob Hussey each claimed a Bf 110 around 1415hrs. Finally, at 1445hrs, No. 66 Sqn. together with 453 Sqn., got airborne to escort aircraft bombing II./ZG 1's home base. No. 66 Sqn. bounced eight to 10 Bf 110s off Brest claiming three Bf 110s destroyed, one probable and one damaged.
The timings for II./ZG 1’s losses are hard to determine. There were some claims by 6. Staffel as Ofw Heinrich Börger claimed a Mitchell, Fw Franz Meissl a Spitfire and Uffz Anders a P-47 around 1545hrs. During the day they lost 11 fighters with three more suffering varying degrees of damage. Those lost included Hptm Karl-Heinrich Matern (who would be awarded the Ritterkreuz the following day – he was possibly lost in the morning as Hptm Rudolf Wangner was leading the Gruppe later that day), Lt Hans-Bodo Busch (Adjutant) while Lt Hans Schmidtal, who was leading 6. Staffel, was wounded. Lt Wolfgang Priebe and his radio operator from 4./ZG 1 were captured after being shot down by No. 610 Sqn. and their interrogation revealed much about the Gruppe but by then it was too late. Having suffered such heavy losses, one more coming on October 14, 1943, when Uffz Max Wichert of 6./ZG 1 crashed due to engine failure off the Ille D’Ouessant, in November, II./ZG 1, now commanded by Ritterkreuz winner Hptm Egon Albrecht, former Staffelkapitän of 6. Staffel, withdrew to Wels where in July 1944 it was disbanded to become the Bf 109-equipped III./JG 76.
Virtue out of necessity
Text: Richard Plos
Illustration: Petr Štěpánek
Cat. No. 8232
In the spring of 1998, a significant event occurred in the Finnish Air Force. The MiG-21BIS was retired from its arsenal and the replacement, the F/A-18C/D Hornet, marked a significant shift for Ilmavoimat. However, the road to this turning point was rather thorny.
Finland was in a difficult situation after the Second World War. Fighting with the Red Army during the Winter War and then the Continuation War had significantly drained its resources and thrown the country into an alliance with Nazi Germany in its fighting for survival. Finland then fought against Germany in the Lapland War after the armistice with the USSR in 1944. The Paris Peace Talks in 1947 limited the post-war development of the Finnish air force which was still using old Bf 109Gs in the early 1950s. The country did not have the funds for modern aircraft, among other things because of the reparations paid to the USSR. However, in 1952 the purchase of six Vampire Mk.52s was agreed by government and Ilmavoimat entered the jet era. But Vampires were obsolete, and the USSR was concerned about the lack of protection of its neighbour’s airspace in a deteriorating international situation. Soviets feared that it could become a “gateway” for a possible strike from the West. Finland was thus threatened that the USSR would use a provision in the 1948 Peace Treaty (YYA) to take over the protection of Finnish airspace, which would have negatively affected Finland’s international position. The result was the purchase of 12 Folland Gnats in 1958.
In the early 1960s, the Soviet Union attempted to persuade Finns to buy the aging MiG-19Ss, but Finnish pilots were already familiar with the Western machinery, including the J 35D Draken or Mirage IIIC thanks to test flights, and so the offer was declined. However, the financial capabilities of Finland did not allow the purchase of these types. On the contrary, the acquisition of Soviet equipment would have been advantageous due to the possibility of repaying it with supplies of goods. In October 1961, the USSR sent another note to Finland demanding increased protection of Finnish airspace, again with a threat of use of the provisions of the YYA. After this crisis was settled, the USSR offered Finland the MiG-21F-13 and on February 1, 1962, a contract was signed for the delivery of twenty aircraft, the first of which were delivered on April 24, 1963.
Just a decade later it was obvious that Ilmavoimat would need another upgrade. The Saab J 35 Draken was selected as a replacement for the Gnats and in the spirit of the ongoing policy of diversification, it was decided that the replacement for the MiG-21F-13 would be procured from the USSR. The Finns requested a presentation of the available types and were offered MiG-23MS and MiG-21bis. The MiG-23 was more expensive and its maintenance requirements were higher, while the MiG-21 was cheaper and already established in Finland. And that made the decision. In the autumn of 1976, Captains Paavo Janhunen and Taisto Myöhänen were enabled to test-fly the type at the Krasnodar base and a year later a contract for 20 aircraft was signed.
The first two MiG-21BISs landed at Risala on September 21, 1978. One of them, coded MB-114, was flown to the test center in Halli, the other, MB-111, was used for pilot conversion training at HävLLv 31 (31st Fighter Squadron). Subsequently, the fuselage designation of the MiG-21BIS was changed from MB to MG, and the remaining 18 aircraft were delivered in three batches during 1980. The MG-129, which is pictured on the boxart by Petr Štěpánek during a landing at Kuopio Air Base was part of the second delivery on July 17, as was its wingman on the painting, coded MG-124. In 1984, it was decided to purchase six more aircraft, so in total the Ilmavoimat operated 26 MiG-21BISs.
All the delivered aircraft underwent avionics and instrumentation modifications by Valmet. The stenciling was translated to Finnish, the aircraft received VHF/COM radios and altimeters of Western origin, as well as VOR/ILS/DME systems and transponders.
In January 1986, the MiG-21F-13s that had served with the Reconnaissance Squadron (TiedLLv) were retired and replaced by MiG-21BISs modified to carry reconnaissance and electronic warfare containers. The reconnaissance squadron was disbanded in 1996, and two years later all Finnish MiG-21BISs were gone…
The Calm Before the Storm
Text: Jan Zdiarský
Illustration: Martin Novotný
Cat. No. 8192
The Avia B.534 is one of the symbols of the determination of Czechoslovakia to stand up against the threat of Nazism that had gripped Germany, and the threat of its spread to other nations in Europe. The attempts to rip away the border regions of Czechoslovakia were obvious from the mid thirties and diplomatic rifts were the order of the day. A strong fighter force was the only way to deter German aggression from the air and to make negotiating meaningful. The Czechoslovak industry lacked the capacity to develop and especially to produce a fast, single engine fighter that could hold its own against the Bf 109 and the fast German bombers of the Luftwaffe. For this reason, the nation turned to the more multi-functional Avia B.534 biplane.
The aircraft’s prototype, designed by Frantisek Novotny, first flew in May 25, 1933. It displayed a very good rate of climb, excellent maneuverability, and, for that time, a good maximum speed, approaching 250mph. Its performance exceeded those of its competition from Praga and Letov. The initial versions had an open cockpit which later was covered, and there was an evolution in the aircraft’s armament, engine cooling system, propeller and on-board equipment. The currently available kit represents the epitome of the B.534, not including the cannon armed Bk.534 which never saw the installation of the cannon firing through the propeller hub, and so production versions were only armed with three machine guns instead of four.
The B.534 entered service at the beginning of 1935. AT the time of increasing tensions provoked by Germany, 27 aircraft were loaned by the army to border guard units.
The main acceptance of the type into service took part in the immediate pre-war years, seeing a growth in numbers from 326 at the beginning of September, 1938 to 443 in March, 1939. The family tree of the type in production can be divided into four blocks, plus the planned cannon armed Bk.534.
The B.534s played their role during both Czechoslovak mobilization periods in May and September, 1938. Their pilots were ready and willing to protect their freedom. As a result of the complete betrayal by Czechoslovakia’s legally bound allies Great Britain and France, culminating in the Munich Agreement and the dismemberment and occupation of Bohemia and Moravia, the B.534 never got the opportunity to put up a fight. In fact, the B.534 became a welcomed prize for the Germans that pressed them into service in their own units and in those of their allies. The type was used by the Luftwaffe, primarily in the advanced training role, and was supplied to Slovakia and Bulgaria, as well as to a lesser extent, Greece. The exception to this are three B.534s that were used during the Slovak National Uprising against the Germans, an event that brought about the last air to air victory to be achieved by a biplane fighter in history.
The painting by Martin Novotny takes us back to the summer of 1937, where the clear sky represents the fragile calm, but history tells us that storm clouds were gathering on the other side of the border. The aircraft bearing the serial number 534.208 was first flown on July 1, 1937 by factory test pilot Oldrich Kosar, and two days later was handed over to Air Force reps. On July 13, 1937, the aircraft was ferried to Kbely, from where it made its way to the 2nd Aviation Regiment at Olomouc, and was later assigned to the 36th Flight.
There, it served with this unit on September 6, 1937, when during a formation flight over Hostynske Vrchy at 6,500m there was a collision involving two B.534s. Jaroslav Sodek, later to become a Czechoslovak member of the RAF, collided with aircraft serialed 208 while flying aircraft B.534.035 as a result of being blinded by the sun. He collided with the second Avia from the left and from behind. The Flight Leader, flying that second plane, was Sgt. Julius Zaoral, who was able to nurse his plane back to Olomouc and land, while Sodek had to take to his chute. The damage to the aircraft flown by the Sergeant was restricted to both the upper and lower left wing and included the interwing struts. The aircraft was repaired and pressed back into service, only to be later taken over by the Germans.
Although the B.534 by 1938/39 would not have the opportunity to stand up to the aggressor, the same could not be said of its pilots. They were, to varying degrees, involved in domestic resistance, and significantly left to oppose the Germans in foreign services of allies that took them to Poland, France, Africa, the Soviet Union, the far east, and most notably, Great Britain.
That, though, leads to other events through history, with which you can get acquainted through other Eduard kits.
Guardians
Text: Richard Plos
Illustration: Adam Tooby
Graphic desing: Jan Zdiarsky
Cat. No. 11170
When Operation Watchtower was launched on August 7, 1942, a “green hell” was waiting for the men of the 1st Marine Division under the command of Maj. Gen. Alexander Vandegrift on Guadalcanal. Though only 2,000 Japanese stood against 6,000 Marines, their fanatical determination did not waver even after fighting for 36 hours, when American forces had captured most of the island, including the airfield under construction. The landing was strongly supported by naval and air forces, with the USS Enterprise’s pilots making 237 combat sorties that day, others added by the pilots from the USS Saratoga. After the Enterprise withdrew from the area, the aerial support weakened and the Marines on the island suffered intense bombing. No wonder they were eagerly awaiting the arrival of the fighters. Those arrived on August 20, when VMF-223 Wildcats landed at Henderson Field.
Air combat and on-site accidents quickly reduced the numbers of aircraft and just ten days after arrival there were only five of the 19 Wildcats left. Even later, after the arrival of reinforcements, the numbers of airworthy Wildcats were rapidly decreasing. The pilots had no choice and no Wildcat from Guadalcanal can be attributed to a particular pilot. In the case of the GUADALCANAL Limited kit, we solved this in a jokey way: Where possible, we assigned a specific pilot to the aircraft he flew in a known event.
The third most successful fighter of the campaign, Capt. Marion Carl, would certainly deserve “his” marking in the kit. But concerning the Wildcat often attributed to him, it’s complicated. The aircraft with the number 2 on the fuselage and nineteen kill marks under the cockpit (marking F) was most likely one he ever flew with. According to the testimony of historians who spoke with the famous ace, Carl said that this aircraft in the well-known photographs was in fact an “hangar queen” pulled out of the hangar at Espiritu Santo to be photographed with the hero by the media. For this purpose, the nineteen kill mark stickers were applied. The media then reportedly took a lot of pictures of Marion Carl at “his” Wildcat. But ...
No matter how much you are searching, you won’t find a proof photo of Carl with this aircraft. Which is strange. In one famous photograph, a man is squatting on the wing, half undressed, wearing a crumpled cap. It’s said to be Marion Carl. But would a pilot, an officer, present himself to the media like that? Hardly ... In several other photos, sitting in the cockpit or standing on the wing is Tech Sgt R. W. Greenwood. The photo of him in the cockpit was published in Stars and Stripes magazine during the war. Firstly with the caption “unknown soldier in the cockpit of a Wildcat on Guadalcanal”. When the editors found out who it was through a letter from a sergeant’s fellow, they published the photo again, this time with his name. The mention of Guadalcanal remained and according to the sergeant’s son, his father never disputed that fact. But historians say this Wildcat never made it to Guadalcanal! But the picture with Greenwood shows the kill marks were worn out and the surroundings on the photo of the whole aircraft looks like Henderson field rather than Espiritu Santo airfield. What’s more, even the official US Navy archive dates the photo to February 2, 1943. At this time Carl was gone from Guadalcanal for some four months! So, there are many questions regarding this aircraft. It is sometimes also attributed to the CO of VMF-223, Maj. John L. Smith, because he achieved nineteen kills, which corresponds to the number of kill marks. But he was also no longer on Guadalcanal in February.
We may never know the full truth about the Wildcat with number 2, but that uncertainty makes it an attractive option as well. We have, however, chosen other Wildcats for the boxart. The one in the background was “Swede” Vejtasa’s personal mount (marking A). For the foreground we have chosen an aircraft that was only marginally related to Guadalcanal, as it was used by 1/Lt. S. B. Folsom shortly after he left the island (marking H). But there are not many Wildcats with such a nice nose art, so it was an obvious choice. The author of the Wildcats on the boxart of the kit 11170 is Adam Tooby and he did a great job, which is supported by the graphics by Jan Zdiarsky. Twelve markings and two complete kits are what is waiting for the modeler inside the box ...
Tail End Charlie
The Golden Era Printed
Can you recall the first accessory set you bought for a kit? Frankly, I don’t. It has been quite some time… I only know I noticed the existence of photo-etched sets sometime in 1992, I would say, and also noted the nice, camouflaged small boxes stuffed with resin parts – detail sets by Verlinden, on the market. As far as I can recall, this producer was really “in” at that time. Amazed by the detail, the supplies of these sets, as well as of the typical flat packages with Eduard photoetch sets, kept growing in my private collection. I never kept any summary of what I spent my money on, leading to some funny moments when, on opening a kit box on which I planned to use my newly acquired accessories, I was met with the exact same pieces already staring back at me from within! Once I even managed to triple one accessory! By the way: who wants some nice Eduard Brassin wheels for the HK Models´ Meteor in 32nd at a very good price?
The wheels are a good example of the “no-problemo” resin accessory, because if one doesn't make any fundamental mistake during the mastering and molding, than all should be OK. In this case, even typical resin shrinkage presents no serious problems. But it is a very different story when it comes to the parts which must be precisely combined with the plastic parts. I think everyone who has ever built a kit with resin accessories knows that: thinning, scribing, placing and, sometimes, shouting … Many of us also experienced a disappointment after opening the box only to find out there are just original plastic parts re-molded with several “easy-to-do-myself” details added. It is even worse when the price of such an “accessory” reaches the price of the kit and the installation of these resin parts requires more effort than to do the detailing using the original kit parts.
And then, after years spent with cast resin sets, 3D printing emerged and the continual progress of this technology led the first enthusiasts to start trying to produce their own home-made parts (the more skilled and daring even made entire models of desired types). Manufacturers, well aware of what was happening, waited for the technology to mature enough to allow for sensible serial production and jumped at the opportunity when it did. Eduard did not stay aloof of this trend, of course, despite its well-established resin casting department. I remember the first attempts about two years ago, when colleagues were testing different materials for printing in search for the right one to use, the one giving the best possible results and was stable enough. And even then, I was impressed with the finesse of the printed parts. Today we have a herd of printers humming merrily along, running at full speed. And the small beauties produced by them make me want to start some super-detailed projects again, after quite a long time. For example, the Wildcat, where the wheel bay, engine and wing folding mechanism sets are really encouraging me to do it!
Anyone who knows something about resin casting knows that a rubber mold does not survive forever and the last part to come out of it will not be exactly the same as the first one quality-wise. And also he knows, there are a number of factors that can affect the result, whether it’s the quality of the air bubble removal in the vacuum chamber, the mix of the material used, the temperature at which it is cast, and so on and so forth ... 3D production is quite a different world! Yes, even the printer can make a mistake occasionally, but it’s visible and the part is discarded during quality control. Otherwise, they’re just like each other, first and last. And since these parts do not shrink, one can also rely on their accuracy. In fact, some of the printed parts seem to fit better than the original plastic parts! And I think it’s a terrible shame that this manufacturing process isn’t fast and cost-effective enough to produce complete kits. It would eliminate the many constraints that limit the detail and sometimes also shape accuracy of parts produced using molds and injection molding machines.
By the way, nowadays even metal parts can be printed with great precision, and perhaps the time is not so far away for printing molds. Such a technology might eliminate at least the milling, maybe even electrode discharging of the molds. Since it is possible to print, for example, H13 tool steel, it may only be a matter of time. Even in this case, 3D printing technology would bring a number of advantages apart from those mentioned.
In any case, 3D printing is a revolution for our hobby, and in combination with other technologies, such as Mimaki printers in our case, it opens up a whole new world of possibilities for the production of perfect accessories. Many modelers keep saying we are in the golden age of modelling thanks to the constant flurry of new kits. But I think the real golden era is coming with the rise of 3D technology.
Richard Plos
Markings for Spitfire Mk.Vc TROP 1/48
BR301, Sgt. George F. Beurling, No. 249 Squadron, RAF Hal Far, Malta, July 1942
Spitfire Mk.Vc serial number BR301 was one of the most successful Spitfires fighting on Malta. The aircraft came from the batch of Spitfires flying off the aircraft carrier USS Wasp (CV-7) on May 9, 1942, during the operation Bowery. Like a majority of Spitfires delivered for the operation Bowery, BR301 had the blue shade of Dark Mediterranean Blue applied already on board of the carrier having the original desert scheme (Dark Earth and Middle Stone) shown slightly through. The lower surfaces were re-painted in Sky Blue including the national markings. The original armament consisting of four cannons was reduced to two in the wing inner gun bays and two machine guns were installed outwards. BR301 coded UF-S first served with No. 601 Squadron however its greatest glory awaited it at No. 249 Squadron where it was transferred. Here it became an “aircraft of the Aces”. Between July 7 and July 13 P/O John McElroy claimed four aerial victories flying it and on July 27, a rising star, Sgt. George Beurling shot down four enemy aircraft in one mission and two days later he claimed another kill with BR301. During the month of July S/Ldr Richard Mitchell and F/Sgt John Rae claimed further kills. On July 29, BR301 was damaged beyond repair and struck of charge having flown 54 hours.
BR476, S/Ldr Jefferson H. Wedgwood, No. 92 Squadron, RAF LG. 173, Egypt, August–October 1942
Jefferson Heywood Wedgwood was born on May 28, 1917, in London. He was educated at Holyrood School, Bognor and Lancing Colleges. In March 1936 he joined the RAF and a year later he became a staff pilot at No. 2 Air Armament School in North Coates. After a brief stint at No. 65 Squadron, he was transferred as an instructor to No. 12 Group Pool in Aston Down. On July 18, 1940, Wedgwood was assigned to No. 253 Squadron at Kirton-in-Lindsey with which he took part in the famous Battle of Britain. During the month of September, he destroyed a Bf 110 and cooperated in destroying five Ju 88s and three Do 17s. At the end of September, he was ordered to Vickers Supermarine where he flew as a Production Test Pilot but on October 10 he was transferred to the RAF Czechoslovak Depot in Cosford as a flight instructor. In January 1942 he assumed command of the No. 92 Squadron in Digby. In February the unit was transferred to the Near East and in April it arrived in Egyptian Fayid. For several month the unit was without any airplanes and as of July 2 the pilots were attached to the No. 80 Squadron in the Western Desert to gain the operational experience. Finally, in the end of August 1942, the tropicalized Spitfires arrived. Between August 14 and October 29 Wedgwood destroyed eight Bf 109s and damaged another eight. For his accomplishments he was awarded DFC. On December 17, 1942 he was on board of a Halifax Mk.II from No. 138 Squadron as a passenger flying back to the Great Britain but the aircraft crashed near Żejtun on Malta. It is highly probable that it was shot down by a friendly AA fire and all on board perished. Jefferson Wedgwood is buried in the Navy cemetery in Capuccini on Malta.
JG959, Lt. McClellan E. S. Robinson, No. 1 Squadron SAAF, Ben Gardane, Tunis, April 1943
Pilot’s full name was McClellan Eric Sutton Robinson, and his usual nickname was “Robbie”. He was born on February 26, 1919, in Johannesburg. His first operational unit was No. 1 Squadron SAAF flying Hurricanes. He was assigned to the unit in August 1942 and remained flying with it for a year. On November 2, 1942, he achieved his first combat success when he shared victory over a Ju 87. After he converted to Spitfire Mk.V, between January and April 1943, he added another five victories to his score. After that he had bad luck for the first time when on July 14, 1943, he was shot down by a friendly fire of a USAAF P-38 and had to bail out over the Mediterranean sea. He got lucky though as he was fished out by the crew of a Greek destroyer. In September 1943, at the end of his tour of duty, Robinson was awarded DFC and sent back to the Great Britain where he assumed the post of a flight instructor at No. 11 OTU. On November 14, 1944, the bad luck struck again as he collided mid-air with one of his students flying Kittyhawk, crashed and was killed. All his personal Spitfires carried the inscription CireCooks on the port side which was the combination of his first name and last name of his fiancé. Number VI indicated it was the sixth airplane christened with this name. On April 22, 1943, flying this aircraft, Robinson shot down two Bf 109Fs. During his combat career he shot down in total five enemy aircraft plus one probable and one aircraft damaged.
Lt. Luis T. Zendegui, 2nd FS, 52nd FG, 12th AF, La Sabala, Tunis, Winter 1942–1943
One of the successful pilots flying with 2nd FS was Cpt. Luis Zendegui who scored his first victory on December 25, 1942, during the dogfight with Mc.202. During his service with 2nd FS he was credited with three confirmed kills and he damaged another two enemy aircraft. Zendegui’s Spitfire carried the pilot’s name on the drop tank and the American flag on the fuselage sides. The original British cockades on wings and fin flash on the vertical tail surface remained intact. The squadron white codes QP were not yet applied on Spitfires during this period. Some sources assign serial number ER148 to this Spitfire, however it cannot be found in the database of the Spitfires’ serial numbers.
MH592, S/Ldr Hinko Šoić, NOVJ No. 352 (Yugoslav) Squadron, Vis, Yugoslav, January–February 1945
No. 352 (Yugoslav) Squadron was the first Yugoslav fighter unit established at Royal Air Force in Mediterranean during WWII. This unit is also known as the Prva Eskadrila NOVJ. In June it converted to Spitfires Mk.Vb/Vc and in August the unit was transferred to Italy to join RAF No. 281 Wing and provide the escort for the fighter-bomber squadrons. As of January 25, 1945, it was deployed to the forward base on the island of Vis. Due to the absence of the Luftwaffe aircraft the Yugoslav Spitfires had very little opportunities for the air combat and for the rest of war they flew the ground attack missions. Šoić’s Spitfire MH592 sported the type “B” desert camouflage scheme and as the only Yugoslav Spitfire featured the Aboukir dust filter (the rest of the aircraft featured Vokes filters). Also, Hinko Šoić as one of very few Yugoslav pilots encountered the enemy aircraft and in the cooperation with another three pilots shot down a Henschel Hs 126 on March 20, 1945. In this Spitfire he flew 73 missions altogether, further six missions were flown by other No. 352 (Yugoslav) Squadron pilots.
A58-137 (EE835), F/Lt David H. Hopton, No. 79 Squadron RAAF, Kiriwina, Trobriand Islands, October 1943
Spitfire serial number EE835 arrived in Australia on April 13, 1943. Before it was delivered to the combat unit it had been repainted in Foliage Green/Earth Brown/Sky Blue. In May it was handed over to the No. 79 Squadron RAAF as A58-137 and the code letters UP-T were applied. It was assigned to F/Lt David Hopton who christened his new Spitfire by the phrase “Down with everything” and had a naked girl painted on the port side of the fuselage. Hopton flew this Spitfire until November 28, 1943, when the fuselage drop tank was not released correctly and damaged the aircraft’s tail. The repaired airplane was returned to the service in October 1944, assigned to No. 85 Squadron and coded SH-W. The camouflage was stripped, and it flew in the natural metal color finish. On February 26, 1945, during the landing at Guildford, the pilot F/O B. O’Connell collided with another Spitfire and A58-137 was struck off charge.
Markings for F4F-4 Wildcat 1/48
Lt. Stanley W. Vejtasa, VF-10, USS Enterprise, April 1943
Unusual surname and blond hair were equally responsible for the nickname “Swede” for Stanley Winifield Vejtasa, a man with strong Czech roots as a grandson of immigrants from then part of the Austria-Hungary Empire. He made himself famous when he managed to shoot down three Zeros while leading a formation of eight SBD-3s tasked with the air cover of the US ships during the Battle of the Coral Sea. This achievement gave him opportunity to join VF-10 fighting squadron as its Operations Officer. There he scored seven more kills during the Guadalcanal campaign on board of the USS Enterprise. After the war he enjoyed a great career, making him the Captain of USS Constellation and CO of the Miramar base. He retired in 1970 and died on January 23, 2012, at the age of 98. The Wildcat No. 79 took over the starboard side panel with eight kill marks from the No. 19 (BuNo. 03417) Vejtasa used before. Ninth kill mark was added on November 13, when he shot down one huge Kawanishi Type 97 Mavis flying boat. Some of the Wildcats sported the kill marks on both sides, but only starboard of this Wildcat is known. This hangs question mark on their port side presence. Also, the white vertical rudder strip is not sure for the period of the early 1943.
BuNo. 5192, Ens. Mortimer Kleinmann jr., VF-5, USS Saratoga, August 1942
This is a reconstruction of the aircraft, assigned to and usually flown by Ens. Mortimer “Junior” Kleinmann. But on August 7, 1942, during the rush to take off against Japanese bombers as soon as possible, Lt. James Julien “Pug” Southerland jumped the plane and took it off against the enemy. He managed to shoot down two bombers but during the consecutive dogfight with Zero he learned his guns would not fire, probably due to the damage from fire by the tail gunner of the bomber. To make the things even worse, two more Zeros joined the fight. Pug was able to outmaneuver them, but the melee was spotted by Saburo Sakai. The Wildcat was hit by numerous shells from machine guns and cannons, but kept flying, until a Zero gave him a burst into the left-wing root setting it afire. “Pug” bailed out over the enemy territory of western part of Guadalcanal. Wounded and weaponless he managed to escape the Japanese soldiers thanks to the help of natives and was evacuated from Henderson Field on August 20, 1942. Later he added three more victories with F6F-5 and died in flying accident on October 12, 1949. Mortimer Kleinmann achieved two kills during the time USS Saratoga was taking part in Guadalcanal campaign.
Capt. Joseph J. Foss, VMF-121, Henderson Field, Guadalcanal, October–November 1942
This is one of the Wildcats of VMF-121 the highest-scoring ace of the Guadalcanal campaign, Capt. Joseph Jacobs Foss, used during the combat missions. The Bureau Number is unknown, but we know Foss scored with nine different Wildcats. This speaks of itself as the Marine pilots on Guadalcanal did not have the luxury of assigned aircraft. Not even the best ones. The fierce combats, harsh environment and other factors made the Wildcats rather consumable goods, and the pilots simply jumped the closest airworthy aircraft. Joe Foss, former flying instructor, joined VMF-121 on August 11, 1942 and was promoted to Captain on the same day. He arrived at Guadalcanal on October 9 and four days later scored his first victory, shooting down a Zero. His score was rising, as he shot down 16 enemies during October and prior to his farewell to the island his score raised to 23. He had to bail out himself on November 7 after shooting down one Rufe and two float biplanes and made it back to the base in three days. The VMF-121 left Guadalcanal on November 19, but Joe returned to Guadalcanal for his final tour there from January 1 to January 26, 1943. Adding three more kills, he became the highest scoring USMC ace of WWII. After the war, he served in the South Dakota Air National Guard, which he helped to organize. Later he turned to politics and was elected to the South Dakota House of Representatives but returned to the duty during Korean war. In 1954, Foss was elected Governor of South Dakota. He passed away on January 1, 2003.
BuNo.02062, Mach. Donald E. Runyon, VF-6, USS Enterprise, September 1942
Donald Eugene Runyon was a petty officer Aviation Machinists Mate 1/c and he was so skilled he had officers for wingmen. He scored six times with Wildcat. This one served him well to get two of his victories at the very start of the Guadalcanal campaign on August 8, when he shot down Zero and Betty. A day before, he also shot down two enemies with aircraft BuNo. 02125. He joined VF-3 in December 1942 and stayed with the unit until April 1943. He did not achieve any aerial victories with the unit, but the things changed when he joined VF-18 based on the USS Bunker Hill in September 1943. There, already flying Hellcats, he added three more kills to finish the war with 11 victories. He was promoted to Lieutenant (junior grade) rank in May 1943 and to Lieutenant on July 1, 1944. He was a test pilot at Moffett Field from July 1945 to July 1946 and served with several units until July 1964, when he retired in the rank of Commander. The Wildcat BuNo. 02062 sported the unusual painting of the tombstone with 41 Japanese roundels symbolizing total score of the VF-6 during their fighting of Guadalcanal Campaign. Such a painting sported only nine Wildcats of the unit, the ones which stayed on the deck of the USS Enterprise on her route from the Solomons to Hawai. Other Wildcats were flown to USS Saratoga or to Guadalcanal.
1/Lt. Jefferson J. DeBlanc, VMF-112/121, Henderson Field, Guadalcanal, January 1943
During his two tours of duty, Jefferson Joseph DeBlanc scored nine kills in the combats during the Guadalcanal and Okinawa campaigns. That made him 11th highest scoring Marines ace. During his mission on January 31, 1943, when escorting SBSs to attack Japanese ships, he detected a serious fuel leak, which made his return to base unlikely. He requested that rescue forces be altered and continued the mission, which resulted in a fierce combat with Japanese Ki-43 Oscars. DeBlanc managed to shoot down five of them but was wounded and had to bail out himself from his crippled and smoking Wildcat. After many mishaps he finally managed to get back to the base and to the hospital on February 12. This Wildcat also received an enemy burst. It happened on November 12, 1942, with 1/Lt. Sam Folsom at the controls. He managed to get it home and the Wildcat was repaired. Mechanics used white aircraft-fabric patches to cover the bullet holes, but the patches lost their white color soon in harsh, dusty environment … DeBlanc was one of the pilots to use it, although it was assigned to VMF-121, while he was a member of VMF-112.
Guadalcanal, Henderson Field, early 1943
Although good photos of this Wildcat are available, there are many questions regarding its identity. Usually, the aircraft is referred to 1/Lt. Marion Carl of VMF-223 or the CO of this unit, Maj. John L. Smith. Both were bright stars of the early stage of the Guadalcanal campaign amongst USMC pilots. The VMF-223 was the first one to land on Henderson Field together with VMSB-232. From August 20 they were frantically fighting Japanese aircraft until late October. Carl got 16,5 of them, Smith 19. That’s one of the reasons this Wildcat is sometimes referred to latter, as it sports 19 kill marks. But the photos are dated to February 1943 when the VMF-223 was gone from Guadalcanal. According to some sources, Carl himself stated this aircraft was a non-airworthy aircraft he used for photo session with media at Espiritu Santo, following the end of the tour on Guadalcanal (i.e., in second half of October). Together with a mechanic, they reportedly put 19 kill mark stickers on. But there are no photos of Carl with this aircraft or in the cockpit ... More to it, other photos show visibly stained kill marks, one of them dated to March 22, 1943. Conclusion? It might be operational aircraft changing units and sporting the kills of all the pilots flying it. Or it might be really used for some photo session on Espiritu Santo in late October, but repaired and sent to Guadalcanal, keeping these kill marks applied. There were repairs on the right wing and on the fuselage, while roundel on the upper side of the left half of the wing showed some damage.
BuNo. 12034, VMF-221, Henderson Field, Guadalcanal, February 1943
This aircraft is usually attributed to 1/Lt. James E. Swett, a member of VMF-221. The squadron was based at Marine Corps Base Ewa on Oahu, Hawai in early 1943, from where they moved to the island of Espiritu Santo aboard the USS Nassau. Most probably during their stay at Espiritu Santo, various arts were painted on the vertical fins of some of the squadron’s Wildcats. In the case of No. 77, the painting was probably inspired by “Hairless Joe” from Al Capp’s strips made for L’il Abner satiric strips (it was painted on the port side only). The squadron was moving to Guadalcanal in stages from February 1943 and there the “tail arts” became a thorn in the side of the commanding officers. So, probably not long after arrival, an order was issued to remove all the paintings. Lt. Swett was a leader of one of flights of VMF-221. He took off for his first combat flight on April 7 when the Japanese made a massive raid, sending approximately 70 bombers against Guadalcanal, covered by more than hundred Zeros. More than a hundred of American naval and Army fighters took off to defend the island, and the most successful among them was Swett, who managed to shoot down seven Val bombers before having to bail out himself. This was his only encounter with enemy aircraft in the cockpit of a Wildcat, as he subsequently switched to the Corsair and achieved 15.5 kills during his 103 total combat missions in WW II.
1/Lt Samuel B. Folsom, VMF-121, Samoa, spring 1943
Nose arts were rare on the Navy and Marines aircraft, especially during the Guadalcanal campaign, where was no time or resources to “play” with drawings. The Wildcat with the painting of Popeye on the port side of the engine cowling is one of rare exceptions, but it was not painted on Guadalcanal. In fact, the aircraft was part of the VMF-111 inventory, the unit which was operating on Samoa. Sam Folsom had the Popeye painted on the engine cowl when he was assigned to the unit as an instructor after his combat tour at Guadalcanal. The aircraft is sometimes portrayed with “winged” roundels, which is not correct. At the time the photographs of the Popeye Wildcat were shot, is still sported the original roundels. Folsom was rather inexperienced pilot when he was thrown with others of VFM-122 into the battle of the Solomon Islands, but he was progressing rapidly. He stayed there for three months and was wounded twice. He scored his first kill on November 11, when he shot down a Zero. Just a day later, he shot down a Mitsubishi Betty bomber and added another one to finish the war with three victories.
BuNo. 11985, Lt. (jg) William N. Leonard, VF-11, Guadalcanal, June 1943
Bill Leonard took part in the battles at Coral Sea and Midway, where he made himself an ace during his service with VF-42 and VF-3. In August 1942 he joined new VF-11 squadron and became its Operations Officer. He served at Guadalcanal in 1943 and added two more kills to his tally. It happened on June 12, 1943, when he shot down two Zeros flying this aircraft and this achievement made him the ace. After his three-month tour in Guadalcanal, he was transferred to Samoa, ending his time with VMF-121. Leonard’s Wildcat sported the Sun Downers symbol painted on both sides as well as four kill marks (six after June 12). The panels with the VF-11 symbol and port side under the cockpit were repainted, probably by fresh camouflage color. The same pays to the area of the fuselage code.
Lt. (jg) Francis R. Register, VF-11, VC-21, USS Nassau, May 1943
Francis Ronald Register enlisted to Navy on February 17, 1941, and joined the VF-3 squadron on January 4, 1942. While still on USS Saratoga, he changed the unit for VF-6 and saw combat in the Eastern Solomons. He managed to shoot down two aircraft on August 24, one of them identified as Zero and the other strangely as “Me 109”. After the Saratoga was torpedoed on August 31, he joined VF-5, based at the Guadalcanal, and added two more victories on September 12 and 13. Two weeks later he entered the prominent club of fighter aces by shooting down two Zeros and prior to leaving the “Death Island”, he added two more victories and one probable. On March 23 “Cash”, as was his nickname joined his old VF-3 unit but was detached to Composite Squadron 21 (VC-21) just four days later. On board of USS Nassau, he was set to participate in the Aleutian Campaign, but perished there in the flying accident. The aircraft he boarded the USS Nassau sported seven kill marks from the Gauadalcanal, and the white stripes on the horizontal and vertical stabilizers, distinguishing the aircraft of the fights for Attu Island. Register’s diary describing in the raw manner the harsh living on Guadalcanal is available on Internet.
VF-11, Guadalcanal, May 1943
As there were not too many possibilities and opportunities to adorn the aircraft with any personal paintings, the Wildcats on Guadalcanal were uniform regardless the unit. But there were some attempts to make the aircraft at least a little bit specific by easier means. This F4F-4 is an example as the page from the 1943 Esquire calendar with the January girl painted by the famous Alberto Vargas was glued to the port side of the engine cowling. More to it, on starboard side the inscription “Nylorac” was painted (a slang word meaning somebody who gets close personally, then betrays and hurts you). The short movie shows Lt. Gordon Cady standing by this Wildcat, but it is the only indication about any link between this Wildcat and him. The VF-11 was divided into flights of four aircraft and Cady was leading the second one, which assigned his aircraft number 5, while No. 17 was the aircraft of the leader of the 5th flight, Lt. Raymond “Sully” Vogel. But Vogel damaged his Wildcat in the collision with the aircraft of Lt. (jg) Maxwell on May 2, 1943 and “the new No. 17” might be the Nylorac … Cady shot down two Zeros and Vogel added another one kill in the same combat on June 7.
Lt. (jg), Charles R. Stimpson, VF-11, Guadalcanal, June 1943
Charles Russell Stimpson was 16-victory ace, ranking him eighth in the Navy list of aces, sharing this position with Ira Kepford. Stimpson enlisted in the Navy on June 17, 1941, the pilot training followed. He joined newly formed VF-11 in the summer of 1942 and served with the unit until February 1945. He served at Guadalcanal from May to July 1943, achieving six victories there. His maiden fighter success came on June 16, when he shot down four Vals flying this aircraft. According to some sources, he was flying Wildcat BuNo. 12163 at the time. Four kill marks were applied under the cockpit of the aircraft named “Missie” of the unknown BuNo. It might be the 12163 but it is not certain. Stimpson shot down two Zeros in July 1943 in the cockpit of the same aircraft and added ten more kills in 1944, while still with VF-11 but flying Hellcats. After serving as a flight instructor from April to September 1945, he was released from active duty on October 11, 1945.
Markings for Bf 109E-4 1/72
WNr. 5819, Obstlt. Adolf Galland, CO of JG 26, Audembert, France, October–December 1940
Adolf Galland, the ace and future General, flew the portrayed Emil during through fall of 1940 up to the beginning of 1941. He was CO of III. Gruppe at the time, later he took command of the entire JG 26. The tactical markings on the aircraft kept pace with these promotions. The standard camouflage of RLM 02/71/65 was darkened on the fuselage sides with RLM 02/71. The yellow cowling was complemented by the yellow rudder which also sported kill marks. The surface area of the original RLM 65 was not large enough for them, and so the yellow was oversprayed with fresh RLM 65 for the next row of kill marks. The most typical changes for WNr. 5819 at this time came with the personal emblem of Mickey Mouse and most of all the installation of the ZFR-4 telescope (installed together with the regular Revi). It didn’t serve as an actual sight as it did for the identification of distant aircraft. After the death of Werner Mölders Galland replaced him as the German fighter force commander (General der Jagdflieger). Later he became famous for locking horns with Hermann Göring. He established JV 44 at the end of the war, the unit well known for its Me 262 jet fighters and colorful Fw 190Ds. Galland managed to shoot down 104 enemy airplanes and was awarded with Knight Cross with Oak Leaves, Swords, and Diamonds.
WNr. 1559, Hptm. Wilhelm Balthasar, CO of 7./JG 27, Carquebut, France, July 1940
The future Knight Cross with Oak Leaves recipient Wilhelm Balthasar was born on February 2, 1914, in Fulda. In 1933 he joined Reichswehr, in 1935 he was transferred to Luftwaffe by his own request and underwent the pilot training. During the Spanish Civil War, he initially served with bomber and reconnaissance units, since September 1937 with fighter detachment of the Legion Condor. In March 1938 he returned to Germany. At the outbreak of World War II Oblt. Balthasar served as 1. Staffel JG 1 commander. This unit saw combat for the first time during the offensive against The Netherlands, Belgium and France. It was the time when Balthasar demonstrated his marksman skills as he shot down 23 enemies during the Western Europe campaign. As of June 5, 1./JG 1 was re-designated as 7./JG 27. On September 1, 1940, he was promoted to command III./JG 3 and in the air battles over the Southern England he achieved further seventeen kills. In the meantime, on February 16, 1941, he was appointed Commanding Officer of JG 2. Balthasar run out of his luck during the combat with the RAF fighters over Aire on July 3, 1941. In the dive, the wing of his Bf 109F-4 wing collapsed and Balthasar perished at the impact with the ground. Balthasar’s aircraft, camouflaged in RLM 71/02/65 colors, carried the non-standard marking on the engine cowling. There is a unit marking painted under the windshield, kill markings are painted on the vertical tail surface and rudder.
WNr. 5587, Ofw. Fritz Beeck, 6./ JG 51, Wissant, France, August 1940
Simple but effective camouflage adorned this aircraft that was shot down with Ofw. Fritz Beeck at the controls in the vicinity of East Langdon shortly after noon on August 28, 1940. It was during the second escort mission of the day that culminated in combat with RAF fighters in which the engine of Yellow 10 was hit. After an unavoidable forced landing, the aircraft, in relatively good shape, was made otherwise by civilian vandals and allied soldiers before it could be inspected by RAF experts. Light blue sides of the RLM 02/71/65 fuselage scheme were sprayed with the upper surface colors. Yellow identification colors, typical for mid-August 1940, were applied to the wing tips, horizontal tail surfaces, and top portion of the fin. Because the aircraft in question belonged to 6. Staffel, tactical numbering and the background II./JG 51 “Gott strafe England” emblem were yellow. Three victory marks on the left side were in white. It is not out of the question that these also appeared on the right side, but documentation is lacking.
WNr. 5901, Oblt. Walter Fiel, CO of 8./JG 53, Le Touquet-Etaples, France, September 1940
After the Luftwaffe tactics changed during the Battle of Britain, when the bombing of London and Southern England was switched to night operation, the decision was made to use certain Staffels in the fighter-bomber roles and to lure RAF fighters into combat. One of these units was 8. Staffel JG 53 commanded by Oblt. Fiel. On October 2, during his unit’s attack, he was attacked by superiority of Spitfires. His aircraft was damaged and made to force-land nearby the little town of East Peckham in the Kent County. The pilot was taken a prisoner of war. The camouflage in RLM 71/02/65 colors was supplemented by the gaudy marking in the form of yellow engine cowling and rudder. The original aircraft’s marking was probably oversprayed with RLM 70 color, the unit marking, originally located on the engine cowling, was overpainted in the red stripe wrapping around the whole engine cowling.
Lt. Josef Eberle, 9./JG 54, The Netherlands, August 1940
A very interesting camouflage was created in the summer of 1940 by the ground staff of JG 54 on many of unit’s aircraft in an attempt to darken the light blue fuselage sides of their Bf 109Es. To achieve such an effect, they sprayed vertical to diagonal stripes with RLM 71 paint. The standard scheme of RLM 02/71/65 was applied along with the quick identification elements. The period scheme was applied to Yellow 13 with which Lt. Josef Eberle managed to cross the Channel and belly land in France despite personal injury on August 12, 1940. The wingtips and fin of Eberle’s aircraft were painted RLM 27 Yellow, which was lighter than the color of the spinner, tactical number and background of the III./JG 54 emblem. The white color cannot be ruled out on the wingtips and fin as well. The bottom wing RLM 65 color extended marginally to the upper surface. Some sources erroneously identify this aircraft as an E-3. Despite having tempted fate once over the Channel, Eberle was not as successful on October 9, 1940, when he lost his life in combat with RAF fighters.
WNr. 2060, Lt. Hans Guse, 2.(J)/LG 2, Tudora, Soviet Union (Republic of Moldova today), July 1941
Like JG 77, Lehrgeschwader 2 was withdrawn from the combat operations after the end of the Greek campaign for rest and rearmament, which was to take place in Belgrade. This was followed in mid-July by a move to Romanian territory, where LG 2 equipped by Messerschmitts Bf 109E (some in the fighter-bomber configuration) was on alert to be deployed against the Soviet Union. It joined Operation Barbarossa in the early hours of July 22. The Black 10, which retained its camouflage from the battles over Greece and Crete and was equipped with a tropical filter, was shot down on July 10, 1941, by Soviet I-16s. The pilot is still listed as missing in action. The markings of the aircraft are complemented by the insignia of I.(J)/LG 2 under the windshield and 2.(J)/LG 2 on the side behind the fuselage cross.
Markings for Bf 110G-2 1/72
Bf 110G-2/R7/M2, 6./ZG 1, Brest, France, August 1943
In August 1943, 6./ZG 1 moved from Sicily to Brest, France, where the unit was tasked with escorts of German submarines on their way across the Bay of Biscay to the Atlantic. The standard camouflage scheme of RLM 74/75/76 colors was darkened on the fuselage sides with patches of the same colors. The unit’s emblem was a drawing of a wasp on the nose, additionally supplemented on the left side of the fuselage under the cockpit by a drawing of a witch on the S9+LP. The color of the 6. Staffel was yellow hence the aircraft code is yellow and the same applies to the color of the spinner. The aircraft had also a white stripe on the fuselage in front of the tail surfaces, which was a remnant of the unit’s time on the Southern Front in Italy.
Bf 110G-2/R3/M1/M5, 7./ZG 26, Fels am Wagram, Austria, May 1944
Due to the intensification of Allied air raids from Italy on the southern areas of the German Reich, 7./ZG 26 was relocated to Fels am Wagram airfield in May 1944. The unit’s aircraft had the tips of the spinner and the third letter in the code painted white, which was the color of the 7. Staffel. The black code letter K was painted also on the bottom of the wingtips. The 3U+KR sported a white fuselage stripe in front of the tail surfaces and white bottom of wing tips. Both were the designation of aircraft operating on the southern front. Two MK 108 guns of 30 mm caliber mounted in the nose were the Rüstsätze 3 kit add ons. Additional armament were WGr. 42 rocket launchers under the wing.
Bf 110G-2/M1/R7, 5./NJG 200, Nikolayev, Soviet Union, September 1943
In September 1943, 5./NJG 200 was based on the airfield near the town of Nikolayev in Ukraine. The pilots were tasked with night interception of VVS (Soviet Air Force) aircraft. This machine was camouflaged with standard RLM 74/75/76 colors. The distinguishing color of 5. Staffel was red hence both the codes and the tips of the propeller cones were painted so. The aircraft had a yellow stripe on the fuselage in front of the tail surfaces, which was a distinguishing feature of machines operating on the Eastern Front and in the USSR.
Bf 110G-2/R1, 4./ZG 76, Wertheim, Germany, October 1943
Dispersed Zerstörer units were called up from all over Eastern Europe and the Mediterranean to be incorporated into the defense of the Reich. ZG 76 was rebuilt in southern Germany with the use of the personnel of training and reconnaissance units and ZG 76 stayed there through the winter of late 1943/44. Its aircraft were armed with a 37 mm BK 3.7 cannon under the fuselage and WGr. 42 rockets to scatter American bomber formations. On October 4, 1943, the American Eighth Air Force attacked targets in Frankfurt am Rhein. II./ZG 76 encountered the stream of bombers alone and shot down four American bombers. But they encountered the American 56th Fighter Group afterwards and without their own fighter escort nine Bf 110s were shot down in the ensuing battle. Eleven of the downed crews were killed and seven wounded. The introduction of the American long-range fighter escort meant a large increase in losses for the Zerstörgeschwader units. In November 1944, 4./ZG 76 was disbanded and its pilots were retrained on the Bf 109, subsequently transferred to the 9./JG 54 fighter unit.
Markings for MiG-21bis 1/48
MiG-21BIS, c/n 75084300, HävLLv 31, Kuopio airbase, Finland, 1980 – 1981
This aircraft was accepted for service on July 17, 1980 and assigned to 31 Fighter Squadron (Hävittäjälentolaivue 31, abbreviated HävLLv 31). It became the last of six Finnish MiG-21BIS fighters to be modified for reconnaissance tasks. After the modification, the aircraft was assigned to TiedLLv (Reconnaissance Squadron) and following its end of service it was used as a teaching aid at the Technical School located at the Kuopio Air Base. The aircraft is shown as it appeared between 1980 and 1981 before being upgraded by western avionics, which included cockpit instrumentation. Unlike other users, Finland used capital letters for designation of their MiGs, that’s why it is written as BIS here as well.
MiG-21bis, c/n 75080880, 1 Pucki DLMW, Lotnictwo Marynarki Wojennej, Gdynia-Babie Doły, Poland, late 1997
This aircraft was delivered to Poland on March 22, 1980 and was assigned to the 1 Pucki Dywizjon Lotniczy (Air Division) of the Polish Naval Forces. The emblem on the tail surface indicates service with the 2nd Eskadra (Squadron) of the Division. The look of the plane evolved over time, and in 2001 it flew with a sharkmouth and a tiger motif on the brake chute housing.
MiG-21bis, c/n 75061874, 47 Pápa Harcászati Repülő Ezred, Pápa airbase, Hungary, 1991
MiG-21bis, serial number 75061874, served with the 47 Combat Regiment (Harcászati Repülõezred). In 1991, it received a temporary white coloring on the rear of the fuselage and a portion of the bottom. In this guise, it took part in DACT (Dissimilar Air Combat Training) exercises, in which the opposing aircraft pitted againt each other were of differing types. Later, it was assigned to the “Sky Hussars” demonstration team. In 2006, it was mothballed and put in storage at Papa, and in 2007, it was sold into the private collection of Gerhard Neumann Museum at Niederalteich in Germany.
MiG-21bis, Tactics & Air Combat Development Establishment, Jamnagar airbase, India, September 1986
The aircraft coded C2305 was assigned to the Center for the development of tactics for aerial combat and served there during September 1986. The front of the aircraft referred to its former user, No. 4 Squadron of the IAF. This unit was dubbed “Oorials” after the local type of mountain sheep. Together with the unit’s motto, “Honor over Death” this symbolizes stamina, strength, and a fighting spirit. The colorful paint scheme of Indian MiGs was used during one of the military exercises.
MiG-21bisD, c/n 75002075, 22 eskadrila lovačkih zrakoplova, Pula airbase, Croatia, 2008
This aircraft was one of a number of MiG-21s purchased in the first half of the nineties despite a UN embargo from the Ukraine. The first unit to use the aircraft was the 22 eskadrila lovačkih zrakoplova (Fighter Squadron) based at Pula. In 2003, this was one of eight MiG-21bis aircraft to be modernized in Romania by Aerostar to MiG-21bisD standard. Later, the plane was observed at Zagreb, Tchakovec and Zadar. It carries a typical camouflage scheme for the modernized bisD aircraft.
MiG-21bis, No. 3 Air Base, Graf Ignatevo, Bulgaria, from 2002
MiG-21bis serial number 75094114 was delivered to Bulgaria in 1983. The first user of the aircraft was the 19 Fighter Regiment. From 2002, it served at Air Base No. 3 based at Graf Ignatevo, where the MiG-21s shared the base with the more modern MiG-29s. The last MiG-21bis delivered directly from the factory was retired from the Bulgarian Air Force in 2015, while the second-hand aircraft from the Soviet Air Force delivered in 1990 were retired in 2000.
Markings for Avia B.534 IV.serie 1/48
B.534.208, 36th Fighter Squadron, Air Regiment 2, Olomouc Airfield, Czechoslovakia, Fall 1937
This aircraft is representative of the camouflage scheme used by Avia at the end of the Thirties, prior to the Munich Crisis. Upper surfaces are khaki, lower are silver doped, typically a matted shade. The lower surface of the upper wing is also khaki. The blue and white Moravian eagle identifies the aircraft as belonging to the Air Regiment 2, while the letter G identifies membership within the 36th Squadron, and the numeral 1 specifies the aircraft within the Squadron. The blue tipped spinner was also a squadron identifier, although this was not an official marking. This aircraft is known to have crashed on September 6, 1937, piloted by četař (Sergeant) Julius Zaoral, following a collision with another Avia B.534.35, with svobodník (Private First Class) Jaroslav Šodek at the controls.
B.534.186, 34th Fighter Squadron, Air Regiment 4, Hradec Králové Airfield, Czechoslovakia, Summer 1937
B.534s of the Air Regiment 4 are among the more striking within the pre-war Czechoslovak Air Force. The color details are not known for certain, and this arises from uncertainties regarding the remarking of squadrons at the end of the Thirties. These could have been either blue and yellow or green and yellow. The colors on the wheel spats would be consistent, and so would, likely, the lower prop blade bandaging. This aircraft is known from photographs likely taken during the course of 1937, when attached to 34th Fighter Squadron, which utilized blue and yellow trimming. In January 1938, she was re-designated as belonging to 50th Fighter Squadron, with the fuselage code K. Coded D, she was then attached to 42nd Squadron, which used green and yellow colors. The aircraft has a tail skid instead of a tail wheel. The lower surface of the upper wing is silver doped.
B.534.239, 45th Fighter Squadron, Air Regiment 3, Piešťany Airfield, Czechoslovakia, July 1938
This aircraft carries the standard Czechoslovak camouflage scheme from the late Thirties. The lower surface of the upper wing is in khaki, and the spinner is yellow. The aircraft was documented on a photograph dated July 14, 1938, when it suffered light damage while flown by desátník (corporal) Baláš. At the time, these aircraft carried no squadron codes. The Air Regiment 3 was the only one that was located in Slovakia prior to the outbreak of the war. After the dissolution of Czechoslovakia, Air Regiment 3 aircraft were incorporated into the services of the newly formed Slovak Air Force. In this service, Avia B.534s took part in combat operations in Poland and later in the Soviet Union. In August 1944, the Slovak National Uprising saw the remaining Avias take part in anti-German operations.
B.534.217, Combined Squadron of Slovak National Uprising, Tri Duby Airfield, Slovakia, September 1944
In the fall of 1944, the Slovak National Uprising saw the use of several Avia B.534s. This specific aircraft is the only one photographically documented with the national markings used during the uprising. These were composed of the original Czechoslovak roundels with the addition of the Slovak two-pronged cross. The markings on the right wing are oriented incorrectly with the red field on the right side, i.e. directed away from the fuselage. Also, blue field pointing upwards on the rudder is wrongly oriented. It has not been conclusively determined weather or not the lower wing markings lacked the Slovak crosses. The aircraft carries the typical camouflage scheme of khaki upper surfaces and silver doped lower (gray respray of the lower surfaces for this aircraft is unlikely) and with khaki undersurface of the top wing. The aircraft was noted to have been rather heavily weathered. The tip of the spinner was either khaki or possibly also heavily weathered. Propeller blades were black on both sides. The top of the nose was likely also khaki, and not yellow. All photographic evidence suggests that the sliding portion of the canopy was missing at the time of the Slovak National Uprising.
.ff0{font-family:sans-serif;visibility:hidden;} @font-face{font-family:ff1;src:url(f1.woff)format("woff");}.ff1{font-family:ff1;line-height:1.005371;font-style:normal;font-weight:normal;visibility:visible;} @font-face{font-family:ff2;src:url(f2.woff)format("woff");}.ff2{font-family:ff2;line-height:1.000000;font-style:normal;font-weight:normal;visibility:visible;} @font-face{font-family:ff3;src:url(f3.woff)format("woff");}.ff3{font-family:ff3;line-height:1.176758;font-style:normal;font-weight:normal;visibility:visible;} @font-face{font-family:ff4;src:url(f4.woff)format("woff");}.ff4{font-family:ff4;line-height:0.666504;font-style:normal;font-weight:normal;visibility:visible;} @font-face{font-family:ff5;src:url(f5.woff)format("woff");}.ff5{font-family:ff5;line-height:0.997070;font-style:normal;font-weight:normal;visibility:visible;} @font-face{font-family:ff6;src:url(f6.woff)format("woff");}.ff6{font-family:ff6;line-height:1.117676;font-style:normal;font-weight:normal;visibility:visible;} @font-face{font-family:ff7;src:url(f7.woff)format("woff");}.ff7{font-family:ff7;line-height:0.666504;font-style:normal;font-weight:normal;visibility:visible;} @font-face{font-family:ff8;src:url(f8.woff)format("woff");}.ff8{font-family:ff8;line-height:0.666504;font-style:normal;font-weight:normal;visibility:visible;} @font-face{font-family:ff9;src:url(f9.woff)format("woff");}.ff9{font-family:ff9;line-height:0.728000;font-style:normal;font-weight:normal;visibility:visible;} @font-face{font-family:ffa;src:url(fa.woff)format("woff");}.ffa{font-family:ffa;line-height:1.121094;font-style:normal;font-weight:normal;visibility:visible;} @font-face{font-family:ffb;src:url(fb.woff)format("woff");}.ffb{font-family:ffb;line-height:0.724609;font-style:normal;font-weight:normal;visibility:visible;} @font-face{font-family:ffc;src:url(fc.woff)format("woff");}.ffc{font-family:ffc;line-height:0.726074;font-style:normal;font-weight:normal;visibility:visible;} @font-face{font-family:ffd;src:url(fd.woff)format("woff");}.ffd{font-family:ffd;line-height:0.724609;font-style:normal;font-weight:normal;visibility:visible;} @font-face{font-family:ffe;src:url(fe.woff)format("woff");}.ffe{font-family:ffe;line-height:0.724609;font-style:normal;font-weight:normal;visibility:visible;} @font-face{font-family:fff;src:url(ff.woff)format("woff");}.fff{font-family:fff;line-height:0.718750;font-style:normal;font-weight:normal;visibility:visible;} @font-face{font-family:ff10;src:url(f10.woff)format("woff");}.ff10{font-family:ff10;line-height:0.726074;font-style:normal;font-weight:normal;visibility:visible;} @font-face{font-family:ff11;src:url(f11.woff)format("woff");}.ff11{font-family:ff11;line-height:1.029785;font-style:normal;font-weight:normal;visibility:visible;} @font-face{font-family:ff12;src:url(f12.woff)format("woff");}.ff12{font-family:ff12;line-height:1.121094;font-style:normal;font-weight:normal;visibility:visible;} @font-face{font-family:ff13;src:url(f13.woff)format("woff");}.ff13{font-family:ff13;line-height:1.000000;font-style:normal;font-weight:normal;visibility:visible;} @font-face{font-family:ff14;src:url(f14.woff)format("woff");}.ff14{font-family:ff14;line-height:0.942383;font-style:normal;font-weight:normal;visibility:visible;} @font-face{font-family:ff15;src:url(f15.woff)format("woff");}.ff15{font-family:ff15;line-height:0.855957;font-style:normal;font-weight:normal;visibility:visible;} @font-face{font-family:ff16;src:url(f16.woff)format("woff");}.ff16{font-family:ff16;line-height:0.855957;font-style:normal;font-weight:normal;visibility:visible;} @font-face{font-family:ff17;src:url(f17.woff)format("woff");}.ff17{font-family:ff17;line-height:1.109375;font-style:normal;font-weight:normal;visibility:visible;} @font-face{font-family:ff18;src:url(f18.woff)format("woff");}.ff18{font-family:ff18;line-height:0.969727;font-style:normal;font-weight:normal;visibility:visible;} @font-face{font-family:ff19;src:url(f19.woff)format("woff");}.ff19{font-family:ff19;line-height:0.804688;font-style:normal;font-weight:normal;visibility:visible;} @font-face{font-family:ff1a;src:url(f1a.woff)format("woff");}.ff1a{font-family:ff1a;line-height:1.039551;font-style:normal;font-weight:normal;visibility:visible;} @font-face{font-family:ff1b;src:url(f1b.woff)format("woff");}.ff1b{font-family:ff1b;line-height:1.025879;font-style:normal;font-weight:normal;visibility:visible;} @font-face{font-family:ff1c;src:url(f1c.woff)format("woff");}.ff1c{font-family:ff1c;line-height:1.034668;font-style:normal;font-weight:normal;visibility:visible;} @font-face{font-family:ff1d;src:url(f1d.woff)format("woff");}.ff1d{font-family:ff1d;line-height:1.163086;font-style:normal;font-weight:normal;visibility:visible;} @font-face{font-family:ff1e;src:url(f1e.woff)format("woff");}.ff1e{font-family:ff1e;line-height:1.117676;font-style:normal;font-weight:normal;visibility:visible;} @font-face{font-family:ff1f;src:url(f1f.woff)format("woff");}.ff1f{font-family:ff1f;line-height:1.154785;font-style:normal;font-weight:normal;visibility:visible;} @font-face{font-family:ff20;src:url(f20.woff)format("woff");}.ff20{font-family:ff20;line-height:1.005371;font-style:normal;font-weight:normal;visibility:visible;} @font-face{font-family:ff21;src:url(f21.woff)format("woff");}.ff21{font-family:ff21;line-height:0.816406;font-style:normal;font-weight:normal;visibility:visible;} @font-face{font-family:ff22;src:url(f22.woff)format("woff");}.ff22{font-family:ff22;line-height:0.952850;font-style:normal;font-weight:normal;visibility:visible;} @font-face{font-family:ff23;src:url(f23.woff)format("woff");}.ff23{font-family:ff23;line-height:0.929199;font-style:normal;font-weight:normal;visibility:visible;} @font-face{font-family:ff24;src:url(f24.woff)format("woff");}.ff24{font-family:ff24;line-height:0.724609;font-style:normal;font-weight:normal;visibility:visible;} @font-face{font-family:ff25;src:url(f25.woff)format("woff");}.ff25{font-family:ff25;line-height:0.724609;font-style:normal;font-weight:normal;visibility:visible;} @font-face{font-family:ff26;src:url(f26.woff)format("woff");}.ff26{font-family:ff26;line-height:0.718750;font-style:normal;font-weight:normal;visibility:visible;} @font-face{font-family:ff27;src:url(f27.woff)format("woff");}.ff27{font-family:ff27;line-height:0.724609;font-style:normal;font-weight:normal;visibility:visible;} @font-face{font-family:ff28;src:url(f28.woff)format("woff");}.ff28{font-family:ff28;line-height:0.724609;font-style:normal;font-weight:normal;visibility:visible;} @font-face{font-family:ff29;src:url(f29.woff)format("woff");}.ff29{font-family:ff29;line-height:0.718750;font-style:normal;font-weight:normal;visibility:visible;} @font-face{font-family:ff2a;src:url(f2a.woff)format("woff");}.ff2a{font-family:ff2a;line-height:0.724609;font-style:normal;font-weight:normal;visibility:visible;} @font-face{font-family:ff2b;src:url(f2b.woff)format("woff");}.ff2b{font-family:ff2b;line-height:0.782000;font-style:normal;font-weight:normal;visibility:visible;} @font-face{font-family:ff2c;src:url(f2c.woff)format("woff");}.ff2c{font-family:ff2c;line-height:0.928711;font-style:normal;font-weight:normal;visibility:visible;} @font-face{font-family:ff2d;src:url(f2d.woff)format("woff");}.ff2d{font-family:ff2d;line-height:0.717773;font-style:normal;font-weight:normal;visibility:visible;} @font-face{font-family:ff2e;src:url(f2e.woff)format("woff");}.ff2e{font-family:ff2e;line-height:1.000000;font-style:normal;font-weight:normal;visibility:visible;} @font-face{font-family:ff2f;src:url(f2f.woff)format("woff");}.ff2f{font-family:ff2f;line-height:0.724609;font-style:normal;font-weight:normal;visibility:visible;} @font-face{font-family:ff30;src:url(f30.woff)format("woff");}.ff30{font-family:ff30;line-height:0.724609;font-style:normal;font-weight:normal;visibility:visible;} @font-face{font-family:ff31;src:url(f31.woff)format("woff");}.ff31{font-family:ff31;line-height:0.724609;font-style:normal;font-weight:normal;visibility:visible;} .m4{transform:matrix(0.000000,-0.322539,0.322539,0.000000,0,0);-ms-transform:matrix(0.000000,-0.322539,0.322539,0.000000,0,0);-webkit-transform:matrix(0.000000,-0.322539,0.322539,0.000000,0,0);} .m3{transform:matrix(0.311550,0.000000,-0.083478,0.311550,0,0);-ms-transform:matrix(0.311550,0.000000,-0.083478,0.311550,0,0);-webkit-transform:matrix(0.311550,0.000000,-0.083478,0.311550,0,0);} .ma{transform:matrix(0.312266,-0.080757,0.080757,0.312266,0,0);-ms-transform:matrix(0.312266,-0.080757,0.080757,0.312266,0,0);-webkit-transform:matrix(0.312266,-0.080757,0.080757,0.312266,0,0);} .m7{transform:matrix(0.316089,0.000000,0.000000,0.322539,0,0);-ms-transform:matrix(0.316089,0.000000,0.000000,0.322539,0,0);-webkit-transform:matrix(0.316089,0.000000,0.000000,0.322539,0,0);} .m5{transform:matrix(0.319314,0.000000,0.000000,0.322539,0,0);-ms-transform:matrix(0.319314,0.000000,0.000000,0.322539,0,0);-webkit-transform:matrix(0.319314,0.000000,0.000000,0.322539,0,0);} .m8{transform:matrix(0.320773,-0.033714,0.033714,0.320773,0,0);-ms-transform:matrix(0.320773,-0.033714,0.033714,0.320773,0,0);-webkit-transform:matrix(0.320773,-0.033714,0.033714,0.320773,0,0);} .m9{transform:matrix(0.322201,-0.014772,0.014772,0.322201,0,0);-ms-transform:matrix(0.322201,-0.014772,0.014772,0.322201,0,0);-webkit-transform:matrix(0.322201,-0.014772,0.014772,0.322201,0,0);} .m0{transform:matrix(0.322539,0.000000,0.000000,0.322539,0,0);-ms-transform:matrix(0.322539,0.000000,0.000000,0.322539,0,0);-webkit-transform:matrix(0.322539,0.000000,0.000000,0.322539,0,0);} .m2{transform:matrix(0.322539,0.000000,0.000000,0.322539,0,0);-ms-transform:matrix(0.322539,0.000000,0.000000,0.322539,0,0);-webkit-transform:matrix(0.322539,0.000000,0.000000,0.322539,0,0);} .m1{transform:matrix(0.597167,0.000000,0.000000,0.322539,0,0);-ms-transform:matrix(0.597167,0.000000,0.000000,0.322539,0,0);-webkit-transform:matrix(0.597167,0.000000,0.000000,0.322539,0,0);} .m6{transform:matrix(1.290158,0.000000,0.000000,1.290158,0,0);-ms-transform:matrix(1.290158,0.000000,0.000000,1.290158,0,0);-webkit-transform:matrix(1.290158,0.000000,0.000000,1.290158,0,0);} .v0{vertical-align:0.000000px;} .ls40{letter-spacing:-7.020000px;} .ls50{letter-spacing:-5.670000px;} .ls56{letter-spacing:-5.613300px;} .ls39{letter-spacing:-3.888000px;} .ls3e{letter-spacing:-3.740000px;} .ls5f{letter-spacing:-3.693600px;} .ls7{letter-spacing:-3.265080px;} .ls23{letter-spacing:-2.860000px;} .ls18{letter-spacing:-2.592000px;} .ls6{letter-spacing:-2.427880px;} .ls4c{letter-spacing:-1.970748px;} .ls24{letter-spacing:-1.920000px;} .ls41{letter-spacing:-1.800000px;} .ls4{letter-spacing:-1.799508px;} .ls4f{letter-spacing:-1.620000px;} .ls45{letter-spacing:-1.541686px;} .ls2c{letter-spacing:-1.416000px;} .ls43{letter-spacing:-1.295316px;} .ls2e{letter-spacing:-1.146382px;} .ls47{letter-spacing:-1.037236px;} .ls2d{letter-spacing:-1.020000px;} .lsc{letter-spacing:-0.972000px;} .lsf{letter-spacing:-0.960000px;} .ls3a{letter-spacing:-0.948730px;} .ls22{letter-spacing:-0.936000px;} .lsd{letter-spacing:-0.756000px;} .ls5a{letter-spacing:-0.751078px;} .ls57{letter-spacing:-0.726210px;} .ls2f{letter-spacing:-0.720000px;} .ls34{letter-spacing:-0.680000px;} .ls54{letter-spacing:-0.672000px;} .ls5{letter-spacing:-0.620520px;} .ls2{letter-spacing:-0.571643px;} .ls3f{letter-spacing:-0.546228px;} .ls35{letter-spacing:-0.528000px;} .ls5d{letter-spacing:-0.515576px;} .ls52{letter-spacing:-0.504000px;} .ls5c{letter-spacing:-0.457000px;} .ls32{letter-spacing:-0.452400px;} .lsa{letter-spacing:-0.400000px;} .ls3c{letter-spacing:-0.394388px;} .ls3d{letter-spacing:-0.380000px;} .ls26{letter-spacing:-0.360000px;} .ls38{letter-spacing:-0.352000px;} .ls9{letter-spacing:-0.348000px;} .ls1e{letter-spacing:-0.345600px;} .ls36{letter-spacing:-0.340000px;} .ls51{letter-spacing:-0.336000px;} .ls53{letter-spacing:-0.320000px;} .lsb{letter-spacing:-0.236731px;} .ls59{letter-spacing:-0.225000px;} .ls55{letter-spacing:-0.224000px;} .ls5b{letter-spacing:-0.197652px;} .ls3b{letter-spacing:-0.180000px;} .ls1d{letter-spacing:-0.153600px;} .ls1f{letter-spacing:-0.128000px;} .ls14{letter-spacing:-0.096000px;} .ls20{letter-spacing:-0.089600px;} .ls21{letter-spacing:-0.080000px;} .ls28{letter-spacing:-0.072000px;} .ls3{letter-spacing:-0.062052px;} .ls0{letter-spacing:0.000000px;} .ls2a{letter-spacing:0.052000px;} .ls25{letter-spacing:0.180000px;} .ls49{letter-spacing:0.211288px;} .ls2b{letter-spacing:0.216000px;} .lse{letter-spacing:0.236731px;} .ls27{letter-spacing:0.252000px;} .ls4d{letter-spacing:0.295803px;} .ls11{letter-spacing:0.360000px;} .ls4a{letter-spacing:0.380318px;} .ls58{letter-spacing:0.392000px;} .ls17{letter-spacing:0.416000px;} .ls1c{letter-spacing:0.432000px;} .ls1a{letter-spacing:0.468000px;} .ls1b{letter-spacing:0.504000px;} .ls16{letter-spacing:0.520000px;} .ls61{letter-spacing:0.532000px;} .ls13{letter-spacing:0.540000px;} .ls4e{letter-spacing:0.549349px;} .ls42{letter-spacing:0.560000px;} .ls10{letter-spacing:0.576000px;} .ls60{letter-spacing:0.588000px;} .ls12{letter-spacing:0.612000px;} .ls19{letter-spacing:0.684000px;} .ls5e{letter-spacing:0.728000px;} .ls29{letter-spacing:0.756000px;} .ls4b{letter-spacing:0.760637px;} .ls30{letter-spacing:0.800000px;} .ls48{letter-spacing:0.971925px;} .ls15{letter-spacing:1.120000px;} .ls1{letter-spacing:1.625264px;} .ls44{letter-spacing:1.920000px;} .ls8{letter-spacing:2.000000px;} .ls33{letter-spacing:2.240000px;} .ls37{letter-spacing:2.480000px;} .ls31{letter-spacing:2.760000px;} .ls46{letter-spacing:3.288664px;} .sc_{text-shadow:none;} .sc2{text-shadow:-0.015em 0 rgb(210,32,39),0 0.015em rgb(210,32,39),0.015em 0 rgb(210,32,39),0 -0.015em rgb(210,32,39);} .sc0{text-shadow:-0.015em 0 transparent,0 0.015em transparent,0.015em 0 transparent,0 -0.015em transparent;} .sc1{text-shadow:-0.015em 0 rgb(35,31,32),0 0.015em rgb(35,31,32),0.015em 0 rgb(35,31,32),0 -0.015em rgb(35,31,32);} @media screen and (-webkit-min-device-pixel-ratio:0){ .sc_{-webkit-text-stroke:0px transparent;} .sc2{-webkit-text-stroke:0.015em rgb(210,32,39);text-shadow:none;} .sc0{-webkit-text-stroke:0.015em transparent;text-shadow:none;} .sc1{-webkit-text-stroke:0.015em rgb(35,31,32);text-shadow:none;} } .ws54a{word-spacing:-19.018154px;} .ws57a{word-spacing:-13.248000px;} .ws1e0{word-spacing:-7.704000px;} .ws331{word-spacing:-7.482000px;} .ws57b{word-spacing:-7.452000px;} .ws560{word-spacing:-7.437338px;} .ws54b{word-spacing:-6.598135px;} .ws2e7{word-spacing:-6.048000px;} .ws4bc{word-spacing:-5.796000px;} .wsff{word-spacing:-5.040000px;} .ws312{word-spacing:-4.752000px;} .wsdd{word-spacing:-4.698000px;} .ws1c1{word-spacing:-4.428000px;} .ws29d{word-spacing:-4.392000px;} .ws4ce{word-spacing:-4.068000px;} .ws28b{word-spacing:-3.996000px;} .ws2c9{word-spacing:-3.852000px;} .ws4b7{word-spacing:-3.744000px;} .ws3c6{word-spacing:-3.731200px;} .ws41b{word-spacing:-3.638000px;} .ws324{word-spacing:-3.636000px;} .wsd9{word-spacing:-3.584400px;} .ws2de{word-spacing:-3.564000px;} .ws1e6{word-spacing:-3.420000px;} .ws4b6{word-spacing:-3.402000px;} .ws282{word-spacing:-3.384000px;} .ws585{word-spacing:-3.353400px;} .ws4c4{word-spacing:-3.348000px;} .ws1d8{word-spacing:-3.312000px;} .ws555{word-spacing:-3.288664px;} .ws3e4{word-spacing:-3.238400px;} .ws204{word-spacing:-3.168000px;} .ws468{word-spacing:-3.132800px;} .wsdf{word-spacing:-3.097200px;} .ws1fc{word-spacing:-3.096000px;} .ws3cb{word-spacing:-3.062400px;} .ws2f9{word-spacing:-3.024000px;} .ws2da{word-spacing:-2.988000px;} .ws442{word-spacing:-2.924000px;} .ws471{word-spacing:-2.921600px;} .ws413{word-spacing:-2.816000px;} .ws2c7{word-spacing:-2.772000px;} .ws4ac{word-spacing:-2.760000px;} .ws2f5{word-spacing:-2.736000px;} .ws106{word-spacing:-2.700000px;} .ws13f{word-spacing:-2.628000px;} .ws1de{word-spacing:-2.592000px;} .ws41f{word-spacing:-2.584000px;} .ws562{word-spacing:-2.576000px;} .ws17a{word-spacing:-2.556000px;} .ws33a{word-spacing:-2.540400px;} .ws10e{word-spacing:-2.484000px;} .ws287{word-spacing:-2.412000px;} .ws105{word-spacing:-2.376000px;} .ws15e{word-spacing:-2.304000px;} .wsf9{word-spacing:-2.268000px;} .ws10b{word-spacing:-2.232000px;} .wsfc{word-spacing:-2.196000px;} .ws4d2{word-spacing:-2.187000px;} .ws3eb{word-spacing:-2.182400px;} .ws359{word-spacing:-2.157600px;} .ws30d{word-spacing:-2.124000px;} .ws229{word-spacing:-2.088000px;} .ws50c{word-spacing:-2.050818px;} .ws499{word-spacing:-2.041600px;} .ws285{word-spacing:-2.016000px;} .ws1c2{word-spacing:-1.980000px;} .ws3d6{word-spacing:-1.971200px;} .ws572{word-spacing:-1.960000px;} .ws326{word-spacing:-1.944000px;} .ws421{word-spacing:-1.938000px;} .ws33d{word-spacing:-1.914000px;} .ws1cf{word-spacing:-1.908000px;} .ws516{word-spacing:-1.893062px;} .ws23c{word-spacing:-1.872000px;} .ws2d2{word-spacing:-1.836000px;} .ws66{word-spacing:-1.809600px;} .ws288{word-spacing:-1.764000px;} .ws81{word-spacing:-1.740000px;} .ws322{word-spacing:-1.728000px;} .ws40c{word-spacing:-1.724800px;} .ws65{word-spacing:-1.705200px;} .ws184{word-spacing:-1.692000px;} .ws67{word-spacing:-1.670400px;} .ws42c{word-spacing:-1.666000px;} .ws402{word-spacing:-1.654400px;} .ws1ba{word-spacing:-1.620000px;} .ws17{word-spacing:-1.600800px;} .ws22d{word-spacing:-1.596000px;} .ws4bf{word-spacing:-1.584000px;} .ws4d6{word-spacing:-1.577552px;} .ws2c{word-spacing:-1.566000px;} .ws37c{word-spacing:-1.564000px;} .ws4ab{word-spacing:-1.548800px;} .ws239{word-spacing:-1.548000px;} .ws19d{word-spacing:-1.540000px;} .ws12f{word-spacing:-1.536000px;} .ws15b{word-spacing:-1.512000px;} .ws71{word-spacing:-1.496400px;} .ws3ac{word-spacing:-1.496000px;} .ws1ec{word-spacing:-1.484000px;} .ws3e8{word-spacing:-1.478400px;} .ws165{word-spacing:-1.476000px;} .ws380{word-spacing:-1.462000px;} .ws80{word-spacing:-1.461600px;} .ws46c{word-spacing:-1.443200px;} .ws15f{word-spacing:-1.440000px;} .ws273{word-spacing:-1.428000px;} .wsa9{word-spacing:-1.426800px;} .ws521{word-spacing:-1.417500px;} .ws30a{word-spacing:-1.416000px;} .ws3db{word-spacing:-1.408000px;} .ws17e{word-spacing:-1.404000px;} .ws41a{word-spacing:-1.394000px;} .wsde{word-spacing:-1.392000px;} .ws4d7{word-spacing:-1.380358px;} .ws173{word-spacing:-1.368000px;} .wsaf{word-spacing:-1.357200px;} .ws52{word-spacing:-1.322400px;} .ws3ec{word-spacing:-1.302400px;} .ws50b{word-spacing:-1.301480px;} .ws4cd{word-spacing:-1.296000px;} .ws42d{word-spacing:-1.292000px;} .ws8b{word-spacing:-1.287600px;} .ws1e3{word-spacing:-1.260000px;} .ws2b{word-spacing:-1.252800px;} .ws151{word-spacing:-1.224000px;} .ws70{word-spacing:-1.218000px;} .ws4ae{word-spacing:-1.188000px;} .ws46d{word-spacing:-1.161600px;} .ws2d3{word-spacing:-1.152000px;} .ws24e{word-spacing:-1.148000px;} .ws537{word-spacing:-1.143725px;} .ws492{word-spacing:-1.126400px;} .ws178{word-spacing:-1.120000px;} .ws115{word-spacing:-1.116000px;} .ws7c{word-spacing:-1.113600px;} .ws3f7{word-spacing:-1.091200px;} .ws571{word-spacing:-1.088000px;} .ws22c{word-spacing:-1.080000px;} .wsac{word-spacing:-1.078800px;} .ws438{word-spacing:-1.054000px;} .ws9f{word-spacing:-1.044000px;} .ws56a{word-spacing:-1.024000px;} .ws44f{word-spacing:-1.020000px;} .wsbb{word-spacing:-1.009200px;} .ws14e{word-spacing:-1.008000px;} .ws47e{word-spacing:-0.985600px;} .ws1ee{word-spacing:-0.972000px;} .ws558{word-spacing:-0.971925px;} .ws41d{word-spacing:-0.952000px;} .ws10d{word-spacing:-0.936000px;} .ws365{word-spacing:-0.918000px;} .ws3c9{word-spacing:-0.915200px;} .ws52d{word-spacing:-0.907092px;} .wse{word-spacing:-0.904800px;} .ws163{word-spacing:-0.900000px;} .ws376{word-spacing:-0.884000px;} .ws346{word-spacing:-0.870000px;} .ws511{word-spacing:-0.867654px;} .ws232{word-spacing:-0.864000px;} .ws41e{word-spacing:-0.850000px;} .ws47a{word-spacing:-0.844800px;} .ws83{word-spacing:-0.835200px;} .ws29b{word-spacing:-0.828000px;} .ws47b{word-spacing:-0.809600px;} .ws332{word-spacing:-0.800400px;} .ws35f{word-spacing:-0.800000px;} .ws2fa{word-spacing:-0.792000px;} .ws515{word-spacing:-0.788776px;} .ws424{word-spacing:-0.782000px;} .ws48a{word-spacing:-0.774400px;} .wse0{word-spacing:-0.765600px;} .ws55d{word-spacing:-0.760637px;} .ws1ae{word-spacing:-0.756000px;} .ws445{word-spacing:-0.748000px;} .ws64{word-spacing:-0.730800px;} .ws583{word-spacing:-0.728000px;} .ws2c6{word-spacing:-0.720000px;} .ws371{word-spacing:-0.714000px;} .ws177{word-spacing:-0.684000px;} .ws38a{word-spacing:-0.680000px;} .ws5c{word-spacing:-0.661200px;} .ws28e{word-spacing:-0.648000px;} .ws501{word-spacing:-0.646000px;} .ws272{word-spacing:-0.624000px;} .ws107{word-spacing:-0.612000px;} .ws31{word-spacing:-0.591600px;} .ws586{word-spacing:-0.588000px;} .ws155{word-spacing:-0.576000px;} .ws54e{word-spacing:-0.560000px;} .wsd6{word-spacing:-0.556800px;} .ws417{word-spacing:-0.552000px;} .ws1c6{word-spacing:-0.540000px;} .ws587{word-spacing:-0.532000px;} .ws6f{word-spacing:-0.522000px;} .ws4d0{word-spacing:-0.518400px;} .ws1c7{word-spacing:-0.504000px;} .wsa6{word-spacing:-0.487200px;} .ws12e{word-spacing:-0.480000px;} .ws1c5{word-spacing:-0.468000px;} .ws344{word-spacing:-0.452400px;} .ws458{word-spacing:-0.442000px;} .ws216{word-spacing:-0.432000px;} .ws497{word-spacing:-0.422400px;} .ws4c3{word-spacing:-0.396000px;} .ws578{word-spacing:-0.392000px;} .ws55b{word-spacing:-0.380318px;} .wsfd{word-spacing:-0.360000px;} .ws4f4{word-spacing:-0.354949px;} .ws56b{word-spacing:-0.352000px;} .ws5f{word-spacing:-0.348000px;} .ws160{word-spacing:-0.324000px;} .ws329{word-spacing:-0.320000px;} .ws423{word-spacing:-0.306000px;} .ws4cf{word-spacing:-0.302400px;} .ws55f{word-spacing:-0.295803px;} .ws233{word-spacing:-0.288000px;} .ws446{word-spacing:-0.272000px;} .ws16d{word-spacing:-0.252000px;} .ws4a2{word-spacing:-0.246400px;} .ws582{word-spacing:-0.243734px;} .ws88{word-spacing:-0.243600px;} .ws19c{word-spacing:-0.240000px;} .wse4{word-spacing:-0.236731px;} .ws2af{word-spacing:-0.216000px;} .ws559{word-spacing:-0.211288px;} .ws3dc{word-spacing:-0.211200px;} .ws355{word-spacing:-0.208800px;} .ws54d{word-spacing:-0.200376px;} .ws1b7{word-spacing:-0.180000px;} .ws335{word-spacing:-0.174000px;} .ws525{word-spacing:-0.172800px;} .ws30c{word-spacing:-0.160000px;} .ws152{word-spacing:-0.144000px;} .ws54c{word-spacing:-0.130680px;} .ws4de{word-spacing:-0.118316px;} .ws235{word-spacing:-0.108000px;} .ws3e2{word-spacing:-0.105600px;} .ws8c{word-spacing:-0.104400px;} .ws579{word-spacing:-0.096244px;} .ws564{word-spacing:-0.092000px;} .ws211{word-spacing:-0.072000px;} .ws44a{word-spacing:-0.068000px;} .ws577{word-spacing:-0.066761px;} .ws2e5{word-spacing:-0.057975px;} .ws2ff{word-spacing:-0.052000px;} .ws507{word-spacing:-0.039439px;} .ws1ed{word-spacing:-0.036000px;} .ws2e6{word-spacing:-0.028988px;} .ws0{word-spacing:0.000000px;} .ws74{word-spacing:0.034800px;} .ws250{word-spacing:0.036000px;} .ws2{word-spacing:0.062052px;} .ws6e{word-spacing:0.069600px;} .ws18e{word-spacing:0.072000px;} .ws4d8{word-spacing:0.078878px;} .ws279{word-spacing:0.080000px;} .ws278{word-spacing:0.089600px;} .ws460{word-spacing:0.102000px;} .ws19b{word-spacing:0.104000px;} .ws247{word-spacing:0.108000px;} .ws277{word-spacing:0.128000px;} .ws4ca{word-spacing:0.144000px;} .ws274{word-spacing:0.153600px;} .ws52e{word-spacing:0.157755px;} .ws350{word-spacing:0.174000px;} .ws405{word-spacing:0.176000px;} .ws133{word-spacing:0.180000px;} .ws57f{word-spacing:0.197652px;} .wsed{word-spacing:0.216000px;} .ws574{word-spacing:0.224000px;} .ws57d{word-spacing:0.225000px;} .wse1{word-spacing:0.236731px;} .ws459{word-spacing:0.238000px;} .ws48{word-spacing:0.243600px;} .ws159{word-spacing:0.252000px;} .ws30{word-spacing:0.278400px;} .ws465{word-spacing:0.281600px;} .ws2d0{word-spacing:0.288000px;} .ws41c{word-spacing:0.306000px;} .wsb4{word-spacing:0.313200px;} .ws48d{word-spacing:0.316800px;} .ws310{word-spacing:0.324000px;} .ws563{word-spacing:0.336000px;} .ws45d{word-spacing:0.340000px;} .ws275{word-spacing:0.345600px;} .wsd{word-spacing:0.348000px;} .ws131{word-spacing:0.360000px;} .ws502{word-spacing:0.380000px;} .wsd5{word-spacing:0.382800px;} .wsea{word-spacing:0.384000px;} .ws4c9{word-spacing:0.396000px;} .ws4c{word-spacing:0.400000px;} .ws431{word-spacing:0.408000px;} .wsad{word-spacing:0.417600px;} .ws49b{word-spacing:0.422400px;} .ws1b5{word-spacing:0.432000px;} .ws540{word-spacing:0.433827px;} .ws3b2{word-spacing:0.442000px;} .ws56e{word-spacing:0.448000px;} .ws580{word-spacing:0.457000px;} .ws1fd{word-spacing:0.468000px;} .ws358{word-spacing:0.487200px;} .ws2dd{word-spacing:0.504000px;} .ws397{word-spacing:0.510000px;} .ws276{word-spacing:0.512000px;} .ws581{word-spacing:0.515576px;} .ws89{word-spacing:0.522000px;} .ws3c4{word-spacing:0.528000px;} .ws1be{word-spacing:0.540000px;} .ws545{word-spacing:0.546228px;} .ws57c{word-spacing:0.560000px;} .ws1{word-spacing:0.571643px;} .ws158{word-spacing:0.576000px;} .ws22{word-spacing:0.591600px;} .ws495{word-spacing:0.598400px;} .ws1a7{word-spacing:0.612000px;} .ws4{word-spacing:0.620520px;} .ws2fe{word-spacing:0.624000px;} .ws3ed{word-spacing:0.633600px;} .ws570{word-spacing:0.640000px;} .ws37b{word-spacing:0.646000px;} .ws1bc{word-spacing:0.648000px;} .ws573{word-spacing:0.672000px;} .ws36a{word-spacing:0.680000px;} .ws16{word-spacing:0.696000px;} .ws304{word-spacing:0.720000px;} .ws576{word-spacing:0.726210px;} .ws434{word-spacing:0.748000px;} .ws4d5{word-spacing:0.749337px;} .ws57e{word-spacing:0.751078px;} .wse3{word-spacing:0.756000px;} .wsf{word-spacing:0.765600px;} .ws44c{word-spacing:0.782000px;} .ws2b6{word-spacing:0.792000px;} .wsa0{word-spacing:0.800400px;} .ws490{word-spacing:0.809600px;} .ws2a7{word-spacing:0.828000px;} .ws509{word-spacing:0.828215px;} .ws47{word-spacing:0.835200px;} .ws40b{word-spacing:0.844800px;} .ws2ac{word-spacing:0.864000px;} .ws2f{word-spacing:0.870000px;} .ws3a3{word-spacing:0.884000px;} .ws4c6{word-spacing:0.900000px;} .ws3cc{word-spacing:0.915200px;} .ws363{word-spacing:0.918000px;} .ws1ac{word-spacing:0.936000px;} .ws1a{word-spacing:0.939600px;} .ws514{word-spacing:0.946531px;} .ws4d1{word-spacing:0.948730px;} .ws3c5{word-spacing:0.950400px;} .wsec{word-spacing:0.960000px;} .wse2{word-spacing:0.972000px;} .wsd4{word-spacing:0.974400px;} .ws3f1{word-spacing:0.985600px;} .ws517{word-spacing:0.985970px;} .wsfa{word-spacing:1.008000px;} .ws1f{word-spacing:1.009200px;} .ws556{word-spacing:1.037236px;} .ws24{word-spacing:1.044000px;} .ws56d{word-spacing:1.056000px;} .ws530{word-spacing:1.064848px;} .wsaa{word-spacing:1.078800px;} .ws13d{word-spacing:1.080000px;} .ws3af{word-spacing:1.088000px;} .ws469{word-spacing:1.091200px;} .ws533{word-spacing:1.104286px;} .wsc6{word-spacing:1.113600px;} .ws1af{word-spacing:1.116000px;} .ws36f{word-spacing:1.122000px;} .ws48b{word-spacing:1.126400px;} .ws311{word-spacing:1.146382px;} .wsb0{word-spacing:1.148400px;} .ws2cd{word-spacing:1.152000px;} .ws75{word-spacing:1.183200px;} .ws4ad{word-spacing:1.188000px;} .ws3ae{word-spacing:1.190000px;} .ws3e1{word-spacing:1.196800px;} .ws86{word-spacing:1.218000px;} .ws325{word-spacing:1.224000px;} .ws3ab{word-spacing:1.258000px;} .ws1b8{word-spacing:1.260000px;} .ws4e3{word-spacing:1.262042px;} .ws48e{word-spacing:1.267200px;} .ws57{word-spacing:1.287600px;} .ws54f{word-spacing:1.295316px;} .ws176{word-spacing:1.296000px;} .ws125{word-spacing:1.332000px;} .ws512{word-spacing:1.340919px;} .ws62{word-spacing:1.357200px;} .ws1aa{word-spacing:1.368000px;} .ws21{word-spacing:1.392000px;} .ws441{word-spacing:1.394000px;} .ws22a{word-spacing:1.404000px;} .ws30b{word-spacing:1.416000px;} .ws2d4{word-spacing:1.440000px;} .ws406{word-spacing:1.443200px;} .ws518{word-spacing:1.459236px;} .wsc3{word-spacing:1.461600px;} .ws4c2{word-spacing:1.476000px;} .wse7{word-spacing:1.488000px;} .ws3b8{word-spacing:1.496000px;} .ws76{word-spacing:1.496400px;} .ws4ee{word-spacing:1.498674px;} .ws161{word-spacing:1.512000px;} .ws430{word-spacing:1.530000px;} .ws90{word-spacing:1.531200px;} .ws569{word-spacing:1.536000px;} .ws4db{word-spacing:1.538113px;} .ws550{word-spacing:1.541686px;} .ws124{word-spacing:1.548000px;} .ws37d{word-spacing:1.564000px;} .ws20f{word-spacing:1.584000px;} .ws9d{word-spacing:1.600800px;} .ws547{word-spacing:1.602269px;} .ws529{word-spacing:1.616991px;} .ws1f2{word-spacing:1.620000px;} .ws306{word-spacing:1.656000px;} .ws52f{word-spacing:1.656430px;} .ws4ba{word-spacing:1.692000px;} .ws340{word-spacing:1.705200px;} .ws3dd{word-spacing:1.724800px;} .ws24f{word-spacing:1.728000px;} .ws4e1{word-spacing:1.735307px;} .wsa1{word-spacing:1.740000px;} .ws491{word-spacing:1.760000px;} .ws186{word-spacing:1.764000px;} .ws508{word-spacing:1.774746px;} .ws12{word-spacing:1.774800px;} .ws3{word-spacing:1.799508px;} .ws549{word-spacing:1.800000px;} .ws38{word-spacing:1.809600px;} .ws24d{word-spacing:1.836000px;} .ws9c{word-spacing:1.844400px;} .ws4d4{word-spacing:1.853624px;} .ws565{word-spacing:1.856000px;} .ws448{word-spacing:1.870000px;} .ws4b3{word-spacing:1.872000px;} .ws3c{word-spacing:1.879200px;} .ws51f{word-spacing:1.893062px;} .ws166{word-spacing:1.908000px;} .ws3e9{word-spacing:1.936000px;} .ws1c8{word-spacing:1.944000px;} .ws15{word-spacing:1.948800px;} .ws55e{word-spacing:1.970748px;} .ws49a{word-spacing:1.971200px;} .ws4c0{word-spacing:1.980000px;} .ws23{word-spacing:1.983600px;} .ws367{word-spacing:2.006000px;} .ws53d{word-spacing:2.011379px;} .ws207{word-spacing:2.016000px;} .ws1c{word-spacing:2.018400px;} .ws407{word-spacing:2.041600px;} .ws26d{word-spacing:2.052000px;} .ws99{word-spacing:2.053200px;} .ws419{word-spacing:2.074000px;} .ws14f{word-spacing:2.088000px;} .ws53a{word-spacing:2.090256px;} .ws44e{word-spacing:2.108000px;} .ws19{word-spacing:2.122800px;} .ws142{word-spacing:2.124000px;} .wse5{word-spacing:2.160000px;} .ws532{word-spacing:2.169134px;} .ws82{word-spacing:2.192400px;} .ws27e{word-spacing:2.196000px;} .ws566{word-spacing:2.208000px;} .ws534{word-spacing:2.208573px;} .ws78{word-spacing:2.227200px;} .wsf7{word-spacing:2.232000px;} .ws3b5{word-spacing:2.244000px;} .ws8f{word-spacing:2.262000px;} .ws128{word-spacing:2.268000px;} .ws433{word-spacing:2.278000px;} .ws4d3{word-spacing:2.287450px;} .ws4a3{word-spacing:2.288000px;} .wsb7{word-spacing:2.296800px;} .ws4b9{word-spacing:2.304000px;} .ws370{word-spacing:2.312000px;} .ws19f{word-spacing:2.340000px;} .ws373{word-spacing:2.346000px;} .ws4fe{word-spacing:2.356000px;} .ws496{word-spacing:2.358400px;} .ws7d{word-spacing:2.366400px;} .ws191{word-spacing:2.376000px;} .ws567{word-spacing:2.400000px;} .ws548{word-spacing:2.403403px;} .ws252{word-spacing:2.412000px;} .ws5{word-spacing:2.427880px;} .ws4a{word-spacing:2.436000px;} .ws15c{word-spacing:2.448000px;} .ws4f7{word-spacing:2.470000px;} .ws449{word-spacing:2.482000px;} .wsf8{word-spacing:2.484000px;} .ws51d{word-spacing:2.484644px;} .ws14{word-spacing:2.505600px;} .ws3b4{word-spacing:2.516000px;} .ws264{word-spacing:2.520000px;} .ws408{word-spacing:2.534400px;} .ws11{word-spacing:2.540400px;} .ws219{word-spacing:2.556000px;} .wsc{word-spacing:2.575200px;} .ws422{word-spacing:2.584000px;} .ws546{word-spacing:2.585479px;} .ws11c{word-spacing:2.592000px;} .ws3e0{word-spacing:2.604800px;} .wsc7{word-spacing:2.610000px;} .ws4fc{word-spacing:2.622000px;} .ws4c5{word-spacing:2.628000px;} .ws30f{word-spacing:2.664000px;} .ws45{word-spacing:2.679600px;} .ws531{word-spacing:2.681838px;} .ws1d0{word-spacing:2.700000px;} .ws15d{word-spacing:2.736000px;} .ws3e6{word-spacing:2.745600px;} .ws305{word-spacing:2.772000px;} .ws483{word-spacing:2.780800px;} .ws2a{word-spacing:2.784000px;} .ws238{word-spacing:2.808000px;} .ws467{word-spacing:2.816000px;} .ws44d{word-spacing:2.822000px;} .ws175{word-spacing:2.844000px;} .ws568{word-spacing:2.848000px;} .ws192{word-spacing:2.880000px;} .ws53f{word-spacing:2.918471px;} .ws84{word-spacing:2.923200px;} .ws2f8{word-spacing:2.952000px;} .ws10f{word-spacing:2.988000px;} .ws10{word-spacing:2.992800px;} .ws544{word-spacing:2.997349px;} .ws56c{word-spacing:3.008000px;} .ws1b4{word-spacing:3.024000px;} .ws4a4{word-spacing:3.027200px;} .ws8a{word-spacing:3.027600px;} .ws14b{word-spacing:3.060000px;} .ws470{word-spacing:3.062400px;} .ws56f{word-spacing:3.072000px;} .ws43e{word-spacing:3.094000px;} .ws268{word-spacing:3.096000px;} .ws33{word-spacing:3.097200px;} .ws46f{word-spacing:3.097600px;} .ws42{word-spacing:3.132000px;} .wsc0{word-spacing:3.166800px;} .ws4b4{word-spacing:3.168000px;} .ws2fb{word-spacing:3.172000px;} .ws1ea{word-spacing:3.192000px;} .ws126{word-spacing:3.204000px;} .wse9{word-spacing:3.216000px;} .ws53{word-spacing:3.236400px;} .ws4c7{word-spacing:3.240000px;} .ws3b7{word-spacing:3.264000px;} .ws6{word-spacing:3.265080px;} .wsce{word-spacing:3.271200px;} .ws3fc{word-spacing:3.273600px;} .ws241{word-spacing:3.276000px;} .ws45a{word-spacing:3.298000px;} .ws1e2{word-spacing:3.312000px;} .ws3cd{word-spacing:3.344000px;} .ws162{word-spacing:3.348000px;} .ws63{word-spacing:3.375600px;} .ws482{word-spacing:3.379200px;} .ws313{word-spacing:3.384000px;} .ws4e0{word-spacing:3.391737px;} .ws362{word-spacing:3.400000px;} .ws40{word-spacing:3.410400px;} .ws20c{word-spacing:3.420000px;} .ws38c{word-spacing:3.434000px;} .ws1f3{word-spacing:3.456000px;} .ws45f{word-spacing:3.468000px;} .ws538{word-spacing:3.470614px;} .ws28{word-spacing:3.480000px;} .ws16b{word-spacing:3.492000px;} .ws39f{word-spacing:3.502000px;} .ws4e5{word-spacing:3.510053px;} .ws1ce{word-spacing:3.528000px;} .ws35e{word-spacing:3.549600px;} .ws1f9{word-spacing:3.564000px;} .ws38b{word-spacing:3.570000px;} .wsb6{word-spacing:3.584400px;} .ws29a{word-spacing:3.600000px;} .ws1b{word-spacing:3.619200px;} .ws4e9{word-spacing:3.628370px;} .ws27d{word-spacing:3.636000px;} .ws450{word-spacing:3.638000px;} .ws61{word-spacing:3.654000px;} .ws489{word-spacing:3.660800px;} .ws132{word-spacing:3.672000px;} .ws295{word-spacing:3.692000px;} .ws584{word-spacing:3.693600px;} .ws3bf{word-spacing:3.696000px;} .ws2d6{word-spacing:3.708000px;} .ws35d{word-spacing:3.723600px;} .ws45e{word-spacing:3.740000px;} .ws4cb{word-spacing:3.744000px;} .ws4ef{word-spacing:3.746686px;} .ws3de{word-spacing:3.766400px;} .ws369{word-spacing:3.774000px;} .ws168{word-spacing:3.780000px;} .ws2e{word-spacing:3.793200px;} .ws486{word-spacing:3.801600px;} .ws30e{word-spacing:3.816000px;} .ws4da{word-spacing:3.825564px;} .ws7a{word-spacing:3.828000px;} .ws3df{word-spacing:3.836800px;} .ws4fb{word-spacing:3.838000px;} .ws15a{word-spacing:3.852000px;} .ws109{word-spacing:3.888000px;} .ws542{word-spacing:3.904441px;} .ws1bd{word-spacing:3.924000px;} .ws7b{word-spacing:3.932400px;} .ws3ad{word-spacing:3.944000px;} .ws226{word-spacing:3.960000px;} .wsbe{word-spacing:3.967200px;} .ws487{word-spacing:3.977600px;} .ws2ea{word-spacing:3.996000px;} .ws34a{word-spacing:4.002000px;} .ws2c0{word-spacing:4.032000px;} .wsc4{word-spacing:4.036800px;} .ws388{word-spacing:4.046000px;} .ws4a6{word-spacing:4.048000px;} .ws20e{word-spacing:4.068000px;} .wsbc{word-spacing:4.071600px;} .wseb{word-spacing:4.080000px;} .ws4f0{word-spacing:4.101635px;} .ws26a{word-spacing:4.104000px;} .ws34{word-spacing:4.106400px;} .ws1f0{word-spacing:4.140000px;} .ws49{word-spacing:4.141200px;} .ws3bd{word-spacing:4.153600px;} .ws5d{word-spacing:4.176000px;} .ws536{word-spacing:4.180513px;} .ws3f6{word-spacing:4.188800px;} .wsf0{word-spacing:4.212000px;} .ws420{word-spacing:4.216000px;} .ws3c7{word-spacing:4.224000px;} .ws85{word-spacing:4.245600px;} .ws4b2{word-spacing:4.248000px;} .ws32{word-spacing:4.280400px;} .ws1d5{word-spacing:4.284000px;} .ws345{word-spacing:4.315200px;} .ws2be{word-spacing:4.320000px;} .ws3f8{word-spacing:4.329600px;} .ws504{word-spacing:4.338268px;} .ws58{word-spacing:4.350000px;} .ws1a9{word-spacing:4.356000px;} .ws478{word-spacing:4.364800px;} .ws4ff{word-spacing:4.370000px;} .ws51e{word-spacing:4.377707px;} .ws351{word-spacing:4.384800px;} .ws22f{word-spacing:4.392000px;} .ws4e6{word-spacing:4.417146px;} .ws8d{word-spacing:4.419600px;} .ws43d{word-spacing:4.420000px;} .ws123{word-spacing:4.428000px;} .wsb5{word-spacing:4.454400px;} .ws52b{word-spacing:4.456584px;} .ws16e{word-spacing:4.464000px;} .ws3c0{word-spacing:4.470400px;} .ws43a{word-spacing:4.488000px;} .ws164{word-spacing:4.500000px;} .wse6{word-spacing:4.512000px;} .ws3a0{word-spacing:4.522000px;} .ws23e{word-spacing:4.536000px;} .ws77{word-spacing:4.558800px;} .ws1d4{word-spacing:4.572000px;} .wscb{word-spacing:4.593600px;} .ws149{word-spacing:4.608000px;} .ws506{word-spacing:4.614340px;} .ws443{word-spacing:4.624000px;} .ws79{word-spacing:4.628400px;} .wsfe{word-spacing:4.644000px;} .ws488{word-spacing:4.646400px;} .ws435{word-spacing:4.658000px;} .ws4b5{word-spacing:4.680000px;} .ws43c{word-spacing:4.692000px;} .ws53c{word-spacing:4.693217px;} .wsd2{word-spacing:4.698000px;} .ws23d{word-spacing:4.716000px;} .ws37a{word-spacing:4.726000px;} .ws296{word-spacing:4.732000px;} .wse8{word-spacing:4.752000px;} .ws4d9{word-spacing:4.772095px;} .ws21c{word-spacing:4.788000px;} .ws42b{word-spacing:4.794000px;} .ws18d{word-spacing:4.824000px;} .ws2b3{word-spacing:4.860000px;} .ws39{word-spacing:4.872000px;} .ws52a{word-spacing:4.890411px;} .ws464{word-spacing:4.892800px;} .ws103{word-spacing:4.896000px;} .ws9{word-spacing:4.906800px;} .ws473{word-spacing:4.928000px;} .ws4e4{word-spacing:4.929850px;} .ws1a8{word-spacing:4.932000px;} .ws1ad{word-spacing:4.968000px;} .ws92{word-spacing:4.976400px;} .ws251{word-spacing:5.004000px;} .ws25{word-spacing:5.011200px;} .ws432{word-spacing:5.032000px;} .ws257{word-spacing:5.040000px;} .ws280{word-spacing:5.076000px;} .ws503{word-spacing:5.087605px;} .ws391{word-spacing:5.100000px;} .ws46e{word-spacing:5.104000px;} .ws22e{word-spacing:5.112000px;} .ws5a{word-spacing:5.115600px;} .ws38f{word-spacing:5.134000px;} .ws46a{word-spacing:5.139200px;} .ws201{word-spacing:5.148000px;} .ws356{word-spacing:5.150400px;} .ws437{word-spacing:5.168000px;} .ws154{word-spacing:5.184000px;} .wsab{word-spacing:5.185200px;} .ws37f{word-spacing:5.202000px;} .wscc{word-spacing:5.220000px;} .ws3ff{word-spacing:5.244800px;} .ws20{word-spacing:5.254800px;} .ws301{word-spacing:5.256000px;} .ws3c8{word-spacing:5.280000px;} .ws167{word-spacing:5.292000px;} .ws4e8{word-spacing:5.324238px;} .ws2aa{word-spacing:5.328000px;} .ws49c{word-spacing:5.350400px;} .ws6a{word-spacing:5.359200px;} .ws1b3{word-spacing:5.364000px;} .ws475{word-spacing:5.385600px;} .ws16c{word-spacing:5.436000px;} .ws451{word-spacing:5.440000px;} .ws1d{word-spacing:5.463600px;} .ws24a{word-spacing:5.472000px;} .ws398{word-spacing:5.474000px;} .ws4ec{word-spacing:5.481993px;} .ws1a1{word-spacing:5.508000px;} .ws12a{word-spacing:5.520000px;} .ws34b{word-spacing:5.533200px;} .ws2ed{word-spacing:5.544000px;} .ws29{word-spacing:5.568000px;} .wsf5{word-spacing:5.580000px;} .ws484{word-spacing:5.596800px;} .ws50{word-spacing:5.602800px;} .ws37e{word-spacing:5.610000px;} .ws575{word-spacing:5.613300px;} .ws4be{word-spacing:5.616000px;} .ws231{word-spacing:5.652000px;} .ws48c{word-spacing:5.667200px;} .ws561{word-spacing:5.670000px;} .ws418{word-spacing:5.678000px;} .ws4f2{word-spacing:5.679187px;} .ws153{word-spacing:5.688000px;} .wsd1{word-spacing:5.707200px;} .ws543{word-spacing:5.718626px;} .ws172{word-spacing:5.724000px;} .ws4bb{word-spacing:5.760000px;} .ws3a2{word-spacing:5.780000px;} .ws524{word-spacing:5.796000px;} .ws6d{word-spacing:5.811600px;} .ws1c9{word-spacing:5.832000px;} .ws395{word-spacing:5.848000px;} .ws10a{word-spacing:5.868000px;} .ws33b{word-spacing:5.881200px;} .ws38e{word-spacing:5.882000px;} .ws31c{word-spacing:5.904000px;} .ws17d{word-spacing:5.940000px;} .ws477{word-spacing:5.948800px;} .ws364{word-spacing:5.950000px;} .wsa2{word-spacing:5.950800px;} .ws1d1{word-spacing:5.976000px;} .ws3a4{word-spacing:5.984000px;} .ws1fa{word-spacing:6.012000px;} .ws360{word-spacing:6.018000px;} .ws180{word-spacing:6.048000px;} .ws39e{word-spacing:6.052000px;} .ws50f{word-spacing:6.073575px;} .ws146{word-spacing:6.084000px;} .wsa8{word-spacing:6.090000px;} .ws4dd{word-spacing:6.113014px;} .ws11b{word-spacing:6.120000px;} .ws5b{word-spacing:6.124800px;} .ws12c{word-spacing:6.144000px;} .ws1ab{word-spacing:6.156000px;} .ws179{word-spacing:6.192000px;} .ws39c{word-spacing:6.222000px;} .ws98{word-spacing:6.264000px;} .ws37{word-spacing:6.298800px;} .ws2cf{word-spacing:6.300000px;} .ws513{word-spacing:6.310208px;} .ws284{word-spacing:6.336000px;} .ws255{word-spacing:6.372000px;} .ws353{word-spacing:6.403200px;} .ws120{word-spacing:6.408000px;} .ws97{word-spacing:6.438000px;} .wsa7{word-spacing:6.440000px;} .ws221{word-spacing:6.444000px;} .ws510{word-spacing:6.467963px;} .ws334{word-spacing:6.472800px;} .ws16f{word-spacing:6.480000px;} .ws2b8{word-spacing:6.516000px;} .ws12b{word-spacing:6.528000px;} .ws1d6{word-spacing:6.552000px;} .ws93{word-spacing:6.577200px;} .ws494{word-spacing:6.582400px;} .ws53e{word-spacing:6.586280px;} .ws183{word-spacing:6.588000px;} .ws3f{word-spacing:6.612000px;} .ws23b{word-spacing:6.624000px;} .ws500{word-spacing:6.650000px;} .ws1b6{word-spacing:6.660000px;} .ws462{word-spacing:6.664000px;} .ws110{word-spacing:6.696000px;} .ws4f3{word-spacing:6.704596px;} .ws13c{word-spacing:6.732000px;} .ws9b{word-spacing:6.751200px;} .ws45c{word-spacing:6.766000px;} .ws1f4{word-spacing:6.768000px;} .ws1eb{word-spacing:6.776000px;} .ws7e{word-spacing:6.786000px;} .ws427{word-spacing:6.800000px;} .ws2ca{word-spacing:6.804000px;} .wsd3{word-spacing:6.820800px;} .ws28f{word-spacing:6.840000px;} .wsd0{word-spacing:6.855600px;} .ws3ca{word-spacing:6.864000px;} .ws190{word-spacing:6.876000px;} .ws35{word-spacing:6.890400px;} .ws1a5{word-spacing:6.912000px;} .ws3a{word-spacing:6.925200px;} .ws3d2{word-spacing:6.934400px;} .ws2db{word-spacing:6.948000px;} .ws6b{word-spacing:6.960000px;} .ws21f{word-spacing:6.984000px;} .ws13{word-spacing:6.994800px;} .ws299{word-spacing:7.020000px;} .ws348{word-spacing:7.029600px;} .ws290{word-spacing:7.056000px;} .ws34e{word-spacing:7.064400px;} .ws404{word-spacing:7.075200px;} .ws318{word-spacing:7.092000px;} .ws96{word-spacing:7.099200px;} .ws240{word-spacing:7.128000px;} .ws9a{word-spacing:7.134000px;} .ws3d7{word-spacing:7.145600px;} .ws104{word-spacing:7.164000px;} .wsca{word-spacing:7.168800px;} .ws50e{word-spacing:7.177862px;} .wsef{word-spacing:7.200000px;} .ws4ea{word-spacing:7.217300px;} .ws523{word-spacing:7.236000px;} .ws33f{word-spacing:7.238400px;} .ws3ba{word-spacing:7.242000px;} .ws1fb{word-spacing:7.272000px;} .wsbd{word-spacing:7.273200px;} .ws45b{word-spacing:7.276000px;} .ws40a{word-spacing:7.286400px;} .ws2ee{word-spacing:7.308000px;} .ws457{word-spacing:7.310000px;} .ws50d{word-spacing:7.335617px;} .wsd7{word-spacing:7.342800px;} .ws119{word-spacing:7.344000px;} .ws2f6{word-spacing:7.380000px;} .ws3e7{word-spacing:7.392000px;} .ws17c{word-spacing:7.416000px;} .ws51b{word-spacing:7.453933px;} .ws35c{word-spacing:7.482000px;} .ws210{word-spacing:7.488000px;} .wsae{word-spacing:7.516800px;} .ws248{word-spacing:7.524000px;} .wsa3{word-spacing:7.551600px;} .ws116{word-spacing:7.560000px;} .ws4a8{word-spacing:7.603200px;} .ws50a{word-spacing:7.611688px;} .ws87{word-spacing:7.621200px;} .ws4b1{word-spacing:7.632000px;} .ws411{word-spacing:7.638400px;} .ws27{word-spacing:7.656000px;} .ws227{word-spacing:7.668000px;} .ws389{word-spacing:7.684000px;} .ws230{word-spacing:7.704000px;} .ws401{word-spacing:7.708800px;} .ws505{word-spacing:7.730005px;} .wsf4{word-spacing:7.740000px;} .ws368{word-spacing:7.752000px;} .ws14c{word-spacing:7.776000px;} .ws3b0{word-spacing:7.786000px;} .ws338{word-spacing:7.795200px;} .ws298{word-spacing:7.800000px;} .ws23f{word-spacing:7.812000px;} .ws3d5{word-spacing:7.814400px;} .ws3b3{word-spacing:7.820000px;} .ws32d{word-spacing:7.830000px;} .ws185{word-spacing:7.848000px;} .wsf3{word-spacing:7.884000px;} .ws3c2{word-spacing:7.884800px;} .ws51a{word-spacing:7.887760px;} .wsb{word-spacing:7.899600px;} .ws4bd{word-spacing:7.920000px;} .ws3f5{word-spacing:7.955200px;} .ws2ab{word-spacing:7.956000px;} .ws352{word-spacing:7.969200px;} .ws4f9{word-spacing:7.980000px;} .ws379{word-spacing:7.990000px;} .ws1c0{word-spacing:7.992000px;} .ws4f8{word-spacing:8.018000px;} .ws234{word-spacing:8.028000px;} .wsb1{word-spacing:8.038800px;} .ws3ea{word-spacing:8.060800px;} .ws2ec{word-spacing:8.064000px;} .ws1dd{word-spacing:8.100000px;} .wsba{word-spacing:8.108400px;} .ws144{word-spacing:8.136000px;} .ws32f{word-spacing:8.143200px;} .ws382{word-spacing:8.160000px;} .ws1a0{word-spacing:8.172000px;} .ws4d{word-spacing:8.178000px;} .ws31a{word-spacing:8.208000px;} .ws4ed{word-spacing:8.242709px;} .ws13a{word-spacing:8.244000px;} .ws91{word-spacing:8.247600px;} .ws13b{word-spacing:8.280000px;} .ws18{word-spacing:8.282400px;} .ws4b0{word-spacing:8.316000px;} .ws375{word-spacing:8.330000px;} .ws23a{word-spacing:8.352000px;} .ws377{word-spacing:8.364000px;} .ws493{word-spacing:8.377600px;} .ws265{word-spacing:8.388000px;} .ws447{word-spacing:8.398000px;} .ws174{word-spacing:8.424000px;} .ws53b{word-spacing:8.439903px;} .ws479{word-spacing:8.448000px;} .ws2b4{word-spacing:8.460000px;} .ws2d{word-spacing:8.491200px;} .ws129{word-spacing:8.496000px;} .ws526{word-spacing:8.532000px;} .ws39a{word-spacing:8.534000px;} .ws480{word-spacing:8.553600px;} .wsb8{word-spacing:8.560800px;} .ws4af{word-spacing:8.568000px;} .wsa5{word-spacing:8.595600px;} .ws4eb{word-spacing:8.597658px;} .ws1e4{word-spacing:8.604000px;} .ws339{word-spacing:8.630400px;} .ws44b{word-spacing:8.636000px;} .ws588{word-spacing:8.640000px;} .ws4a9{word-spacing:8.659200px;} .ws8{word-spacing:8.665200px;} .ws453{word-spacing:8.670000px;} .ws217{word-spacing:8.676000px;} .ws308{word-spacing:8.712000px;} .ws3e{word-spacing:8.734800px;} .ws108{word-spacing:8.748000px;} .ws4e2{word-spacing:8.755414px;} .ws56{word-spacing:8.769600px;} .ws22b{word-spacing:8.784000px;} .ws54{word-spacing:8.804400px;} .ws4fd{word-spacing:8.816000px;} .ws21a{word-spacing:8.820000px;} .ws12d{word-spacing:8.832000px;} .ws3b6{word-spacing:8.840000px;} .ws194{word-spacing:8.856000px;} .ws392{word-spacing:8.874000px;} .ws1fe{word-spacing:8.892000px;} .wsdc{word-spacing:8.943600px;} .ws100{word-spacing:8.964000px;} .ws14d{word-spacing:9.000000px;} .ws3aa{word-spacing:9.010000px;} .ws410{word-spacing:9.011200px;} .ws347{word-spacing:9.048000px;} .ws2a9{word-spacing:9.072000px;} .wsee{word-spacing:9.108000px;} .ws3f3{word-spacing:9.116800px;} .ws31f{word-spacing:9.144000px;} .ws589{word-spacing:9.180000px;} .wsc8{word-spacing:9.187200px;} .ws444{word-spacing:9.214000px;} .ws302{word-spacing:9.216000px;} .ws42e{word-spacing:9.248000px;} .ws27c{word-spacing:9.252000px;} .ws26{word-spacing:9.256800px;} .ws485{word-spacing:9.257600px;} .ws4dc{word-spacing:9.268118px;} .ws399{word-spacing:9.282000px;} .ws1cd{word-spacing:9.288000px;} .ws3fe{word-spacing:9.292800px;} .wsf1{word-spacing:9.324000px;} .ws44{word-spacing:9.326400px;} .ws3c3{word-spacing:9.328000px;} .ws150{word-spacing:9.360000px;} .ws16a{word-spacing:9.396000px;} .ws3e3{word-spacing:9.398400px;} .ws383{word-spacing:9.418000px;} .ws4f5{word-spacing:9.424000px;} .ws269{word-spacing:9.432000px;} .ws40e{word-spacing:9.433600px;} .ws118{word-spacing:9.468000px;} .ws3fb{word-spacing:9.468800px;} .ws3a9{word-spacing:9.486000px;} .ws35b{word-spacing:9.500400px;} .ws19e{word-spacing:9.504000px;} .ws342{word-spacing:9.535200px;} .ws14a{word-spacing:9.540000px;} .ws2b9{word-spacing:9.576000px;} .ws381{word-spacing:9.588000px;} .ws2cc{word-spacing:9.612000px;} .ws41{word-spacing:9.639600px;} .ws171{word-spacing:9.648000px;} .ws2a6{word-spacing:9.684000px;} .ws2dc{word-spacing:9.720000px;} .ws2c5{word-spacing:9.756000px;} .ws386{word-spacing:9.758000px;} .ws2e3{word-spacing:9.792000px;} .ws1b9{word-spacing:9.828000px;} .ws32a{word-spacing:9.848400px;} .ws4a5{word-spacing:9.856000px;} .ws11a{word-spacing:9.864000px;} .ws137{word-spacing:9.900000px;} .ws4c8{word-spacing:9.936000px;} .ws3fa{word-spacing:9.961600px;} .ws169{word-spacing:9.972000px;} .wsb3{word-spacing:9.987600px;} .ws463{word-spacing:9.996000px;} .ws1bb{word-spacing:10.008000px;} .wsa4{word-spacing:10.022400px;} .ws220{word-spacing:10.044000px;} .ws236{word-spacing:10.080000px;} .ws357{word-spacing:10.092000px;} .ws266{word-spacing:10.116000px;} .ws3b9{word-spacing:10.132000px;} .ws202{word-spacing:10.152000px;} .ws1e8{word-spacing:10.188000px;} .ws51c{word-spacing:10.214649px;} .ws262{word-spacing:10.224000px;} .ws333{word-spacing:10.231200px;} .ws385{word-spacing:10.234000px;} .ws591{word-spacing:10.260000px;} .ws2c1{word-spacing:10.296000px;} .ws193{word-spacing:10.332000px;} .ws541{word-spacing:10.332966px;} .wsa{word-spacing:10.335600px;} .ws4aa{word-spacing:10.348800px;} .ws429{word-spacing:10.370000px;} .ws1f5{word-spacing:10.404000px;} .ws3d0{word-spacing:10.419200px;} .ws136{word-spacing:10.440000px;} .ws46{word-spacing:10.474800px;} .ws52c{word-spacing:10.490721px;} .ws69{word-spacing:10.509600px;} .ws4fa{word-spacing:10.526000px;} .ws20d{word-spacing:10.548000px;} .ws271{word-spacing:10.556000px;} .ws476{word-spacing:10.560000px;} .ws539{word-spacing:10.569598px;} .ws1e9{word-spacing:10.584000px;} .ws394{word-spacing:10.608000px;} .ws32c{word-spacing:10.614000px;} .ws2e9{word-spacing:10.620000px;} .ws3c1{word-spacing:10.630400px;} .ws354{word-spacing:10.648800px;} .ws2a4{word-spacing:10.656000px;} .ws409{word-spacing:10.665600px;} .ws1d2{word-spacing:10.692000px;} .wsda{word-spacing:10.718400px;} .ws337{word-spacing:10.753200px;} .ws21b{word-spacing:10.764000px;} .ws2a5{word-spacing:10.800000px;} .ws11f{word-spacing:10.836000px;} .ws366{word-spacing:10.846000px;} .ws58d{word-spacing:10.872000px;} .ws4df{word-spacing:10.885109px;} .ws8e{word-spacing:10.892400px;} .ws223{word-spacing:10.908000px;} .ws39d{word-spacing:10.914000px;} .ws68{word-spacing:10.927200px;} .ws2bc{word-spacing:10.944000px;} .ws48f{word-spacing:10.947200px;} .ws520{word-spacing:10.980000px;} .ws43{word-spacing:10.996800px;} .ws535{word-spacing:11.003425px;} .ws27f{word-spacing:11.016000px;} .ws292{word-spacing:11.088000px;} .ws181{word-spacing:11.124000px;} .ws263{word-spacing:11.160000px;} .ws19a{word-spacing:11.180000px;} .ws147{word-spacing:11.196000px;} .ws4f6{word-spacing:11.210000px;} .ws24b{word-spacing:11.232000px;} .ws187{word-spacing:11.268000px;} .ws26e{word-spacing:11.340000px;} .ws2ce{word-spacing:11.376000px;} .wsb2{word-spacing:11.379600px;} .ws309{word-spacing:11.412000px;} .ws294{word-spacing:11.440000px;} .ws138{word-spacing:11.448000px;} .ws4b8{word-spacing:11.484000px;} .ws1ff{word-spacing:11.520000px;} .ws439{word-spacing:11.526000px;} .ws27a{word-spacing:11.556000px;} .ws224{word-spacing:11.592000px;} .ws3f2{word-spacing:11.616000px;} .ws114{word-spacing:11.664000px;} .ws13e{word-spacing:11.700000px;} .ws58f{word-spacing:11.736000px;} .ws1e{word-spacing:11.797200px;} .ws3a8{word-spacing:11.798000px;} .ws32e{word-spacing:11.832000px;} .ws25a{word-spacing:11.844000px;} .ws4cc{word-spacing:11.880000px;} .ws522{word-spacing:11.916000px;} .ws498{word-spacing:11.932800px;} .ws36b{word-spacing:11.934000px;} .ws327{word-spacing:11.952000px;} .ws2b0{word-spacing:11.988000px;} .ws3bb{word-spacing:12.003200px;} .ws127{word-spacing:12.024000px;} .ws3d{word-spacing:12.040800px;} .ws396{word-spacing:12.070000px;} .ws3da{word-spacing:12.073600px;} .ws4b{word-spacing:12.075600px;} .ws4a7{word-spacing:12.108800px;} .ws139{word-spacing:12.132000px;} .ws3d1{word-spacing:12.144000px;} .ws1a2{word-spacing:12.168000px;} .ws17b{word-spacing:12.204000px;} .ws289{word-spacing:12.240000px;} .ws2c4{word-spacing:12.276000px;} .ws461{word-spacing:12.308000px;} .ws182{word-spacing:12.312000px;} .ws21e{word-spacing:12.348000px;} .ws113{word-spacing:12.384000px;} .ws4a1{word-spacing:12.390400px;} .ws2e0{word-spacing:12.420000px;} .ws3a1{word-spacing:12.444000px;} .ws320{word-spacing:12.492000px;} .ws101{word-spacing:12.564000px;} .ws2a8{word-spacing:12.600000px;} .ws47d{word-spacing:12.636800px;} .ws73{word-spacing:12.667200px;} .wsf6{word-spacing:12.744000px;} .ws456{word-spacing:12.750000px;} .ws130{word-spacing:12.780000px;} .ws303{word-spacing:12.816000px;} .ws291{word-spacing:12.852000px;} .ws2e4{word-spacing:12.924000px;} .ws2fd{word-spacing:12.948000px;} .ws38d{word-spacing:12.954000px;} .ws156{word-spacing:12.960000px;} .ws474{word-spacing:12.988800px;} .ws1dc{word-spacing:12.996000px;} .ws519{word-spacing:13.014804px;} .ws4c1{word-spacing:13.032000px;} .ws134{word-spacing:13.068000px;} .ws36{word-spacing:13.084800px;} .ws1a4{word-spacing:13.104000px;} .ws36e{word-spacing:13.124000px;} .ws212{word-spacing:13.140000px;} .ws2c2{word-spacing:13.176000px;} .ws3a6{word-spacing:13.192000px;} .ws208{word-spacing:13.212000px;} .wsc9{word-spacing:13.224000px;} .ws3b1{word-spacing:13.226000px;} .ws58c{word-spacing:13.248000px;} .ws35a{word-spacing:13.258800px;} .ws46b{word-spacing:13.270400px;} .wsf2{word-spacing:13.284000px;} .ws3fd{word-spacing:13.305600px;} .ws2b5{word-spacing:13.320000px;} .ws59{word-spacing:13.328400px;} .ws1f7{word-spacing:13.356000px;} .ws197{word-spacing:13.392000px;} .ws170{word-spacing:13.428000px;} .ws40d{word-spacing:13.446400px;} .ws2d1{word-spacing:13.464000px;} .ws141{word-spacing:13.500000px;} .wsd8{word-spacing:13.502400px;} .ws400{word-spacing:13.516800px;} .ws527{word-spacing:13.527508px;} .ws3a7{word-spacing:13.532000px;} .ws2f7{word-spacing:13.536000px;} .ws384{word-spacing:13.566000px;} .ws3f0{word-spacing:13.587200px;} .ws1e5{word-spacing:13.608000px;} .ws28c{word-spacing:13.644000px;} .ws2bd{word-spacing:13.680000px;} .ws3ee{word-spacing:13.692800px;} .ws34d{word-spacing:13.711200px;} .ws135{word-spacing:13.716000px;} .ws528{word-spacing:13.764141px;} .ws148{word-spacing:13.824000px;} .ws40f{word-spacing:13.833600px;} .ws43f{word-spacing:13.838000px;} .ws32b{word-spacing:13.850400px;} .ws254{word-spacing:13.896000px;} .ws55{word-spacing:13.920000px;} .ws18f{word-spacing:14.004000px;} .ws36c{word-spacing:14.008000px;} .wsc5{word-spacing:14.024400px;} .ws47c{word-spacing:14.044800px;} .ws1ca{word-spacing:14.076000px;} .ws319{word-spacing:14.112000px;} .ws2f2{word-spacing:14.184000px;} .ws1d9{word-spacing:14.292000px;} .ws378{word-spacing:14.314000px;} .wsc1{word-spacing:14.337600px;} .ws1c3{word-spacing:14.364000px;} .ws256{word-spacing:14.400000px;} .ws25c{word-spacing:14.472000px;} .ws372{word-spacing:14.484000px;} .ws3ef{word-spacing:14.608000px;} .ws117{word-spacing:14.616000px;} .ws3a5{word-spacing:14.620000px;} .ws472{word-spacing:14.678400px;} .ws18c{word-spacing:14.688000px;} .ws416{word-spacing:14.713600px;} .ws243{word-spacing:14.724000px;} .ws4a0{word-spacing:14.748800px;} .ws60{word-spacing:14.755200px;} .ws390{word-spacing:14.790000px;} .ws1ef{word-spacing:14.796000px;} .ws2a2{word-spacing:14.832000px;} .ws222{word-spacing:14.868000px;} .ws2d8{word-spacing:14.904000px;} .ws58e{word-spacing:14.976000px;} .ws336{word-spacing:14.998800px;} .ws267{word-spacing:15.012000px;} .ws307{word-spacing:15.120000px;} .ws145{word-spacing:15.192000px;} .ws246{word-spacing:15.228000px;} .ws188{word-spacing:15.264000px;} .wsb9{word-spacing:15.277200px;} .ws245{word-spacing:15.300000px;} .ws49e{word-spacing:15.312000px;} .ws205{word-spacing:15.336000px;} .ws4e{word-spacing:15.346800px;} .ws2b7{word-spacing:15.372000px;} .ws2ad{word-spacing:15.408000px;} .ws36d{word-spacing:15.436000px;} .ws481{word-spacing:15.488000px;} .ws31b{word-spacing:15.516000px;} .ws7f{word-spacing:15.520800px;} .ws466{word-spacing:15.558400px;} .ws43b{word-spacing:15.606000px;} .ws25d{word-spacing:15.624000px;} .ws4e7{word-spacing:15.657204px;} .ws225{word-spacing:15.660000px;} .ws6c{word-spacing:15.694800px;} .ws102{word-spacing:15.696000px;} .ws51{word-spacing:15.729600px;} .ws49d{word-spacing:15.734400px;} .ws4f1{word-spacing:15.736081px;} .ws20a{word-spacing:15.768000px;} .ws454{word-spacing:15.776000px;} .ws206{word-spacing:15.804000px;} .ws297{word-spacing:15.808000px;} .ws24c{word-spacing:15.840000px;} .ws34f{word-spacing:15.868800px;} .ws314{word-spacing:15.876000px;} .ws7{word-spacing:15.903600px;} .ws2ef{word-spacing:15.912000px;} .ws237{word-spacing:15.984000px;} .ws283{word-spacing:16.020000px;} .ws3d9{word-spacing:16.086400px;} .ws25f{word-spacing:16.092000px;} .ws1c4{word-spacing:16.128000px;} .ws3f4{word-spacing:16.156800px;} .ws58a{word-spacing:16.236000px;} .ws436{word-spacing:16.252000px;} .ws281{word-spacing:16.308000px;} .ws94{word-spacing:16.321200px;} .ws228{word-spacing:16.344000px;} .ws590{word-spacing:16.380000px;} .ws261{word-spacing:16.416000px;} .ws393{word-spacing:16.456000px;} .ws2bb{word-spacing:16.560000px;} .ws2bf{word-spacing:16.596000px;} .ws415{word-spacing:16.614400px;} .ws2ae{word-spacing:16.632000px;} .ws3f9{word-spacing:16.684800px;} .ws242{word-spacing:16.704000px;} .ws1b1{word-spacing:16.740000px;} .wscd{word-spacing:16.773600px;} .ws11d{word-spacing:16.776000px;} .ws258{word-spacing:16.848000px;} .ws95{word-spacing:16.982400px;} .ws2b2{word-spacing:17.172000px;} .ws1a3{word-spacing:17.208000px;} .ws28a{word-spacing:17.244000px;} .ws374{word-spacing:17.272000px;} .ws143{word-spacing:17.388000px;} .ws1a6{word-spacing:17.460000px;} .ws21d{word-spacing:17.496000px;} .ws10c{word-spacing:17.532000px;} .wsc2{word-spacing:17.574000px;} .ws3cf{word-spacing:17.635200px;} .ws341{word-spacing:17.678400px;} .ws33c{word-spacing:17.782800px;} .ws2c3{word-spacing:17.784000px;} .ws34c{word-spacing:17.817600px;} .ws1df{word-spacing:17.820000px;} .ws27b{word-spacing:17.856000px;} .ws203{word-spacing:17.964000px;} .ws253{word-spacing:18.000000px;} .ws244{word-spacing:18.072000px;} .ws25e{word-spacing:18.108000px;} .ws42a{word-spacing:18.122000px;} .ws1f1{word-spacing:18.144000px;} .ws29c{word-spacing:18.180000px;} .ws3bc{word-spacing:18.198400px;} .ws199{word-spacing:18.200000px;} .ws25b{word-spacing:18.252000px;} .ws140{word-spacing:18.360000px;} .ws412{word-spacing:18.374400px;} .ws1da{word-spacing:18.396000px;} .ws157{word-spacing:18.468000px;} .ws209{word-spacing:18.684000px;} .ws260{word-spacing:18.756000px;} .ws316{word-spacing:18.864000px;} .ws17f{word-spacing:18.936000px;} .ws426{word-spacing:18.938000px;} .ws111{word-spacing:19.008000px;} .ws28d{word-spacing:19.080000px;} .ws349{word-spacing:19.209600px;} .ws1d3{word-spacing:19.296000px;} .ws29f{word-spacing:19.440000px;} .ws198{word-spacing:19.500000px;} .ws3ce{word-spacing:19.571200px;} .ws3be{word-spacing:19.641600px;} .ws31e{word-spacing:19.908000px;} .ws323{word-spacing:20.124000px;} .ws2a3{word-spacing:20.340000px;} .ws328{word-spacing:20.376000px;} .ws1f6{word-spacing:20.520000px;} .ws2c8{word-spacing:20.592000px;} .ws361{word-spacing:20.706000px;} .ws1b2{word-spacing:20.736000px;} .ws1cc{word-spacing:20.772000px;} .ws2fc{word-spacing:20.800000px;} .ws3e5{word-spacing:20.803200px;} .ws455{word-spacing:20.842000px;} .ws452{word-spacing:20.876000px;} .ws286{word-spacing:20.916000px;} .ws11e{word-spacing:21.024000px;} .ws2d5{word-spacing:21.060000px;} .ws315{word-spacing:21.096000px;} .ws330{word-spacing:21.123600px;} .ws189{word-spacing:21.240000px;} .ws121{word-spacing:21.312000px;} .ws72{word-spacing:21.367200px;} .ws300{word-spacing:21.420000px;} .ws1bf{word-spacing:21.456000px;} .ws195{word-spacing:21.636000px;} .ws3b{word-spacing:21.784800px;} .ws9e{word-spacing:21.854400px;} .ws47f{word-spacing:22.070400px;} .ws49f{word-spacing:22.140800px;} .ws20b{word-spacing:22.644000px;} .ws26f{word-spacing:22.788000px;} .ws5e{word-spacing:23.037600px;} .ws414{word-spacing:23.337600px;} .wscf{word-spacing:23.385600px;} .wsbf{word-spacing:23.490000px;} .ws1f8{word-spacing:23.508000px;} .ws33e{word-spacing:23.524800px;} .ws18a{word-spacing:23.688000px;} .ws29e{word-spacing:23.724000px;} .ws2d7{word-spacing:23.760000px;} .ws196{word-spacing:23.976000px;} .ws2f1{word-spacing:24.048000px;} .ws2df{word-spacing:24.084000px;} .ws1cb{word-spacing:24.264000px;} .ws2e8{word-spacing:24.336000px;} .ws317{word-spacing:24.552000px;} .ws343{word-spacing:24.638400px;} .ws58b{word-spacing:24.804000px;} .ws214{word-spacing:24.948000px;} .wsfb{word-spacing:25.020000px;} .ws26b{word-spacing:25.092000px;} .ws2f0{word-spacing:25.128000px;} .ws42f{word-spacing:26.112000px;} .ws293{word-spacing:26.208000px;} .ws4f{word-spacing:26.239200px;} .ws215{word-spacing:26.316000px;} .ws2e1{word-spacing:26.424000px;} .ws2d9{word-spacing:26.532000px;} .ws1e1{word-spacing:26.604000px;} .ws213{word-spacing:26.640000px;} .ws2a1{word-spacing:26.964000px;} .ws122{word-spacing:27.036000px;} .ws2cb{word-spacing:27.108000px;} .ws1db{word-spacing:27.468000px;} .ws26c{word-spacing:27.756000px;} .ws428{word-spacing:27.914000px;} .ws440{word-spacing:28.730000px;} .ws3d4{word-spacing:28.899200px;} .ws387{word-spacing:28.934000px;} .ws1d7{word-spacing:29.232000px;} .ws18b{word-spacing:30.132000px;} .ws249{word-spacing:30.312000px;} .ws39b{word-spacing:30.600000px;} .ws2f3{word-spacing:31.536000px;} .ws2a0{word-spacing:31.788000px;} .ws270{word-spacing:32.004000px;} .ws2ba{word-spacing:32.040000px;} .ws403{word-spacing:32.208000px;} .ws1e7{word-spacing:33.192000px;} .ws2eb{word-spacing:34.236000px;} .ws321{word-spacing:35.028000px;} .ws3d3{word-spacing:35.164800px;} .ws3d8{word-spacing:35.270400px;} .ws2b1{word-spacing:36.144000px;} .ws31d{word-spacing:37.080000px;} .ws2e2{word-spacing:37.116000px;} .ws1b0{word-spacing:37.260000px;} .ws425{word-spacing:37.910000px;} .ws218{word-spacing:40.212000px;} .ws259{word-spacing:41.004000px;} .ws112{word-spacing:44.316000px;} .ws200{word-spacing:47.556000px;} .ws553{word-spacing:48.982000px;} .ws551{word-spacing:50.122000px;} .ws2f4{word-spacing:59.400000px;} .ws554{word-spacing:66.462000px;} .ws552{word-spacing:66.956000px;} .wsdb{word-spacing:68.277600px;} .ws55c{word-spacing:134.759486px;} .ws55a{word-spacing:135.139805px;} .ws557{word-spacing:135.520123px;} ._1e{margin-left:-2595.980936px;} ._85{margin-left:-2154.818943px;} ._83{margin-left:-2146.302943px;} ._43{margin-left:-1741.481130px;} ._49{margin-left:-1571.118147px;} ._41{margin-left:-1060.062820px;} ._40{margin-left:-823.049200px;} ._3f{margin-left:-737.664000px;} ._42{margin-left:-619.680000px;} ._84{margin-left:-331.365763px;} ._71{margin-left:-277.253365px;} ._9{margin-left:-248.549716px;} ._2{margin-left:-230.580774px;} ._55{margin-left:-138.444664px;} ._4e{margin-left:-135.378279px;} ._6c{margin-left:-133.370147px;} ._4f{margin-left:-106.839639px;} ._67{margin-left:-98.540859px;} ._5d{margin-left:-86.385130px;} ._6e{margin-left:-58.787565px;} ._50{margin-left:-57.577561px;} ._66{margin-left:-49.900935px;} ._69{margin-left:-42.874456px;} ._6a{margin-left:-40.459007px;} ._16{margin-left:-39.389028px;} ._1d{margin-left:-36.709120px;} ._5c{margin-left:-35.683898px;} ._13{margin-left:-34.119940px;} ._1c{margin-left:-31.597120px;} ._21{margin-left:-29.448000px;} ._17{margin-left:-27.925120px;} ._20{margin-left:-26.658422px;} ._14{margin-left:-25.461242px;} ._d{margin-left:-24.073120px;} ._c{margin-left:-22.050422px;} ._18{margin-left:-20.963725px;} ._e{margin-left:-19.105242px;} ._19{margin-left:-17.726320px;} ._a2{margin-left:-16.627817px;} ._11{margin-left:-15.570422px;} ._b{margin-left:-14.353120px;} ._a{margin-left:-12.647725px;} ._38{margin-left:-11.598820px;} ._10{margin-left:-10.193028px;} ._12{margin-left:-8.998331px;} ._31{margin-left:-7.818820px;} ._3{margin-left:-5.659268px;} ._0{margin-left:-3.726870px;} ._1{margin-left:-1.937180px;} ._6{width:1.793303px;} ._7{width:3.046753px;} ._15{width:4.058627px;} ._5{width:5.430610px;} ._8{width:7.229180px;} ._f{width:11.036594px;} ._4{width:12.072860px;} ._82{width:15.156000px;} ._81{width:17.928000px;} ._4c{width:21.360701px;} ._76{width:23.649221px;} ._54{width:24.883920px;} ._5f{width:26.337783px;} ._58{width:27.955899px;} ._7c{width:29.163034px;} ._79{width:32.287449px;} ._6d{width:34.218246px;} ._2f{width:35.420000px;} ._63{width:37.216470px;} ._3c{width:38.582180px;} ._72{width:41.079678px;} ._73{width:42.136118px;} ._5a{width:43.765680px;} ._65{width:46.882865px;} ._80{width:48.276000px;} ._37{width:49.350000px;} ._52{width:50.454251px;} ._7a{width:52.971298px;} ._35{width:54.040000px;} ._74{width:55.843230px;} ._47{width:57.760000px;} ._34{width:58.800000px;} ._44{width:60.382000px;} ._46{width:62.433180px;} ._45{width:63.460000px;} ._62{width:65.631343px;} ._7f{width:66.694039px;} ._33{width:67.830000px;} ._9b{width:69.124000px;} ._36{width:70.595000px;} ._2b{width:71.855000px;} ._75{width:73.659751px;} ._61{width:75.265042px;} ._3b{width:77.245000px;} ._27{width:78.645000px;} ._29{width:79.765000px;} ._28{width:81.165000px;} ._2d{width:82.425000px;} ._2c{width:84.012180px;} ._25{width:85.575000px;} ._2e{width:86.660000px;} ._2a{width:88.375000px;} ._6f{width:89.729410px;} ._68{width:90.930959px;} ._94{width:92.477379px;} ._26{width:93.555000px;} ._30{width:95.200000px;} ._39{width:96.705000px;} ._56{width:97.850118px;} ._3a{width:99.657180px;} ._59{width:101.484272px;} ._70{width:103.367380px;} ._78{width:104.489721px;} ._5b{width:106.934123px;} ._86{width:108.018158px;} ._95{width:109.193011px;} ._89{width:110.208571px;} ._7b{width:111.912962px;} ._60{width:114.108188px;} ._5e{width:115.581407px;} ._57{width:117.589708px;} ._4b{width:119.316979px;} ._90{width:120.526661px;} ._7d{width:121.894207px;} ._64{width:123.043939px;} ._6b{width:127.122984px;} ._51{width:129.301586px;} ._53{width:132.072104px;} ._4d{width:135.507446px;} ._77{width:136.537145px;} ._8b{width:139.992915px;} ._96{width:146.666667px;} ._8f{width:153.360373px;} ._88{width:158.005720px;} ._9f{width:165.072637px;} ._7e{width:183.024733px;} ._1f{width:187.614497px;} ._8a{width:192.923394px;} ._9c{width:215.031540px;} ._9d{width:217.578360px;} ._91{width:223.369882px;} ._98{width:234.811088px;} ._99{width:236.673801px;} ._9e{width:242.987017px;} ._9a{width:274.242743px;} ._97{width:275.494645px;} ._8c{width:312.695269px;} ._87{width:320.298634px;} ._8d{width:324.035976px;} ._8e{width:335.931282px;} ._93{width:338.281662px;} ._92{width:347.903849px;} ._1b{width:388.819064px;} ._32{width:498.718580px;} ._1a{width:554.019064px;} ._a1{width:587.089669px;} ._4a{width:595.971416px;} ._48{width:723.105530px;} ._3d{width:890.836697px;} ._3e{width:1101.939380px;} ._a0{width:1620.451287px;} ._22{width:1738.963580px;} ._23{width:1750.257180px;} ._24{width:1755.017180px;} .fc21{color:rgb(223,164,20);} .fc1f{color:rgb(91,8,10);} .fc23{color:rgb(236,28,38);} .fc1e{color:rgb(212,31,41);} .fc1c{color:rgb(65,75,98);} .fc1b{color:rgb(251,199,7);} .fc17{color:rgb(48,44,45);} .fc16{color:rgb(41,70,117);} .fc15{color:rgb(151,208,220);} .fc14{color:rgb(151,208,221);} .fc12{color:rgb(16,71,72);} .fc11{color:rgb(234,169,16);} .fc10{color:rgb(236,168,10);} .fcd{color:rgb(236,107,30);} .fc3{color:rgb(251,202,142);} .fc18{color:rgb(193,34,41);} .fc2{color:transparent;} .fc0{color:rgb(255,255,255);} .fcb{color:rgb(0,0,0);} .fc1a{color:rgb(231,221,25);} .fc4{color:rgb(244,111,22);} .fc1{color:rgb(35,31,32);} .fc6{color:rgb(75,71,72);} .fc8{color:rgb(22,115,183);} .fc1d{color:rgb(255,242,0);} .fcf{color:rgb(228,164,9);} .fc19{color:rgb(232,220,0);} .fc9{color:rgb(228,162,10);} .fc22{color:rgb(225,164,22);} .fc20{color:rgb(229,183,6);} .fc13{color:rgb(172,108,35);} .fc7{color:rgb(16,15,13);} .fca{color:rgb(94,60,38);} .fcc{color:rgb(150,46,30);} .fc5{color:rgb(165,163,164);} .fce{color:rgb(237,28,36);} .fs23{font-size:20.000000px;} .fs22{font-size:24.000000px;} .fs19{font-size:28.000000px;} .fs18{font-size:28.987687px;} .fs38{font-size:31.049600px;} .fs4{font-size:32.000000px;} .fs51{font-size:32.076000px;} .fs60{font-size:33.380400px;} .fs26{font-size:34.000000px;} .fs10{font-size:34.800000px;} .fs31{font-size:35.000000px;} .fs27{font-size:35.200000px;} .fs15{font-size:36.000000px;} .fs3f{font-size:36.415200px;} .fs34{font-size:38.000000px;} .fs33{font-size:39.438800px;} .fs11{font-size:39.530400px;} .fs8{font-size:40.000000px;} .fs2c{font-size:40.500000px;} .fs65{font-size:40.622400px;} .fs7{font-size:41.511200px;} .fs55{font-size:42.257600px;} .fs32{font-size:43.200000px;} .fs3e{font-size:44.000000px;} .fs64{font-size:45.700000px;} .fs67{font-size:45.829200px;} .fs5a{font-size:46.000000px;} .fs35{font-size:46.070000px;} .fs14{font-size:48.000000px;} .fs5c{font-size:48.122000px;} .fs50{font-size:48.413600px;} .fs2d{font-size:48.600000px;} .fsd{font-size:48.601200px;} .fs66{font-size:51.557600px;} .fs17{font-size:52.000000px;} .fs42{font-size:53.437600px;} .fs3a{font-size:55.000000px;} .fs3{font-size:55.348000px;} .fs16{font-size:56.000000px;} .fs2e{font-size:56.341200px;} .fs3d{font-size:57.600000px;} .fs29{font-size:58.418000px;} .fs1a{font-size:60.000000px;} .fsc{font-size:62.052000px;} .fs62{font-size:62.673600px;} .fs43{font-size:65.340000px;} .fs4c{font-size:68.471200px;} .fs9{font-size:69.160400px;} .fs37{font-size:69.884000px;} .fs6{font-size:72.000000px;} .fs47{font-size:72.600000px;} .fs63{font-size:75.000098px;} .fs12{font-size:78.910400px;} .fs1f{font-size:80.000000px;} .fs5f{font-size:80.690000px;} .fsa{font-size:81.263200px;} .fse{font-size:83.720000px;} .fs5b{font-size:84.000000px;} .fs40{font-size:84.375200px;} .fs30{font-size:85.000000px;} .fs61{font-size:88.000000px;} .fs1e{font-size:89.600000px;} .fs4d{font-size:92.000000px;} .fs56{font-size:92.264015px;} .fs36{font-size:94.549200px;} .fs1{font-size:96.000000px;} .fs44{font-size:100.188000px;} .fs54{font-size:103.723600px;} .fs53{font-size:104.000000px;} .fs13{font-size:108.000000px;} .fs48{font-size:111.320000px;} .fs25{font-size:112.000000px;} .fs2f{font-size:115.000000px;} .fs2{font-size:119.114400px;} .fs28{font-size:124.000000px;} .fs1d{font-size:128.000000px;} .fs41{font-size:129.375200px;} .fs49{font-size:129.531600px;} .fs58{font-size:132.000000px;} .fs24{font-size:138.000000px;} .fs4b{font-size:140.000000px;} .fs20{font-size:143.000000px;} .fs4a{font-size:143.254000px;} .fs39{font-size:145.800000px;} .fs1b{font-size:153.600000px;} .fs21{font-size:155.769200px;} .fs5e{font-size:160.380000px;} .fs59{font-size:162.000000px;} .fs52{font-size:164.433200px;} .fs3c{font-size:165.000000px;} .fs2b{font-size:167.400000px;} .fsf{font-size:180.000000px;} .fs4e{font-size:187.238400px;} .fs4f{font-size:189.129600px;} .fs3b{font-size:192.000000px;} .fs2a{font-size:194.400000px;} .fs46{font-size:200.000000px;} .fs45{font-size:202.388290px;} .fs5d{font-size:208.614000px;} .fs57{font-size:217.171600px;} .fs5{font-size:271.374000px;} .fsb{font-size:285.821600px;} .fs1c{font-size:345.600000px;} .fs0{font-size:361.832000px;} .yf{bottom:0.000000px;} .y12{bottom:5.524198px;} .ye6b{bottom:14.306818px;} .ye67{bottom:14.307076px;} .ye69{bottom:14.307334px;} .yce{bottom:21.843404px;} .y17f{bottom:21.942876px;} .ycd{bottom:22.382045px;} .y180{bottom:22.665235px;} .ybd4{bottom:23.190200px;} .y11{bottom:36.570814px;} .ye{bottom:36.571459px;} .y3e0{bottom:37.407998px;} .y5b9{bottom:49.987037px;} .y42{bottom:50.763196px;} .ybb5{bottom:54.767367px;} .ybb2{bottom:54.781812px;} .ybb3{bottom:54.785392px;} .y927{bottom:54.864091px;} .y930{bottom:54.887314px;} .y939{bottom:54.910537px;} .ya6c{bottom:56.312939px;} .ya72{bottom:56.336161px;} .ya78{bottom:56.359384px;} .y86f{bottom:56.464790px;} .y877{bottom:56.488013px;} .y87f{bottom:56.511236px;} .y602{bottom:57.130383px;} .y673{bottom:57.186891px;} .y47d{bottom:57.187537px;} .y5df{bottom:57.211662px;} .y41e{bottom:57.226370px;} .y404{bottom:57.261205px;} .y650{bottom:57.264817px;} .y43b{bottom:57.289975px;} .y481{bottom:57.295265px;} .y72c{bottom:57.297458px;} .y752{bottom:57.299780px;} .y7fb{bottom:57.306618px;} .y7dc{bottom:57.329325px;} .y7bb{bottom:57.346742px;} .y796{bottom:57.356160px;} .y6bc{bottom:57.361966px;} .y6e0{bottom:57.427764px;} .y4e5{bottom:57.579486px;} .y8ad{bottom:58.252691px;} .y8b3{bottom:58.275914px;} .y350{bottom:60.038011px;} .yac5{bottom:60.237857px;} .y5b8{bottom:60.262112px;} .yac2{bottom:60.269337px;} .y583{bottom:60.384935px;} .yd29{bottom:60.544011px;} .yabd{bottom:62.064591px;} .yf33{bottom:62.225732px;} .yb21{bottom:63.602717px;} .y387{bottom:64.144068px;} .y10c{bottom:64.365717px;} .ycc{bottom:64.383134px;} .y239{bottom:64.408292px;} .ya4{bottom:64.424935px;} .y10b{bottom:64.435385px;} .y975{bottom:64.439772px;} .y245{bottom:64.454738px;} .y97e{bottom:64.474606px;} .y147{bottom:64.477186px;} .y1ab{bottom:64.477831px;} .y1f4{bottom:64.477960px;} .y27c{bottom:64.481831px;} .y3ab{bottom:64.497313px;} .y987{bottom:64.509440px;} .y257{bottom:64.524406px;} .y7b{bottom:64.557305px;} .y1c9{bottom:64.593946px;} .y212{bottom:64.594075px;} .y29b{bottom:64.597945px;} .y383{bottom:64.605686px;} .y1cf{bottom:64.617169px;} .y2d9{bottom:64.830174px;} .y41{bottom:64.954932px;} .y3d3{bottom:65.601688px;} .y9a3{bottom:65.660519px;} .y9a9{bottom:65.672131px;} .yb63{bottom:65.911971px;} .yd2d{bottom:66.742833px;} .yb47{bottom:67.151684px;} .yd{bottom:67.535248px;} .yb85{bottom:68.480159px;} .y43a{bottom:68.903976px;} .y926{bottom:69.053247px;} .y92f{bottom:69.076470px;} .y938{bottom:69.099693px;} .y581{bottom:69.953519px;} .y696{bottom:70.880627px;} .y672{bottom:71.037768px;} .y584{bottom:71.092600px;} .y64f{bottom:71.115694px;} .ybb4{bottom:71.126019px;} .ybb1{bottom:71.140465px;} .y7ba{bottom:71.197232px;} .y795{bottom:71.206650px;} .y6bb{bottom:71.212455px;} .y6df{bottom:71.278253px;} .y703{bottom:71.344051px;} .y601{bottom:71.377596px;} .y5de{bottom:71.458876px;} .y72b{bottom:71.545961px;} .y751{bottom:71.548283px;} .y773{bottom:71.552799px;} .y7fa{bottom:71.555121px;} .y818{bottom:71.561959px;} .y7db{bottom:71.577828px;} .y47c{bottom:71.585698px;} .ya03{bottom:71.610082px;} .ya09{bottom:71.621693px;} .y41d{bottom:71.717423px;} .y403{bottom:71.752257px;} .y582{bottom:71.782189px;} .ya6b{bottom:71.790962px;} .ya71{bottom:71.814185px;} .ya77{bottom:71.837408px;} .y86e{bottom:71.942814px;} .y876{bottom:71.966037px;} .y87e{bottom:71.989259px;} .y4e4{bottom:72.035705px;} .yf42{bottom:72.278771px;} .yf3b{bottom:72.419140px;} .yf32{bottom:73.063058px;} .y3df{bottom:73.532417px;} .yd66{bottom:73.599088px;} .y8ab{bottom:73.730714px;} .y8b2{bottom:73.753937px;} .y8b9{bottom:73.777160px;} .ya25{bottom:74.637695px;} .y8ac{bottom:74.787354px;} .yc98{bottom:76.215894px;} .y388{bottom:76.800000px;} .y3d2{bottom:77.215689px;} .yd1e{bottom:79.140475px;} .y8d6{bottom:79.640153px;} .y9a2{bottom:79.849675px;} .y9a8{bottom:79.861287px;} .ycb{bottom:79.861545px;} .y17e{bottom:79.871221px;} .y238{bottom:79.886316px;} .ya3{bottom:79.903346px;} .y10a{bottom:79.913796px;} .y974{bottom:79.917795px;} .y244{bottom:79.932761px;} .y97d{bottom:79.952630px;} .y146{bottom:79.955597px;} .y1aa{bottom:79.955855px;} .y1f3{bottom:79.955984px;} .y27b{bottom:79.959855px;} .y3aa{bottom:79.975336px;} .y986{bottom:79.987464px;} .y256{bottom:80.002430px;} .y7a{bottom:80.035716px;} .y1c8{bottom:80.071969px;} .y211{bottom:80.072098px;} .y29a{bottom:80.075969px;} .y382{bottom:80.083710px;} .y1ce{bottom:80.095192px;} .yb62{bottom:80.101127px;} .y2d8{bottom:80.308197px;} .yf0d{bottom:80.418857px;} .y439{bottom:80.517977px;} .yb46{bottom:81.340840px;} .yac1{bottom:81.483789px;} .yafd{bottom:81.964425px;} .yaf9{bottom:81.977146px;} .yc{bottom:83.017142px;} .y925{bottom:83.242403px;} .y92e{bottom:83.265626px;} .yac4{bottom:83.279044px;} .y937{bottom:83.288849px;} .y695{bottom:84.731503px;} .y671{bottom:84.888645px;} .y64e{bottom:84.966570px;} .y7b9{bottom:85.047721px;} .y794{bottom:85.057139px;} .y6ba{bottom:85.062945px;} .y6de{bottom:85.128743px;} .y702{bottom:85.194541px;} .y623{bottom:85.543529px;} .y600{bottom:85.624809px;} .y5dd{bottom:85.706089px;} .y40{bottom:85.711856px;} .y72a{bottom:85.796787px;} .ya02{bottom:85.799238px;} .y772{bottom:85.801302px;} .y729{bottom:85.803625px;} .y817{bottom:85.810462px;} .ya08{bottom:85.810849px;} .ya0e{bottom:85.822461px;} .y7da{bottom:85.826331px;} .y47b{bottom:85.983860px;} .y41c{bottom:86.208476px;} .y402{bottom:86.243310px;} .y4e3{bottom:86.491924px;} .ya6a{bottom:87.268986px;} .ya70{bottom:87.292209px;} .ya76{bottom:87.315431px;} .y86d{bottom:87.420837px;} .y875{bottom:87.444060px;} .y87d{bottom:87.467283px;} .ybb9{bottom:87.471950px;} .ybaf{bottom:87.484671px;} .ybb0{bottom:87.495538px;} .yd65{bottom:88.728104px;} .y3d1{bottom:88.829690px;} .yf4b{bottom:89.021665px;} .y8aa{bottom:89.208738px;} .y8b1{bottom:89.231961px;} .y8b8{bottom:89.255184px;} .y1e{bottom:89.403304px;} .y9a1{bottom:94.038831px;} .y9a7{bottom:94.050442px;} .yb61{bottom:94.290283px;} .yf2a{bottom:94.759900px;} .yca{bottom:95.339955px;} .y17d{bottom:95.349631px;} .y237{bottom:95.364339px;} .ya2{bottom:95.381756px;} .y109{bottom:95.392207px;} .y973{bottom:95.395819px;} .y243{bottom:95.410785px;} .y97c{bottom:95.430653px;} .y1a9{bottom:95.433879px;} .y145{bottom:95.434008px;} .y27a{bottom:95.437878px;} .y3a9{bottom:95.453360px;} .y985{bottom:95.465488px;} .y255{bottom:95.480453px;} .y79{bottom:95.514127px;} .yb45{bottom:95.529995px;} .y1c7{bottom:95.549993px;} .y210{bottom:95.550122px;} .y299{bottom:95.553992px;} .y381{bottom:95.561733px;} .y1cd{bottom:95.573216px;} .ye68{bottom:95.671784px;} .y2d7{bottom:95.786221px;} .ye1f{bottom:95.854470px;} .y924{bottom:97.431559px;} .y92d{bottom:97.454782px;} .y936{bottom:97.478005px;} .yafc{bottom:98.323077px;} .yaf8{bottom:98.335798px;} .yb01{bottom:98.365925px;} .yb{bottom:98.499036px;} .y694{bottom:98.582380px;} .y670{bottom:98.739521px;} .y64d{bottom:98.817447px;} .y7b8{bottom:98.898211px;} .y793{bottom:98.907629px;} .y6b9{bottom:98.913434px;} .y6dd{bottom:98.979232px;} .y701{bottom:99.045031px;} .y622{bottom:99.790742px;} .y5ff{bottom:99.872022px;} .y5dc{bottom:99.953302px;} .ya01{bottom:99.988394px;} .ya07{bottom:100.000005px;} .ya0d{bottom:100.011617px;} .y750{bottom:100.047612px;} .y771{bottom:100.049805px;} .y728{bottom:100.052128px;} .y816{bottom:100.058966px;} .y74f{bottom:100.061288px;} .y7d9{bottom:100.074835px;} .y47a{bottom:100.382021px;} .y41b{bottom:100.699529px;} .y401{bottom:100.734363px;} .y4e2{bottom:100.948142px;} .yabc{bottom:101.599608px;} .yac0{bottom:102.698241px;} .ya69{bottom:102.747009px;} .ya6f{bottom:102.770232px;} .ya75{bottom:102.793455px;} .y86c{bottom:102.898861px;} .y874{bottom:102.922084px;} .y87c{bottom:102.945307px;} .ybb8{bottom:103.830603px;} .ybae{bottom:103.843323px;} .yd64{bottom:103.857119px;} .yac3{bottom:104.493499px;} .y8a9{bottom:104.686762px;} .y8b0{bottom:104.709985px;} .y8b7{bottom:104.733207px;} .ybeb{bottom:104.888465px;} .y9a0{bottom:108.227987px;} .y9a6{bottom:108.239598px;} .yb60{bottom:108.479439px;} .y3de{bottom:109.656837px;} .yb44{bottom:109.719151px;} .yc9{bottom:110.818366px;} .y236{bottom:110.842363px;} .ya1{bottom:110.860167px;} .y108{bottom:110.870617px;} .y972{bottom:110.873843px;} .y242{bottom:110.888809px;} .y97b{bottom:110.908677px;} .y1a8{bottom:110.911902px;} .y1f2{bottom:110.912031px;} .y144{bottom:110.912418px;} .y279{bottom:110.915902px;} .y3a8{bottom:110.931384px;} .y984{bottom:110.943511px;} .y254{bottom:110.958477px;} .y78{bottom:110.992537px;} .y1c6{bottom:111.028017px;} .y20f{bottom:111.028146px;} .y298{bottom:111.032016px;} .y380{bottom:111.039757px;} .y1cc{bottom:111.051239px;} .y22d{bottom:111.144260px;} .y2d6{bottom:111.264244px;} .ye1e{bottom:111.336364px;} .y923{bottom:111.620715px;} .y92c{bottom:111.643938px;} .y935{bottom:111.667161px;} .y693{bottom:112.433257px;} .y66f{bottom:112.590398px;} .y64c{bottom:112.668323px;} .y7b7{bottom:112.748700px;} .y792{bottom:112.758118px;} .y6b8{bottom:112.763924px;} .y6dc{bottom:112.829722px;} .y700{bottom:112.895520px;} .ya{bottom:113.980930px;} .y621{bottom:114.037955px;} .y5fe{bottom:114.119235px;} .ya00{bottom:114.177550px;} .ya06{bottom:114.189161px;} .y5db{bottom:114.200515px;} .ya0c{bottom:114.200773px;} .y770{bottom:114.298309px;} .y727{bottom:114.300631px;} .y815{bottom:114.307469px;} .y74e{bottom:114.309791px;} .y7d8{bottom:114.323338px;} .yafb{bottom:114.681730px;} .yaf7{bottom:114.694450px;} .yb00{bottom:114.724577px;} .y479{bottom:114.780183px;} .yb84{bottom:115.106335px;} .y41a{bottom:115.190582px;} .y400{bottom:115.225416px;} .y8d5{bottom:115.233802px;} .y4e1{bottom:115.404361px;} .ya24{bottom:116.491706px;} .ye65{bottom:117.036282px;} .ya68{bottom:118.225033px;} .ya6e{bottom:118.248256px;} .ya74{bottom:118.271479px;} .yebd{bottom:118.361532px;} .y86b{bottom:118.376885px;} .y873{bottom:118.400108px;} .y87b{bottom:118.423330px;} .ybea{bottom:118.982872px;} .yd63{bottom:118.986134px;} .y8a8{bottom:120.164785px;} .y8af{bottom:120.188008px;} .ybb7{bottom:120.189255px;} .ybad{bottom:120.201975px;} .y8b6{bottom:120.211231px;} .y8da{bottom:121.494035px;} .y99f{bottom:122.417143px;} .y9a5{bottom:122.428754px;} .y9ab{bottom:122.440366px;} .yb5f{bottom:122.668595px;} .yb43{bottom:123.908307px;} .yf29{bottom:124.165178px;} .y922{bottom:125.809871px;} .y92b{bottom:125.833094px;} .y934{bottom:125.856317px;} .yf1a{bottom:125.939919px;} .y692{bottom:126.284133px;} .yc8{bottom:126.296777px;} .y17c{bottom:126.317677px;} .y235{bottom:126.320387px;} .ya0{bottom:126.338578px;} .y107{bottom:126.349028px;} .y971{bottom:126.351866px;} .y241{bottom:126.366832px;} .y97a{bottom:126.386701px;} .y1a7{bottom:126.389926px;} .y1f1{bottom:126.390055px;} .y143{bottom:126.390829px;} .y278{bottom:126.393926px;} .y3a7{bottom:126.409407px;} .y983{bottom:126.421535px;} .y253{bottom:126.436501px;} .y66e{bottom:126.441274px;} .y77{bottom:126.470948px;} .y1c5{bottom:126.506040px;} .y20e{bottom:126.506169px;} .y297{bottom:126.510040px;} .y37f{bottom:126.517781px;} .y64b{bottom:126.519200px;} .y1cb{bottom:126.529263px;} .y7b6{bottom:126.599190px;} .y791{bottom:126.608608px;} .y6b7{bottom:126.614413px;} .y22c{bottom:126.622283px;} .y6db{bottom:126.680212px;} .y2d5{bottom:126.742268px;} .y6ff{bottom:126.746010px;} .ye1d{bottom:126.818258px;} .yabe{bottom:127.729497px;} .yf31{bottom:127.917989px;} .y3f{bottom:128.106571px;} .y620{bottom:128.285168px;} .y5fd{bottom:128.366448px;} .y9ff{bottom:128.366706px;} .ye85{bottom:128.375221px;} .ya05{bottom:128.378317px;} .ya0b{bottom:128.389929px;} .y5da{bottom:128.447728px;} .y726{bottom:128.549134px;} .y76f{bottom:128.555972px;} .y74d{bottom:128.558294px;} .y7d7{bottom:128.571841px;} .y478{bottom:129.178344px;} .y9{bottom:129.462824px;} .yf18{bottom:129.525268px;} .yabf{bottom:129.528752px;} .y419{bottom:129.681635px;} .y3ff{bottom:129.716469px;} .y4e0{bottom:129.860580px;} .yabb{bottom:129.975017px;} .yafe{bottom:131.027661px;} .yafa{bottom:131.040382px;} .yaf6{bottom:131.053102px;} .yaff{bottom:131.079650px;} .y1c{bottom:131.813433px;} .ye64{bottom:132.518176px;} .ybe8{bottom:133.077227px;} .ybe9{bottom:133.077330px;} .ye9f{bottom:133.177833px;} .y1d{bottom:133.634727px;} .ya67{bottom:133.703057px;} .ya6d{bottom:133.726280px;} .ya73{bottom:133.749502px;} .yebc{bottom:133.843426px;} .y86a{bottom:133.854908px;} .y872{bottom:133.878131px;} .y87a{bottom:133.901354px;} .yd62{bottom:134.115150px;} .yf28{bottom:135.002504px;} .y8a7{bottom:135.642809px;} .y8ae{bottom:135.666032px;} .y8b4{bottom:135.689255px;} .yd92{bottom:136.060432px;} .ybb6{bottom:136.547907px;} .ybac{bottom:136.560627px;} .y99e{bottom:136.606299px;} .y9a4{bottom:136.617910px;} .y9aa{bottom:136.629522px;} .y8b5{bottom:136.745894px;} .yf19{bottom:136.777245px;} .yc3f{bottom:136.848720px;} .yb5e{bottom:136.857751px;} .yb42{bottom:138.097463px;} .yf30{bottom:138.755315px;} .y921{bottom:139.999027px;} .y92a{bottom:140.022250px;} .y933{bottom:140.045473px;} .y691{bottom:140.135010px;} .y66d{bottom:140.292151px;} .yf17{bottom:140.362593px;} .y64a{bottom:140.370076px;} .y7b5{bottom:140.449679px;} .y790{bottom:140.459097px;} .y6b6{bottom:140.464903px;} .y6da{bottom:140.530701px;} .y6fe{bottom:140.596499px;} .yede{bottom:140.706550px;} .yc7{bottom:141.775187px;} .y17b{bottom:141.796088px;} .y234{bottom:141.798410px;} .y9f{bottom:141.816988px;} .y106{bottom:141.827439px;} .y970{bottom:141.829890px;} .y240{bottom:141.844856px;} .y979{bottom:141.864724px;} .y1a6{bottom:141.867950px;} .y1f0{bottom:141.868079px;} .y142{bottom:141.869240px;} .y277{bottom:141.871949px;} .y3a6{bottom:141.887431px;} .y982{bottom:141.899559px;} .y252{bottom:141.914524px;} .y76{bottom:141.949359px;} .y1c4{bottom:141.984064px;} .y20d{bottom:141.984193px;} .y296{bottom:141.988063px;} .y37e{bottom:141.995804px;} .y1ca{bottom:142.007287px;} .y22b{bottom:142.100307px;} .y2d4{bottom:142.220292px;} .ya23{bottom:142.290025px;} .ye1c{bottom:142.300153px;} .y61f{bottom:142.532381px;} .y9fe{bottom:142.555862px;} .ya04{bottom:142.567473px;} .ya0a{bottom:142.579085px;} .y5fc{bottom:142.613661px;} .y5d9{bottom:142.694941px;} .y725{bottom:142.799960px;} .y724{bottom:142.802153px;} .y76e{bottom:142.804475px;} .y74c{bottom:142.806798px;} .y7d6{bottom:142.820344px;} .y7f9{bottom:142.899818px;} .y477{bottom:143.576506px;} .ye84{bottom:143.857115px;} .y418{bottom:144.172688px;} .y3fe{bottom:144.207522px;} .y4df{bottom:144.316798px;} .yc66{bottom:144.794286px;} .y8d4{bottom:144.952588px;} .ybe7{bottom:147.171634px;} .y8d8{bottom:147.292354px;} .ye63{bottom:148.000070px;} .ye9e{bottom:148.659728px;} .yd61{bottom:149.244165px;} .yebb{bottom:149.325320px;} .y869{bottom:149.332932px;} .y871{bottom:149.356155px;} .y879{bottom:149.379378px;} .y8d9{bottom:149.787197px;} .yb5d{bottom:151.046907px;} .yf41{bottom:151.580903px;} .yb41{bottom:152.286619px;} .yd91{bottom:152.470643px;} .yf3a{bottom:153.870675px;} .y690{bottom:153.985886px;} .y66c{bottom:154.143027px;} .y920{bottom:154.188183px;} .y929{bottom:154.211406px;} .y649{bottom:154.220953px;} .y932{bottom:154.234629px;} .y7b4{bottom:154.300169px;} .y78f{bottom:154.309587px;} .y6b5{bottom:154.315393px;} .y6d9{bottom:154.381191px;} .y6fd{bottom:154.446989px;} .y61e{bottom:156.779594px;} .y5fb{bottom:156.860874px;} .y5d8{bottom:156.942154px;} .ye16{bottom:157.046657px;} .y723{bottom:157.050656px;} .y76d{bottom:157.052978px;} .y74b{bottom:157.055301px;} .y7d5{bottom:157.068847px;} .y7f8{bottom:157.148321px;} .yc6{bottom:157.257081px;} .y17a{bottom:157.274499px;} .y233{bottom:157.276434px;} .y9e{bottom:157.295399px;} .y105{bottom:157.305849px;} .y96f{bottom:157.307914px;} .y23f{bottom:157.322879px;} .y978{bottom:157.342748px;} .y1a5{bottom:157.345973px;} .y1ef{bottom:157.346102px;} .y141{bottom:157.347651px;} .y276{bottom:157.349973px;} .y3a5{bottom:157.365455px;} .y981{bottom:157.377582px;} .y251{bottom:157.392548px;} .y75{bottom:157.427769px;} .y1c3{bottom:157.462088px;} .y20c{bottom:157.462217px;} .y295{bottom:157.466087px;} .y37d{bottom:157.473828px;} .y22a{bottom:157.578331px;} .y2d3{bottom:157.698315px;} .ye1b{bottom:157.782047px;} .y476{bottom:157.974667px;} .y417{bottom:158.663741px;} .y3fd{bottom:158.698575px;} .y4de{bottom:158.773017px;} .ye83{bottom:159.339009px;} .y8{bottom:160.426612px;} .ybe6{bottom:161.266040px;} .yf40{bottom:162.418229px;} .ye62{bottom:163.481964px;} .ye9d{bottom:164.141622px;} .yd60{bottom:164.373180px;} .yf39{bottom:164.708001px;} .yeba{bottom:164.807214px;} .y868{bottom:164.810956px;} .ye3e{bottom:164.829147px;} .y870{bottom:164.834178px;} .y878{bottom:164.857401px;} .yb5c{bottom:165.236063px;} .yb40{bottom:166.475775px;} .y68f{bottom:167.836763px;} .y66b{bottom:167.993904px;} .y647{bottom:168.045897px;} .y648{bottom:168.067572px;} .ya22{bottom:168.088344px;} .y7b3{bottom:168.150658px;} .y78e{bottom:168.160076px;} .y6b4{bottom:168.165882px;} .y6d8{bottom:168.231680px;} .y6fc{bottom:168.297478px;} .y91f{bottom:168.377339px;} .y928{bottom:168.400562px;} .y931{bottom:168.423785px;} .y61d{bottom:171.026807px;} .y5fa{bottom:171.108087px;} .y5d7{bottom:171.189367px;} .y722{bottom:171.301482px;} .y74a{bottom:171.303804px;} .y7d4{bottom:171.317351px;} .y721{bottom:171.319673px;} .y7f7{bottom:171.396824px;} .yd71{bottom:171.516493px;} .y8d3{bottom:172.039452px;} .y475{bottom:172.372829px;} .ye15{bottom:172.528551px;} .y179{bottom:172.752909px;} .y232{bottom:172.754457px;} .y9d{bottom:172.773810px;} .y104{bottom:172.784260px;} .y96e{bottom:172.785937px;} .y23e{bottom:172.800903px;} .y977{bottom:172.820772px;} .yc88{bottom:172.822143px;} .y1a4{bottom:172.823997px;} .y1ee{bottom:172.824126px;} .y140{bottom:172.826061px;} .y275{bottom:172.827996px;} .y3a4{bottom:172.843478px;} .y980{bottom:172.855606px;} .y250{bottom:172.870572px;} .y74{bottom:172.906180px;} .y1c2{bottom:172.940111px;} .y20b{bottom:172.940240px;} .y294{bottom:172.944111px;} .y37c{bottom:172.951852px;} .y229{bottom:173.056354px;} .y8d7{bottom:173.090673px;} .y416{bottom:173.154793px;} .y2d2{bottom:173.176339px;} .y3fc{bottom:173.189628px;} .y4dd{bottom:173.229236px;} .ye1a{bottom:173.263941px;} .y2c{bottom:174.324862px;} .ye82{bottom:174.820903px;} .ybe5{bottom:175.360447px;} .yed6{bottom:177.001270px;} .yab6{bottom:177.883996px;} .yab0{bottom:177.896252px;} .yc75{bottom:178.762981px;} .ye61{bottom:178.963858px;} .yd5f{bottom:179.502196px;} .ye9c{bottom:179.623516px;} .yc4a{bottom:179.677315px;} .yeb9{bottom:180.289108px;} .ye3d{bottom:180.311041px;} .yb3f{bottom:180.664931px;} .y68e{bottom:181.687639px;} .y66a{bottom:181.844781px;} .y646{bottom:181.896774px;} .y7b2{bottom:182.001148px;} .y78d{bottom:182.010566px;} .y6b3{bottom:182.016372px;} .y6d7{bottom:182.082170px;} .y6fb{bottom:182.147968px;} .y61c{bottom:185.274020px;} .y5f9{bottom:185.355300px;} .y5d6{bottom:185.436580px;} .y749{bottom:185.552307px;} .y76c{bottom:185.556823px;} .y7d3{bottom:185.565854px;} .y720{bottom:185.568176px;} .y7f6{bottom:185.645328px;} .yc0e{bottom:185.927485px;} .yc61{bottom:186.431395px;} .y474{bottom:186.770990px;} .y415{bottom:187.645846px;} .y3fb{bottom:187.680681px;} .y4dc{bottom:187.685454px;} .ye14{bottom:188.010445px;} .yc5{bottom:188.224353px;} .y178{bottom:188.231320px;} .y231{bottom:188.232481px;} .y9c{bottom:188.252220px;} .y103{bottom:188.262671px;} .y96d{bottom:188.263961px;} .y23d{bottom:188.278927px;} .y976{bottom:188.298795px;} .y1a3{bottom:188.302021px;} .y1ed{bottom:188.302150px;} .y13f{bottom:188.304472px;} .y274{bottom:188.306020px;} .y3a3{bottom:188.321502px;} .y97f{bottom:188.333629px;} .y24f{bottom:188.348595px;} .y73{bottom:188.384591px;} .y1c1{bottom:188.418135px;} .y20a{bottom:188.418264px;} .y293{bottom:188.422134px;} .y37b{bottom:188.429875px;} .y228{bottom:188.534378px;} .y2d1{bottom:188.654363px;} .yc48{bottom:188.680037px;} .ye19{bottom:188.745835px;} .ye81{bottom:190.302797px;} .yc57{bottom:190.751901px;} .y3dd{bottom:190.869306px;} .y2b{bottom:191.960142px;} .yab5{bottom:192.077022px;} .yaaf{bottom:192.089279px;} .yed5{bottom:192.483164px;} .ye60{bottom:194.445752px;} .yd5e{bottom:194.631211px;} .yb3e{bottom:194.854087px;} .ye9b{bottom:195.105410px;} .y68d{bottom:195.538516px;} .y669{bottom:195.695657px;} .y645{bottom:195.747651px;} .yeb8{bottom:195.771002px;} .ye3c{bottom:195.792935px;} .y7b1{bottom:195.851637px;} .y78c{bottom:195.861055px;} .y6b2{bottom:195.866861px;} .y6d6{bottom:195.932659px;} .y6fa{bottom:195.998457px;} .ya21{bottom:198.533875px;} .y61b{bottom:199.521233px;} .yc77{bottom:199.588708px;} .y5f8{bottom:199.602513px;} .y5d5{bottom:199.683793px;} .y748{bottom:199.803004px;} .y747{bottom:199.805326px;} .y7d2{bottom:199.814357px;} .y71f{bottom:199.816679px;} .y814{bottom:199.830355px;} .y7f5{bottom:199.893831px;} .y473{bottom:201.169152px;} .y414{bottom:202.136899px;} .y4db{bottom:202.141673px;} .y3fa{bottom:202.171733px;} .ye13{bottom:203.492339px;} .y8d2{bottom:203.536333px;} .yc4{bottom:203.702764px;} .y177{bottom:203.709731px;} .y230{bottom:203.710505px;} .y9b{bottom:203.730631px;} .y102{bottom:203.741081px;} .y23c{bottom:203.756950px;} .y1a2{bottom:203.780044px;} .y1ec{bottom:203.780173px;} .y13e{bottom:203.782883px;} .y273{bottom:203.784044px;} .y3a2{bottom:203.799526px;} .y24e{bottom:203.826619px;} .y72{bottom:203.863001px;} .y1c0{bottom:203.896158px;} .y209{bottom:203.896287px;} .y292{bottom:203.900158px;} .y37a{bottom:203.907899px;} .y227{bottom:204.012402px;} .y2d0{bottom:204.132386px;} .ye18{bottom:204.227729px;} .yfc8{bottom:204.843650px;} .ye80{bottom:205.784691px;} .yaba{bottom:206.257792px;} .yab4{bottom:206.270049px;} .yaae{bottom:206.282305px;} .yc60{bottom:207.114277px;} .ya29{bottom:207.724702px;} .yed4{bottom:207.965058px;} .y68c{bottom:209.389392px;} .y668{bottom:209.546534px;} .y2a{bottom:209.595423px;} .y644{bottom:209.598527px;} .y7b0{bottom:209.702127px;} .y78b{bottom:209.711545px;} .y6b1{bottom:209.717351px;} .yd5d{bottom:209.760226px;} .y6d5{bottom:209.783149px;} .y6f9{bottom:209.848947px;} .ye5f{bottom:209.927646px;} .ye9a{bottom:210.587304px;} .yeb7{bottom:211.252896px;} .ye3b{bottom:211.274829px;} .yd90{bottom:211.446543px;} .y61a{bottom:213.768446px;} .y5f7{bottom:213.849726px;} .y5d4{bottom:213.931006px;} .y746{bottom:214.053829px;} .y7d1{bottom:214.062860px;} .y71e{bottom:214.065183px;} .y813{bottom:214.078858px;} .y7f4{bottom:214.142334px;} .y472{bottom:215.567313px;} .y4da{bottom:216.597891px;} .y413{bottom:216.627952px;} .y3f9{bottom:216.662786px;} .ye12{bottom:218.974233px;} .yfc7{bottom:219.032806px;} .yc3{bottom:219.184658px;} .y176{bottom:219.188141px;} .y22f{bottom:219.188528px;} .y9a{bottom:219.209042px;} .y101{bottom:219.219492px;} .y23b{bottom:219.234974px;} .y1a1{bottom:219.258068px;} .y1eb{bottom:219.258197px;} .y13d{bottom:219.261293px;} .y272{bottom:219.262067px;} .y3a1{bottom:219.277549px;} .y24d{bottom:219.304643px;} .y71{bottom:219.341412px;} .yc2{bottom:219.343734px;} .y1bf{bottom:219.374182px;} .y208{bottom:219.374311px;} .y291{bottom:219.378182px;} .y379{bottom:219.385922px;} .y226{bottom:219.490425px;} .y2cf{bottom:219.610410px;} .ye17{bottom:219.709623px;} .yc70{bottom:220.117029px;} .yc2c{bottom:220.259979px;} .yab9{bottom:220.450819px;} .yab3{bottom:220.463075px;} .yaad{bottom:220.475332px;} .ye7f{bottom:221.266586px;} .y68b{bottom:223.240269px;} .y667{bottom:223.397410px;} .yed3{bottom:223.446952px;} .y643{bottom:223.449404px;} .y7af{bottom:223.552616px;} .y78a{bottom:223.562034px;} .y6b0{bottom:223.567840px;} .y6d4{bottom:223.633638px;} .y6f8{bottom:223.699436px;} .yf3e{bottom:224.750915px;} .yd5c{bottom:224.889241px;} .ye5e{bottom:225.409540px;} .ye99{bottom:226.069198px;} .yeb6{bottom:226.734791px;} .y29{bottom:227.230703px;} .yc5f{bottom:227.797158px;} .yd8f{bottom:227.856755px;} .y619{bottom:228.015659px;} .y5f6{bottom:228.096939px;} .y5d3{bottom:228.178219px;} .y745{bottom:228.304526px;} .y7d0{bottom:228.311363px;} .y71d{bottom:228.313686px;} .y744{bottom:228.320524px;} .y812{bottom:228.327361px;} .y76b{bottom:228.338715px;} .y7f3{bottom:228.390837px;} .yc52{bottom:228.568673px;} .yc0d{bottom:229.678750px;} .y471{bottom:229.965475px;} .y4d9{bottom:231.054110px;} .y412{bottom:231.119005px;} .y3f8{bottom:231.153839px;} .yfc6{bottom:233.221962px;} .y534{bottom:233.286728px;} .yab8{bottom:234.643845px;} .yab2{bottom:234.656102px;} .y175{bottom:234.666552px;} .yaac{bottom:234.668358px;} .y99{bottom:234.687453px;} .y100{bottom:234.697903px;} .y23a{bottom:234.712998px;} .y1a0{bottom:234.736091px;} .y1ea{bottom:234.736221px;} .y13c{bottom:234.739704px;} .y271{bottom:234.740091px;} .y3a0{bottom:234.755573px;} .y5a1{bottom:234.770926px;} .y24c{bottom:234.782666px;} .y70{bottom:234.819823px;} .yc1{bottom:234.822145px;} .y1be{bottom:234.852206px;} .y207{bottom:234.852335px;} .y290{bottom:234.856205px;} .y378{bottom:234.863946px;} .y225{bottom:234.968449px;} .y2ce{bottom:235.088434px;} .yf3d{bottom:235.588241px;} .ye7e{bottom:236.748480px;} .y68a{bottom:237.091146px;} .y666{bottom:237.248287px;} .y642{bottom:237.300280px;} .y7ae{bottom:237.403106px;} .y789{bottom:237.412524px;} .y6af{bottom:237.418330px;} .y6d3{bottom:237.484128px;} .y6f7{bottom:237.549926px;} .yed2{bottom:238.928846px;} .yd5b{bottom:240.018257px;} .yc6f{bottom:240.799911px;} .ye5d{bottom:240.891435px;} .yc2b{bottom:240.942860px;} .ye98{bottom:241.551092px;} .yc46{bottom:241.714246px;} .ycdc{bottom:242.081476px;} .yeb5{bottom:242.216685px;} .ye3a{bottom:242.238617px;} .y618{bottom:242.262872px;} .y5f5{bottom:242.344152px;} .y5d1{bottom:242.425432px;} .y7cf{bottom:242.559867px;} .y71c{bottom:242.562189px;} .y743{bottom:242.569027px;} .y811{bottom:242.575865px;} .y76a{bottom:242.587218px;} .y7f2{bottom:242.639340px;} .yf4a{bottom:242.920724px;} .y5d2{bottom:243.482072px;} .yd8e{bottom:244.266966px;} .y470{bottom:244.363636px;} .y28{bottom:244.865984px;} .y411{bottom:245.610058px;} .y3f7{bottom:245.644892px;} .yb22{bottom:246.261218px;} .ydd8{bottom:246.907312px;} .yfc5{bottom:247.411118px;} .yc06{bottom:247.630316px;} .yc5e{bottom:248.480040px;} .yab7{bottom:248.836872px;} .yab1{bottom:248.849128px;} .yaab{bottom:248.861385px;} .yc51{bottom:249.251554px;} .ye11{bottom:249.938021px;} .y174{bottom:250.148446px;} .y98{bottom:250.165863px;} .yff{bottom:250.176314px;} .y19f{bottom:250.214115px;} .y1e9{bottom:250.214244px;} .y13b{bottom:250.218115px;} .y39f{bottom:250.233597px;} .y5a0{bottom:250.248949px;} .y24b{bottom:250.260690px;} .y6f{bottom:250.298233px;} .yc0{bottom:250.300556px;} .y3dc{bottom:250.304297px;} .y1bd{bottom:250.330229px;} .y206{bottom:250.330358px;} .y28f{bottom:250.334229px;} .y377{bottom:250.341970px;} .yc0c{bottom:250.361632px;} .y224{bottom:250.446473px;} .y2cd{bottom:250.566457px;} .y689{bottom:250.942022px;} .y665{bottom:251.099163px;} .y640{bottom:251.142513px;} .y641{bottom:251.146770px;} .y7ad{bottom:251.253595px;} .y788{bottom:251.263013px;} .y6ae{bottom:251.268819px;} .y6d2{bottom:251.334617px;} .y6f6{bottom:251.400415px;} .ye7d{bottom:252.230374px;} .yd5a{bottom:255.147272px;} .ye5c{bottom:256.373329px;} .y617{bottom:256.510085px;} .y5f4{bottom:256.591365px;} .y5d0{bottom:256.672645px;} .y7ce{bottom:256.808370px;} .y71b{bottom:256.810692px;} .y742{bottom:256.817530px;} .y810{bottom:256.824368px;} .yf15{bottom:256.827722px;} .y769{bottom:256.835721px;} .y7f1{bottom:256.887844px;} .ye97{bottom:257.032986px;} .yeb4{bottom:257.698579px;} .ye39{bottom:257.720511px;} .y46f{bottom:258.761798px;} .y4d8{bottom:259.978159px;} .y410{bottom:260.101111px;} .y3f6{bottom:260.135945px;} .yd8d{bottom:260.677177px;} .yc6e{bottom:261.482792px;} .yfc4{bottom:261.600274px;} .yc2a{bottom:261.625742px;} .yc45{bottom:262.397127px;} .yc22{bottom:262.408687px;} .y688{bottom:264.792899px;} .y664{bottom:264.950040px;} .y3e{bottom:264.984797px;} .y63f{bottom:264.993389px;} .y7ac{bottom:265.104085px;} .y787{bottom:265.113503px;} .y6ad{bottom:265.119309px;} .yd24{bottom:265.168602px;} .y6d1{bottom:265.185107px;} .y6f5{bottom:265.250905px;} .ye10{bottom:265.419915px;} .y97{bottom:265.644274px;} .yfe{bottom:265.654724px;} .y19e{bottom:265.692139px;} .y1e8{bottom:265.692268px;} .y13a{bottom:265.696525px;} .y39e{bottom:265.711620px;} .y59f{bottom:265.726973px;} .y24a{bottom:265.738713px;} .y6e{bottom:265.776644px;} .ybf{bottom:265.778966px;} .y1bc{bottom:265.808253px;} .y205{bottom:265.808382px;} .y376{bottom:265.819993px;} .y223{bottom:265.924496px;} .y2cc{bottom:266.044481px;} .y25b{bottom:266.295030px;} .yf14{bottom:267.665048px;} .yf16{bottom:267.872764px;} .y1b{bottom:268.690675px;} .yc5d{bottom:269.162921px;} .yed1{bottom:269.892635px;} .yc50{bottom:269.934436px;} .yd59{bottom:270.276287px;} .y616{bottom:270.757298px;} .y34b{bottom:270.772522px;} .y5f3{bottom:270.838578px;} .y5cf{bottom:270.919858px;} .ycde{bottom:270.958692px;} .yc0b{bottom:271.044513px;} .y7cd{bottom:271.056873px;} .y71a{bottom:271.059195px;} .y741{bottom:271.066033px;} .y80f{bottom:271.072871px;} .y768{bottom:271.084224px;} .y7f0{bottom:271.136347px;} .ydd7{bottom:272.710468px;} .y46e{bottom:273.159959px;} .y4d7{bottom:274.434377px;} .y40f{bottom:274.592164px;} .y3f5{bottom:274.626998px;} .yfc3{bottom:275.789430px;} .yd8c{bottom:277.087388px;} .yd23{bottom:278.069784px;} .y687{bottom:278.643775px;} .y663{bottom:278.800917px;} .y63d{bottom:278.818205px;} .y63e{bottom:278.839879px;} .yec6{bottom:278.953800px;} .y7ab{bottom:278.954574px;} .y786{bottom:278.963993px;} .y6ac{bottom:278.969798px;} .y6d0{bottom:279.035596px;} .y6f4{bottom:279.101394px;} .ye72{bottom:279.502375px;} .y96{bottom:281.122685px;} .yfd{bottom:281.133135px;} .y19d{bottom:281.170162px;} .y1e7{bottom:281.170291px;} .y139{bottom:281.174936px;} .y39d{bottom:281.189644px;} .y59e{bottom:281.204997px;} .y249{bottom:281.216737px;} .y6d{bottom:281.255055px;} .ybe{bottom:281.257377px;} .y1bb{bottom:281.286277px;} .y204{bottom:281.286406px;} .y375{bottom:281.298017px;} .y222{bottom:281.402520px;} .yb86{bottom:281.512570px;} .y2cb{bottom:281.522505px;} .yc6d{bottom:282.165674px;} .yf2f{bottom:282.286665px;} .yc29{bottom:282.308623px;} .yc44{bottom:283.080009px;} .ye8c{bottom:283.978191px;} .ya35{bottom:284.061077px;} .ye30{bottom:284.663652px;} .y615{bottom:285.004512px;} .y5f2{bottom:285.085791px;} .y5ce{bottom:285.167071px;} .y719{bottom:285.307699px;} .y740{bottom:285.314536px;} .y80e{bottom:285.321374px;} .y767{bottom:285.332728px;} .y7cc{bottom:285.348726px;} .yed0{bottom:285.374529px;} .y7ef{bottom:285.384850px;} .yd58{bottom:285.405303px;} .ye48{bottom:285.613208px;} .y25a{bottom:285.649977px;} .y46d{bottom:287.558121px;} .yf27{bottom:287.592052px;} .y8cc{bottom:288.822863px;} .y4d6{bottom:288.890596px;} .y40e{bottom:289.083217px;} .y3f4{bottom:289.118051px;} .y9b1{bottom:289.336583px;} .yf77{bottom:289.781192px;} .yc5c{bottom:289.845803px;} .yf96{bottom:289.862472px;} .yfc2{bottom:289.978586px;} .yc4f{bottom:290.617317px;} .yc02{bottom:291.727395px;} .y686{bottom:292.494652px;} .ydd5{bottom:292.621474px;} .y662{bottom:292.651793px;} .y63c{bottom:292.669081px;} .y7aa{bottom:292.805064px;} .y785{bottom:292.814482px;} .y6ab{bottom:292.820288px;} .y6cf{bottom:292.886086px;} .y6f3{bottom:292.951884px;} .yf2e{bottom:293.123991px;} .yd8b{bottom:293.497599px;} .y9d2{bottom:294.930735px;} .y95{bottom:296.601095px;} .yfc{bottom:296.611546px;} .y19c{bottom:296.648186px;} .y1e6{bottom:296.648315px;} .y138{bottom:296.653347px;} .y39c{bottom:296.667667px;} .y59d{bottom:296.683020px;} .y248{bottom:296.694761px;} .ybd3{bottom:296.704050px;} .y6c{bottom:296.733465px;} .ybd{bottom:296.735788px;} .y1ba{bottom:296.764300px;} .y203{bottom:296.764429px;} .y374{bottom:296.776041px;} .y221{bottom:296.880543px;} .y2ca{bottom:297.000528px;} .yf26{bottom:298.429378px;} .y614{bottom:299.251725px;} .y5f1{bottom:299.333005px;} .y5cd{bottom:299.414284px;} .y718{bottom:299.558524px;} .y73f{bottom:299.563040px;} .y80d{bottom:299.569878px;} .y766{bottom:299.581231px;} .y717{bottom:299.592713px;} .y7cb{bottom:299.597229px;} .y2dd{bottom:299.625096px;} .y7ee{bottom:299.633353px;} .y46c{bottom:301.956282px;} .yf38{bottom:302.206573px;} .yc6c{bottom:302.848556px;} .yc28{bottom:302.991505px;} .y4d5{bottom:303.346815px;} .y40d{bottom:303.574269px;} .y3f3{bottom:303.609104px;} .ydd6{bottom:303.671676px;} .yc1d{bottom:303.762890px;} .yf76{bottom:303.970348px;} .yf95{bottom:304.051628px;} .yfc1{bottom:304.167742px;} .yec5{bottom:304.756957px;} .y259{bottom:305.004925px;} .ye71{bottom:305.305532px;} .ya34{bottom:305.994995px;} .yd34{bottom:306.243262px;} .y685{bottom:306.345528px;} .y661{bottom:306.502670px;} .y63b{bottom:306.519958px;} .y7a9{bottom:306.655553px;} .y784{bottom:306.664972px;} .y6aa{bottom:306.670777px;} .y6ce{bottom:306.736575px;} .ya2a{bottom:306.737607px;} .y6f2{bottom:306.802373px;} .yedc{bottom:308.721741px;} .ye8b{bottom:309.781348px;} .yd8a{bottom:309.907811px;} .ye2f{bottom:310.466809px;} .yc5b{bottom:310.528685px;} .y9b0{bottom:311.270501px;} .yc4e{bottom:311.300199px;} .ye47{bottom:311.416365px;} .y94{bottom:312.079506px;} .yfb{bottom:312.089956px;} .y3d{bottom:312.105038px;} .y19b{bottom:312.126210px;} .y1e5{bottom:312.126339px;} .y137{bottom:312.131757px;} .y39b{bottom:312.145691px;} .y59c{bottom:312.161044px;} .y247{bottom:312.172784px;} .y6b{bottom:312.211876px;} .ybc{bottom:312.214198px;} .y304{bottom:312.219230px;} .y1b9{bottom:312.242324px;} .y202{bottom:312.242453px;} .y373{bottom:312.254064px;} .y220{bottom:312.358567px;} .yc01{bottom:312.410277px;} .y2c9{bottom:312.478552px;} .ycdd{bottom:312.821992px;} .y613{bottom:313.498938px;} .y5f0{bottom:313.580218px;} .y5cc{bottom:313.661498px;} .y73e{bottom:313.811543px;} .y80c{bottom:313.818381px;} .y765{bottom:313.829734px;} .y716{bottom:313.841217px;} .y7ca{bottom:313.845732px;} .y7ed{bottom:313.881856px;} .y1a{bottom:315.804145px;} .y46b{bottom:316.354444px;} .y4d4{bottom:317.803033px;} .yf0b{bottom:317.846124px;} .yd28{bottom:318.049978px;} .y3f2{bottom:318.100157px;} .y9d1{bottom:318.154884px;} .yf75{bottom:318.159504px;} .yf94{bottom:318.240784px;} .yfc0{bottom:318.356898px;} .ydd4{bottom:318.424631px;} .y8d0{bottom:318.794261px;} .y533{bottom:319.338966px;} .y684{bottom:320.196405px;} .y660{bottom:320.353546px;} .y63a{bottom:320.370834px;} .y7a8{bottom:320.506043px;} .y783{bottom:320.515461px;} .y6a9{bottom:320.521267px;} .y6cd{bottom:320.587065px;} .y6f1{bottom:320.652863px;} .y2dc{bottom:321.344387px;} .yce3{bottom:323.056298px;} .yc6b{bottom:323.531437px;} .yc27{bottom:323.674387px;} .y8f1{bottom:323.922755px;} .yf0a{bottom:324.075394px;} .y258{bottom:324.359873px;} .yc1c{bottom:324.445772px;} .y830{bottom:324.630476px;} .yf3f{bottom:326.179254px;} .yd89{bottom:326.318022px;} .yda1{bottom:326.818140px;} .yb4b{bottom:326.826624px;} .y93{bottom:327.557917px;} .yfa{bottom:327.568367px;} .y19a{bottom:327.604233px;} .y1e4{bottom:327.604362px;} .y136{bottom:327.610168px;} .y39a{bottom:327.623715px;} .y59b{bottom:327.639068px;} .y246{bottom:327.650808px;} .y6a{bottom:327.690287px;} .ybb{bottom:327.692609px;} .y303{bottom:327.697254px;} .y1b8{bottom:327.720348px;} .y201{bottom:327.720477px;} .y372{bottom:327.732088px;} .yda0{bottom:327.732475px;} .y612{bottom:327.746151px;} .y5ef{bottom:327.827431px;} .y21f{bottom:327.836591px;} .y5cb{bottom:327.908711px;} .y2c8{bottom:327.956575px;} .y73d{bottom:328.060046px;} .y80b{bottom:328.066884px;} .y764{bottom:328.078237px;} .y715{bottom:328.089720px;} .y7c9{bottom:328.094235px;} .y7ec{bottom:328.130360px;} .y50e{bottom:328.935934px;} .y52d{bottom:328.982380px;} .y4fa{bottom:329.040437px;} .yf25{bottom:329.189321px;} .y46a{bottom:330.752606px;} .y532{bottom:330.950387px;} .yd27{bottom:330.951161px;} .yc5a{bottom:331.211566px;} .y42f{bottom:331.639073px;} .yc4d{bottom:331.983081px;} .y4d3{bottom:332.259252px;} .yf74{bottom:332.348660px;} .yf93{bottom:332.429940px;} .yfbf{bottom:332.546054px;} .y40c{bottom:332.556375px;} .y3f1{bottom:332.591209px;} .y885{bottom:333.028406px;} .yc00{bottom:333.093158px;} .y683{bottom:334.047282px;} .y65f{bottom:334.204423px;} .y639{bottom:334.221711px;} .y7a7{bottom:334.356532px;} .y782{bottom:334.365951px;} .y6a8{bottom:334.371756px;} .y6cc{bottom:334.437554px;} .y6f0{bottom:334.503352px;} .yedb{bottom:334.524898px;} .y5ba{bottom:335.348148px;} .yec4{bottom:335.727970px;} .ye70{bottom:336.275642px;} .yad7{bottom:338.747982px;} .yb2b{bottom:338.758164px;} .yc97{bottom:339.129791px;} .y2db{bottom:339.406597px;} .yf24{bottom:340.026647px;} .yf09{bottom:340.637150px;} .y940{bottom:340.640117px;} .ye8a{bottom:340.750168px;} .yda2{bottom:341.198498px;} .ye2e{bottom:341.431371px;} .y611{bottom:341.993364px;} .y5ee{bottom:342.074644px;} .y5ca{bottom:342.155924px;} .y73c{bottom:342.310872px;} .y73b{bottom:342.313065px;} .y80a{bottom:342.315387px;} .y763{bottom:342.326741px;} .y714{bottom:342.338223px;} .y7c8{bottom:342.342738px;} .y7eb{bottom:342.378863px;} .ye46{bottom:342.384669px;} .yb8e{bottom:342.496654px;} .y92{bottom:343.039811px;} .yf9{bottom:343.046778px;} .y173{bottom:343.050261px;} .y199{bottom:343.082257px;} .y1e3{bottom:343.082386px;} .y135{bottom:343.088579px;} .y399{bottom:343.101738px;} .y59a{bottom:343.117091px;} .y69{bottom:343.168698px;} .yba{bottom:343.171020px;} .y302{bottom:343.175277px;} .y1b7{bottom:343.198371px;} .y200{bottom:343.198500px;} .y52c{bottom:343.206370px;} .y371{bottom:343.210112px;} .ybd2{bottom:343.241914px;} .y21e{bottom:343.314614px;} .y2c7{bottom:343.434599px;} .y349{bottom:343.488786px;} .y50d{bottom:343.844998px;} .y4f9{bottom:343.949501px;} .yc6a{bottom:344.214319px;} .yc26{bottom:344.357268px;} .yc1b{bottom:345.128654px;} .y469{bottom:345.150767px;} .y42e{bottom:345.828229px;} .yf73{bottom:346.537816px;} .yf92{bottom:346.619096px;} .y4d2{bottom:346.715470px;} .yfbe{bottom:346.735210px;} .y40b{bottom:347.047428px;} .y3f0{bottom:347.082262px;} .y8f0{bottom:347.146904px;} .y82f{bottom:347.854625px;} .y682{bottom:347.898158px;} .y65e{bottom:348.055299px;} .y638{bottom:348.072588px;} .y7a6{bottom:348.207022px;} .y781{bottom:348.216440px;} .y6a7{bottom:348.222246px;} .y6cb{bottom:348.288044px;} .y6ef{bottom:348.353842px;} .yce7{bottom:348.914682px;} .yd70{bottom:349.061934px;} .ydd3{bottom:349.386355px;} .yd57{bottom:350.623625px;} .yc87{bottom:351.022404px;} .yc59{bottom:351.894448px;} .yf2d{bottom:352.593817px;} .yc4c{bottom:352.665962px;} .yc89{bottom:352.814921px;} .yc0a{bottom:353.776040px;} .y3c{bottom:355.552871px;} .y610{bottom:356.240577px;} .y5ed{bottom:356.321857px;} .y5c9{bottom:356.403137px;} .y73a{bottom:356.561568px;} .y809{bottom:356.563890px;} .y762{bottom:356.575244px;} .y713{bottom:356.586726px;} .y7c7{bottom:356.591242px;} .y7ea{bottom:356.627366px;} .y3db{bottom:356.955840px;} .yf08{bottom:357.198906px;} .y52b{bottom:357.441972px;} .y2da{bottom:357.468807px;} .y884{bottom:357.542785px;} .ycc7{bottom:357.572278px;} .yf8{bottom:358.525188px;} .y172{bottom:358.528672px;} .y198{bottom:358.560281px;} .y1e2{bottom:358.560410px;} .y134{bottom:358.566989px;} .y398{bottom:358.579762px;} .y599{bottom:358.595115px;} .y68{bottom:358.647108px;} .yb9{bottom:358.649431px;} .y301{bottom:358.653301px;} .y1b6{bottom:358.676395px;} .y1ff{bottom:358.676524px;} .y370{bottom:358.688135px;} .y50c{bottom:358.754062px;} .y21d{bottom:358.792638px;} .y4f8{bottom:358.858565px;} .y2c6{bottom:358.912623px;} .y348{bottom:358.966809px;} .y18{bottom:359.275028px;} .yce2{bottom:359.505837px;} .y468{bottom:359.548929px;} .yb83{bottom:359.573184px;} .y42d{bottom:360.017385px;} .yf72{bottom:360.726972px;} .yf91{bottom:360.808252px;} .yfbd{bottom:360.924366px;} .y19{bottom:361.096322px;} .y4d1{bottom:361.171689px;} .y40a{bottom:361.538481px;} .y3ef{bottom:361.573315px;} .y681{bottom:361.749035px;} .y65d{bottom:361.906176px;} .y637{bottom:361.919078px;} .y7a5{bottom:362.057511px;} .y780{bottom:362.066930px;} .y6a6{bottom:362.072735px;} .y6ca{bottom:362.138533px;} .y6ee{bottom:362.204331px;} .yf2c{bottom:363.431143px;} .y93f{bottom:363.862958px;} .y93e{bottom:363.870311px;} .yb2a{bottom:364.086285px;} .yb29{bottom:364.091410px;} .ydac{bottom:364.607250px;} .yc69{bottom:364.897200px;} .yc25{bottom:365.040150px;} .yeda{bottom:365.496685px;} .yd56{bottom:365.752641px;} .yc43{bottom:365.811535px;} .yda3{bottom:365.997912px;} .yb8d{bottom:367.824775px;} .yb8c{bottom:367.831157px;} .ya83{bottom:370.174540px;} .y60f{bottom:370.487790px;} .y5ec{bottom:370.569070px;} .y5c8{bottom:370.650350px;} .y739{bottom:370.812394px;} .y761{bottom:370.823747px;} .y712{bottom:370.835229px;} .y738{bottom:370.837423px;} .y7c6{bottom:370.839745px;} .y7e9{bottom:370.875869px;} .yd2b{bottom:371.199828px;} .ybd1{bottom:371.617323px;} .y52a{bottom:371.665962px;} .yce6{bottom:372.236087px;} .yc58{bottom:372.577330px;} .y25c{bottom:372.926962px;} .yc4b{bottom:373.348844px;} .y50b{bottom:373.663126px;} .yf13{bottom:373.681189px;} .yf07{bottom:373.760662px;} .y4f7{bottom:373.767629px;} .y467{bottom:373.947090px;} .y91{bottom:374.003599px;} .y171{bottom:374.007082px;} .y197{bottom:374.038304px;} .y1e1{bottom:374.038433px;} .y133{bottom:374.045400px;} .y397{bottom:374.057786px;} .y598{bottom:374.073139px;} .y54f{bottom:374.104231px;} .y67{bottom:374.125519px;} .yb8{bottom:374.127841px;} .y300{bottom:374.131325px;} .y1b5{bottom:374.154418px;} .y1fe{bottom:374.154547px;} .y36f{bottom:374.166159px;} .y3ba{bottom:374.185511px;} .y42c{bottom:374.206541px;} .y56a{bottom:374.208734px;} .y57a{bottom:374.266791px;} .y21c{bottom:374.270662px;} .y2c5{bottom:374.390646px;} .y347{bottom:374.444833px;} .ybff{bottom:374.458922px;} .yf71{bottom:374.916128px;} .yf90{bottom:374.997408px;} .yfbc{bottom:375.113522px;} .yb5b{bottom:375.216992px;} .yf37{bottom:375.439803px;} .y680{bottom:375.599911px;} .y4d0{bottom:375.627908px;} .y65c{bottom:375.757053px;} .y635{bottom:375.761310px;} .y636{bottom:375.765697px;} .y7a4{bottom:375.908001px;} .y77f{bottom:375.917419px;} .y6a5{bottom:375.923225px;} .y6c9{bottom:375.989023px;} .y409{bottom:376.029534px;} .y6ed{bottom:376.054821px;} .y3ee{bottom:376.064368px;} .ya56{bottom:376.184353px;} .ya5f{bottom:376.219187px;} .yccf{bottom:378.624170px;} .yf11{bottom:379.912651px;} .yd55{bottom:380.881656px;} .yf12{bottom:384.518514px;} .y60e{bottom:384.735003px;} .y5eb{bottom:384.816283px;} .y5c7{bottom:384.897563px;} .y808{bottom:385.063219px;} .y807{bottom:385.070057px;} .y760{bottom:385.072250px;} .y711{bottom:385.083733px;} .y737{bottom:385.085926px;} .y7c5{bottom:385.088248px;} .y7e8{bottom:385.124373px;} .ydf7{bottom:385.565607px;} .yc68{bottom:385.580082px;} .y853{bottom:385.639146px;} .y85e{bottom:385.662368px;} .yc24{bottom:385.723032px;} .yce4{bottom:385.837572px;} .y529{bottom:385.889952px;} .yf36{bottom:386.277129px;} .yc1a{bottom:386.494417px;} .ydb5{bottom:387.843638px;} .y466{bottom:388.345252px;} .y42b{bottom:388.395697px;} .y50a{bottom:388.572190px;} .y4f6{bottom:388.676693px;} .yd88{bottom:388.755877px;} .yf70{bottom:389.105284px;} .yf8f{bottom:389.186564px;} .yfbb{bottom:389.302678px;} .y98f{bottom:389.381764px;} .y997{bottom:389.386925px;} .yb5a{bottom:389.406148px;} .y67f{bottom:389.450788px;} .y90{bottom:389.485493px;} .y196{bottom:389.516328px;} .y1e0{bottom:389.516457px;} .y132{bottom:389.523811px;} .y396{bottom:389.535809px;} .y8f{bottom:389.544711px;} .y597{bottom:389.551162px;} .y54e{bottom:389.582255px;} .y66{bottom:389.603930px;} .yb7{bottom:389.606252px;} .y65b{bottom:389.607929px;} .y2ff{bottom:389.609348px;} .y634{bottom:389.612187px;} .yf7{bottom:389.624830px;} .y1b4{bottom:389.632442px;} .y1fd{bottom:389.632571px;} .y36e{bottom:389.644183px;} .y3b9{bottom:389.663535px;} .y569{bottom:389.686758px;} .y579{bottom:389.744815px;} .y21b{bottom:389.748685px;} .y7a3{bottom:389.758491px;} .y77e{bottom:389.767909px;} .y6a4{bottom:389.773714px;} .y6c8{bottom:389.839512px;} .y2c4{bottom:389.868670px;} .y6ec{bottom:389.905310px;} .y346{bottom:389.922857px;} .y49a{bottom:390.060904px;} .y4b5{bottom:390.072515px;} .y4cf{bottom:390.084126px;} .yccb{bottom:390.123863px;} .yf06{bottom:390.322419px;} .y408{bottom:390.520587px;} .y3ed{bottom:390.555421px;} .yf49{bottom:390.714756px;} .yf10{bottom:390.749977px;} .ya55{bottom:391.662376px;} .ya5e{bottom:391.697211px;} .ya81{bottom:392.098447px;} .ya82{bottom:392.107223px;} .y910{bottom:394.788429px;} .y918{bottom:394.811652px;} .ybfe{bottom:395.141803px;} .yce5{bottom:395.557492px;} .yd54{bottom:396.010671px;} .yb23{bottom:397.904127px;} .y60d{bottom:398.982216px;} .y3b{bottom:399.000704px;} .y5ea{bottom:399.063496px;} .y5c6{bottom:399.144776px;} .y806{bottom:399.318560px;} .y75f{bottom:399.320753px;} .y710{bottom:399.332236px;} .y736{bottom:399.334429px;} .y7c4{bottom:399.336751px;} .y7e7{bottom:399.372876px;} .ydf6{bottom:399.754762px;} .y852{bottom:399.828301px;} .y85d{bottom:399.851524px;} .y528{bottom:400.125554px;} .yf48{bottom:401.552081px;} .yba1{bottom:401.587948px;} .yba6{bottom:401.599559px;} .ybab{bottom:401.611171px;} .yf3c{bottom:402.049566px;} .y899{bottom:402.438420px;} .y8a0{bottom:402.461643px;} .y42a{bottom:402.584853px;} .y465{bottom:402.743413px;} .y17{bottom:402.745911px;} .yf6f{bottom:403.294440px;} .y67e{bottom:403.301664px;} .ydb4{bottom:403.321662px;} .yf8e{bottom:403.375719px;} .y632{bottom:403.454419px;} .y633{bottom:403.458806px;} .y509{bottom:403.481254px;} .yfba{bottom:403.491834px;} .y98e{bottom:403.573501px;} .y996{bottom:403.576081px;} .y4f5{bottom:403.585757px;} .y98d{bottom:403.586402px;} .y99d{bottom:403.587692px;} .yb59{bottom:403.595304px;} .y7a2{bottom:403.608980px;} .y77d{bottom:403.618398px;} .y6a3{bottom:403.624204px;} .yaf1{bottom:403.680343px;} .y6c7{bottom:403.690002px;} .yaec{bottom:403.693064px;} .y6eb{bottom:403.755800px;} .y499{bottom:404.517122px;} .y4b4{bottom:404.528734px;} .y4ce{bottom:404.540345px;} .y170{bottom:404.967387px;} .y195{bottom:404.994352px;} .y1df{bottom:404.994481px;} .y131{bottom:405.002221px;} .y16f{bottom:405.009188px;} .y407{bottom:405.011640px;} .y395{bottom:405.013833px;} .y8e{bottom:405.023122px;} .y596{bottom:405.029186px;} .y270{bottom:405.033185px;} .y3ec{bottom:405.046474px;} .y54d{bottom:405.060279px;} .y65{bottom:405.082340px;} .yb6{bottom:405.084663px;} .y2fe{bottom:405.087372px;} .yf6{bottom:405.103241px;} .y1b3{bottom:405.110466px;} .y1fc{bottom:405.110595px;} .y36d{bottom:405.122206px;} .y3b8{bottom:405.141559px;} .y28e{bottom:405.149299px;} .y568{bottom:405.164781px;} .y578{bottom:405.222838px;} .y21a{bottom:405.226709px;} .y3d0{bottom:405.234450px;} .y2c3{bottom:405.346694px;} .y345{bottom:405.400880px;} .ybf1{bottom:405.790637px;} .yc67{bottom:406.262964px;} .yc23{bottom:406.405913px;} .y9ef{bottom:406.762126px;} .y9f6{bottom:406.773737px;} .y9fd{bottom:406.785349px;} .yf05{bottom:406.877982px;} .ya54{bottom:407.140400px;} .yd87{bottom:407.142401px;} .ya5d{bottom:407.175234px;} .yc19{bottom:407.177299px;} .ya66{bottom:407.210069px;} .y95f{bottom:408.590667px;} .y966{bottom:408.602278px;} .ycd6{bottom:408.891273px;} .y90f{bottom:408.977585px;} .y917{bottom:409.000808px;} .yc64{bottom:409.667561px;} .y480{bottom:409.743810px;} .yc55{bottom:410.439076px;} .yda9{bottom:410.611054px;} .yd53{bottom:411.139687px;} .y60c{bottom:413.229429px;} .y5e9{bottom:413.310709px;} .y5c5{bottom:413.391989px;} .y805{bottom:413.567063px;} .y75e{bottom:413.569257px;} .y70f{bottom:413.580739px;} .y735{bottom:413.582932px;} .y7c3{bottom:413.585255px;} .y7e6{bottom:413.621379px;} .y851{bottom:414.017457px;} .ya80{bottom:414.032365px;} .y85c{bottom:414.040680px;} .y867{bottom:414.063903px;} .y527{bottom:414.349544px;} .yba0{bottom:415.777104px;} .yba5{bottom:415.788715px;} .ybaa{bottom:415.800327px;} .y429{bottom:416.774009px;} .y464{bottom:417.141575px;} .y67d{bottom:417.152541px;} .y65a{bottom:417.270590px;} .y631{bottom:417.305296px;} .y7a1{bottom:417.459470px;} .y77c{bottom:417.468888px;} .y6a2{bottom:417.474693px;} .yf6e{bottom:417.483596px;} .y6c6{bottom:417.540491px;} .yf8d{bottom:417.564875px;} .y6ea{bottom:417.606290px;} .yfb9{bottom:417.680990px;} .y995{bottom:417.765237px;} .y98c{bottom:417.775558px;} .y99c{bottom:417.776848px;} .yb58{bottom:417.784460px;} .y898{bottom:417.916443px;} .y89f{bottom:417.939666px;} .y8a6{bottom:417.962889px;} .ye0f{bottom:418.097195px;} .y508{bottom:418.390318px;} .y4f4{bottom:418.494821px;} .ydb3{bottom:418.799686px;} .y498{bottom:418.973341px;} .y4b3{bottom:418.984952px;} .y4cd{bottom:418.996564px;} .y406{bottom:419.502693px;} .y3eb{bottom:419.537527px;} .yaf5{bottom:420.026275px;} .yaf0{bottom:420.038995px;} .yaeb{bottom:420.051716px;} .y194{bottom:420.472375px;} .y1de{bottom:420.472504px;} .y130{bottom:420.480632px;} .y16e{bottom:420.487599px;} .y394{bottom:420.491857px;} .y8d{bottom:420.501533px;} .y595{bottom:420.507209px;} .y26f{bottom:420.511209px;} .y54c{bottom:420.538302px;} .y64{bottom:420.560751px;} .yb5{bottom:420.563073px;} .y2fd{bottom:420.565396px;} .yf5{bottom:420.581652px;} .y1b2{bottom:420.588489px;} .y1fb{bottom:420.588618px;} .y36c{bottom:420.600230px;} .y3b7{bottom:420.619582px;} .y28d{bottom:420.627323px;} .y567{bottom:420.642805px;} .y577{bottom:420.700862px;} .y219{bottom:420.704733px;} .ydfb{bottom:420.710538px;} .y3cf{bottom:420.712474px;} .y2c2{bottom:420.824717px;} .y344{bottom:420.878904px;} .y9ee{bottom:420.951282px;} .y9f5{bottom:420.962893px;} .y9fc{bottom:420.974505px;} .ya53{bottom:422.618424px;} .ya5c{bottom:422.653258px;} .ya65{bottom:422.688092px;} .y95e{bottom:422.779822px;} .y965{bottom:422.791434px;} .y96c{bottom:422.803045px;} .yd26{bottom:423.029993px;} .y90e{bottom:423.166741px;} .y916{bottom:423.189964px;} .y91e{bottom:423.213186px;} .yd6f{bottom:424.904315px;} .yd52{bottom:426.268702px;} .y60b{bottom:427.476642px;} .y5e8{bottom:427.557922px;} .y5c4{bottom:427.639202px;} .y804{bottom:427.815567px;} .y75d{bottom:427.817760px;} .y70e{bottom:427.829242px;} .y734{bottom:427.831436px;} .y7c2{bottom:427.833758px;} .y7e5{bottom:427.869882px;} .y850{bottom:428.206613px;} .y85b{bottom:428.229836px;} .y866{bottom:428.253059px;} .y526{bottom:428.573534px;} .y386{bottom:428.586952px;} .yb9f{bottom:429.966260px;} .yba4{bottom:429.977871px;} .yba9{bottom:429.989483px;} .ycc1{bottom:430.595986px;} .y428{bottom:430.963165px;} .y67c{bottom:431.003418px;} .y659{bottom:431.121467px;} .y630{bottom:431.151915px;} .y7a0{bottom:431.309959px;} .y77b{bottom:431.319377px;} .y6a1{bottom:431.325183px;} .y6c5{bottom:431.390981px;} .y6e9{bottom:431.456779px;} .y463{bottom:431.539736px;} .yf6d{bottom:431.672751px;} .yf8c{bottom:431.754031px;} .yfb8{bottom:431.870146px;} .ycc9{bottom:431.952200px;} .y994{bottom:431.956973px;} .y993{bottom:431.960844px;} .y98b{bottom:431.964714px;} .y99b{bottom:431.966004px;} .yb57{bottom:431.973616px;} .yc05{bottom:432.232035px;} .y507{bottom:433.299382px;} .y897{bottom:433.394467px;} .y4f3{bottom:433.403885px;} .y89e{bottom:433.417690px;} .y8a5{bottom:433.440913px;} .y4b2{bottom:433.441171px;} .y4cc{bottom:433.452782px;} .ye0e{bottom:433.579089px;} .y405{bottom:433.993745px;} .y3ea{bottom:434.028580px;} .ydb1{bottom:434.277709px;} .y9ed{bottom:435.140438px;} .y9f4{bottom:435.152049px;} .y9fb{bottom:435.163661px;} .ydb2{bottom:435.334348px;} .yd25{bottom:435.931175px;} .y193{bottom:435.950399px;} .y1dd{bottom:435.950528px;} .y12f{bottom:435.959043px;} .y16d{bottom:435.966010px;} .y393{bottom:435.969880px;} .y8c{bottom:435.979943px;} .y594{bottom:435.985233px;} .y26e{bottom:435.989233px;} .y54b{bottom:436.016326px;} .y63{bottom:436.039162px;} .yb4{bottom:436.041484px;} .y2fc{bottom:436.043419px;} .yf4{bottom:436.060062px;} .y1b1{bottom:436.066513px;} .y1fa{bottom:436.066642px;} .y36b{bottom:436.078253px;} .y3b6{bottom:436.097606px;} .y28c{bottom:436.105347px;} .y566{bottom:436.120829px;} .ye66{bottom:436.139149px;} .y576{bottom:436.178886px;} .y218{bottom:436.182756px;} .y3ce{bottom:436.190497px;} .y2c1{bottom:436.302741px;} .y343{bottom:436.356928px;} .yaf4{bottom:436.384927px;} .yaef{bottom:436.397647px;} .yaea{bottom:436.410368px;} .y95d{bottom:436.968978px;} .y964{bottom:436.980590px;} .y96b{bottom:436.992201px;} .y90d{bottom:437.355897px;} .y915{bottom:437.379120px;} .y91d{bottom:437.402342px;} .y27{bottom:437.866493px;} .ya52{bottom:438.096447px;} .ya5b{bottom:438.131282px;} .ya64{bottom:438.166116px;} .ya2c{bottom:438.620122px;} .yf04{bottom:439.988531px;} .ycfa{bottom:440.900218px;} .yd51{bottom:441.397717px;} .y60a{bottom:441.723855px;} .y5e7{bottom:441.805135px;} .y5c3{bottom:441.886415px;} .y75c{bottom:442.066263px;} .y70d{bottom:442.077745px;} .y733{bottom:442.079939px;} .y7c1{bottom:442.082261px;} .y803{bottom:442.095679px;} .y7e4{bottom:442.118385px;} .yeb3{bottom:442.139544px;} .y84f{bottom:442.395769px;} .y85a{bottom:442.418992px;} .y865{bottom:442.442215px;} .y525{bottom:442.809136px;} .yc73{bottom:443.353325px;} .yc2f{bottom:443.496145px;} .yb9e{bottom:444.155416px;} .yba3{bottom:444.167027px;} .yba8{bottom:444.178638px;} .yc20{bottom:444.267530px;} .y67b{bottom:444.854294px;} .y62e{bottom:444.968086px;} .y658{bottom:444.972344px;} .ycf4{bottom:444.984342px;} .y62f{bottom:444.998405px;} .y427{bottom:445.152321px;} .y79f{bottom:445.162255px;} .y77a{bottom:445.169867px;} .y6a0{bottom:445.175672px;} .y79e{bottom:445.235665px;} .y6c4{bottom:445.241471px;} .y6e8{bottom:445.307269px;} .yf6c{bottom:445.861907px;} .y462{bottom:445.937898px;} .yf8b{bottom:445.943187px;} .yc63{bottom:445.953251px;} .yfb7{bottom:446.059302px;} .y992{bottom:446.150000px;} .y98a{bottom:446.153870px;} .y99a{bottom:446.155160px;} .yb56{bottom:446.162772px;} .yc54{bottom:446.724765px;} .y497{bottom:447.885778px;} .y4b1{bottom:447.897389px;} .y4cb{bottom:447.909001px;} .y506{bottom:448.208447px;} .y4f2{bottom:448.312949px;} .y896{bottom:448.872491px;} .y89d{bottom:448.895714px;} .y8a4{bottom:448.918936px;} .ye0d{bottom:449.060983px;} .y9ec{bottom:449.329594px;} .y9f3{bottom:449.341205px;} .y9fa{bottom:449.352817px;} .ydaf{bottom:449.755733px;} .ybf0{bottom:450.004733px;} .ydb0{bottom:450.812372px;} .y95c{bottom:451.158134px;} .y963{bottom:451.169746px;} .y96a{bottom:451.181357px;} .y192{bottom:451.428422px;} .y1dc{bottom:451.428551px;} .y12e{bottom:451.437454px;} .y16c{bottom:451.444420px;} .y392{bottom:451.447904px;} .y8b{bottom:451.458354px;} .y593{bottom:451.463257px;} .y26d{bottom:451.467256px;} .y54a{bottom:451.494350px;} .y62{bottom:451.517572px;} .yb3{bottom:451.519895px;} .y2fb{bottom:451.521443px;} .yf3{bottom:451.538473px;} .y1b0{bottom:451.544537px;} .y1f9{bottom:451.544666px;} .y90c{bottom:451.545053px;} .y36a{bottom:451.556277px;} .y914{bottom:451.568276px;} .y3b5{bottom:451.575629px;} .y28b{bottom:451.583370px;} .y91c{bottom:451.591498px;} .y565{bottom:451.598852px;} .y575{bottom:451.656909px;} .y217{bottom:451.660780px;} .y3cd{bottom:451.668521px;} .y2c0{bottom:451.780765px;} .y342{bottom:451.834951px;} .ye5b{bottom:452.722451px;} .yaf3{bottom:452.743579px;} .yaee{bottom:452.756299px;} .yae9{bottom:452.769020px;} .ycd4{bottom:453.056602px;} .ya51{bottom:453.574471px;} .ya5a{bottom:453.609305px;} .ya63{bottom:453.644140px;} .yf03{bottom:454.663137px;} .ycf9{bottom:455.093245px;} .y26{bottom:455.501773px;} .y609{bottom:455.971068px;} .y5e6{bottom:456.052348px;} .y5c2{bottom:456.133628px;} .y75b{bottom:456.317089px;} .y75a{bottom:456.321604px;} .y70c{bottom:456.326249px;} .y732{bottom:456.328442px;} .y7c0{bottom:456.330764px;} .y802{bottom:456.344182px;} .y7e3{bottom:456.366889px;} .ybd0{bottom:456.464941px;} .yd50{bottom:456.526732px;} .y84e{bottom:456.584925px;} .y859{bottom:456.608148px;} .y864{bottom:456.631371px;} .y524{bottom:457.033126px;} .yeb2{bottom:457.621438px;} .y438{bottom:457.863085px;} .ya28{bottom:457.960105px;} .yb9d{bottom:458.344572px;} .yba2{bottom:458.356183px;} .yba7{bottom:458.367794px;} .yb81{bottom:458.455525px;} .y67a{bottom:458.705171px;} .yaaa{bottom:458.723612px;} .yaa3{bottom:458.749053px;} .ya9c{bottom:458.774494px;} .y62d{bottom:458.818963px;} .y657{bottom:458.823220px;} .y779{bottom:459.020356px;} .y69f{bottom:459.026162px;} .y79d{bottom:459.086154px;} .y6c3{bottom:459.091960px;} .y6e7{bottom:459.157758px;} .ycf3{bottom:459.177368px;} .y426{bottom:459.341477px;} .ydf5{bottom:459.518744px;} .yf6b{bottom:460.051063px;} .yf8a{bottom:460.132343px;} .yfb6{bottom:460.248458px;} .y461{bottom:460.336059px;} .y991{bottom:460.339156px;} .y989{bottom:460.343026px;} .y999{bottom:460.344316px;} .yb55{bottom:460.351928px;} .ye38{bottom:461.488041px;} .y496{bottom:462.341997px;} .y4b0{bottom:462.353608px;} .y4ca{bottom:462.365219px;} .y505{bottom:463.117511px;} .y4f1{bottom:463.222013px;} .y9eb{bottom:463.518750px;} .y9f2{bottom:463.530361px;} .y9f9{bottom:463.541972px;} .ycc5{bottom:464.047456px;} .y895{bottom:464.350514px;} .y89c{bottom:464.373737px;} .y8a3{bottom:464.396960px;} .ye0c{bottom:464.542877px;} .yd86{bottom:464.714437px;} .ydad{bottom:465.233756px;} .y95b{bottom:465.347290px;} .y962{bottom:465.358902px;} .y969{bottom:465.370513px;} .y90b{bottom:465.734209px;} .y913{bottom:465.757432px;} .y91b{bottom:465.780654px;} .ydae{bottom:466.290396px;} .y191{bottom:466.906446px;} .y1db{bottom:466.906575px;} .y12d{bottom:466.915864px;} .y16b{bottom:466.922831px;} .y8a{bottom:466.936765px;} .y592{bottom:466.941280px;} .y26c{bottom:466.945280px;} .y549{bottom:466.972373px;} .y61{bottom:466.995983px;} .yb2{bottom:466.998305px;} .y2fa{bottom:466.999466px;} .yf2{bottom:467.016884px;} .y1af{bottom:467.022560px;} .y1f8{bottom:467.022689px;} .y369{bottom:467.034301px;} .y28a{bottom:467.061394px;} .y564{bottom:467.076876px;} .y574{bottom:467.134933px;} .y216{bottom:467.138804px;} .y3cc{bottom:467.146544px;} .y2bf{bottom:467.258788px;} .y341{bottom:467.312975px;} .yb3d{bottom:468.128871px;} .ye5a{bottom:468.204345px;} .yc04{bottom:468.517724px;} .ya50{bottom:469.052495px;} .ya59{bottom:469.087329px;} .yaf2{bottom:469.102231px;} .yaed{bottom:469.114951px;} .ya62{bottom:469.122163px;} .yae8{bottom:469.127672px;} .ycf8{bottom:469.286271px;} .yf02{bottom:469.337743px;} .yd94{bottom:470.101006px;} .y608{bottom:470.218281px;} .y5e5{bottom:470.299561px;} .y5c1{bottom:470.380841px;} .y759{bottom:470.570107px;} .y70b{bottom:470.574752px;} .y731{bottom:470.576945px;} .y7bf{bottom:470.579267px;} .y801{bottom:470.592685px;} .y7e2{bottom:470.615392px;} .ye7c{bottom:470.692801px;} .y84d{bottom:470.774081px;} .y858{bottom:470.797304px;} .y863{bottom:470.820527px;} .y523{bottom:471.268728px;} .yd4f{bottom:471.655748px;} .yb09{bottom:472.094687px;} .y679{bottom:472.556047px;} .y62c{bottom:472.669839px;} .y656{bottom:472.674097px;} .y778{bottom:472.870846px;} .y69e{bottom:472.876652px;} .y79c{bottom:472.936644px;} .y6c2{bottom:472.942450px;} .y6e6{bottom:473.008248px;} .yeb1{bottom:473.103332px;} .y25{bottom:473.137054px;} .ycf2{bottom:473.370395px;} .y425{bottom:473.530633px;} .ydf4{bottom:473.626620px;} .yf6a{bottom:474.240219px;} .yf89{bottom:474.321499px;} .yfb5{bottom:474.437613px;} .y990{bottom:474.528312px;} .y988{bottom:474.532182px;} .y998{bottom:474.533472px;} .yb54{bottom:474.541084px;} .yd22{bottom:474.653715px;} .y460{bottom:474.734221px;} .yaa9{bottom:475.082264px;} .yaa2{bottom:475.107705px;} .ya9b{bottom:475.133146px;} .yb80{bottom:476.517735px;} .y495{bottom:476.798215px;} .y4af{bottom:476.809827px;} .y4c9{bottom:476.821438px;} .ye37{bottom:476.969935px;} .y437{bottom:477.218033px;} .y9ea{bottom:477.707906px;} .y9f1{bottom:477.719517px;} .y9f8{bottom:477.731128px;} .y504{bottom:478.026575px;} .y4f0{bottom:478.131077px;} .yc9f{bottom:479.255966px;} .y95a{bottom:479.536446px;} .y961{bottom:479.548058px;} .y968{bottom:479.559669px;} .yc72{bottom:479.639014px;} .yc2e{bottom:479.781834px;} .y894{bottom:479.828538px;} .y89b{bottom:479.851761px;} .y8a2{bottom:479.874984px;} .y90a{bottom:479.923365px;} .y912{bottom:479.946587px;} .y91a{bottom:479.969810px;} .ye0b{bottom:480.024771px;} .yc1f{bottom:480.553220px;} .ycb5{bottom:480.986713px;} .ye96{bottom:481.068896px;} .yd85{bottom:481.124649px;} .yca4{bottom:481.809446px;} .yb3c{bottom:482.318027px;} .y190{bottom:482.384470px;} .y1da{bottom:482.384599px;} .y12c{bottom:482.394275px;} .y16a{bottom:482.401242px;} .y89{bottom:482.415175px;} .y591{bottom:482.419304px;} .y26b{bottom:482.423303px;} .y548{bottom:482.450397px;} .y60{bottom:482.474394px;} .yb1{bottom:482.476716px;} .y2f9{bottom:482.477490px;} .yf1{bottom:482.495294px;} .y1ae{bottom:482.500584px;} .y1f7{bottom:482.500713px;} .y368{bottom:482.512324px;} .y289{bottom:482.539418px;} .y563{bottom:482.554900px;} .y573{bottom:482.612957px;} .y215{bottom:482.616827px;} .y3cb{bottom:482.624568px;} .y2be{bottom:482.736812px;} .y340{bottom:482.790998px;} .ybce{bottom:483.101927px;} .ye59{bottom:483.686239px;} .yf01{bottom:484.012350px;} .ya2b{bottom:484.420210px;} .y607{bottom:484.465494px;} .ya4f{bottom:484.530518px;} .y5e4{bottom:484.546774px;} .ya58{bottom:484.565353px;} .ya61{bottom:484.600187px;} .y5c0{bottom:484.628054px;} .y758{bottom:484.818611px;} .y70a{bottom:484.823255px;} .y730{bottom:484.825448px;} .y7be{bottom:484.827771px;} .y800{bottom:484.841188px;} .y7e1{bottom:484.863895px;} .y84c{bottom:484.963237px;} .y857{bottom:484.986460px;} .y862{bottom:485.009683px;} .y522{bottom:485.492718px;} .ye7b{bottom:486.174695px;} .y678{bottom:486.406924px;} .y62b{bottom:486.520716px;} .y655{bottom:486.524973px;} .y777{bottom:486.721335px;} .y69d{bottom:486.727141px;} .yd4e{bottom:486.784763px;} .y79b{bottom:486.787133px;} .y6c1{bottom:486.792939px;} .y6e5{bottom:486.858737px;} .yca8{bottom:487.194694px;} .yecf{bottom:487.413247px;} .ycf1{bottom:487.563421px;} .y424{bottom:487.719788px;} .ydf3{bottom:487.734496px;} .ydb6{bottom:488.301779px;} .yf69{bottom:488.429375px;} .yf88{bottom:488.510655px;} .yeb0{bottom:488.585226px;} .yfb4{bottom:488.626769px;} .y45f{bottom:489.132382px;} .ycf7{bottom:489.354676px;} .yc62{bottom:489.496078px;} .yc53{bottom:490.267592px;} .y3d8{bottom:490.373643px;} .y24{bottom:490.772334px;} .y494{bottom:491.254434px;} .y4ae{bottom:491.266045px;} .y4c8{bottom:491.277657px;} .yaa8{bottom:491.440916px;} .yb08{bottom:491.443829px;} .yaa1{bottom:491.466357px;} .ya9a{bottom:491.491798px;} .y9e9{bottom:491.897062px;} .y9f0{bottom:491.908673px;} .y9f7{bottom:491.920284px;} .ydaa{bottom:492.396353px;} .ye36{bottom:492.451829px;} .y503{bottom:492.935639px;} .y4ef{bottom:493.040141px;} .yf23{bottom:493.076782px;} .y959{bottom:493.725602px;} .y960{bottom:493.737214px;} .y967{bottom:493.748825px;} .y909{bottom:494.112521px;} .y911{bottom:494.135743px;} .y919{bottom:494.158966px;} .yd1d{bottom:494.249148px;} .ycfb{bottom:494.400742px;} .yb7f{bottom:494.579945px;} .y893{bottom:495.306562px;} .y89a{bottom:495.329785px;} .y8a1{bottom:495.353007px;} .ye0a{bottom:495.506665px;} .ycac{bottom:495.953705px;} .yb3b{bottom:496.507183px;} .ye95{bottom:496.550790px;} .y436{bottom:496.572981px;} .yd84{bottom:497.534860px;} .y18f{bottom:497.862493px;} .y1d9{bottom:497.862622px;} .y12b{bottom:497.872686px;} .y169{bottom:497.879652px;} .y88{bottom:497.893586px;} .y590{bottom:497.897328px;} .y26a{bottom:497.901327px;} .y547{bottom:497.928420px;} .y5f{bottom:497.952804px;} .yb0{bottom:497.955127px;} .y2f8{bottom:497.955514px;} .yf0{bottom:497.973705px;} .y1ad{bottom:497.978608px;} .y1f6{bottom:497.978737px;} .y367{bottom:497.990348px;} .y288{bottom:498.017441px;} .y562{bottom:498.032923px;} .y572{bottom:498.090980px;} .y214{bottom:498.094851px;} .y3ca{bottom:498.102592px;} .y2bd{bottom:498.214835px;} .y33f{bottom:498.269022px;} .yf00{bottom:498.686956px;} .y606{bottom:498.712707px;} .y5e3{bottom:498.793987px;} .y5bf{bottom:498.875267px;} .y757{bottom:499.069436px;} .y709{bottom:499.071758px;} .y72f{bottom:499.073952px;} .y7bd{bottom:499.076274px;} .y756{bottom:499.082854px;} .y7ff{bottom:499.089692px;} .y7e0{bottom:499.112398px;} .y84b{bottom:499.152393px;} .ye58{bottom:499.168133px;} .y856{bottom:499.175616px;} .y861{bottom:499.198839px;} .y521{bottom:499.716708px;} .ya4e{bottom:500.008542px;} .ya57{bottom:500.043376px;} .ya60{bottom:500.078210px;} .y677{bottom:500.257800px;} .ycd3{bottom:500.289280px;} .y62a{bottom:500.371592px;} .y654{bottom:500.375850px;} .y776{bottom:500.571825px;} .y69c{bottom:500.577631px;} .y79a{bottom:500.637623px;} .y6c0{bottom:500.643429px;} .y6e4{bottom:500.709227px;} .ye7a{bottom:501.656590px;} .y423{bottom:501.908944px;} .yf68{bottom:502.618531px;} .yf87{bottom:502.699811px;} .yfb3{bottom:502.815925px;} .yece{bottom:502.895141px;} .y45e{bottom:503.530544px;} .yf22{bottom:503.914108px;} .yeaf{bottom:504.067120px;} .ydfa{bottom:504.454684px;} .y493{bottom:505.710653px;} .y4ad{bottom:505.722264px;} .y4c7{bottom:505.733875px;} .ycc3{bottom:507.214073px;} .ycec{bottom:507.634278px;} .yced{bottom:507.640471px;} .yaa7{bottom:507.799568px;} .yaa0{bottom:507.825009px;} .y502{bottom:507.844703px;} .ya99{bottom:507.850450px;} .ye35{bottom:507.933724px;} .y4ee{bottom:507.949205px;} .yc9e{bottom:508.163114px;} .y23{bottom:508.407615px;} .ycb3{bottom:508.834512px;} .ybcd{bottom:508.900245px;} .yd33{bottom:509.615927px;} .yc99{bottom:509.746328px;} .yb3a{bottom:510.696339px;} .yca2{bottom:510.724593px;} .yca1{bottom:510.734637px;} .yb07{bottom:510.792971px;} .ye09{bottom:510.988559px;} .yd1c{bottom:511.023781px;} .ybcf{bottom:511.395088px;} .ye94{bottom:512.032684px;} .yc03{bottom:512.060551px;} .y3d7{bottom:512.089193px;} .yb7e{bottom:512.642155px;} .y605{bottom:512.959920px;} .ycf6{bottom:513.021848px;} .y5e2{bottom:513.041200px;} .y5be{bottom:513.122480px;} .ybef{bottom:513.127125px;} .y708{bottom:513.320262px;} .y72e{bottom:513.322455px;} .y7bc{bottom:513.324777px;} .y755{bottom:513.331357px;} .y7fe{bottom:513.338195px;} .y18e{bottom:513.340517px;} .y1d8{bottom:513.340646px;} .y84a{bottom:513.341549px;} .y12a{bottom:513.351096px;} .y168{bottom:513.358063px;} .y7df{bottom:513.360901px;} .yeff{bottom:513.361562px;} .y855{bottom:513.364772px;} .y87{bottom:513.371997px;} .y58f{bottom:513.375351px;} .y269{bottom:513.379351px;} .y860{bottom:513.387995px;} .y546{bottom:513.406444px;} .y5e{bottom:513.431215px;} .yaf{bottom:513.433537px;} .yef{bottom:513.452116px;} .y1ac{bottom:513.456631px;} .y1f5{bottom:513.456760px;} .y366{bottom:513.468372px;} .y287{bottom:513.495465px;} .y561{bottom:513.510947px;} .y571{bottom:513.569004px;} .y213{bottom:513.572874px;} .y3c9{bottom:513.580615px;} .y2bc{bottom:513.692859px;} .y33e{bottom:513.747046px;} .yd83{bottom:513.945071px;} .y520{bottom:513.952310px;} .y676{bottom:514.108677px;} .y629{bottom:514.222469px;} .y653{bottom:514.226726px;} .y775{bottom:514.424250px;} .y69b{bottom:514.428120px;} .y799{bottom:514.488112px;} .y6bf{bottom:514.493918px;} .y6e3{bottom:514.559716px;} .ye57{bottom:514.650027px;} .y435{bottom:515.927929px;} .y422{bottom:516.098100px;} .yca7{bottom:516.235760px;} .yf67{bottom:516.807687px;} .yf86{bottom:516.888967px;} .yfb2{bottom:517.005081px;} .ye79{bottom:517.138484px;} .y45d{bottom:517.928705px;} .yecd{bottom:518.377035px;} .yeae{bottom:519.549015px;} .y492{bottom:520.166871px;} .y4ac{bottom:520.178483px;} .y4c6{bottom:520.190094px;} .ycd7{bottom:521.790277px;} .y501{bottom:522.753767px;} .y4ed{bottom:522.858269px;} .yc71{bottom:523.181841px;} .yc2d{bottom:523.324662px;} .ye34{bottom:523.415618px;} .ydc0{bottom:523.720869px;} .yc1e{bottom:524.096047px;} .yaa6{bottom:524.158220px;} .ya9f{bottom:524.183661px;} .ya98{bottom:524.209102px;} .yca9{bottom:524.645925px;} .ycaa{bottom:524.655072px;} .yb39{bottom:524.885494px;} .y22{bottom:526.042895px;} .ye08{bottom:526.470453px;} .y604{bottom:527.207133px;} .y5e1{bottom:527.288413px;} .y5bd{bottom:527.369693px;} .ye93{bottom:527.514578px;} .y849{bottom:527.530705px;} .y854{bottom:527.553928px;} .y707{bottom:527.570958px;} .y706{bottom:527.573280px;} .y85f{bottom:527.577151px;} .y754{bottom:527.579860px;} .y7fd{bottom:527.586698px;} .y7de{bottom:527.609405px;} .yd1b{bottom:527.798413px;} .y675{bottom:527.959554px;} .yefe{bottom:528.036168px;} .y628{bottom:528.073345px;} .y652{bottom:528.077603px;} .y51f{bottom:528.176300px;} .y69a{bottom:528.278610px;} .y798{bottom:528.338602px;} .y6be{bottom:528.344408px;} .y6e2{bottom:528.410206px;} .y129{bottom:528.829507px;} .y167{bottom:528.836474px;} .y86{bottom:528.850408px;} .y58e{bottom:528.853375px;} .y268{bottom:528.857374px;} .y545{bottom:528.884468px;} .y5d{bottom:528.909626px;} .y2f7{bottom:528.911561px;} .yae{bottom:528.911948px;} .yee{bottom:528.930526px;} .y365{bottom:528.946395px;} .y286{bottom:528.973489px;} .y560{bottom:528.988970px;} .y570{bottom:529.047028px;} .y31c{bottom:529.050898px;} .y3c8{bottom:529.058639px;} .y2bb{bottom:529.170883px;} .y33d{bottom:529.225069px;} .yf2b{bottom:529.523225px;} .ye56{bottom:530.131921px;} .yb06{bottom:530.142114px;} .y3d6{bottom:530.152693px;} .y421{bottom:530.287256px;} .yb7d{bottom:530.704364px;} .yf66{bottom:530.996843px;} .yf85{bottom:531.078123px;} .yfb1{bottom:531.194237px;} .ybee{bottom:531.705398px;} .yf21{bottom:532.325964px;} .y45c{bottom:532.326867px;} .ye78{bottom:532.620378px;} .yecc{bottom:533.858929px;} .yd6e{bottom:534.034375px;} .y491{bottom:534.623090px;} .y4ab{bottom:534.634701px;} .y4c5{bottom:534.646313px;} .ybcc{bottom:534.698564px;} .yead{bottom:535.030909px;} .y434{bottom:535.282877px;} .ydbf{bottom:536.640664px;} .yf0f{bottom:536.889510px;} .y500{bottom:537.662831px;} .y4ec{bottom:537.767333px;} .ye33{bottom:538.897512px;} .yb38{bottom:539.074650px;} .ycb2{bottom:540.056332px;} .yaa5{bottom:540.516872px;} .ya9e{bottom:540.542313px;} .ya97{bottom:540.567754px;} .y603{bottom:541.454347px;} .y5e0{bottom:541.535626px;} .y5bc{bottom:541.616906px;} .y674{bottom:541.810430px;} .y705{bottom:541.821784px;} .y72d{bottom:541.826041px;} .y753{bottom:541.828363px;} .y7fc{bottom:541.835201px;} .y7dd{bottom:541.857908px;} .y651{bottom:541.888356px;} .y627{bottom:541.924222px;} .ye07{bottom:541.952347px;} .y699{bottom:542.129099px;} .y797{bottom:542.189091px;} .y6bd{bottom:542.194897px;} .y6e1{bottom:542.260695px;} .y51e{bottom:542.400290px;} .yefd{bottom:542.710775px;} .ye92{bottom:542.996472px;} .yf20{bottom:543.163290px;} .ydf2{bottom:543.341589px;} .y18c{bottom:543.983701px;} .y128{bottom:544.307918px;} .y166{bottom:544.314885px;} .y85{bottom:544.328818px;} .y58d{bottom:544.331399px;} .y267{bottom:544.335398px;} .y544{bottom:544.362491px;} .y5c{bottom:544.388036px;} .y2f6{bottom:544.389585px;} .yad{bottom:544.390359px;} .yed{bottom:544.408937px;} .y364{bottom:544.424419px;} .y285{bottom:544.451512px;} .y55f{bottom:544.466994px;} .y420{bottom:544.476412px;} .y56f{bottom:544.525051px;} .y31b{bottom:544.528922px;} .y3c7{bottom:544.536663px;} .yd1a{bottom:544.573045px;} .y2ba{bottom:544.648906px;} .y33c{bottom:544.703093px;} .ycd8{bottom:544.982283px;} .yf65{bottom:545.185999px;} .yf84{bottom:545.267279px;} .yfb0{bottom:545.383393px;} .ye55{bottom:545.613815px;} .y1d6{bottom:545.810565px;} .y3a{bottom:546.221080px;} .y45b{bottom:546.725028px;} .ye77{bottom:548.102272px;} .y3d5{bottom:548.216193px;} .y16{bottom:548.729621px;} .yb7c{bottom:548.766574px;} .y490{bottom:549.079308px;} .y4aa{bottom:549.090920px;} .y4c4{bottom:549.102531px;} .yecb{bottom:549.340823px;} .yb04{bottom:549.491256px;} .ydbe{bottom:549.560460px;} .yd4d{bottom:549.795067px;} .ybed{bottom:550.283671px;} .yeac{bottom:550.512803px;} .yb05{bottom:550.518544px;} .yd9f{bottom:552.108083px;} .y4ff{bottom:552.571895px;} .y4eb{bottom:552.676398px;} .ye32{bottom:554.379406px;} .y433{bottom:554.637824px;} .y51d{bottom:556.635892px;} .yaa4{bottom:556.875524px;} .ya9d{bottom:556.900965px;} .ya96{bottom:556.926407px;} .ydca{bottom:556.966095px;} .yefc{bottom:557.385381px;} .ye06{bottom:557.434242px;} .ydf1{bottom:557.449465px;} .ye91{bottom:558.478366px;} .y41f{bottom:558.665568px;} .yf64{bottom:559.375155px;} .yfaf{bottom:559.572549px;} .y127{bottom:559.786328px;} .y165{bottom:559.793295px;} .y84{bottom:559.807229px;} .y58c{bottom:559.809422px;} .y266{bottom:559.813422px;} .y543{bottom:559.840515px;} .y5b{bottom:559.866447px;} .y2f5{bottom:559.867608px;} .yac{bottom:559.868769px;} .yec{bottom:559.887348px;} .y363{bottom:559.902443px;} .y284{bottom:559.929536px;} .y55e{bottom:559.945018px;} .y56e{bottom:560.003075px;} .y31a{bottom:560.006945px;} .y3c6{bottom:560.014686px;} .y2b9{bottom:560.126930px;} .y33b{bottom:560.181117px;} .ye54{bottom:561.095710px;} .yd19{bottom:561.347677px;} .ydbd{bottom:562.480255px;} .y18b{bottom:562.561974px;} .y8d1{bottom:563.199570px;} .y48f{bottom:563.535527px;} .y4a9{bottom:563.547138px;} .y4c3{bottom:563.558750px;} .ye76{bottom:563.584166px;} .yd9e{bottom:563.719504px;} .y1d5{bottom:564.388837px;} .yeca{bottom:564.822718px;} .yd4c{bottom:564.924083px;} .ybcb{bottom:565.144096px;} .yeab{bottom:565.994697px;} .y3d4{bottom:566.279693px;} .yb7b{bottom:566.828784px;} .y4fe{bottom:567.480959px;} .y4ea{bottom:567.585462px;} .yb02{bottom:568.840398px;} .ybec{bottom:568.861944px;} .ye31{bottom:569.861300px;} .yb03{bottom:569.867686px;} .ydc9{bottom:569.885890px;} .ydba{bottom:570.815372px;} .y51c{bottom:570.859882px;} .ydf0{bottom:571.557341px;} .yefb{bottom:572.059987px;} .ye05{bottom:572.916136px;} .yf63{bottom:573.564311px;} .yfae{bottom:573.761705px;} .ye90{bottom:573.960260px;} .yd82{bottom:574.079499px;} .y126{bottom:575.268222px;} .y164{bottom:575.271706px;} .y83{bottom:575.285640px;} .y58b{bottom:575.287446px;} .y265{bottom:575.291445px;} .y542{bottom:575.318539px;} .yd9d{bottom:575.330924px;} .y125{bottom:575.341374px;} .y5a{bottom:575.344858px;} .y2f4{bottom:575.345632px;} .yab{bottom:575.347180px;} .yeb{bottom:575.365758px;} .y362{bottom:575.380466px;} .ydbc{bottom:575.400051px;} .y283{bottom:575.407560px;} .y55d{bottom:575.423041px;} .y56d{bottom:575.481099px;} .y319{bottom:575.484969px;} .y3c5{bottom:575.492710px;} .y45a{bottom:575.521351px;} .y2b8{bottom:575.604954px;} .y33a{bottom:575.659140px;} .ye53{bottom:576.577604px;} .ycb1{bottom:577.520128px;} .y48e{bottom:577.991746px;} .y4a8{bottom:578.003357px;} .y4c2{bottom:578.014969px;} .yd18{bottom:578.122310px;} .y35{bottom:578.776303px;} .ye75{bottom:579.066060px;} .yd4b{bottom:580.053098px;} .yec9{bottom:580.304612px;} .y18a{bottom:581.140247px;} .yeaa{bottom:581.476591px;} .y4fd{bottom:582.390023px;} .y4e9{bottom:582.494526px;} .ydc8{bottom:582.805686px;} .y1d4{bottom:582.967110px;} .yb7a{bottom:584.890994px;} .y51b{bottom:585.083872px;} .ydef{bottom:585.665217px;} .yd9c{bottom:586.942345px;} .yf62{bottom:587.753467px;} .yfad{bottom:587.950861px;} .ydbb{bottom:588.319846px;} .ye8f{bottom:589.442155px;} .yda7{bottom:589.534659px;} .y459{bottom:589.919513px;} .y163{bottom:590.750117px;} .y82{bottom:590.764050px;} .y58a{bottom:590.765469px;} .y264{bottom:590.769469px;} .y541{bottom:590.796562px;} .y124{bottom:590.819785px;} .y59{bottom:590.823269px;} .y2f3{bottom:590.823656px;} .yaa{bottom:590.825591px;} .yea{bottom:590.844169px;} .y361{bottom:590.858490px;} .y282{bottom:590.885583px;} .y55c{bottom:590.901065px;} .y56c{bottom:590.959122px;} .y318{bottom:590.962993px;} .y3c4{bottom:590.970734px;} .y2b7{bottom:591.082977px;} .y339{bottom:591.137164px;} .ye52{bottom:592.059498px;} .y48d{bottom:592.447964px;} .y4a7{bottom:592.459576px;} .yd81{bottom:592.466023px;} .y4c1{bottom:592.471187px;} .ye74{bottom:594.547954px;} .yd17{bottom:594.896942px;} .yd4a{bottom:595.182113px;} .ydc6{bottom:595.725481px;} .yec8{bottom:595.786506px;} .y34{bottom:596.411583px;} .ydc7{bottom:596.705232px;} .ye2d{bottom:596.805214px;} .yea9{bottom:596.958485px;} .y4fc{bottom:597.299087px;} .y4e8{bottom:597.403590px;} .yd9b{bottom:598.553765px;} .y51a{bottom:599.319474px;} .y189{bottom:599.718520px;} .ydee{bottom:599.773093px;} .ydd2{bottom:600.115630px;} .y432{bottom:601.472489px;} .y1d3{bottom:601.545383px;} .yf61{bottom:601.942623px;} .yfac{bottom:602.140017px;} .yb79{bottom:602.953204px;} .y8ce{bottom:603.334445px;} .y458{bottom:604.317674px;} .y531{bottom:604.486556px;} .ye8e{bottom:604.924049px;} .yc65{bottom:605.349930px;} .y162{bottom:606.232011px;} .y161{bottom:606.238978px;} .y81{bottom:606.242461px;} .y589{bottom:606.243493px;} .y263{bottom:606.247493px;} .y391{bottom:606.262974px;} .y540{bottom:606.274586px;} .y123{bottom:606.298196px;} .y58{bottom:606.301679px;} .ya9{bottom:606.304002px;} .ye9{bottom:606.322580px;} .y360{bottom:606.336513px;} .y281{bottom:606.363607px;} .y55b{bottom:606.379089px;} .y3b4{bottom:606.390700px;} .y56b{bottom:606.437146px;} .y317{bottom:606.441016px;} .y3c3{bottom:606.448757px;} .y2b6{bottom:606.561001px;} .y338{bottom:606.615188px;} .y48c{bottom:606.904183px;} .y4a6{bottom:606.915794px;} .y4c0{bottom:606.927406px;} .ydb8{bottom:607.692082px;} .ydc1{bottom:607.930633px;} .y9af{bottom:608.078028px;} .yd9a{bottom:610.165186px;} .yd49{bottom:610.311129px;} .yc3e{bottom:610.649769px;} .yd80{bottom:610.852547px;} .yec7{bottom:611.268400px;} .yd16{bottom:611.671574px;} .yda5{bottom:611.766659px;} .y4fb{bottom:612.208151px;} .y4e7{bottom:612.312654px;} .yea8{bottom:612.440379px;} .yda6{bottom:613.175511px;} .y519{bottom:613.543464px;} .yded{bottom:613.880969px;} .y33{bottom:614.046863px;} .yd95{bottom:614.531080px;} .yc76{bottom:615.205575px;} .yefa{bottom:616.083264px;} .yf60{bottom:616.131779px;} .yfab{bottom:616.329173px;} .ydc5{bottom:616.705125px;} .yb20{bottom:617.128619px;} .y188{bottom:618.296793px;} .y457{bottom:618.715836px;} .ye45{bottom:619.007412px;} .ybe4{bottom:619.093465px;} .yc95{bottom:619.781377px;} .y1d2{bottom:620.123656px;} .yb78{bottom:621.015413px;} .y48b{bottom:621.360402px;} .y4a5{bottom:621.372013px;} .y4bf{bottom:621.383624px;} .ye6f{bottom:621.490837px;} .y160{bottom:621.717388px;} .y80{bottom:621.720872px;} .y588{bottom:621.721517px;} .y262{bottom:621.725516px;} .y390{bottom:621.740998px;} .y53f{bottom:621.752610px;} .y122{bottom:621.776606px;} .y2f2{bottom:621.779703px;} .y57{bottom:621.780090px;} .ya8{bottom:621.782412px;} .ye8{bottom:621.800990px;} .y35f{bottom:621.814537px;} .y280{bottom:621.841630px;} .y55a{bottom:621.857112px;} .y3b3{bottom:621.868724px;} .y316{bottom:621.919040px;} .y3c2{bottom:621.926781px;} .y2b5{bottom:622.039025px;} .y337{bottom:622.093211px;} .ye2c{bottom:622.608371px;} .yd48{bottom:625.440144px;} .ydd1{bottom:625.918787px;} .y518{bottom:627.779066px;} .ydec{bottom:627.988846px;} .ycbc{bottom:628.077350px;} .yd15{bottom:628.446206px;} .yd7f{bottom:629.239071px;} .y9ae{bottom:630.011946px;} .yf5f{bottom:630.320935px;} .yfaa{bottom:630.518329px;} .yef9{bottom:630.757870px;} .y32{bottom:631.682144px;} .ye89{bottom:631.867834px;} .y456{bottom:633.113998px;} .yd99{bottom:633.388027px;} .yec3{bottom:633.696375px;} .yed9{bottom:634.610710px;} .y48a{bottom:635.816620px;} .y4a4{bottom:635.828232px;} .y4be{bottom:635.839843px;} .y187{bottom:636.875066px;} .y15f{bottom:637.195799px;} .y7f{bottom:637.199282px;} .y587{bottom:637.199540px;} .y261{bottom:637.203540px;} .y38f{bottom:637.219022px;} .y53e{bottom:637.230633px;} .y121{bottom:637.255017px;} .y2f1{bottom:637.257726px;} .y56{bottom:637.258501px;} .ya7{bottom:637.260823px;} .ye7{bottom:637.279401px;} .y35e{bottom:637.292561px;} .y27f{bottom:637.319654px;} .y559{bottom:637.335136px;} .y3b2{bottom:637.346747px;} .y315{bottom:637.397064px;} .y3c1{bottom:637.404804px;} .y2b4{bottom:637.517048px;} .y336{bottom:637.571235px;} .yc84{bottom:638.163546px;} .y1d1{bottom:638.701929px;} .y52e{bottom:639.046530px;} .yb77{bottom:639.077623px;} .ya20{bottom:640.046725px;} .ybca{bottom:640.334316px;} .ybc1{bottom:640.359757px;} .ybc2{bottom:640.384940px;} .yd47{bottom:640.569159px;} .y517{bottom:642.003056px;} .ydeb{bottom:642.096722px;} .yda4{bottom:642.530989px;} .yc07{bottom:643.650072px;} .ybe3{bottom:643.909264px;} .yf5e{bottom:644.510091px;} .yfa9{bottom:644.707485px;} .ye44{bottom:644.810569px;} .yd14{bottom:645.220839px;} .yef8{bottom:645.432476px;} .yb1f{bottom:645.504028px;} .y8ef{bottom:645.571762px;} .ya33{bottom:646.325085px;} .ye6e{bottom:647.293993px;} .yc47{bottom:647.316829px;} .y455{bottom:647.512159px;} .yd7e{bottom:647.625595px;} .yc49{bottom:648.135434px;} .y31{bottom:649.317424px;} .y489{bottom:650.272839px;} .y4a3{bottom:650.284450px;} .y4bd{bottom:650.296062px;} .y9d0{bottom:650.398318px;} .y93d{bottom:651.319124px;} .y586{bottom:652.677564px;} .y7e{bottom:652.677693px;} .y260{bottom:652.681564px;} .y38e{bottom:652.697045px;} .y53d{bottom:652.708657px;} .y120{bottom:652.733428px;} .y2f0{bottom:652.735750px;} .y55{bottom:652.736911px;} .ya6{bottom:652.739234px;} .ye6{bottom:652.757812px;} .y35d{bottom:652.770584px;} .y27e{bottom:652.797678px;} .y558{bottom:652.813160px;} .y3b1{bottom:652.824771px;} .yd98{bottom:652.868894px;} .y314{bottom:652.875087px;} .y3c0{bottom:652.882828px;} .y2b3{bottom:652.995072px;} .y335{bottom:653.049258px;} .ye2b{bottom:653.572159px;} .y186{bottom:655.453339px;} .y8e9{bottom:655.591902px;} .yd46{bottom:655.698174px;} .ycbe{bottom:655.778974px;} .ydea{bottom:656.204598px;} .y516{bottom:656.227046px;} .ybc9{bottom:656.692968px;} .ybc0{bottom:656.718409px;} .ydd0{bottom:656.889671px;} .yc3a{bottom:656.921022px;} .yc74{bottom:656.932634px;} .yb76{bottom:657.139833px;} .y1d0{bottom:657.280202px;} .ye88{bottom:657.670991px;} .ya1f{bottom:657.781557px;} .y8cb{bottom:657.840260px;} .yf5d{bottom:658.699247px;} .yfa8{bottom:658.896641px;} .yb8b{bottom:659.386901px;} .yec2{bottom:659.499532px;} .yef7{bottom:660.107082px;} .yed8{bottom:660.413867px;} .ybe2{bottom:660.939348px;} .ydc3{bottom:661.113777px;} .y82e{bottom:661.816765px;} .y454{bottom:661.910321px;} .yd13{bottom:661.995471px;} .yb4a{bottom:662.777200px;} .ybfd{bottom:663.205252px;} .y488{bottom:664.729057px;} .y4a2{bottom:664.740669px;} .y4bc{bottom:664.752280px;} .yd7c{bottom:665.958893px;} .yd7d{bottom:666.012119px;} .yb82{bottom:666.139974px;} .yad6{bottom:666.357490px;} .y30{bottom:666.952705px;} .y3e6{bottom:667.110173px;} .y8ee{bottom:667.504445px;} .y8ed{bottom:667.508047px;} .y7d{bottom:668.159587px;} .y38d{bottom:668.175069px;} .y53c{bottom:668.186680px;} .y11f{bottom:668.211839px;} .y2ef{bottom:668.213774px;} .y54{bottom:668.215322px;} .ya5{bottom:668.217644px;} .ye5{bottom:668.236223px;} .ya31{bottom:668.248438px;} .y35c{bottom:668.248608px;} .ya32{bottom:668.257768px;} .y27d{bottom:668.275701px;} .y557{bottom:668.291183px;} .y3b0{bottom:668.302795px;} .y7c{bottom:668.350014px;} .y313{bottom:668.353111px;} .y3bf{bottom:668.360852px;} .y2b2{bottom:668.473096px;} .y334{bottom:668.527282px;} .y47f{bottom:670.171072px;} .yde9{bottom:670.312474px;} .y515{bottom:670.462648px;} .yd45{bottom:670.827190px;} .yf5c{bottom:672.888403px;} .ybc8{bottom:673.051620px;} .yc56{bottom:673.054317px;} .ybbf{bottom:673.077061px;} .yfa7{bottom:673.085797px;} .y93c{bottom:673.253042px;} .y185{bottom:674.031612px;} .yef6{bottom:674.781689px;} .yb75{bottom:675.202043px;} .ya1e{bottom:675.516390px;} .ye43{bottom:675.772034px;} .y453{bottom:676.308482px;} .ya2d{bottom:676.468462px;} .y8ca{bottom:677.189402px;} .yc39{bottom:677.603904px;} .ye6d{bottom:678.260749px;} .yd12{bottom:678.770103px;} .y487{bottom:679.185276px;} .y4a1{bottom:679.196887px;} .y4bb{bottom:679.208499px;} .yc80{bottom:679.517621px;} .yc91{bottom:681.335943px;} .ydb9{bottom:681.377899px;} .y47e{bottom:681.782493px;} .ycbd{bottom:682.880030px;} .y15e{bottom:683.641481px;} .y38c{bottom:683.653093px;} .y53b{bottom:683.664704px;} .y11e{bottom:683.690249px;} .y2ee{bottom:683.691797px;} .y53{bottom:683.693733px;} .ye4{bottom:683.714633px;} .y35b{bottom:683.726632px;} .y556{bottom:683.769207px;} .y3af{bottom:683.780818px;} .y5b7{bottom:683.831005px;} .y312{bottom:683.831134px;} .y3be{bottom:683.838875px;} .y2b1{bottom:683.951119px;} .y333{bottom:684.005306px;} .yd7b{bottom:684.345417px;} .yde8{bottom:684.420350px;} .y514{bottom:684.686638px;} .yb8a{bottom:684.715022px;} .yb89{bottom:684.716516px;} .yd44{bottom:685.956205px;} .y82d{bottom:686.403833px;} .y39{bottom:686.528687px;} .yf5b{bottom:687.077559px;} .yfa6{bottom:687.274953px;} .yad4{bottom:687.551950px;} .ye87{bottom:688.634779px;} .y21{bottom:689.169393px;} .yc09{bottom:689.229877px;} .ybc7{bottom:689.410272px;} .ybbe{bottom:689.435713px;} .yef5{bottom:689.456295px;} .y883{bottom:689.695358px;} .yec1{bottom:690.471706px;} .y452{bottom:690.706644px;} .yb28{bottom:690.901339px;} .y1d7{bottom:691.108141px;} .yed7{bottom:691.381267px;} .y5bb{bottom:691.947775px;} .ya1d{bottom:693.251222px;} .yb73{bottom:693.264253px;} .y486{bottom:693.641495px;} .y4a0{bottom:693.653106px;} .y4ba{bottom:693.664718px;} .yb74{bottom:694.291541px;} .ybe1{bottom:694.999515px;} .yd2c{bottom:695.282446px;} .yd11{bottom:695.544736px;} .y3e5{bottom:696.138724px;} .y8c9{bottom:696.538544px;} .yc42{bottom:696.889828px;} .y8e8{bottom:697.495712px;} .ya7f{bottom:697.810382px;} .yc38{bottom:698.286785px;} .yde7{bottom:698.528226px;} .y513{bottom:698.910628px;} .y82a{bottom:698.996940px;} .y15d{bottom:699.123375px;} .y38b{bottom:699.131116px;} .y53a{bottom:699.142728px;} .y11d{bottom:699.168660px;} .y2ed{bottom:699.169821px;} .y52{bottom:699.172143px;} .ye3{bottom:699.193044px;} .y35a{bottom:699.204655px;} .y555{bottom:699.247231px;} .y3ae{bottom:699.258842px;} .y15c{bottom:699.305288px;} .y5b6{bottom:699.309029px;} .y311{bottom:699.309158px;} .y3bd{bottom:699.316899px;} .y2b0{bottom:699.429143px;} .y332{bottom:699.483329px;} .yc21{bottom:699.653888px;} .y2df{bottom:700.151244px;} .yc7f{bottom:700.200502px;} .yd43{bottom:701.085220px;} .yf5a{bottom:701.266715px;} .yfa5{bottom:701.464109px;} .yc90{bottom:702.018825px;} .yd7a{bottom:702.731941px;} .yf1f{bottom:703.528619px;} .yef4{bottom:704.130901px;} .y451{bottom:705.104805px;} .y18d{bottom:705.227628px;} .ybc6{bottom:705.768924px;} .ybbd{bottom:705.794365px;} .y9da{bottom:706.981469px;} .y9e2{bottom:707.004692px;} .y9c5{bottom:707.071651px;} .y9ba{bottom:707.089713px;} .y485{bottom:708.097713px;} .y49e{bottom:708.109325px;} .y4b9{bottom:708.120936px;} .y49f{bottom:709.165964px;} .ybfc{bottom:709.912759px;} .yb11{bottom:710.411740px;} .yb18{bottom:710.423352px;} .ya1c{bottom:710.986054px;} .yb71{bottom:711.326462px;} .y2de{bottom:711.762665px;} .ybe0{bottom:712.029598px;} .yd10{bottom:712.319368px;} .yb72{bottom:712.353751px;} .yde6{bottom:712.636102px;} .yb27{bottom:712.835257px;} .y882{bottom:712.919507px;} .y8f9{bottom:713.138747px;} .y512{bottom:713.146230px;} .y901{bottom:713.161970px;} .y8e7{bottom:713.171130px;} .y38a{bottom:714.609140px;} .y539{bottom:714.620751px;} .y11c{bottom:714.647071px;} .y51{bottom:714.650554px;} .ye2{bottom:714.671455px;} .y359{bottom:714.682679px;} .y554{bottom:714.725254px;} .y3ad{bottom:714.736866px;} .y15b{bottom:714.783698px;} .y5b5{bottom:714.787053px;} .y3bc{bottom:714.794923px;} .y2af{bottom:714.907166px;} .y331{bottom:714.961353px;} .yd2a{bottom:715.433938px;} .yf59{bottom:715.455871px;} .yfa4{bottom:715.653265px;} .y8c8{bottom:715.887686px;} .yd42{bottom:716.214236px;} .yb93{bottom:716.988965px;} .yb98{bottom:717.000577px;} .ya2f{bottom:717.241965px;} .yc41{bottom:717.572710px;} .y948{bottom:717.952971px;} .y950{bottom:717.976194px;} .y958{bottom:717.999417px;} .yef3{bottom:718.805507px;} .yc37{bottom:718.969667px;} .y450{bottom:719.502967px;} .ya7d{bottom:719.740196px;} .ya7e{bottom:719.743065px;} .yd79{bottom:721.118465px;} .y9d9{bottom:721.170625px;} .y9e1{bottom:721.193848px;} .y9c4{bottom:721.260807px;} .y9b9{bottom:721.278869px;} .y9cd{bottom:721.284030px;} .y3e4{bottom:721.873503px;} .ybc5{bottom:722.127576px;} .ybbc{bottom:722.153017px;} .y484{bottom:722.553932px;} .y49d{bottom:722.565543px;} .y4b8{bottom:722.577155px;} .yb53{bottom:723.698947px;} .yb10{bottom:724.600896px;} .yb17{bottom:724.612508px;} .yb1e{bottom:724.624119px;} .y2e0{bottom:725.028197px;} .yde5{bottom:726.743978px;} .y8f8{bottom:727.327903px;} .y900{bottom:727.351126px;} .y511{bottom:727.370220px;} .y908{bottom:727.374349px;} .y385{bottom:728.082645px;} .y838{bottom:728.489561px;} .y841{bottom:728.512784px;} .ya1b{bottom:728.720886px;} .y8e6{bottom:728.846548px;} .ybdf{bottom:729.059682px;} .yd0f{bottom:729.094000px;} .yf58{bottom:729.645027px;} .yfa3{bottom:729.842421px;} .y389{bottom:730.087164px;} .y538{bottom:730.098775px;} .y11b{bottom:730.125481px;} .y50{bottom:730.128965px;} .ye1{bottom:730.149865px;} .y358{bottom:730.160703px;} .y553{bottom:730.203278px;} .y3ac{bottom:730.214889px;} .y15a{bottom:730.262109px;} .y5b4{bottom:730.265076px;} .y3bb{bottom:730.272946px;} .y2ae{bottom:730.385190px;} .yad1{bottom:730.427894px;} .y330{bottom:730.439377px;} .ybfb{bottom:730.595641px;} .yb92{bottom:731.178121px;} .yb97{bottom:731.189732px;} .yb9c{bottom:731.201344px;} .yd41{bottom:731.343251px;} .y947{bottom:732.142127px;} .y94f{bottom:732.165350px;} .y2f{bottom:732.179729px;} .y957{bottom:732.188573px;} .y3e9{bottom:732.564138px;} .yb24{bottom:733.228182px;} .yef2{bottom:733.480021px;} .y44f{bottom:733.901128px;} .yae1{bottom:734.108126px;} .yadc{bottom:734.120846px;} .yae7{bottom:734.135292px;} .ya3d{bottom:734.698575px;} .ya45{bottom:734.721798px;} .ya4d{bottom:734.745020px;} .y8c7{bottom:735.236829px;} .y9d8{bottom:735.359781px;} .y9e0{bottom:735.383004px;} .y9e8{bottom:735.406226px;} .y9c3{bottom:735.452543px;} .y9c2{bottom:735.455123px;} .y9b8{bottom:735.468025px;} .y9cc{bottom:735.473186px;} .yf1e{bottom:736.094784px;} .y483{bottom:737.010151px;} .y49c{bottom:737.021762px;} .y4b7{bottom:737.033373px;} .yb52{bottom:737.888103px;} .yc15{bottom:738.255592px;} .ybc4{bottom:738.486228px;} .ybbb{bottom:738.511670px;} .yb0f{bottom:738.790052px;} .yb16{bottom:738.801664px;} .yb1d{bottom:738.813275px;} .yd78{bottom:739.504989px;} .yc36{bottom:739.652549px;} .y384{bottom:739.694066px;} .ye6a{bottom:740.295150px;} .ya27{bottom:740.479901px;} .yde4{bottom:740.851854px;} .yc96{bottom:741.515253px;} .y8f7{bottom:741.517059px;} .yc86{bottom:741.519330px;} .y8ff{bottom:741.540282px;} .y907{bottom:741.563505px;} .yc7e{bottom:741.566266px;} .y510{bottom:741.594210px;} .yc8f{bottom:743.384588px;} .yf57{bottom:743.834182px;} .yb87{bottom:743.849406px;} .yf83{bottom:743.950297px;} .y837{bottom:743.967585px;} .y840{bottom:743.990808px;} .y848{bottom:744.014030px;} .yfa2{bottom:744.031577px;} .y8e5{bottom:744.521966px;} .y34f{bottom:745.337603px;} .yb91{bottom:745.367277px;} .yb96{bottom:745.378888px;} .yb9b{bottom:745.390500px;} .y537{bottom:745.576799px;} .y11a{bottom:745.603892px;} .y4f{bottom:745.607375px;} .ye0{bottom:745.628276px;} .y357{bottom:745.638726px;} .y552{bottom:745.681301px;} .y159{bottom:745.740520px;} .y5b3{bottom:745.743100px;} .y2ad{bottom:745.863214px;} .yd0e{bottom:745.868632px;} .y32f{bottom:745.917400px;} .yad0{bottom:746.103312px;} .y946{bottom:746.331283px;} .y94e{bottom:746.354506px;} .y956{bottom:746.377729px;} .ya1a{bottom:746.455719px;} .yd40{bottom:746.472266px;} .yf1d{bottom:746.932109px;} .y829{bottom:746.974427px;} .y44e{bottom:748.299290px;} .y9d7{bottom:749.548937px;} .y9df{bottom:749.572159px;} .y9e7{bottom:749.595382px;} .y9c1{bottom:749.644279px;} .y9b7{bottom:749.657181px;} .y9cb{bottom:749.662342px;} .ya3c{bottom:750.176598px;} .ya44{bottom:750.199821px;} .ya4c{bottom:750.223044px;} .yae0{bottom:750.466778px;} .yadb{bottom:750.479498px;} .yae6{bottom:750.490365px;} .ybfa{bottom:751.278522px;} .y482{bottom:751.466369px;} .y49b{bottom:751.477981px;} .y4b6{bottom:751.489592px;} .yb51{bottom:752.077259px;} .y38{bottom:752.551031px;} .yb0e{bottom:752.979208px;} .yb15{bottom:752.990820px;} .yb1c{bottom:753.002431px;} .y3e3{bottom:754.127449px;} .y88a{bottom:754.252852px;} .y88f{bottom:754.264464px;} .y3da{bottom:754.285235px;} .y8c6{bottom:754.585971px;} .ybc3{bottom:754.844881px;} .ybba{bottom:754.870322px;} .yde3{bottom:754.959730px;} .y20{bottom:755.196301px;} .y8f6{bottom:755.706215px;} .y8fe{bottom:755.729438px;} .y906{bottom:755.752661px;} .y50f{bottom:755.829812px;} .ya89{bottom:756.701351px;} .ya90{bottom:756.715668px;} .yd77{bottom:757.891513px;} .yf56{bottom:758.023338px;} .yf82{bottom:758.139453px;} .yfa1{bottom:758.220733px;} .yc14{bottom:758.938473px;} .y836{bottom:759.445608px;} .y83f{bottom:759.468831px;} .y847{bottom:759.492054px;} .yb90{bottom:759.556433px;} .yb95{bottom:759.568044px;} .yb9a{bottom:759.579656px;} .y8e4{bottom:760.197383px;} .yc35{bottom:760.335430px;} .y945{bottom:760.520439px;} .y94d{bottom:760.543662px;} .y955{bottom:760.566885px;} .y536{bottom:761.054822px;} .y119{bottom:761.082303px;} .y4e{bottom:761.085786px;} .ydf{bottom:761.106687px;} .y356{bottom:761.116750px;} .y551{bottom:761.159325px;} .y158{bottom:761.218930px;} .y5b2{bottom:761.221124px;} .yb31{bottom:761.282406px;} .yb37{bottom:761.294018px;} .y2ac{bottom:761.341237px;} .y32e{bottom:761.395424px;} .yd3f{bottom:761.601282px;} .yacf{bottom:761.778730px;} .yc7d{bottom:762.249147px;} .yd0d{bottom:762.643265px;} .y828{bottom:762.649844px;} .y44d{bottom:762.697451px;} .ybde{bottom:763.119849px;} .y9d6{bottom:763.738093px;} .y9de{bottom:763.761315px;} .y9e6{bottom:763.784538px;} .y9c0{bottom:763.836016px;} .y9b6{bottom:763.846337px;} .y9ca{bottom:763.851497px;} .y9bf{bottom:763.869560px;} .yc8e{bottom:764.067470px;} .ya19{bottom:764.190551px;} .y3e8{bottom:764.818084px;} .ya3b{bottom:765.654622px;} .ya43{bottom:765.677845px;} .ya4b{bottom:765.701068px;} .yb50{bottom:766.266415px;} .yedd{bottom:766.295314px;} .yadf{bottom:766.825430px;} .yada{bottom:766.838150px;} .yae5{bottom:766.845309px;} .y34e{bottom:767.069796px;} .yb0d{bottom:767.168364px;} .yb14{bottom:767.179976px;} .yb1b{bottom:767.191587px;} .y889{bottom:768.442008px;} .y88e{bottom:768.453619px;} .yb70{bottom:768.689267px;} .yde2{bottom:769.067606px;} .y8f5{bottom:769.895371px;} .y8fd{bottom:769.918594px;} .y905{bottom:769.941817px;} .ybf9{bottom:771.961404px;} .yf55{bottom:772.212494px;} .yf81{bottom:772.328609px;} .yfa0{bottom:772.409889px;} .ya88{bottom:773.060003px;} .ya95{bottom:773.061599px;} .ya8f{bottom:773.074320px;} .yb8f{bottom:773.745589px;} .yb94{bottom:773.757200px;} .yb99{bottom:773.768812px;} .y8c5{bottom:773.935113px;} .y944{bottom:774.709595px;} .y94c{bottom:774.732818px;} .y954{bottom:774.756041px;} .y835{bottom:774.923632px;} .y83d{bottom:774.946855px;} .y846{bottom:774.970078px;} .yb30{bottom:775.471562px;} .yb36{bottom:775.483174px;} .y8e3{bottom:775.872801px;} .y83e{bottom:776.003494px;} .yd76{bottom:776.278037px;} .y535{bottom:776.532846px;} .y118{bottom:776.560713px;} .y4d{bottom:776.564197px;} .yde{bottom:776.585097px;} .y355{bottom:776.594774px;} .y550{bottom:776.637349px;} .y157{bottom:776.697341px;} .y5b1{bottom:776.699147px;} .yd3e{bottom:776.730297px;} .y2ab{bottom:776.819261px;} .y32d{bottom:776.873448px;} .y4e6{bottom:776.898477px;} .y44c{bottom:777.095613px;} .yace{bottom:777.454148px;} .yef1{bottom:777.502849px;} .y9d5{bottom:777.927249px;} .y9dd{bottom:777.950471px;} .y9e5{bottom:777.973694px;} .y9b5{bottom:778.035493px;} .y9c9{bottom:778.040653px;} .y9be{bottom:778.058716px;} .y827{bottom:778.325262px;} .y8cf{bottom:778.425378px;} .ye04{bottom:778.825327px;} .yd0c{bottom:779.417897px;} .yc13{bottom:779.621355px;} .ybdd{bottom:780.149932px;} .yb4f{bottom:780.455571px;} .yc34{bottom:781.018312px;} .ya3a{bottom:781.132646px;} .ya42{bottom:781.155869px;} .ya4a{bottom:781.179091px;} .yb0c{bottom:781.357520px;} .yb13{bottom:781.369132px;} .yb1a{bottom:781.380743px;} .ye86{bottom:781.777209px;} .ya18{bottom:781.925383px;} .y888{bottom:782.631164px;} .y88d{bottom:782.642775px;} .y892{bottom:782.654387px;} .yc7c{bottom:782.932029px;} .yd21{bottom:783.030339px;} .yae3{bottom:783.171361px;} .yde1{bottom:783.175482px;} .yade{bottom:783.184082px;} .yad9{bottom:783.196803px;} .yae4{bottom:783.200382px;} .y8f4{bottom:784.084527px;} .y8fc{bottom:784.107750px;} .y904{bottom:784.130973px;} .yc8d{bottom:784.750352px;} .yd1f{bottom:784.858182px;} .yd20{bottom:784.858880px;} .y3e2{bottom:786.381395px;} .yf54{bottom:786.401650px;} .yf80{bottom:786.517765px;} .yf9f{bottom:786.599044px;} .y943{bottom:788.898751px;} .y94b{bottom:788.921974px;} .y953{bottom:788.945197px;} .y34d{bottom:788.996029px;} .ya8d{bottom:789.405935px;} .ya87{bottom:789.418655px;} .ya94{bottom:789.420251px;} .ya8e{bottom:789.429393px;} .yb2f{bottom:789.660718px;} .yb35{bottom:789.672329px;} .y834{bottom:790.401656px;} .y83c{bottom:790.424879px;} .y845{bottom:790.448101px;} .y44b{bottom:791.493774px;} .y8e2{bottom:791.548219px;} .yd3d{bottom:791.859312px;} .y117{bottom:792.039124px;} .y4c{bottom:792.042607px;} .ydd{bottom:792.063508px;} .y354{bottom:792.072797px;} .y9d4{bottom:792.116404px;} .y9dc{bottom:792.139627px;} .y9e4{bottom:792.162850px;} .y156{bottom:792.175752px;} .y5b0{bottom:792.177171px;} .yef0{bottom:792.177455px;} .y9b4{bottom:792.224649px;} .y9c8{bottom:792.229809px;} .y9bd{bottom:792.247872px;} .y2aa{bottom:792.297285px;} .y32c{bottom:792.351471px;} .ybf8{bottom:792.644285px;} .ydab{bottom:792.685106px;} .yacd{bottom:793.129565px;} .y8c4{bottom:793.284255px;} .y826{bottom:794.000680px;} .ye03{bottom:794.307222px;} .yb4e{bottom:794.644727px;} .yd75{bottom:794.664561px;} .y530{bottom:795.200398px;} .yb0b{bottom:795.546676px;} .yb12{bottom:795.558288px;} .yb19{bottom:795.569899px;} .yd0b{bottom:796.192529px;} .ya39{bottom:796.610669px;} .ya41{bottom:796.633892px;} .ya49{bottom:796.657115px;} .y887{bottom:796.820320px;} .y88c{bottom:796.831931px;} .y891{bottom:796.843543px;} .ye73{bottom:796.999523px;} .yb6f{bottom:797.064676px;} .y3e7{bottom:797.072030px;} .ybdc{bottom:797.180016px;} .ye51{bottom:797.259103px;} .yde0{bottom:797.283358px;} .y2e{bottom:797.626214px;} .y8f3{bottom:798.273683px;} .y8fb{bottom:798.296906px;} .y903{bottom:798.320128px;} .yae2{bottom:799.530013px;} .yadd{bottom:799.542734px;} .yad8{bottom:799.555455px;} .ya17{bottom:799.660215px;} .yc12{bottom:800.304236px;} .yf53{bottom:800.590806px;} .yf7f{bottom:800.706920px;} .yf9e{bottom:800.788200px;} .yc33{bottom:801.701194px;} .y942{bottom:803.087907px;} .y94a{bottom:803.111130px;} .y952{bottom:803.134352px;} .yc7b{bottom:803.614910px;} .yb2e{bottom:803.849874px;} .yb34{bottom:803.861485px;} .yc8c{bottom:805.433233px;} .ya8c{bottom:805.764587px;} .ya86{bottom:805.777307px;} .ya93{bottom:805.778903px;} .y833{bottom:805.879679px;} .y44a{bottom:805.891936px;} .y83b{bottom:805.902902px;} .y844{bottom:805.926125px;} .y9d3{bottom:806.305560px;} .y9db{bottom:806.328783px;} .y9e3{bottom:806.352006px;} .y9b3{bottom:806.413805px;} .y9c7{bottom:806.418965px;} .y9bc{bottom:806.437028px;} .y580{bottom:806.752471px;} .y52f{bottom:806.814399px;} .yeef{bottom:806.852061px;} .yd3c{bottom:806.988327px;} .ya2e{bottom:807.223637px;} .y116{bottom:807.517535px;} .y4b{bottom:807.521018px;} .ydc{bottom:807.541919px;} .y353{bottom:807.550821px;} .y155{bottom:807.654162px;} .y5af{bottom:807.655195px;} .y2a9{bottom:807.775308px;} .y32b{bottom:807.829495px;} .yacc{bottom:808.804983px;} .yb4d{bottom:808.833883px;} .y825{bottom:809.676098px;} .ye02{bottom:809.789116px;} .y34c{bottom:810.922261px;} .y886{bottom:811.009476px;} .y88b{bottom:811.021087px;} .y890{bottom:811.032699px;} .yddf{bottom:811.391234px;} .ya38{bottom:812.088693px;} .ya40{bottom:812.111916px;} .ya48{bottom:812.135139px;} .y8f2{bottom:812.462839px;} .ye2a{bottom:812.481417px;} .y8fa{bottom:812.486062px;} .y902{bottom:812.509284px;} .y8c3{bottom:812.633398px;} .ye50{bottom:812.740997px;} .yd0a{bottom:812.967161px;} .yd74{bottom:813.051085px;} .yc08{bottom:813.327167px;} .yc85{bottom:813.926652px;} .yea7{bottom:814.569408px;} .yf52{bottom:814.779962px;} .yf7e{bottom:814.896076px;} .yf9d{bottom:814.977356px;} .y2d{bottom:815.261494px;} .y941{bottom:817.277063px;} .y949{bottom:817.300286px;} .y951{bottom:817.323508px;} .ya16{bottom:817.395048px;} .yb2d{bottom:818.039030px;} .yb33{bottom:818.050641px;} .y3e1{bottom:818.635341px;} .y449{bottom:820.290097px;} .y9b2{bottom:820.602961px;} .y9c6{bottom:820.608121px;} .y9bb{bottom:820.626183px;} .yc11{bottom:820.987118px;} .y832{bottom:821.357703px;} .y83a{bottom:821.380926px;} .y843{bottom:821.404149px;} .yeee{bottom:821.526667px;} .yd3b{bottom:822.117343px;} .ya8b{bottom:822.123239px;} .ya85{bottom:822.135959px;} .ya92{bottom:822.137556px;} .yc32{bottom:822.384075px;} .y8e1{bottom:822.899055px;} .y115{bottom:822.995945px;} .y4a{bottom:822.999429px;} .ydb{bottom:823.020329px;} .yb4c{bottom:823.023039px;} .y352{bottom:823.028844px;} .y154{bottom:823.132573px;} .y5ae{bottom:823.133218px;} .y2a8{bottom:823.253332px;} .y32a{bottom:823.307519px;} .yc7a{bottom:824.297792px;} .yacb{bottom:824.480401px;} .ye01{bottom:825.271010px;} .y824{bottom:825.351516px;} .ydde{bottom:825.499110px;} .y57f{bottom:826.878933px;} .ya37{bottom:827.566717px;} .ya3f{bottom:827.589939px;} .ya47{bottom:827.613162px;} .ye29{bottom:827.963311px;} .ye4f{bottom:828.222891px;} .yf51{bottom:828.969118px;} .yf7d{bottom:829.085232px;} .yf9c{bottom:829.166512px;} .yd09{bottom:829.741794px;} .yea6{bottom:830.051303px;} .ybdb{bottom:831.240183px;} .yd73{bottom:831.437609px;} .y8c2{bottom:831.982540px;} .yb2c{bottom:832.228186px;} .yb32{bottom:832.239797px;} .ybf7{bottom:834.010049px;} .y448{bottom:834.688259px;} .y37{bottom:834.829183px;} .ya15{bottom:835.129880px;} .yeed{bottom:836.201273px;} .y831{bottom:836.835727px;} .y839{bottom:836.858949px;} .y842{bottom:836.882172px;} .y1f{bottom:837.474753px;} .y114{bottom:838.474356px;} .y49{bottom:838.477840px;} .ya8a{bottom:838.481891px;} .ya84{bottom:838.494612px;} .ya91{bottom:838.496208px;} .yda{bottom:838.498740px;} .y351{bottom:838.506868px;} .y8e0{bottom:838.574472px;} .y153{bottom:838.610984px;} .y5ad{bottom:838.611242px;} .y2a7{bottom:838.731356px;} .y329{bottom:838.785542px;} .yddd{bottom:839.606986px;} .ye00{bottom:840.752904px;} .y823{bottom:841.026933px;} .yc40{bottom:841.670000px;} .ya36{bottom:843.044740px;} .yc31{bottom:843.066957px;} .ya3e{bottom:843.067963px;} .ya46{bottom:843.091186px;} .yf50{bottom:843.158274px;} .yf7c{bottom:843.274388px;} .yf9b{bottom:843.355668px;} .ye28{bottom:843.445205px;} .ye4e{bottom:843.704785px;} .yd31{bottom:843.931282px;} .yea5{bottom:845.533197px;} .y183{bottom:845.562096px;} .y182{bottom:845.564008px;} .yd08{bottom:846.516426px;} .yc8b{bottom:846.798996px;} .yd32{bottom:846.975683px;} .y57e{bottom:847.005396px;} .ybda{bottom:848.270267px;} .y447{bottom:849.086420px;} .yd72{bottom:849.824133px;} .yeec{bottom:850.875880px;} .y8c1{bottom:851.331682px;} .ya14{bottom:852.864712px;} .yddc{bottom:853.714862px;} .y113{bottom:853.952767px;} .y48{bottom:853.956250px;} .yd9{bottom:853.977151px;} .y2ec{bottom:853.984892px;} .y5ac{bottom:854.089265px;} .y152{bottom:854.089394px;} .y310{bottom:854.124229px;} .y2a6{bottom:854.209379px;} .y8df{bottom:854.249890px;} .y328{bottom:854.263566px;} .ybf6{bottom:854.692930px;} .yaca{bottom:855.831237px;} .ydff{bottom:856.234798px;} .y822{bottom:856.702351px;} .yf4f{bottom:857.347430px;} .yf7b{bottom:857.463544px;} .yf9a{bottom:857.544824px;} .ye27{bottom:858.927099px;} .ye4d{bottom:859.186679px;} .y184{bottom:860.648944px;} .yea4{bottom:861.015091px;} .yc10{bottom:862.352881px;} .yd07{bottom:863.291058px;} .y446{bottom:863.484582px;} .yc30{bottom:863.749838px;} .yeeb{bottom:865.550486px;} .yc79{bottom:865.663555px;} .y57d{bottom:867.131858px;} .yc8a{bottom:867.481878px;} .ycbb{bottom:868.057675px;} .y112{bottom:869.431177px;} .y47{bottom:869.434661px;} .yd8{bottom:869.455561px;} .y2eb{bottom:869.462915px;} .y5ab{bottom:869.567289px;} .y151{bottom:869.567805px;} .y30f{bottom:869.602252px;} .y2a5{bottom:869.687403px;} .y327{bottom:869.741589px;} .yd6d{bottom:869.788293px;} .y8de{bottom:869.925308px;} .ya13{bottom:870.599544px;} .y8c0{bottom:870.680824px;} .yac9{bottom:871.506654px;} .yf4e{bottom:871.536586px;} .yf7a{bottom:871.652700px;} .ydfe{bottom:871.716692px;} .yf99{bottom:871.733980px;} .yb6d{bottom:871.812680px;} .y821{bottom:872.377769px;} .yb6e{bottom:873.209792px;} .ydf9{bottom:874.114967px;} .ye26{bottom:874.408993px;} .ye4c{bottom:874.668573px;} .yea3{bottom:876.496985px;} .y445{bottom:877.882743px;} .yd06{bottom:880.065691px;} .yeea{bottom:880.225092px;} .yd3a{bottom:881.543024px;} .y36{bottom:881.787406px;} .ybd9{bottom:882.330434px;} .yc0f{bottom:883.035763px;} .y15{bottom:883.647556px;} .y111{bottom:884.909588px;} .y46{bottom:884.913072px;} .yd7{bottom:884.933972px;} .y8cd{bottom:884.934617px;} .y2ea{bottom:884.940939px;} .y5aa{bottom:885.045313px;} .y150{bottom:885.046216px;} .y30e{bottom:885.080276px;} .y2a4{bottom:885.165426px;} .y326{bottom:885.219613px;} .y8dd{bottom:885.600726px;} .yf4d{bottom:885.725742px;} .yf79{bottom:885.841856px;} .yf98{bottom:885.923136px;} .ydc4{bottom:886.307861px;} .yc78{bottom:886.346437px;} .yac8{bottom:887.182072px;} .ydfd{bottom:887.198586px;} .y57c{bottom:887.258321px;} .y820{bottom:888.053187px;} .ya11{bottom:888.334377px;} .ya12{bottom:889.361665px;} .ye25{bottom:889.890888px;} .y8be{bottom:890.029967px;} .ye4b{bottom:890.150467px;} .y6{bottom:890.418562px;} .y8bf{bottom:891.057255px;} .ybf4{bottom:891.783291px;} .yea2{bottom:891.978879px;} .y444{bottom:892.280905px;} .yee9{bottom:894.899698px;} .yd39{bottom:896.672040px;} .yd05{bottom:896.840323px;} .y181{bottom:897.867288px;} .yb68{bottom:898.449666px;} .ycb4{bottom:899.161446px;} .ybd8{bottom:899.360517px;} .yb6c{bottom:899.847874px;} .yf4c{bottom:899.914898px;} .yf78{bottom:900.031012px;} .yf97{bottom:900.112292px;} .y110{bottom:900.387999px;} .y45{bottom:900.391482px;} .yd6{bottom:900.412383px;} .y2e9{bottom:900.418963px;} .y5a9{bottom:900.523336px;} .y14f{bottom:900.524627px;} .y30d{bottom:900.558300px;} .y2a3{bottom:900.643450px;} .y325{bottom:900.697637px;} .yc3d{bottom:900.840070px;} .y8dc{bottom:901.276144px;} .ydfc{bottom:902.680480px;} .yac7{bottom:902.857490px;} .ycce{bottom:903.638423px;} .y81f{bottom:903.728605px;} .ycba{bottom:904.330076px;} .yf34{bottom:905.314596px;} .ye24{bottom:905.372782px;} .yc94{bottom:905.528246px;} .ye4a{bottom:905.632361px;} .ya0f{bottom:906.069209px;} .ycc0{bottom:906.643587px;} .y443{bottom:906.679067px;} .ya10{bottom:907.096497px;} .yea1{bottom:907.460773px;} .yd6c{bottom:907.529006px;} .ycc6{bottom:907.819437px;} .ycdf{bottom:909.129205px;} .y8bc{bottom:909.379109px;} .yee8{bottom:909.574305px;} .y8bd{bottom:910.406397px;} .ycd9{bottom:910.562313px;} .yd38{bottom:911.801055px;} .yddb{bottom:913.014387px;} .yd04{bottom:913.614955px;} .ya26{bottom:915.097088px;} .y44{bottom:915.869893px;} .yd5{bottom:915.890794px;} .y2e8{bottom:915.896986px;} .y5a8{bottom:916.001360px;} .y14e{bottom:916.003037px;} .y30c{bottom:916.036323px;} .y2a2{bottom:916.121474px;} .y324{bottom:916.175660px;} .yc18{bottom:920.126124px;} .ye23{bottom:920.854676px;} .y442{bottom:921.077228px;} .ye49{bottom:921.114256px;} .yea0{bottom:922.942667px;} .yc83{bottom:923.436798px;} .y2{bottom:923.883063px;} .yd6b{bottom:923.939217px;} .yb67{bottom:924.247984px;} .yee7{bottom:924.248911px;} .ydc2{bottom:925.168190px;} .yb6a{bottom:925.646193px;} .yd37{bottom:926.930070px;} .ydda{bottom:927.203543px;} .ybf3{bottom:928.068980px;} .yb6b{bottom:928.141036px;} .ydcf{bottom:929.874169px;} .y14{bottom:930.322499px;} .ycb0{bottom:930.381330px;} .yd03{bottom:930.389587px;} .y81c{bottom:930.627234px;} .y8ea{bottom:930.959708px;} .y10f{bottom:931.351787px;} .yd4{bottom:931.369204px;} .y2e7{bottom:931.375010px;} .y5a7{bottom:931.479384px;} .y14d{bottom:931.481448px;} .y30b{bottom:931.514347px;} .y2a1{bottom:931.599497px;} .y323{bottom:931.653684px;} .yad2{bottom:932.541055px;} .yfc9{bottom:932.821664px;} .ycf0{bottom:933.700003px;} .ycd5{bottom:933.913266px;} .yc9c{bottom:934.230774px;} .yf35{bottom:934.615370px;} .y441{bottom:935.475390px;} .ycca{bottom:936.696653px;} .yc3c{bottom:937.125759px;} .yc9d{bottom:937.561317px;} .y430{bottom:938.314511px;} .yee6{bottom:938.923517px;} .ycdb{bottom:939.439529px;} .yd6a{bottom:940.349428px;} .ycc4{bottom:941.013650px;} .ydd9{bottom:941.392699px;} .yce1{bottom:941.461851px;} .yc93{bottom:941.813935px;} .yd36{bottom:942.059086px;} .ybd7{bottom:943.012492px;} .yec0{bottom:944.200598px;} .y7{bottom:944.340709px;} .yf47{bottom:945.047587px;} .y585{bottom:946.077391px;} .yd3{bottom:946.847615px;} .y2e6{bottom:946.853034px;} .y5a6{bottom:946.957407px;} .y14c{bottom:946.959859px;} .y30a{bottom:946.992371px;} .y322{bottom:947.131708px;} .yd02{bottom:947.164220px;} .ycef{bottom:947.893030px;} .ybd6{bottom:948.619776px;} .ycb9{bottom:948.915093px;} .y440{bottom:949.873551px;} .yb66{bottom:950.046303px;} .yb69{bottom:951.444512px;} .ye22{bottom:952.522503px;} .ye42{bottom:952.781825px;} .yee5{bottom:953.598123px;} .ydce{bottom:955.677326px;} .yc17{bottom:956.411813px;} .yd69{bottom:956.759640px;} .y0{bottom:956.941939px;} .yd35{bottom:957.188101px;} .ya7c{bottom:957.433360px;} .y8bb{bottom:958.860597px;} .ycab{bottom:959.462133px;} .yca3{bottom:959.499161px;} .yca6{bottom:959.549735px;} .yc82{bottom:959.722487px;} .ycaf{bottom:961.603150px;} .ycee{bottom:962.086056px;} .y10e{bottom:962.315575px;} .yd2{bottom:962.326026px;} .y2e5{bottom:962.331057px;} .y5a5{bottom:962.435431px;} .y14b{bottom:962.438269px;} .y309{bottom:962.470394px;} .y2a0{bottom:962.567156px;} .y321{bottom:962.609731px;} .ydf8{bottom:963.013809px;} .y8db{bottom:963.746360px;} .yf44{bottom:963.779388px;} .yd01{bottom:963.938852px;} .y43f{bottom:964.271713px;} .yf1c{bottom:964.578899px;} .yf1b{bottom:964.579028px;} .yf0e{bottom:964.630376px;} .yf45{bottom:964.928274px;} .yc9a{bottom:965.306419px;} .yac6{bottom:965.327578px;} .yb25{bottom:966.690888px;} .y81d{bottom:967.373123px;} .y81e{bottom:967.373252px;} .yee4{bottom:968.272729px;} .y8ec{bottom:968.531538px;} .y9cf{bottom:968.794490px;} .yad3{bottom:968.954470px;} .y5{bottom:969.134834px;} .yf43{bottom:969.201664px;} .yebf{bottom:970.003755px;} .y9ad{bottom:970.360208px;} .yf46{bottom:971.544590px;} .ybf2{bottom:971.611808px;} .y81b{bottom:973.261274px;} .yd67{bottom:973.692316px;} .yb49{bottom:973.704573px;} .yd96{bottom:974.227474px;} .yf0c{bottom:975.661553px;} .yd68{bottom:975.809465px;} .y698{bottom:976.480734px;} .y625{bottom:976.492217px;} .yd30{bottom:976.713995px;} .ycd2{bottom:977.357397px;} .yb88{bottom:977.398940px;} .y774{bottom:977.654778px;} .y10d{bottom:977.797469px;} .y626{bottom:977.800953px;} .yd1{bottom:977.804436px;} .y2e4{bottom:977.809081px;} .y5a4{bottom:977.913455px;} .y14a{bottom:977.916680px;} .y308{bottom:977.948418px;} .y29f{bottom:978.045180px;} .ybd5{bottom:978.087239px;} .y320{bottom:978.087755px;} .y57b{bottom:978.176131px;} .ye21{bottom:978.325660px;} .ycc8{bottom:978.559824px;} .ye41{bottom:978.584982px;} .y43e{bottom:978.669874px;} .ya7a{bottom:979.364809px;} .ya7b{bottom:979.366043px;} .y82c{bottom:979.504219px;} .y93b{bottom:979.764556px;} .y431{bottom:980.065696px;} .yb64{bottom:980.491964px;} .y43{bottom:980.575824px;} .yc3b{bottom:980.668587px;} .yd00{bottom:980.713484px;} .ya30{bottom:980.793142px;} .ycda{bottom:981.302699px;} .yb65{bottom:981.901462px;} .yceb{bottom:982.154332px;} .yda8{bottom:982.255610px;} .yee3{bottom:982.947336px;} .yce0{bottom:983.238581px;} .ycc2{bottom:983.288768px;} .yc92{bottom:985.356762px;} .ydcd{bottom:986.641114px;} .y8ba{bottom:987.236006px;} .ycf5{bottom:987.765229px;} .yca5{bottom:988.163501px;} .yc9b{bottom:988.929854px;} .yca0{bottom:989.320643px;} .y881{bottom:990.918744px;} .y8eb{bottom:991.755687px;} .y9ce{bottom:992.017331px;} .yb26{bottom:992.669893px;} .y43d{bottom:993.068036px;} .yd0{bottom:993.282847px;} .y2e3{bottom:993.287104px;} .y5a3{bottom:993.391478px;} .y149{bottom:993.395091px;} .y307{bottom:993.426442px;} .y29e{bottom:993.523203px;} .y31f{bottom:993.565779px;} .y9ac{bottom:993.584357px;} .yb0a{bottom:994.898770px;} .y81a{bottom:995.026237px;} .y624{bottom:995.470439px;} .yb48{bottom:995.637256px;} .yad5{bottom:996.420253px;} .yee2{bottom:997.621942px;} .y697{bottom:998.374713px;} .yd97{bottom:999.026888px;} .ycae{bottom:999.069334px;} .yc16{bottom:999.954640px;} .ydb7{bottom:1000.515988px;} .yebe{bottom:1000.967543px;} .ya79{bottom:1001.298727px;} .y82b{bottom:1002.727060px;} .y93a{bottom:1002.988704px;} .yc81{bottom:1003.265314px;} .y25f{bottom:1004.871432px;} .y43c{bottom:1007.466197px;} .ycf{bottom:1008.761258px;} .y2e2{bottom:1008.765128px;} .y5a2{bottom:1008.869502px;} .y148{bottom:1008.873501px;} .y306{bottom:1008.904465px;} .y29d{bottom:1009.001227px;} .y31e{bottom:1009.043802px;} .ye20{bottom:1009.289448px;} .ye40{bottom:1009.548770px;} .ye8d{bottom:1009.556511px;} .y13{bottom:1010.500132px;} .yee0{bottom:1012.296548px;} .y3d9{bottom:1012.854025px;} .yee1{bottom:1013.637893px;} .y880{bottom:1014.142893px;} .ycad{bottom:1014.434340px;} .y819{bottom:1015.746172px;} .y1{bottom:1016.353837px;} .ycff{bottom:1017.222629px;} .y25e{bottom:1018.931959px;} .ybf5{bottom:1021.788755px;} .y2e1{bottom:1024.243152px;} .y305{bottom:1024.382489px;} .y29c{bottom:1024.479251px;} .y31d{bottom:1024.521826px;} .yd93{bottom:1024.533179px;} .ycfe{bottom:1025.046275px;} .ydcb{bottom:1025.060338px;} .ycb6{bottom:1025.228187px;} .yce8{bottom:1025.907068px;} .yd2e{bottom:1028.519509px;} .ycb7{bottom:1030.511384px;} .y25d{bottom:1030.543380px;} .ycfd{bottom:1031.863598px;} .ycea{bottom:1032.039318px;} .ycb8{bottom:1032.788641px;} .yd2f{bottom:1033.024095px;} .ydcc{bottom:1034.791353px;} .yedf{bottom:1041.057650px;} .yccc{bottom:1045.784143px;} .ycd0{bottom:1046.698478px;} .ycfc{bottom:1047.341622px;} .yccd{bottom:1047.427804px;} .yce9{bottom:1047.517341px;} .ycd1{bottom:1048.342139px;} .y704{bottom:1051.708677px;} .y34a{bottom:1051.715386px;} .y22e{bottom:1052.629850px;} .ye6c{bottom:1052.630237px;} .ye3f{bottom:1052.636559px;} .ycbf{bottom:1054.273511px;} .y4{bottom:1067.395835px;} .y3{bottom:1077.717098px;} .y10{bottom:1079.599954px;} .h4{height:21.328125px;} .h9{height:22.308119px;} .h6f{height:23.007639px;} .h1d{height:25.470703px;} .h68{height:25.839844px;} .h1c{height:26.369170px;} .h79{height:26.500000px;} .h20{height:27.029297px;} .h14{height:28.354569px;} .h40{height:28.813477px;} .h50{height:28.911677px;} .h2d{height:29.109375px;} .h47{height:29.548667px;} .h82{height:30.365081px;} .h32{height:30.928711px;} .h13{height:31.384976px;} .h11{height:31.656445px;} .h33{height:32.020313px;} .h3b{height:32.625000px;} .h19{height:32.748047px;} .h2e{height:32.929688px;} .h7{height:32.957623px;} .h3f{height:33.308105px;} .h51{height:34.352620px;} .h43{height:34.437500px;} .h1e{height:34.751953px;} .h4f{height:34.933594px;} .h42{height:35.741413px;} .h8{height:36.250000px;} .h8b{height:36.283301px;} .h38{height:36.703125px;} .h8d{height:36.814050px;} .h7a{height:36.917969px;} .h53{height:37.710937px;} .h30{height:38.066406px;} .h7b{height:38.109375px;} .h73{height:38.295950px;} .h6e{height:38.437751px;} .h12{height:38.613281px;} .h41{height:39.150000px;} .h18{height:39.281250px;} .h6d{height:39.875000px;} .h77{height:40.167969px;} .h8c{height:41.415625px;} .h28{height:41.462891px;} .h8e{height:41.532713px;} .h2c{height:42.351562px;} .h7c{height:42.474609px;} .h4b{height:43.666992px;} .h44{height:43.842983px;} .h3{height:43.943285px;} .h39{height:44.043750px;} .he{height:44.044837px;} .h78{height:44.405273px;} .h1a{height:44.460938px;} .h3a{height:44.731832px;} .h4e{height:45.731250px;} .h17{height:46.335937px;} .h7e{height:46.453708px;} .h83{height:47.636719px;} .h58{height:48.427825px;} .h67{height:49.146809px;} .hd{height:49.265895px;} .ha{height:49.518846px;} .h1b{height:50.197266px;} .h63{height:50.750000px;} .h64{height:51.679688px;} .h35{height:52.941312px;} .h3c{height:53.149999px;} .h89{height:53.796457px;} .h1f{height:54.058594px;} .h6a{height:54.375000px;} .h46{height:55.484074px;} .h6{height:56.566406px;} .h85{height:56.601562px;} .h54{height:57.164062px;} .h81{height:57.877739px;} .h21{height:57.919922px;} .h5c{height:59.214375px;} .h7d{height:60.251953px;} .h52{height:62.851562px;} .hb{height:64.518537px;} .h5e{height:65.793750px;} .hf{height:66.469102px;} .h55{height:66.989295px;} .h3e{height:67.485352px;} .h66{height:68.906250px;} .h27{height:69.750000px;} .h87{height:69.867188px;} .h74{height:71.043291px;} .h69{height:73.042969px;} .h25{height:73.675000px;} .h45{height:75.066894px;} .h86{height:75.468750px;} .h15{height:76.174737px;} .h62{height:76.218750px;} .h26{height:77.500000px;} .h84{height:79.242188px;} .h2a{height:79.500000px;} .h5a{height:79.543793px;} .h57{height:79.596136px;} .h4a{height:80.185547px;} .h72{height:82.350866px;} .h71{height:82.570312px;} .h6b{height:86.789062px;} .h5f{height:88.381992px;} .h3d{height:91.303711px;} .h2{height:94.570320px;} .h65{height:100.488281px;} .h56{height:102.716834px;} .h61{height:102.823916px;} .h60{height:102.841007px;} .h16{height:104.255859px;} .h31{height:108.117188px;} .h24{height:108.562500px;} .h8a{height:109.509759px;} .h88{height:109.509888px;} .h48{height:115.757227px;} .h34{height:119.701172px;} .h59{height:122.047308px;} .h2b{height:123.672226px;} .h80{height:127.332949px;} .h76{height:128.619141px;} .h22{height:130.275000px;} .h70{height:130.550968px;} .h4d{height:131.564941px;} .h37{height:132.906445px;} .h2f{height:133.215820px;} .h29{height:138.042480px;} .h10{height:142.910156px;} .h6c{height:150.158559px;} .h4c{height:153.093750px;} .h36{height:154.342969px;} .h5d{height:158.789062px;} .h7f{height:165.628107px;} .h75{height:172.422374px;} .h5b{height:174.377751px;} .h49{height:183.389062px;} .h5{height:215.456115px;} .hc{height:226.926720px;} .h23{height:284.175000px;} .h1{height:287.274820px;} .h0{height:1086.170986px;} .w2{width:154.028074px;} .w4{width:297.663927px;} .w1{width:448.409840px;} .w3{width:767.998710px;} .w0{width:768.000000px;} .x7{left:-767.999484px;} .xe1{left:-223.085579px;} .x3{left:-0.000129px;} .x9{left:6.626767px;} .xb{left:9.908799px;} .x53{left:29.257167px;} .x26{left:31.246333px;} .x9f{left:32.458307px;} .x3a{left:33.469017px;} .x17{left:34.742790px;} .x0{left:36.571330px;} .x6{left:38.400000px;} .x66{left:39.766793px;} .xcb{left:40.850526px;} .x2{left:42.057081px;} .x69{left:43.477803px;} .x50{left:44.532507px;} .x22{left:46.445682px;} .x7c{left:47.924590px;} .x4{left:49.466071px;} .x54{left:50.479619px;} .x25{left:52.418984px;} .x5{left:53.580384px;} .x42{left:55.776620px;} .x52{left:57.847839px;} .x64{left:58.944990px;} .x6b{left:60.683348px;} .xa6{left:61.999438px;} .x1c{left:63.634197px;} .x38{left:66.204321px;} .x90{left:67.669037px;} .xbb{left:72.239421px;} .x97{left:74.971330px;} .xb0{left:76.254134px;} .x9b{left:77.531390px;} .x21{left:80.383026px;} .x37{left:83.698861px;} .xe4{left:84.845682px;} .x71{left:94.378917px;} .x98{left:98.742747px;} .xb9{left:100.978461px;} .xa5{left:117.073567px;} .xc2{left:118.756578px;} .xa4{left:120.915270px;} .xc7{left:122.443075px;} .xc4{left:124.227621px;} .x6f{left:127.025587px;} .x9d{left:129.218984px;} .xc3{left:132.806010px;} .xc8{left:136.492507px;} .xc5{left:138.277053px;} .x2f{left:145.866923px;} .x30{left:150.558453px;} .x31{left:156.845263px;} .xa7{left:157.910804px;} .xe3{left:167.670203px;} .xd6{left:174.722052px;} .x5d{left:176.992755px;} .xa8{left:178.579133px;} .xd7{left:179.879204px;} .x7d{left:182.429351px;} .x9e{left:185.338536px;} .x7e{left:187.836725px;} .x81{left:193.622761px;} .x56{left:196.089026px;} .xc0{left:197.323062px;} .x57{left:200.234303px;} .xae{left:206.847911px;} .xd3{left:212.948938px;} .x8a{left:216.978165px;} .x85{left:218.209428px;} .x76{left:219.774647px;} .x8b{left:222.385539px;} .xc1{left:227.187894px;} .x6a{left:228.869486px;} .x7f{left:231.039273px;} .x8f{left:233.452255px;} .x80{left:236.446647px;} .xd1{left:245.368024px;} .x6c{left:248.157797px;} .xbd{left:249.599871px;} .xd2{left:250.929895px;} .x6d{left:253.565171px;} .x46{left:255.999828px;} .x1e{left:258.437968px;} .x8c{left:264.707555px;} .x68{left:265.725038px;} .x75{left:268.001263px;} .x18{left:273.068874px;} .x29{left:274.280462px;} .x67{left:276.256596px;} .xcc{left:277.279691px;} .x59{left:278.464185px;} .x5a{left:283.871559px;} .x73{left:286.998450px;} .xe8{left:288.976004px;} .x79{left:292.049934px;} .x65{left:293.112379px;} .x5b{left:295.995818px;} .x78{left:299.775013px;} .x5c{left:301.403192px;} .xd4{left:306.165422px;} .x96{left:308.312245px;} .x77{left:309.587179px;} .xd0{left:315.579575px;} .x8{left:319.590160px;} .x32{left:322.745886px;} .xb5{left:325.485407px;} .xda{left:329.734671px;} .xdc{left:346.404800px;} .x33{left:355.593305px;} .x2d{left:358.114402px;} .xba{left:361.459007px;} .xd{left:362.902178px;} .xa1{left:365.714251px;} .xc{left:372.662222px;} .x16{left:374.468907px;} .x15{left:375.576030px;} .x13{left:377.655262px;} .x14{left:378.897400px;} .xdb{left:380.004381px;} .x3e{left:384.700685px;} .x3c{left:386.075090px;} .xce{left:388.875894px;} .x3d{left:391.764686px;} .x61{left:393.752045px;} .xd8{left:397.104520px;} .xb7{left:399.990345px;} .x34{left:401.135876px;} .xb6{left:403.502155px;} .xe9{left:405.101951px;} .x7b{left:409.198460px;} .x63{left:413.030616px;} .x99{left:418.742661px;} .x6e{left:420.566944px;} .xbf{left:431.864340px;} .x55{left:436.190110px;} .xe2{left:438.610575px;} .x23{left:440.075937px;} .xe5{left:441.158895px;} .xe{left:442.683475px;} .x83{left:444.462473px;} .x82{left:446.564575px;} .xe6{left:453.921394px;} .x91{left:455.352696px;} .x94{left:458.871988px;} .x5e{left:460.989524px;} .xe7{left:468.110937px;} .xb2{left:473.569724px;} .x3f{left:477.236998px;} .x87{left:480.437622px;} .x86{left:482.137017px;} .xf{left:484.112907px;} .xa3{left:486.172373px;} .x84{left:488.157539px;} .x10{left:491.257983px;} .x27{left:492.949701px;} .x19{left:494.932932px;} .x93{left:496.778116px;} .x36{left:499.953968px;} .xb8{left:501.867014px;} .x5f{left:503.208649px;} .x1a{left:509.563967px;} .x39{left:511.989335px;} .xcd{left:513.708857px;} .x89{left:522.373170px;} .x7a{left:524.123338px;} .xbe{left:527.344922px;} .x35{left:529.354085px;} .x11{left:535.689548px;} .x12{left:544.115534px;} .x44{left:546.617945px;} .xa0{left:552.859858px;} .x92{left:558.986689px;} .x4f{left:560.163312px;} .xb3{left:566.499794px;} .x4d{left:567.501343px;} .xa2{left:568.906327px;} .x8d{left:569.987090px;} .xa9{left:571.760928px;} .x4b{left:579.674757px;} .xac{left:581.412470px;} .xa{left:584.713726px;} .xcf{left:586.545105px;} .x43{left:587.657866px;} .xbc{left:591.002859px;} .x8e{left:592.462156px;} .x24{left:595.498672px;} .xab{left:596.925328px;} .x74{left:598.667557px;} .x48{left:601.453524px;} .x62{left:604.744459px;} .x58{left:605.763167px;} .xaf{left:614.034756px;} .xb4{left:615.086235px;} .x88{left:617.677904px;} .x4c{left:624.332796px;} .x4e{left:625.535610px;} .x70{left:627.566061px;} .x4a{left:630.107027px;} .xde{left:631.659474px;} .x49{left:633.599484px;} .xc9{left:638.932351px;} .x2c{left:640.620652px;} .x45{left:642.805405px;} .x47{left:644.015831px;} .xd9{left:647.003192px;} .x1f{left:650.239553px;} .x60{left:652.995975px;} .x51{left:656.735368px;} .x1{left:659.116355px;} .xd5{left:661.028111px;} .xe0{left:663.057587px;} .x72{left:664.072367px;} .x95{left:668.982450px;} .xc6{left:670.929298px;} .x2e{left:677.464335px;} .x9c{left:680.171602px;} .x1d{left:682.046330px;} .x9a{left:686.343201px;} .xaa{left:690.185033px;} .xb1{left:691.856561px;} .x40{left:694.176136px;} .xad{left:695.259482px;} .xca{left:699.670660px;} .xdf{left:717.706809px;} .xdd{left:719.275641px;} .x41{left:721.261581px;} .x3b{left:722.799320px;} .x2b{left:724.567481px;} .x20{left:726.229721px;} .x1b{left:731.428025px;} .x28{left:743.474357px;} .x2a{left:744.485841px;} @media print{ .v0{vertical-align:0.000000pt;} .ls40{letter-spacing:-7.254926pt;} .ls50{letter-spacing:-5.859748pt;} .ls56{letter-spacing:-5.801151pt;} .ls39{letter-spacing:-4.018113pt;} .ls3e{letter-spacing:-3.865160pt;} .ls5f{letter-spacing:-3.817207pt;} .ls7{letter-spacing:-3.374347pt;} .ls23{letter-spacing:-2.955711pt;} .ls18{letter-spacing:-2.678742pt;} .ls6{letter-spacing:-2.509130pt;} .ls4c{letter-spacing:-2.036700pt;} .ls24{letter-spacing:-1.984253pt;} .ls41{letter-spacing:-1.860238pt;} .ls4{letter-spacing:-1.859729pt;} .ls4f{letter-spacing:-1.674214pt;} .ls45{letter-spacing:-1.593279pt;} .ls2c{letter-spacing:-1.463387pt;} .ls43{letter-spacing:-1.338664pt;} .ls2e{letter-spacing:-1.184746pt;} .ls47{letter-spacing:-1.071947pt;} .ls2d{letter-spacing:-1.054135pt;} .lsc{letter-spacing:-1.004528pt;} .lsf{letter-spacing:-0.992127pt;} .ls3a{letter-spacing:-0.980479pt;} .ls22{letter-spacing:-0.967324pt;} .lsd{letter-spacing:-0.781300pt;} .ls5a{letter-spacing:-0.776213pt;} .ls57{letter-spacing:-0.750513pt;} .ls2f{letter-spacing:-0.744095pt;} .ls34{letter-spacing:-0.702756pt;} .ls54{letter-spacing:-0.694489pt;} .ls5{letter-spacing:-0.641286pt;} .ls2{letter-spacing:-0.590773pt;} .ls3f{letter-spacing:-0.564508pt;} .ls35{letter-spacing:-0.545670pt;} .ls5d{letter-spacing:-0.532830pt;} .ls52{letter-spacing:-0.520867pt;} .ls5c{letter-spacing:-0.472294pt;} .ls32{letter-spacing:-0.467540pt;} .lsa{letter-spacing:-0.413386pt;} .ls3c{letter-spacing:-0.407586pt;} .ls3d{letter-spacing:-0.392717pt;} .ls26{letter-spacing:-0.372048pt;} .ls38{letter-spacing:-0.363780pt;} .ls9{letter-spacing:-0.359646pt;} .ls1e{letter-spacing:-0.357166pt;} .ls36{letter-spacing:-0.351378pt;} .ls51{letter-spacing:-0.347244pt;} .ls53{letter-spacing:-0.330709pt;} .lsb{letter-spacing:-0.244653pt;} .ls59{letter-spacing:-0.232530pt;} .ls55{letter-spacing:-0.231496pt;} .ls5b{letter-spacing:-0.204266pt;} .ls3b{letter-spacing:-0.186024pt;} .ls1d{letter-spacing:-0.158740pt;} .ls1f{letter-spacing:-0.132284pt;} .ls14{letter-spacing:-0.099213pt;} .ls20{letter-spacing:-0.092598pt;} .ls21{letter-spacing:-0.082677pt;} .ls28{letter-spacing:-0.074410pt;} .ls3{letter-spacing:-0.064129pt;} .ls0{letter-spacing:0.000000pt;} .ls2a{letter-spacing:0.053740pt;} .ls25{letter-spacing:0.186024pt;} .ls49{letter-spacing:0.218359pt;} .ls2b{letter-spacing:0.223229pt;} .lse{letter-spacing:0.244653pt;} .ls27{letter-spacing:0.260433pt;} .ls4d{letter-spacing:0.305702pt;} .ls11{letter-spacing:0.372048pt;} .ls4a{letter-spacing:0.393046pt;} .ls58{letter-spacing:0.405118pt;} .ls17{letter-spacing:0.429922pt;} .ls1c{letter-spacing:0.446457pt;} .ls1a{letter-spacing:0.483662pt;} .ls1b{letter-spacing:0.520867pt;} .ls16{letter-spacing:0.537402pt;} .ls61{letter-spacing:0.549804pt;} .ls13{letter-spacing:0.558071pt;} .ls4e{letter-spacing:0.567733pt;} .ls42{letter-spacing:0.578741pt;} .ls10{letter-spacing:0.595276pt;} .ls60{letter-spacing:0.607678pt;} .ls12{letter-spacing:0.632481pt;} .ls19{letter-spacing:0.706890pt;} .ls5e{letter-spacing:0.752363pt;} .ls29{letter-spacing:0.781300pt;} .ls4b{letter-spacing:0.786092pt;} .ls30{letter-spacing:0.826772pt;} .ls48{letter-spacing:1.004451pt;} .ls15{letter-spacing:1.157481pt;} .ls1{letter-spacing:1.679654pt;} .ls44{letter-spacing:1.984253pt;} .ls8{letter-spacing:2.066931pt;} .ls33{letter-spacing:2.314962pt;} .ls37{letter-spacing:2.562994pt;} .ls31{letter-spacing:2.852364pt;} .ls46{letter-spacing:3.398720pt;} .ws54a{word-spacing:-19.654602pt;} .ws57a{word-spacing:-13.691348pt;} .ws1e0{word-spacing:-7.961817pt;} .ws331{word-spacing:-7.732387pt;} .ws57b{word-spacing:-7.701383pt;} .ws560{word-spacing:-7.686230pt;} .ws54b{word-spacing:-6.818944pt;} .ws2e7{word-spacing:-6.250398pt;} .ws4bc{word-spacing:-5.989965pt;} .wsff{word-spacing:-5.208665pt;} .ws312{word-spacing:-4.911027pt;} .wsdd{word-spacing:-4.855220pt;} .ws1c1{word-spacing:-4.576184pt;} .ws29d{word-spacing:-4.538980pt;} .ws4ce{word-spacing:-4.204137pt;} .ws28b{word-spacing:-4.129727pt;} .ws2c9{word-spacing:-3.980908pt;} .ws4b7{word-spacing:-3.869294pt;} .ws3c6{word-spacing:-3.856066pt;} .ws41b{word-spacing:-3.759747pt;} .ws324{word-spacing:-3.757680pt;} .wsd9{word-spacing:-3.704353pt;} .ws2de{word-spacing:-3.683270pt;} .ws1e6{word-spacing:-3.534451pt;} .ws4b6{word-spacing:-3.515849pt;} .ws282{word-spacing:-3.497247pt;} .ws585{word-spacing:-3.465622pt;} .ws4c4{word-spacing:-3.460042pt;} .ws1d8{word-spacing:-3.422837pt;} .ws555{word-spacing:-3.398720pt;} .ws3e4{word-spacing:-3.346774pt;} .ws204{word-spacing:-3.274018pt;} .ws468{word-spacing:-3.237640pt;} .wsdf{word-spacing:-3.200849pt;} .ws1fc{word-spacing:-3.199609pt;} .ws3cb{word-spacing:-3.164884pt;} .ws2f9{word-spacing:-3.125199pt;} .ws2da{word-spacing:-3.087994pt;} .ws442{word-spacing:-3.021852pt;} .ws471{word-spacing:-3.019372pt;} .ws413{word-spacing:-2.910238pt;} .ws2c7{word-spacing:-2.864766pt;} .ws4ac{word-spacing:-2.852364pt;} .ws2f5{word-spacing:-2.827561pt;} .ws106{word-spacing:-2.790356pt;} .ws13f{word-spacing:-2.715947pt;} .ws1de{word-spacing:-2.678742pt;} .ws41f{word-spacing:-2.670474pt;} .ws562{word-spacing:-2.662207pt;} .ws17a{word-spacing:-2.641537pt;} .ws33a{word-spacing:-2.625415pt;} .ws10e{word-spacing:-2.567128pt;} .ws287{word-spacing:-2.492718pt;} .ws105{word-spacing:-2.455514pt;} .ws15e{word-spacing:-2.381104pt;} .wsf9{word-spacing:-2.343899pt;} .ws10b{word-spacing:-2.306695pt;} .wsfc{word-spacing:-2.269490pt;} .ws4d2{word-spacing:-2.260189pt;} .ws3eb{word-spacing:-2.255435pt;} .ws359{word-spacing:-2.229805pt;} .ws30d{word-spacing:-2.195080pt;} .ws229{word-spacing:-2.157876pt;} .ws50c{word-spacing:-2.119449pt;} .ws499{word-spacing:-2.109923pt;} .ws285{word-spacing:-2.083466pt;} .ws1c2{word-spacing:-2.046261pt;} .ws3d6{word-spacing:-2.037167pt;} .ws572{word-spacing:-2.025592pt;} .ws326{word-spacing:-2.009057pt;} .ws421{word-spacing:-2.002856pt;} .ws33d{word-spacing:-1.978053pt;} .ws1cf{word-spacing:-1.971852pt;} .ws516{word-spacing:-1.956414pt;} .ws23c{word-spacing:-1.934647pt;} .ws2d2{word-spacing:-1.897442pt;} .ws66{word-spacing:-1.870159pt;} .ws288{word-spacing:-1.823033pt;} .ws81{word-spacing:-1.798230pt;} .ws322{word-spacing:-1.785828pt;} .ws40c{word-spacing:-1.782521pt;} .ws65{word-spacing:-1.762265pt;} .ws184{word-spacing:-1.748623pt;} .ws67{word-spacing:-1.726300pt;} .ws42c{word-spacing:-1.721753pt;} .ws402{word-spacing:-1.709765pt;} .ws1ba{word-spacing:-1.674214pt;} .ws17{word-spacing:-1.654371pt;} .ws22d{word-spacing:-1.649411pt;} .ws4bf{word-spacing:-1.637009pt;} .ws4d6{word-spacing:-1.630345pt;} .ws2c{word-spacing:-1.618407pt;} .ws37c{word-spacing:-1.616340pt;} .ws4ab{word-spacing:-1.600631pt;} .ws239{word-spacing:-1.599804pt;} .ws19d{word-spacing:-1.591537pt;} .ws12f{word-spacing:-1.587403pt;} .ws15b{word-spacing:-1.562600pt;} .ws71{word-spacing:-1.546477pt;} .ws3ac{word-spacing:-1.546064pt;} .ws1ec{word-spacing:-1.533662pt;} .ws3e8{word-spacing:-1.527875pt;} .ws165{word-spacing:-1.525395pt;} .ws380{word-spacing:-1.510926pt;} .ws80{word-spacing:-1.510513pt;} .ws46c{word-spacing:-1.491497pt;} .ws15f{word-spacing:-1.488190pt;} .ws273{word-spacing:-1.475788pt;} .wsa9{word-spacing:-1.474548pt;} .ws521{word-spacing:-1.464937pt;} .ws30a{word-spacing:-1.463387pt;} .ws3db{word-spacing:-1.455119pt;} .ws17e{word-spacing:-1.450985pt;} .ws41a{word-spacing:-1.440651pt;} .wsde{word-spacing:-1.438584pt;} .ws4d7{word-spacing:-1.426552pt;} .ws173{word-spacing:-1.413781pt;} .wsaf{word-spacing:-1.402619pt;} .ws52{word-spacing:-1.366654pt;} .ws3ec{word-spacing:-1.345985pt;} .ws50b{word-spacing:-1.345035pt;} .ws4cd{word-spacing:-1.339371pt;} .ws42d{word-spacing:-1.335237pt;} .ws8b{word-spacing:-1.330690pt;} .ws1e3{word-spacing:-1.302166pt;} .ws2b{word-spacing:-1.294725pt;} .ws151{word-spacing:-1.264962pt;} .ws70{word-spacing:-1.258761pt;} .ws4ae{word-spacing:-1.227757pt;} .ws46d{word-spacing:-1.200473pt;} .ws2d3{word-spacing:-1.190552pt;} .ws24e{word-spacing:-1.186418pt;} .ws537{word-spacing:-1.182000pt;} .ws492{word-spacing:-1.164095pt;} .ws178{word-spacing:-1.157481pt;} .ws115{word-spacing:-1.153347pt;} .ws7c{word-spacing:-1.150867pt;} .ws3f7{word-spacing:-1.127717pt;} .ws571{word-spacing:-1.124410pt;} .ws22c{word-spacing:-1.116143pt;} .wsac{word-spacing:-1.114902pt;} .ws438{word-spacing:-1.089272pt;} .ws9f{word-spacing:-1.078938pt;} .ws56a{word-spacing:-1.058268pt;} .ws44f{word-spacing:-1.054135pt;} .wsbb{word-spacing:-1.042973pt;} .ws14e{word-spacing:-1.041733pt;} .ws47e{word-spacing:-1.018583pt;} .ws1ee{word-spacing:-1.004528pt;} .ws558{word-spacing:-1.004451pt;} .ws41d{word-spacing:-0.983859pt;} .ws10d{word-spacing:-0.967324pt;} .ws365{word-spacing:-0.948721pt;} .ws3c9{word-spacing:-0.945827pt;} .ws52d{word-spacing:-0.937448pt;} .wse{word-spacing:-0.935079pt;} .ws163{word-spacing:-0.930119pt;} .ws376{word-spacing:-0.913583pt;} .ws346{word-spacing:-0.899115pt;} .ws511{word-spacing:-0.896690pt;} .ws232{word-spacing:-0.892914pt;} .ws41e{word-spacing:-0.878445pt;} .ws47a{word-spacing:-0.873071pt;} .ws83{word-spacing:-0.863150pt;} .ws29b{word-spacing:-0.855709pt;} .ws47b{word-spacing:-0.836693pt;} .ws332{word-spacing:-0.827186pt;} .ws35f{word-spacing:-0.826772pt;} .ws2fa{word-spacing:-0.818505pt;} .ws515{word-spacing:-0.815173pt;} .ws424{word-spacing:-0.808170pt;} .ws48a{word-spacing:-0.800316pt;} .wse0{word-spacing:-0.791221pt;} .ws55d{word-spacing:-0.786092pt;} .ws1ae{word-spacing:-0.781300pt;} .ws445{word-spacing:-0.773032pt;} .ws64{word-spacing:-0.755256pt;} .ws583{word-spacing:-0.752363pt;} .ws2c6{word-spacing:-0.744095pt;} .ws371{word-spacing:-0.737894pt;} .ws177{word-spacing:-0.706890pt;} .ws38a{word-spacing:-0.702756pt;} .ws5c{word-spacing:-0.683327pt;} .ws28e{word-spacing:-0.669686pt;} .ws501{word-spacing:-0.667619pt;} .ws272{word-spacing:-0.644882pt;} .ws107{word-spacing:-0.632481pt;} .ws31{word-spacing:-0.611398pt;} .ws586{word-spacing:-0.607678pt;} .ws155{word-spacing:-0.595276pt;} .ws54e{word-spacing:-0.578741pt;} .wsd6{word-spacing:-0.575433pt;} .ws417{word-spacing:-0.570473pt;} .ws1c6{word-spacing:-0.558071pt;} .ws587{word-spacing:-0.549804pt;} .ws6f{word-spacing:-0.539469pt;} .ws4d0{word-spacing:-0.535748pt;} .ws1c7{word-spacing:-0.520867pt;} .wsa6{word-spacing:-0.503504pt;} .ws12e{word-spacing:-0.496063pt;} .ws1c5{word-spacing:-0.483662pt;} .ws344{word-spacing:-0.467540pt;} .ws458{word-spacing:-0.456792pt;} .ws216{word-spacing:-0.446457pt;} .ws497{word-spacing:-0.436536pt;} .ws4c3{word-spacing:-0.409252pt;} .ws578{word-spacing:-0.405118pt;} .ws55b{word-spacing:-0.393046pt;} .wsfd{word-spacing:-0.372048pt;} .ws4f4{word-spacing:-0.366828pt;} .ws56b{word-spacing:-0.363780pt;} .ws5f{word-spacing:-0.359646pt;} .ws160{word-spacing:-0.334843pt;} .ws329{word-spacing:-0.330709pt;} .ws423{word-spacing:-0.316240pt;} .ws4cf{word-spacing:-0.312520pt;} .ws55f{word-spacing:-0.305702pt;} .ws233{word-spacing:-0.297638pt;} .ws446{word-spacing:-0.281103pt;} .ws16d{word-spacing:-0.260433pt;} .ws4a2{word-spacing:-0.254646pt;} .ws582{word-spacing:-0.251891pt;} .ws88{word-spacing:-0.251752pt;} .ws19c{word-spacing:-0.248032pt;} .wse4{word-spacing:-0.244653pt;} .ws2af{word-spacing:-0.223229pt;} .ws559{word-spacing:-0.218359pt;} .ws3dc{word-spacing:-0.218268pt;} .ws355{word-spacing:-0.215788pt;} .ws54d{word-spacing:-0.207082pt;} .ws1b7{word-spacing:-0.186024pt;} .ws335{word-spacing:-0.179823pt;} .ws525{word-spacing:-0.178583pt;} .ws30c{word-spacing:-0.165354pt;} .ws152{word-spacing:-0.148819pt;} .ws54c{word-spacing:-0.135053pt;} .ws4de{word-spacing:-0.122276pt;} .ws235{word-spacing:-0.111614pt;} .ws3e2{word-spacing:-0.109134pt;} .ws8c{word-spacing:-0.107894pt;} .ws579{word-spacing:-0.099465pt;} .ws564{word-spacing:-0.095079pt;} .ws211{word-spacing:-0.074410pt;} .ws44a{word-spacing:-0.070276pt;} .ws577{word-spacing:-0.068995pt;} .ws2e5{word-spacing:-0.059916pt;} .ws2ff{word-spacing:-0.053740pt;} .ws507{word-spacing:-0.040759pt;} .ws1ed{word-spacing:-0.037205pt;} .ws2e6{word-spacing:-0.029958pt;} .ws0{word-spacing:0.000000pt;} .ws74{word-spacing:0.035965pt;} .ws250{word-spacing:0.037205pt;} .ws2{word-spacing:0.064129pt;} .ws6e{word-spacing:0.071929pt;} .ws18e{word-spacing:0.074410pt;} .ws4d8{word-spacing:0.081517pt;} .ws279{word-spacing:0.082677pt;} .ws278{word-spacing:0.092598pt;} .ws460{word-spacing:0.105413pt;} .ws19b{word-spacing:0.107480pt;} .ws247{word-spacing:0.111614pt;} .ws277{word-spacing:0.132284pt;} .ws4ca{word-spacing:0.148819pt;} .ws274{word-spacing:0.158740pt;} .ws52e{word-spacing:0.163035pt;} .ws350{word-spacing:0.179823pt;} .ws405{word-spacing:0.181890pt;} .ws133{word-spacing:0.186024pt;} .ws57f{word-spacing:0.204266pt;} .wsed{word-spacing:0.223229pt;} .ws574{word-spacing:0.231496pt;} .ws57d{word-spacing:0.232530pt;} .wse1{word-spacing:0.244653pt;} .ws459{word-spacing:0.245965pt;} .ws48{word-spacing:0.251752pt;} .ws159{word-spacing:0.260433pt;} .ws30{word-spacing:0.287717pt;} .ws465{word-spacing:0.291024pt;} .ws2d0{word-spacing:0.297638pt;} .ws41c{word-spacing:0.316240pt;} .wsb4{word-spacing:0.323681pt;} .ws48d{word-spacing:0.327402pt;} .ws310{word-spacing:0.334843pt;} .ws563{word-spacing:0.347244pt;} .ws45d{word-spacing:0.351378pt;} .ws275{word-spacing:0.357166pt;} .wsd{word-spacing:0.359646pt;} .ws131{word-spacing:0.372048pt;} .ws502{word-spacing:0.392717pt;} .wsd5{word-spacing:0.395611pt;} .wsea{word-spacing:0.396851pt;} .ws4c9{word-spacing:0.409252pt;} .ws4c{word-spacing:0.413386pt;} .ws431{word-spacing:0.421654pt;} .wsad{word-spacing:0.431575pt;} .ws49b{word-spacing:0.436536pt;} .ws1b5{word-spacing:0.446457pt;} .ws540{word-spacing:0.448345pt;} .ws3b2{word-spacing:0.456792pt;} .ws56e{word-spacing:0.462992pt;} .ws580{word-spacing:0.472294pt;} .ws1fd{word-spacing:0.483662pt;} .ws358{word-spacing:0.503504pt;} .ws2dd{word-spacing:0.520867pt;} .ws397{word-spacing:0.527067pt;} .ws276{word-spacing:0.529134pt;} .ws581{word-spacing:0.532830pt;} .ws89{word-spacing:0.539469pt;} .ws3c4{word-spacing:0.545670pt;} .ws1be{word-spacing:0.558071pt;} .ws545{word-spacing:0.564508pt;} .ws57c{word-spacing:0.578741pt;} .ws1{word-spacing:0.590773pt;} .ws158{word-spacing:0.595276pt;} .ws22{word-spacing:0.611398pt;} .ws495{word-spacing:0.618426pt;} .ws1a7{word-spacing:0.632481pt;} .ws4{word-spacing:0.641286pt;} .ws2fe{word-spacing:0.644882pt;} .ws3ed{word-spacing:0.654804pt;} .ws570{word-spacing:0.661418pt;} .ws37b{word-spacing:0.667619pt;} .ws1bc{word-spacing:0.669686pt;} .ws573{word-spacing:0.694489pt;} .ws36a{word-spacing:0.702756pt;} .ws16{word-spacing:0.719292pt;} .ws304{word-spacing:0.744095pt;} .ws576{word-spacing:0.750513pt;} .ws434{word-spacing:0.773032pt;} .ws4d5{word-spacing:0.774414pt;} .ws57e{word-spacing:0.776213pt;} .wse3{word-spacing:0.781300pt;} .wsf{word-spacing:0.791221pt;} .ws44c{word-spacing:0.808170pt;} .ws2b6{word-spacing:0.818505pt;} .wsa0{word-spacing:0.827186pt;} .ws490{word-spacing:0.836693pt;} .ws2a7{word-spacing:0.855709pt;} .ws509{word-spacing:0.855931pt;} .ws47{word-spacing:0.863150pt;} .ws40b{word-spacing:0.873071pt;} .ws2ac{word-spacing:0.892914pt;} .ws2f{word-spacing:0.899115pt;} .ws3a3{word-spacing:0.913583pt;} .ws4c6{word-spacing:0.930119pt;} .ws3cc{word-spacing:0.945827pt;} .ws363{word-spacing:0.948721pt;} .ws1ac{word-spacing:0.967324pt;} .ws1a{word-spacing:0.971044pt;} .ws514{word-spacing:0.978207pt;} .ws4d1{word-spacing:0.980479pt;} .ws3c5{word-spacing:0.982205pt;} .wsec{word-spacing:0.992127pt;} .wse2{word-spacing:1.004528pt;} .wsd4{word-spacing:1.007009pt;} .ws3f1{word-spacing:1.018583pt;} .ws517{word-spacing:1.018966pt;} .wsfa{word-spacing:1.041733pt;} .ws1f{word-spacing:1.042973pt;} .ws556{word-spacing:1.071947pt;} .ws24{word-spacing:1.078938pt;} .ws56d{word-spacing:1.091339pt;} .ws530{word-spacing:1.100483pt;} .wsaa{word-spacing:1.114902pt;} .ws13d{word-spacing:1.116143pt;} .ws3af{word-spacing:1.124410pt;} .ws469{word-spacing:1.127717pt;} .ws533{word-spacing:1.141242pt;} .wsc6{word-spacing:1.150867pt;} .ws1af{word-spacing:1.153347pt;} .ws36f{word-spacing:1.159548pt;} .ws48b{word-spacing:1.164095pt;} .ws311{word-spacing:1.184746pt;} .wsb0{word-spacing:1.186832pt;} .ws2cd{word-spacing:1.190552pt;} .ws75{word-spacing:1.222796pt;} .ws4ad{word-spacing:1.227757pt;} .ws3ae{word-spacing:1.229824pt;} .ws3e1{word-spacing:1.236851pt;} .ws86{word-spacing:1.258761pt;} .ws325{word-spacing:1.264962pt;} .ws3ab{word-spacing:1.300099pt;} .ws1b8{word-spacing:1.302166pt;} .ws4e3{word-spacing:1.304276pt;} .ws48e{word-spacing:1.309607pt;} .ws57{word-spacing:1.330690pt;} .ws54f{word-spacing:1.338664pt;} .ws176{word-spacing:1.339371pt;} .ws125{word-spacing:1.376576pt;} .ws512{word-spacing:1.385793pt;} .ws62{word-spacing:1.402619pt;} .ws1aa{word-spacing:1.413781pt;} .ws21{word-spacing:1.438584pt;} .ws441{word-spacing:1.440651pt;} .ws22a{word-spacing:1.450985pt;} .ws30b{word-spacing:1.463387pt;} .ws2d4{word-spacing:1.488190pt;} .ws406{word-spacing:1.491497pt;} .ws518{word-spacing:1.508069pt;} .wsc3{word-spacing:1.510513pt;} .ws4c2{word-spacing:1.525395pt;} .wse7{word-spacing:1.537796pt;} .ws3b8{word-spacing:1.546064pt;} .ws76{word-spacing:1.546477pt;} .ws4ee{word-spacing:1.548828pt;} .ws161{word-spacing:1.562600pt;} .ws430{word-spacing:1.581202pt;} .ws90{word-spacing:1.582442pt;} .ws569{word-spacing:1.587403pt;} .ws4db{word-spacing:1.589587pt;} .ws550{word-spacing:1.593279pt;} .ws124{word-spacing:1.599804pt;} .ws37d{word-spacing:1.616340pt;} .ws20f{word-spacing:1.637009pt;} .ws9d{word-spacing:1.654371pt;} .ws547{word-spacing:1.655889pt;} .ws529{word-spacing:1.671104pt;} .ws1f2{word-spacing:1.674214pt;} .ws306{word-spacing:1.711419pt;} .ws52f{word-spacing:1.711862pt;} .ws4ba{word-spacing:1.748623pt;} .ws340{word-spacing:1.762265pt;} .ws3dd{word-spacing:1.782521pt;} .ws24f{word-spacing:1.785828pt;} .ws4e1{word-spacing:1.793380pt;} .wsa1{word-spacing:1.798230pt;} .ws491{word-spacing:1.818899pt;} .ws186{word-spacing:1.823033pt;} .ws508{word-spacing:1.834138pt;} .ws12{word-spacing:1.834194pt;} .ws3{word-spacing:1.859729pt;} .ws549{word-spacing:1.860238pt;} .ws38{word-spacing:1.870159pt;} .ws24d{word-spacing:1.897442pt;} .ws9c{word-spacing:1.906123pt;} .ws4d4{word-spacing:1.915656pt;} .ws565{word-spacing:1.918112pt;} .ws448{word-spacing:1.932580pt;} .ws4b3{word-spacing:1.934647pt;} .ws3c{word-spacing:1.942088pt;} .ws51f{word-spacing:1.956414pt;} .ws166{word-spacing:1.971852pt;} .ws3e9{word-spacing:2.000789pt;} .ws1c8{word-spacing:2.009057pt;} .ws15{word-spacing:2.014017pt;} .ws55e{word-spacing:2.036700pt;} .ws49a{word-spacing:2.037167pt;} .ws4c0{word-spacing:2.046261pt;} .ws23{word-spacing:2.049982pt;} .ws367{word-spacing:2.073131pt;} .ws53d{word-spacing:2.078690pt;} .ws207{word-spacing:2.083466pt;} .ws1c{word-spacing:2.085946pt;} .ws407{word-spacing:2.109923pt;} .ws26d{word-spacing:2.120671pt;} .ws99{word-spacing:2.121911pt;} .ws419{word-spacing:2.143407pt;} .ws14f{word-spacing:2.157876pt;} .ws53a{word-spacing:2.160207pt;} .ws44e{word-spacing:2.178545pt;} .ws19{word-spacing:2.193840pt;} .ws142{word-spacing:2.195080pt;} .wse5{word-spacing:2.232285pt;} .ws532{word-spacing:2.241725pt;} .ws82{word-spacing:2.265769pt;} .ws27e{word-spacing:2.269490pt;} .ws566{word-spacing:2.281891pt;} .ws534{word-spacing:2.282483pt;} .ws78{word-spacing:2.301734pt;} .wsf7{word-spacing:2.306695pt;} .ws3b5{word-spacing:2.319096pt;} .ws8f{word-spacing:2.337698pt;} .ws128{word-spacing:2.343899pt;} .ws433{word-spacing:2.354234pt;} .ws4d3{word-spacing:2.364001pt;} .ws4a3{word-spacing:2.364569pt;} .wsb7{word-spacing:2.373663pt;} .ws4b9{word-spacing:2.381104pt;} .ws370{word-spacing:2.389372pt;} .ws19f{word-spacing:2.418309pt;} .ws373{word-spacing:2.424510pt;} .ws4fe{word-spacing:2.434844pt;} .ws496{word-spacing:2.437325pt;} .ws7d{word-spacing:2.445592pt;} .ws191{word-spacing:2.455514pt;} .ws567{word-spacing:2.480317pt;} .ws548{word-spacing:2.483834pt;} .ws252{word-spacing:2.492718pt;} .ws5{word-spacing:2.509130pt;} .ws4a{word-spacing:2.517521pt;} .ws15c{word-spacing:2.529923pt;} .ws4f7{word-spacing:2.552659pt;} .ws449{word-spacing:2.565061pt;} .wsf8{word-spacing:2.567128pt;} .ws51d{word-spacing:2.567794pt;} .ws14{word-spacing:2.589451pt;} .ws3b4{word-spacing:2.600199pt;} .ws264{word-spacing:2.604333pt;} .ws408{word-spacing:2.619214pt;} .ws11{word-spacing:2.625415pt;} .ws219{word-spacing:2.641537pt;} .wsc{word-spacing:2.661380pt;} .ws422{word-spacing:2.670474pt;} .ws546{word-spacing:2.672003pt;} .ws11c{word-spacing:2.678742pt;} .ws3e0{word-spacing:2.691970pt;} .wsc7{word-spacing:2.697344pt;} .ws4fc{word-spacing:2.709746pt;} .ws4c5{word-spacing:2.715947pt;} .ws30f{word-spacing:2.753152pt;} .ws45{word-spacing:2.769274pt;} .ws531{word-spacing:2.771587pt;} .ws1d0{word-spacing:2.790356pt;} .ws15d{word-spacing:2.827561pt;} .ws3e6{word-spacing:2.837482pt;} .ws305{word-spacing:2.864766pt;} .ws483{word-spacing:2.873860pt;} .ws2a{word-spacing:2.877167pt;} .ws238{word-spacing:2.901971pt;} .ws467{word-spacing:2.910238pt;} .ws44d{word-spacing:2.916439pt;} .ws175{word-spacing:2.939175pt;} .ws568{word-spacing:2.943309pt;} .ws192{word-spacing:2.976380pt;} .ws53f{word-spacing:3.016139pt;} .ws84{word-spacing:3.021026pt;} .ws2f8{word-spacing:3.050790pt;} .ws10f{word-spacing:3.087994pt;} .ws10{word-spacing:3.092955pt;} .ws544{word-spacing:3.097656pt;} .ws56c{word-spacing:3.108664pt;} .ws1b4{word-spacing:3.125199pt;} .ws4a4{word-spacing:3.128506pt;} .ws8a{word-spacing:3.128919pt;} .ws14b{word-spacing:3.162404pt;} .ws470{word-spacing:3.164884pt;} .ws56f{word-spacing:3.174805pt;} .ws43e{word-spacing:3.197542pt;} .ws268{word-spacing:3.199609pt;} .ws33{word-spacing:3.200849pt;} .ws46f{word-spacing:3.201262pt;} .ws42{word-spacing:3.236813pt;} .wsc0{word-spacing:3.272778pt;} .ws4b4{word-spacing:3.274018pt;} .ws2fb{word-spacing:3.278152pt;} .ws1ea{word-spacing:3.298821pt;} .ws126{word-spacing:3.311223pt;} .wse9{word-spacing:3.323624pt;} .ws53{word-spacing:3.344707pt;} .ws4c7{word-spacing:3.348428pt;} .ws3b7{word-spacing:3.373231pt;} .ws6{word-spacing:3.374347pt;} .wsce{word-spacing:3.380672pt;} .ws3fc{word-spacing:3.383152pt;} .ws241{word-spacing:3.385632pt;} .ws45a{word-spacing:3.408368pt;} .ws1e2{word-spacing:3.422837pt;} .ws3cd{word-spacing:3.455908pt;} .ws162{word-spacing:3.460042pt;} .ws63{word-spacing:3.488565pt;} .ws482{word-spacing:3.492286pt;} .ws313{word-spacing:3.497247pt;} .ws4e0{word-spacing:3.505242pt;} .ws362{word-spacing:3.513782pt;} .ws40{word-spacing:3.524530pt;} .ws20c{word-spacing:3.534451pt;} .ws38c{word-spacing:3.548920pt;} .ws1f3{word-spacing:3.571656pt;} .ws45f{word-spacing:3.584058pt;} .ws538{word-spacing:3.586759pt;} .ws28{word-spacing:3.596459pt;} .ws16b{word-spacing:3.608861pt;} .ws39f{word-spacing:3.619195pt;} .ws4e5{word-spacing:3.627518pt;} .ws1ce{word-spacing:3.646066pt;} .ws35e{word-spacing:3.668388pt;} .ws1f9{word-spacing:3.683270pt;} .ws38b{word-spacing:3.689471pt;} .wsb6{word-spacing:3.704353pt;} .ws29a{word-spacing:3.720475pt;} .ws1b{word-spacing:3.740318pt;} .ws4e9{word-spacing:3.749794pt;} .ws27d{word-spacing:3.757680pt;} .ws450{word-spacing:3.759747pt;} .ws61{word-spacing:3.776282pt;} .ws489{word-spacing:3.783310pt;} .ws132{word-spacing:3.794885pt;} .ws295{word-spacing:3.815554pt;} .ws584{word-spacing:3.817207pt;} .ws3bf{word-spacing:3.819688pt;} .ws2d6{word-spacing:3.832089pt;} .ws35d{word-spacing:3.848211pt;} .ws45e{word-spacing:3.865160pt;} .ws4cb{word-spacing:3.869294pt;} .ws4ef{word-spacing:3.872070pt;} .ws3de{word-spacing:3.892444pt;} .ws369{word-spacing:3.900298pt;} .ws168{word-spacing:3.906499pt;} .ws2e{word-spacing:3.920140pt;} .ws486{word-spacing:3.928822pt;} .ws30e{word-spacing:3.943704pt;} .ws4da{word-spacing:3.953587pt;} .ws7a{word-spacing:3.956105pt;} .ws3df{word-spacing:3.965200pt;} .ws4fb{word-spacing:3.966440pt;} .ws15a{word-spacing:3.980908pt;} .ws109{word-spacing:4.018113pt;} .ws542{word-spacing:4.035104pt;} .ws1bd{word-spacing:4.055318pt;} .ws7b{word-spacing:4.063999pt;} .ws3ad{word-spacing:4.075987pt;} .ws226{word-spacing:4.092523pt;} .wsbe{word-spacing:4.099963pt;} .ws487{word-spacing:4.110711pt;} .ws2ea{word-spacing:4.129727pt;} .ws34a{word-spacing:4.135928pt;} .ws2c0{word-spacing:4.166932pt;} .wsc4{word-spacing:4.171893pt;} .ws388{word-spacing:4.181401pt;} .ws4a6{word-spacing:4.183467pt;} .ws20e{word-spacing:4.204137pt;} .wsbc{word-spacing:4.207857pt;} .wseb{word-spacing:4.216538pt;} .ws4f0{word-spacing:4.238898pt;} .ws26a{word-spacing:4.241342pt;} .ws34{word-spacing:4.243822pt;} .ws1f0{word-spacing:4.278546pt;} .ws49{word-spacing:4.279786pt;} .ws3bd{word-spacing:4.292601pt;} .ws5d{word-spacing:4.315751pt;} .ws536{word-spacing:4.320415pt;} .ws3f6{word-spacing:4.328979pt;} .wsf0{word-spacing:4.352956pt;} .ws420{word-spacing:4.357090pt;} .ws3c7{word-spacing:4.365357pt;} .ws85{word-spacing:4.387680pt;} .ws4b2{word-spacing:4.390161pt;} .ws32{word-spacing:4.423645pt;} .ws1d5{word-spacing:4.427365pt;} .ws345{word-spacing:4.459609pt;} .ws2be{word-spacing:4.464570pt;} .ws3f8{word-spacing:4.474491pt;} .ws504{word-spacing:4.483449pt;} .ws58{word-spacing:4.495574pt;} .ws1a9{word-spacing:4.501775pt;} .ws478{word-spacing:4.510869pt;} .ws4ff{word-spacing:4.516243pt;} .ws51e{word-spacing:4.524208pt;} .ws351{word-spacing:4.531539pt;} .ws22f{word-spacing:4.538980pt;} .ws4e6{word-spacing:4.564967pt;} .ws8d{word-spacing:4.567503pt;} .ws43d{word-spacing:4.567917pt;} .ws123{word-spacing:4.576184pt;} .wsb5{word-spacing:4.603468pt;} .ws52b{word-spacing:4.605725pt;} .ws16e{word-spacing:4.613389pt;} .ws3c0{word-spacing:4.620003pt;} .ws43a{word-spacing:4.638192pt;} .ws164{word-spacing:4.650594pt;} .wse6{word-spacing:4.662995pt;} .ws3a0{word-spacing:4.673330pt;} .ws23e{word-spacing:4.687799pt;} .ws77{word-spacing:4.711362pt;} .ws1d4{word-spacing:4.725003pt;} .wscb{word-spacing:4.747326pt;} .ws149{word-spacing:4.762208pt;} .ws506{word-spacing:4.768760pt;} .ws443{word-spacing:4.778743pt;} .ws79{word-spacing:4.783291pt;} .wsfe{word-spacing:4.799413pt;} .ws488{word-spacing:4.801893pt;} .ws435{word-spacing:4.813881pt;} .ws4b5{word-spacing:4.836618pt;} .ws43c{word-spacing:4.849019pt;} .ws53c{word-spacing:4.850277pt;} .wsd2{word-spacing:4.855220pt;} .ws23d{word-spacing:4.873822pt;} .ws37a{word-spacing:4.884157pt;} .ws296{word-spacing:4.890358pt;} .wse8{word-spacing:4.911027pt;} .ws4d9{word-spacing:4.931794pt;} .ws21c{word-spacing:4.948232pt;} .ws42b{word-spacing:4.954433pt;} .ws18d{word-spacing:4.985437pt;} .ws2b3{word-spacing:5.022641pt;} .ws39{word-spacing:5.035043pt;} .ws52a{word-spacing:5.054070pt;} .ws464{word-spacing:5.056539pt;} .ws103{word-spacing:5.059846pt;} .ws9{word-spacing:5.071007pt;} .ws473{word-spacing:5.092917pt;} .ws4e4{word-spacing:5.094829pt;} .ws1a8{word-spacing:5.097051pt;} .ws1ad{word-spacing:5.134256pt;} .ws92{word-spacing:5.142937pt;} .ws251{word-spacing:5.171460pt;} .ws25{word-spacing:5.178901pt;} .ws432{word-spacing:5.200397pt;} .ws257{word-spacing:5.208665pt;} .ws280{word-spacing:5.245870pt;} .ws503{word-spacing:5.257863pt;} .ws391{word-spacing:5.270673pt;} .ws46e{word-spacing:5.274807pt;} .ws22e{word-spacing:5.283075pt;} .ws5a{word-spacing:5.286795pt;} .ws38f{word-spacing:5.305811pt;} .ws46a{word-spacing:5.311185pt;} .ws201{word-spacing:5.320279pt;} .ws356{word-spacing:5.322760pt;} .ws437{word-spacing:5.340949pt;} .ws154{word-spacing:5.357484pt;} .wsab{word-spacing:5.358724pt;} .ws37f{word-spacing:5.376086pt;} .wscc{word-spacing:5.394689pt;} .ws3ff{word-spacing:5.420319pt;} .ws20{word-spacing:5.430653pt;} .ws301{word-spacing:5.431894pt;} .ws3c8{word-spacing:5.456697pt;} .ws167{word-spacing:5.469098pt;} .ws4e8{word-spacing:5.502415pt;} .ws2aa{word-spacing:5.506303pt;} .ws49c{word-spacing:5.529453pt;} .ws6a{word-spacing:5.538547pt;} .ws1b3{word-spacing:5.543508pt;} .ws475{word-spacing:5.565831pt;} .ws16c{word-spacing:5.617917pt;} .ws451{word-spacing:5.622051pt;} .ws1d{word-spacing:5.646441pt;} .ws24a{word-spacing:5.655122pt;} .ws398{word-spacing:5.657189pt;} .ws4ec{word-spacing:5.665450pt;} .ws1a1{word-spacing:5.692327pt;} .ws12a{word-spacing:5.704728pt;} .ws34b{word-spacing:5.718370pt;} .ws2ed{word-spacing:5.729532pt;} .ws29{word-spacing:5.754335pt;} .wsf5{word-spacing:5.766736pt;} .ws484{word-spacing:5.784098pt;} .ws50{word-spacing:5.790299pt;} .ws37e{word-spacing:5.797740pt;} .ws575{word-spacing:5.801151pt;} .ws4be{word-spacing:5.803941pt;} .ws231{word-spacing:5.841146pt;} .ws48c{word-spacing:5.856854pt;} .ws561{word-spacing:5.859748pt;} .ws418{word-spacing:5.868016pt;} .ws4f2{word-spacing:5.869243pt;} .ws153{word-spacing:5.878351pt;} .wsd1{word-spacing:5.898193pt;} .ws543{word-spacing:5.910001pt;} .ws172{word-spacing:5.915555pt;} .ws4bb{word-spacing:5.952760pt;} .ws3a2{word-spacing:5.973429pt;} .ws524{word-spacing:5.989965pt;} .ws6d{word-spacing:6.006087pt;} .ws1c9{word-spacing:6.027170pt;} .ws395{word-spacing:6.043705pt;} .ws10a{word-spacing:6.064374pt;} .ws33b{word-spacing:6.078016pt;} .ws38e{word-spacing:6.078843pt;} .ws31c{word-spacing:6.101579pt;} .ws17d{word-spacing:6.138784pt;} .ws477{word-spacing:6.147878pt;} .ws364{word-spacing:6.149118pt;} .wsa2{word-spacing:6.149945pt;} .ws1d1{word-spacing:6.175989pt;} .ws3a4{word-spacing:6.184256pt;} .ws1fa{word-spacing:6.213193pt;} .ws360{word-spacing:6.219394pt;} .ws180{word-spacing:6.250398pt;} .ws39e{word-spacing:6.254532pt;} .ws50f{word-spacing:6.276829pt;} .ws146{word-spacing:6.287603pt;} .wsa8{word-spacing:6.293804pt;} .ws4dd{word-spacing:6.317588pt;} .ws11b{word-spacing:6.324808pt;} .ws5b{word-spacing:6.329768pt;} .ws12c{word-spacing:6.349611pt;} .ws1ab{word-spacing:6.362012pt;} .ws179{word-spacing:6.399217pt;} .ws39c{word-spacing:6.430221pt;} .ws98{word-spacing:6.473627pt;} .ws37{word-spacing:6.509591pt;} .ws2cf{word-spacing:6.510831pt;} .ws513{word-spacing:6.521381pt;} .ws284{word-spacing:6.548036pt;} .ws255{word-spacing:6.585241pt;} .ws353{word-spacing:6.617485pt;} .ws120{word-spacing:6.622446pt;} .ws97{word-spacing:6.653449pt;} .wsa7{word-spacing:6.655516pt;} .ws221{word-spacing:6.659650pt;} .ws510{word-spacing:6.684415pt;} .ws334{word-spacing:6.689414pt;} .ws16f{word-spacing:6.696855pt;} .ws2b8{word-spacing:6.734060pt;} .ws12b{word-spacing:6.746461pt;} .ws1d6{word-spacing:6.771265pt;} .ws93{word-spacing:6.797308pt;} .ws494{word-spacing:6.802682pt;} .ws53e{word-spacing:6.806691pt;} .ws183{word-spacing:6.808469pt;} .ws3f{word-spacing:6.833272pt;} .ws23b{word-spacing:6.845674pt;} .ws500{word-spacing:6.872544pt;} .ws1b6{word-spacing:6.882879pt;} .ws462{word-spacing:6.887013pt;} .ws110{word-spacing:6.920084pt;} .ws4f3{word-spacing:6.928967pt;} .ws13c{word-spacing:6.957288pt;} .ws9b{word-spacing:6.977131pt;} .ws45c{word-spacing:6.992426pt;} .ws1f4{word-spacing:6.994493pt;} .ws1eb{word-spacing:7.002761pt;} .ws7e{word-spacing:7.013095pt;} .ws427{word-spacing:7.027564pt;} .ws2ca{word-spacing:7.031698pt;} .wsd3{word-spacing:7.049060pt;} .ws28f{word-spacing:7.068903pt;} .wsd0{word-spacing:7.085025pt;} .ws3ca{word-spacing:7.093706pt;} .ws190{word-spacing:7.106107pt;} .ws35{word-spacing:7.120989pt;} .ws1a5{word-spacing:7.143312pt;} .ws3a{word-spacing:7.156954pt;} .ws3d2{word-spacing:7.166462pt;} .ws2db{word-spacing:7.180517pt;} .ws6b{word-spacing:7.192918pt;} .ws21f{word-spacing:7.217722pt;} .ws13{word-spacing:7.228883pt;} .ws299{word-spacing:7.254926pt;} .ws348{word-spacing:7.264848pt;} .ws290{word-spacing:7.292131pt;} .ws34e{word-spacing:7.300812pt;} .ws404{word-spacing:7.311974pt;} .ws318{word-spacing:7.329336pt;} .ws96{word-spacing:7.336777pt;} .ws240{word-spacing:7.366541pt;} .ws9a{word-spacing:7.372741pt;} .ws3d7{word-spacing:7.384729pt;} .ws104{word-spacing:7.403745pt;} .wsca{word-spacing:7.408706pt;} .ws50e{word-spacing:7.418071pt;} .wsef{word-spacing:7.440950pt;} .ws4ea{word-spacing:7.458829pt;} .ws523{word-spacing:7.478155pt;} .ws33f{word-spacing:7.480635pt;} .ws3ba{word-spacing:7.484356pt;} .ws1fb{word-spacing:7.515360pt;} .wsbd{word-spacing:7.516600pt;} .ws45b{word-spacing:7.519493pt;} .ws40a{word-spacing:7.530241pt;} .ws2ee{word-spacing:7.552564pt;} .ws457{word-spacing:7.554631pt;} .ws50d{word-spacing:7.581105pt;} .wsd7{word-spacing:7.588529pt;} .ws119{word-spacing:7.589769pt;} .ws2f6{word-spacing:7.626974pt;} .ws3e7{word-spacing:7.639375pt;} .ws17c{word-spacing:7.664179pt;} .ws51b{word-spacing:7.703381pt;} .ws35c{word-spacing:7.732387pt;} .ws210{word-spacing:7.738588pt;} .wsae{word-spacing:7.768352pt;} .ws248{word-spacing:7.775793pt;} .wsa3{word-spacing:7.804316pt;} .ws116{word-spacing:7.812998pt;} .ws4a8{word-spacing:7.857643pt;} .ws50a{word-spacing:7.866416pt;} .ws87{word-spacing:7.876246pt;} .ws4b1{word-spacing:7.887407pt;} .ws411{word-spacing:7.894021pt;} .ws27{word-spacing:7.912210pt;} .ws227{word-spacing:7.924612pt;} .ws389{word-spacing:7.941147pt;} .ws230{word-spacing:7.961817pt;} .ws401{word-spacing:7.966777pt;} .ws505{word-spacing:7.988692pt;} .wsf4{word-spacing:7.999021pt;} .ws368{word-spacing:8.011423pt;} .ws14c{word-spacing:8.036226pt;} .ws3b0{word-spacing:8.046561pt;} .ws338{word-spacing:8.056069pt;} .ws298{word-spacing:8.061029pt;} .ws23f{word-spacing:8.073431pt;} .ws3d5{word-spacing:8.075911pt;} .ws3b3{word-spacing:8.081698pt;} .ws32d{word-spacing:8.092033pt;} .ws185{word-spacing:8.110636pt;} .wsf3{word-spacing:8.147840pt;} .ws3c2{word-spacing:8.148667pt;} .ws51a{word-spacing:8.151726pt;} .wsb{word-spacing:8.163962pt;} .ws4bd{word-spacing:8.185045pt;} .ws3f5{word-spacing:8.221423pt;} .ws2ab{word-spacing:8.222250pt;} .ws352{word-spacing:8.235891pt;} .ws4f9{word-spacing:8.247053pt;} .ws379{word-spacing:8.257388pt;} .ws1c0{word-spacing:8.259455pt;} .ws4f8{word-spacing:8.286325pt;} .ws234{word-spacing:8.296659pt;} .wsb1{word-spacing:8.307821pt;} .ws3ea{word-spacing:8.330557pt;} .ws2ec{word-spacing:8.333864pt;} .ws1dd{word-spacing:8.371069pt;} .wsba{word-spacing:8.379750pt;} .ws144{word-spacing:8.408274pt;} .ws32f{word-spacing:8.415714pt;} .ws382{word-spacing:8.433077pt;} .ws1a0{word-spacing:8.445478pt;} .ws4d{word-spacing:8.451679pt;} .ws31a{word-spacing:8.482683pt;} .ws4ed{word-spacing:8.518554pt;} .ws13a{word-spacing:8.519888pt;} .ws91{word-spacing:8.523608pt;} .ws13b{word-spacing:8.557093pt;} .ws18{word-spacing:8.559573pt;} .ws4b0{word-spacing:8.594297pt;} .ws375{word-spacing:8.608766pt;} .ws23a{word-spacing:8.631502pt;} .ws377{word-spacing:8.643904pt;} .ws493{word-spacing:8.657959pt;} .ws265{word-spacing:8.668707pt;} .ws447{word-spacing:8.679041pt;} .ws174{word-spacing:8.705912pt;} .ws53b{word-spacing:8.722347pt;} .ws479{word-spacing:8.730715pt;} .ws2b4{word-spacing:8.743116pt;} .ws2d{word-spacing:8.775360pt;} .ws129{word-spacing:8.780321pt;} .ws526{word-spacing:8.817526pt;} .ws39a{word-spacing:8.819593pt;} .ws480{word-spacing:8.839849pt;} .wsb8{word-spacing:8.847290pt;} .ws4af{word-spacing:8.854731pt;} .wsa5{word-spacing:8.883254pt;} .ws4eb{word-spacing:8.885381pt;} .ws1e4{word-spacing:8.891935pt;} .ws339{word-spacing:8.919219pt;} .ws44b{word-spacing:8.925006pt;} .ws588{word-spacing:8.929140pt;} .ws4a9{word-spacing:8.948983pt;} .ws8{word-spacing:8.955183pt;} .ws453{word-spacing:8.960144pt;} .ws217{word-spacing:8.966345pt;} .ws308{word-spacing:9.003550pt;} .ws3e{word-spacing:9.027113pt;} .ws108{word-spacing:9.040754pt;} .ws4e2{word-spacing:9.048416pt;} .ws56{word-spacing:9.063077pt;} .ws22b{word-spacing:9.077959pt;} .ws54{word-spacing:9.099042pt;} .ws4fd{word-spacing:9.111030pt;} .ws21a{word-spacing:9.115164pt;} .ws12d{word-spacing:9.127565pt;} .ws3b6{word-spacing:9.135833pt;} .ws194{word-spacing:9.152369pt;} .ws392{word-spacing:9.170971pt;} .ws1fe{word-spacing:9.189573pt;} .wsdc{word-spacing:9.242900pt;} .ws100{word-spacing:9.263983pt;} .ws14d{word-spacing:9.301188pt;} .ws3aa{word-spacing:9.311522pt;} .ws410{word-spacing:9.312762pt;} .ws347{word-spacing:9.350794pt;} .ws2a9{word-spacing:9.375597pt;} .wsee{word-spacing:9.412802pt;} .ws3f3{word-spacing:9.421896pt;} .ws31f{word-spacing:9.450007pt;} .ws589{word-spacing:9.487211pt;} .wsc8{word-spacing:9.494652pt;} .ws444{word-spacing:9.522349pt;} .ws302{word-spacing:9.524416pt;} .ws42e{word-spacing:9.557487pt;} .ws27c{word-spacing:9.561621pt;} .ws26{word-spacing:9.566581pt;} .ws485{word-spacing:9.567408pt;} .ws4dc{word-spacing:9.578278pt;} .ws399{word-spacing:9.592625pt;} .ws1cd{word-spacing:9.598826pt;} .ws3fe{word-spacing:9.603786pt;} .wsf1{word-spacing:9.636030pt;} .ws44{word-spacing:9.638511pt;} .ws3c3{word-spacing:9.640164pt;} .ws150{word-spacing:9.673235pt;} .ws16a{word-spacing:9.710440pt;} .ws3e3{word-spacing:9.712920pt;} .ws383{word-spacing:9.733176pt;} .ws4f5{word-spacing:9.739377pt;} .ws269{word-spacing:9.747645pt;} .ws40e{word-spacing:9.749298pt;} .ws118{word-spacing:9.784849pt;} .ws3fb{word-spacing:9.785676pt;} .ws3a9{word-spacing:9.803452pt;} .ws35b{word-spacing:9.818334pt;} .ws19e{word-spacing:9.822054pt;} .ws342{word-spacing:9.854298pt;} .ws14a{word-spacing:9.859259pt;} .ws2b9{word-spacing:9.896464pt;} .ws381{word-spacing:9.908865pt;} .ws2cc{word-spacing:9.933668pt;} .ws41{word-spacing:9.962192pt;} .ws171{word-spacing:9.970873pt;} .ws2a6{word-spacing:10.008078pt;} .ws2dc{word-spacing:10.045283pt;} .ws2c5{word-spacing:10.082487pt;} .ws386{word-spacing:10.084554pt;} .ws2e3{word-spacing:10.119692pt;} .ws1b9{word-spacing:10.156897pt;} .ws32a{word-spacing:10.177979pt;} .ws4a5{word-spacing:10.185834pt;} .ws11a{word-spacing:10.194102pt;} .ws137{word-spacing:10.231306pt;} .ws4c8{word-spacing:10.268511pt;} .ws3fa{word-spacing:10.294968pt;} .ws169{word-spacing:10.305716pt;} .wsb3{word-spacing:10.321838pt;} .ws463{word-spacing:10.330519pt;} .ws1bb{word-spacing:10.342921pt;} .wsa4{word-spacing:10.357802pt;} .ws220{word-spacing:10.380125pt;} .ws236{word-spacing:10.417330pt;} .ws357{word-spacing:10.429732pt;} .ws266{word-spacing:10.454535pt;} .ws3b9{word-spacing:10.471070pt;} .ws202{word-spacing:10.491740pt;} .ws1e8{word-spacing:10.528944pt;} .ws51c{word-spacing:10.556485pt;} .ws262{word-spacing:10.566149pt;} .ws333{word-spacing:10.573590pt;} .ws385{word-spacing:10.576484pt;} .ws591{word-spacing:10.603354pt;} .ws2c1{word-spacing:10.640559pt;} .ws193{word-spacing:10.677763pt;} .ws541{word-spacing:10.678761pt;} .wsa{word-spacing:10.681484pt;} .ws4aa{word-spacing:10.695125pt;} .ws429{word-spacing:10.717035pt;} .ws1f5{word-spacing:10.752173pt;} .ws3d0{word-spacing:10.767881pt;} .ws136{word-spacing:10.789378pt;} .ws46{word-spacing:10.825342pt;} .ws52c{word-spacing:10.841796pt;} .ws69{word-spacing:10.861307pt;} .ws4fa{word-spacing:10.878256pt;} .ws20d{word-spacing:10.900992pt;} .ws271{word-spacing:10.909259pt;} .ws476{word-spacing:10.913393pt;} .ws539{word-spacing:10.923313pt;} .ws1e9{word-spacing:10.938197pt;} .ws394{word-spacing:10.963000pt;} .ws32c{word-spacing:10.969200pt;} .ws2e9{word-spacing:10.975401pt;} .ws3c1{word-spacing:10.986149pt;} .ws354{word-spacing:11.005165pt;} .ws2a4{word-spacing:11.012606pt;} .ws409{word-spacing:11.022527pt;} .ws1d2{word-spacing:11.049811pt;} .wsda{word-spacing:11.077094pt;} .ws337{word-spacing:11.113059pt;} .ws21b{word-spacing:11.124220pt;} .ws2a5{word-spacing:11.161425pt;} .ws11f{word-spacing:11.198630pt;} .ws366{word-spacing:11.208964pt;} .ws58d{word-spacing:11.235835pt;} .ws4df{word-spacing:11.249382pt;} .ws8e{word-spacing:11.256917pt;} .ws223{word-spacing:11.273039pt;} .ws39d{word-spacing:11.279240pt;} .ws68{word-spacing:11.292882pt;} .ws2bc{word-spacing:11.310244pt;} .ws48f{word-spacing:11.313551pt;} .ws520{word-spacing:11.347449pt;} .ws43{word-spacing:11.364811pt;} .ws535{word-spacing:11.371658pt;} .ws27f{word-spacing:11.384654pt;} .ws292{word-spacing:11.459063pt;} .ws181{word-spacing:11.496268pt;} .ws263{word-spacing:11.533473pt;} .ws19a{word-spacing:11.554142pt;} .ws147{word-spacing:11.570677pt;} .ws4f6{word-spacing:11.585146pt;} .ws24b{word-spacing:11.607882pt;} .ws187{word-spacing:11.645087pt;} .ws26e{word-spacing:11.719496pt;} .ws2ce{word-spacing:11.756701pt;} .wsb2{word-spacing:11.760421pt;} .ws309{word-spacing:11.793906pt;} .ws294{word-spacing:11.822843pt;} .ws138{word-spacing:11.831111pt;} .ws4b8{word-spacing:11.868315pt;} .ws1ff{word-spacing:11.905520pt;} .ws439{word-spacing:11.911721pt;} .ws27a{word-spacing:11.942725pt;} .ws224{word-spacing:11.979930pt;} .ws3f2{word-spacing:12.004733pt;} .ws114{word-spacing:12.054339pt;} .ws13e{word-spacing:12.091544pt;} .ws58f{word-spacing:12.128749pt;} .ws1e{word-spacing:12.191997pt;} .ws3a8{word-spacing:12.192823pt;} .ws32e{word-spacing:12.227961pt;} .ws25a{word-spacing:12.240363pt;} .ws4cc{word-spacing:12.277568pt;} .ws522{word-spacing:12.314772pt;} .ws498{word-spacing:12.332134pt;} .ws36b{word-spacing:12.333375pt;} .ws327{word-spacing:12.351977pt;} .ws2b0{word-spacing:12.389182pt;} .ws3bb{word-spacing:12.404890pt;} .ws127{word-spacing:12.426387pt;} .ws3d{word-spacing:12.443749pt;} .ws396{word-spacing:12.473926pt;} .ws3da{word-spacing:12.477646pt;} .ws4b{word-spacing:12.479713pt;} .ws4a7{word-spacing:12.514024pt;} .ws139{word-spacing:12.538001pt;} .ws3d1{word-spacing:12.550402pt;} .ws1a2{word-spacing:12.575206pt;} .ws17b{word-spacing:12.612410pt;} .ws289{word-spacing:12.649615pt;} .ws2c4{word-spacing:12.686820pt;} .ws461{word-spacing:12.719891pt;} .ws182{word-spacing:12.724025pt;} .ws21e{word-spacing:12.761229pt;} .ws113{word-spacing:12.798434pt;} .ws4a1{word-spacing:12.805048pt;} .ws2e0{word-spacing:12.835639pt;} .ws3a1{word-spacing:12.860442pt;} .ws320{word-spacing:12.910048pt;} .ws101{word-spacing:12.984458pt;} .ws2a8{word-spacing:13.021663pt;} .ws47d{word-spacing:13.059694pt;} .ws73{word-spacing:13.091111pt;} .wsf6{word-spacing:13.170482pt;} .ws456{word-spacing:13.176682pt;} .ws130{word-spacing:13.207686pt;} .ws303{word-spacing:13.244891pt;} .ws291{word-spacing:13.282096pt;} .ws2e4{word-spacing:13.356505pt;} .ws2fd{word-spacing:13.381308pt;} .ws38d{word-spacing:13.387509pt;} .ws156{word-spacing:13.393710pt;} .ws474{word-spacing:13.423474pt;} .ws1dc{word-spacing:13.430915pt;} .ws519{word-spacing:13.450348pt;} .ws4c1{word-spacing:13.468120pt;} .ws134{word-spacing:13.505324pt;} .ws36{word-spacing:13.522686pt;} .ws1a4{word-spacing:13.542529pt;} .ws36e{word-spacing:13.563198pt;} .ws212{word-spacing:13.579734pt;} .ws2c2{word-spacing:13.616939pt;} .ws3a6{word-spacing:13.633474pt;} .ws208{word-spacing:13.654143pt;} .wsc9{word-spacing:13.666545pt;} .ws3b1{word-spacing:13.668612pt;} .ws58c{word-spacing:13.691348pt;} .ws35a{word-spacing:13.702509pt;} .ws46b{word-spacing:13.714498pt;} .wsf2{word-spacing:13.728553pt;} .ws3fd{word-spacing:13.750876pt;} .ws2b5{word-spacing:13.765758pt;} .ws59{word-spacing:13.774439pt;} .ws1f7{word-spacing:13.802962pt;} .ws197{word-spacing:13.840167pt;} .ws170{word-spacing:13.877372pt;} .ws40d{word-spacing:13.896388pt;} .ws2d1{word-spacing:13.914577pt;} .ws141{word-spacing:13.951781pt;} .wsd8{word-spacing:13.954262pt;} .ws400{word-spacing:13.969143pt;} .ws527{word-spacing:13.980210pt;} .ws3a7{word-spacing:13.984852pt;} .ws2f7{word-spacing:13.988986pt;} .ws384{word-spacing:14.019990pt;} .ws3f0{word-spacing:14.041899pt;} .ws1e5{word-spacing:14.063396pt;} .ws28c{word-spacing:14.100600pt;} .ws2bd{word-spacing:14.137805pt;} .ws3ee{word-spacing:14.151033pt;} .ws34d{word-spacing:14.170049pt;} .ws135{word-spacing:14.175010pt;} .ws528{word-spacing:14.224762pt;} .ws148{word-spacing:14.286624pt;} .ws40f{word-spacing:14.296545pt;} .ws43f{word-spacing:14.301093pt;} .ws32b{word-spacing:14.313907pt;} .ws254{word-spacing:14.361034pt;} .ws55{word-spacing:14.385837pt;} .ws18f{word-spacing:14.472648pt;} .ws36c{word-spacing:14.476782pt;} .wsc5{word-spacing:14.493730pt;} .ws47c{word-spacing:14.514813pt;} .ws1ca{word-spacing:14.547057pt;} .ws319{word-spacing:14.584262pt;} .ws2f2{word-spacing:14.658672pt;} .ws1d9{word-spacing:14.770286pt;} .ws378{word-spacing:14.793022pt;} .wsc1{word-spacing:14.817412pt;} .ws1c3{word-spacing:14.844695pt;} .ws256{word-spacing:14.881900pt;} .ws25c{word-spacing:14.956310pt;} .ws372{word-spacing:14.968711pt;} .ws3ef{word-spacing:15.096861pt;} .ws117{word-spacing:15.105129pt;} .ws3a5{word-spacing:15.109262pt;} .ws472{word-spacing:15.169617pt;} .ws18c{word-spacing:15.179538pt;} .ws416{word-spacing:15.205995pt;} .ws243{word-spacing:15.216743pt;} .ws4a0{word-spacing:15.242373pt;} .ws60{word-spacing:15.248987pt;} .ws390{word-spacing:15.284951pt;} .ws1ef{word-spacing:15.291152pt;} .ws2a2{word-spacing:15.328357pt;} .ws222{word-spacing:15.365562pt;} .ws2d8{word-spacing:15.402767pt;} .ws58e{word-spacing:15.477176pt;} .ws336{word-spacing:15.500739pt;} .ws267{word-spacing:15.514381pt;} .ws307{word-spacing:15.625995pt;} .ws145{word-spacing:15.700405pt;} .ws246{word-spacing:15.737609pt;} .ws188{word-spacing:15.774814pt;} .wsb9{word-spacing:15.788456pt;} .ws245{word-spacing:15.812019pt;} .ws49e{word-spacing:15.824420pt;} .ws205{word-spacing:15.849224pt;} .ws4e{word-spacing:15.860385pt;} .ws2b7{word-spacing:15.886428pt;} .ws2ad{word-spacing:15.923633pt;} .ws36d{word-spacing:15.952570pt;} .ws481{word-spacing:16.006310pt;} .ws31b{word-spacing:16.035247pt;} .ws7f{word-spacing:16.040208pt;} .ws466{word-spacing:16.079066pt;} .ws43b{word-spacing:16.128259pt;} .ws25d{word-spacing:16.146862pt;} .ws4e7{word-spacing:16.181176pt;} .ws225{word-spacing:16.184066pt;} .ws6c{word-spacing:16.220031pt;} .ws102{word-spacing:16.221271pt;} .ws51{word-spacing:16.255995pt;} .ws49d{word-spacing:16.260956pt;} .ws4f1{word-spacing:16.262694pt;} .ws20a{word-spacing:16.295681pt;} .ws454{word-spacing:16.303948pt;} .ws206{word-spacing:16.332885pt;} .ws297{word-spacing:16.337019pt;} .ws24c{word-spacing:16.370090pt;} .ws34f{word-spacing:16.399854pt;} .ws314{word-spacing:16.407295pt;} .ws7{word-spacing:16.435818pt;} .ws2ef{word-spacing:16.444500pt;} .ws237{word-spacing:16.518909pt;} .ws283{word-spacing:16.556114pt;} .ws3d9{word-spacing:16.624736pt;} .ws25f{word-spacing:16.630523pt;} .ws1c4{word-spacing:16.667728pt;} .ws3f4{word-spacing:16.697492pt;} .ws58a{word-spacing:16.779342pt;} .ws436{word-spacing:16.795878pt;} .ws281{word-spacing:16.853752pt;} .ws94{word-spacing:16.867393pt;} .ws228{word-spacing:16.890957pt;} .ws590{word-spacing:16.928161pt;} .ws261{word-spacing:16.965366pt;} .ws393{word-spacing:17.006705pt;} .ws2bb{word-spacing:17.114185pt;} .ws2bf{word-spacing:17.151390pt;} .ws415{word-spacing:17.170406pt;} .ws2ae{word-spacing:17.188595pt;} .ws3f9{word-spacing:17.243161pt;} .ws242{word-spacing:17.263004pt;} .ws1b1{word-spacing:17.300209pt;} .wscd{word-spacing:17.334933pt;} .ws11d{word-spacing:17.337414pt;} .ws258{word-spacing:17.411823pt;} .ws95{word-spacing:17.550721pt;} .ws2b2{word-spacing:17.746666pt;} .ws1a3{word-spacing:17.783871pt;} .ws28a{word-spacing:17.821075pt;} .ws374{word-spacing:17.850012pt;} .ws143{word-spacing:17.969894pt;} .ws1a6{word-spacing:18.044304pt;} .ws21d{word-spacing:18.081509pt;} .ws10c{word-spacing:18.118713pt;} .wsc2{word-spacing:18.162119pt;} .ws3cf{word-spacing:18.225367pt;} .ws341{word-spacing:18.270013pt;} .ws33c{word-spacing:18.377906pt;} .ws2c3{word-spacing:18.379147pt;} .ws34c{word-spacing:18.413871pt;} .ws1df{word-spacing:18.416351pt;} .ws27b{word-spacing:18.453556pt;} .ws203{word-spacing:18.565170pt;} .ws253{word-spacing:18.602375pt;} .ws244{word-spacing:18.676785pt;} .ws25e{word-spacing:18.713989pt;} .ws42a{word-spacing:18.728458pt;} .ws1f1{word-spacing:18.751194pt;} .ws29c{word-spacing:18.788399pt;} .ws3bc{word-spacing:18.807415pt;} .ws199{word-spacing:18.809068pt;} .ws25b{word-spacing:18.862808pt;} .ws140{word-spacing:18.974423pt;} .ws412{word-spacing:18.989304pt;} .ws1da{word-spacing:19.011627pt;} .ws157{word-spacing:19.086037pt;} .ws209{word-spacing:19.309265pt;} .ws260{word-spacing:19.383675pt;} .ws316{word-spacing:19.495289pt;} .ws17f{word-spacing:19.569699pt;} .ws426{word-spacing:19.571765pt;} .ws111{word-spacing:19.644108pt;} .ws28d{word-spacing:19.718518pt;} .ws349{word-spacing:19.852455pt;} .ws1d3{word-spacing:19.941746pt;} .ws29f{word-spacing:20.090565pt;} .ws198{word-spacing:20.152573pt;} .ws3ce{word-spacing:20.226156pt;} .ws3be{word-spacing:20.298912pt;} .ws31e{word-spacing:20.574227pt;} .ws323{word-spacing:20.797455pt;} .ws2a3{word-spacing:21.020684pt;} .ws328{word-spacing:21.057889pt;} .ws1f6{word-spacing:21.206708pt;} .ws2c8{word-spacing:21.281117pt;} .ws361{word-spacing:21.398932pt;} .ws1b2{word-spacing:21.429936pt;} .ws1cc{word-spacing:21.467141pt;} .ws2fc{word-spacing:21.496078pt;} .ws3e5{word-spacing:21.499385pt;} .ws455{word-spacing:21.539483pt;} .ws452{word-spacing:21.574621pt;} .ws286{word-spacing:21.615960pt;} .ws11e{word-spacing:21.727574pt;} .ws2d5{word-spacing:21.764779pt;} .ws315{word-spacing:21.801984pt;} .ws330{word-spacing:21.830507pt;} .ws189{word-spacing:21.950803pt;} .ws121{word-spacing:22.025212pt;} .ws72{word-spacing:22.082259pt;} .ws300{word-spacing:22.136826pt;} .ws1bf{word-spacing:22.174031pt;} .ws195{word-spacing:22.360055pt;} .ws3b{word-spacing:22.513834pt;} .ws9e{word-spacing:22.585764pt;} .ws47f{word-spacing:22.808992pt;} .ws49f{word-spacing:22.881748pt;} .ws20b{word-spacing:23.401788pt;} .ws26f{word-spacing:23.550607pt;} .ws5e{word-spacing:23.808560pt;} .ws414{word-spacing:24.118599pt;} .wscf{word-spacing:24.168206pt;} .wsbf{word-spacing:24.276099pt;} .ws1f8{word-spacing:24.294702pt;} .ws33e{word-spacing:24.312064pt;} .ws18a{word-spacing:24.480726pt;} .ws29e{word-spacing:24.517930pt;} .ws2d7{word-spacing:24.555135pt;} .ws196{word-spacing:24.778364pt;} .ws2f1{word-spacing:24.852773pt;} .ws2df{word-spacing:24.889978pt;} .ws1cb{word-spacing:25.076002pt;} .ws2e8{word-spacing:25.150411pt;} .ws317{word-spacing:25.373640pt;} .ws343{word-spacing:25.462931pt;} .ws58b{word-spacing:25.634073pt;} .ws214{word-spacing:25.782892pt;} .wsfb{word-spacing:25.857301pt;} .ws26b{word-spacing:25.931711pt;} .ws2f0{word-spacing:25.968916pt;} .ws42f{word-spacing:26.985845pt;} .ws293{word-spacing:27.085058pt;} .ws4f{word-spacing:27.117302pt;} .ws215{word-spacing:27.196672pt;} .ws2e1{word-spacing:27.308287pt;} .ws2d9{word-spacing:27.419901pt;} .ws1e1{word-spacing:27.494310pt;} .ws213{word-spacing:27.531515pt;} .ws2a1{word-spacing:27.866358pt;} .ws122{word-spacing:27.940767pt;} .ws2cb{word-spacing:28.015177pt;} .ws1db{word-spacing:28.387224pt;} .ws26c{word-spacing:28.684862pt;} .ws428{word-spacing:28.848150pt;} .ws440{word-spacing:29.691457pt;} .ws3d4{word-spacing:29.866320pt;} .ws387{word-spacing:29.902284pt;} .ws1d7{word-spacing:30.210257pt;} .ws18b{word-spacing:31.140376pt;} .ws249{word-spacing:31.326400pt;} .ws39b{word-spacing:31.624038pt;} .ws2f3{word-spacing:32.591361pt;} .ws2a0{word-spacing:32.851794pt;} .ws270{word-spacing:33.075023pt;} .ws2ba{word-spacing:33.112228pt;} .ws403{word-spacing:33.285850pt;} .ws1e7{word-spacing:34.302780pt;} .ws2eb{word-spacing:35.381717pt;} .ws321{word-spacing:36.200222pt;} .ws3d3{word-spacing:36.341600pt;} .ws3d8{word-spacing:36.450734pt;} .ws2b1{word-spacing:37.353569pt;} .ws31d{word-spacing:38.320893pt;} .ws2e2{word-spacing:38.358097pt;} .ws1b0{word-spacing:38.506916pt;} .ws425{word-spacing:39.178669pt;} .ws218{word-spacing:41.557706pt;} .ws259{word-spacing:42.376210pt;} .ws112{word-spacing:45.799047pt;} .ws200{word-spacing:49.147475pt;} .ws553{word-spacing:50.621196pt;} .ws551{word-spacing:51.799347pt;} .ws2f4{word-spacing:61.387838pt;} .ws554{word-spacing:68.686169pt;} .ws552{word-spacing:69.196701pt;} .wsdb{word-spacing:70.562529pt;} .ws55c{word-spacing:139.269250pt;} .ws55a{word-spacing:139.662296pt;} .ws557{word-spacing:140.055342pt;} ._1e{margin-left:-2682.856160pt;} ._85{margin-left:-2226.930557pt;} ._83{margin-left:-2218.129567pt;} ._43{margin-left:-1799.760280pt;} ._49{margin-left:-1623.696052pt;} ._41{margin-left:-1095.538117pt;} ._40{margin-left:-850.592770pt;} ._3f{margin-left:-762.350131pt;} ._42{margin-left:-640.417763pt;} ._84{margin-left:-342.455010pt;} ._71{margin-left:-286.531726pt;} ._9{margin-left:-256.867501pt;} ._2{margin-left:-238.297223pt;} ._55{margin-left:-143.077753pt;} ._4e{margin-left:-139.908750pt;} ._6c{margin-left:-137.833416pt;} ._4f{margin-left:-110.415058pt;} ._67{margin-left:-101.838557pt;} ._5d{margin-left:-89.276032pt;} ._6e{margin-left:-60.754907pt;} ._50{margin-left:-59.504410pt;} ._66{margin-left:-51.570884pt;} ._69{margin-left:-44.309262pt;} ._6a{margin-left:-41.812979pt;} ._16{margin-left:-40.707193pt;} ._1d{margin-left:-37.937600pt;} ._5c{margin-left:-36.878070pt;} ._13{margin-left:-35.261773pt;} ._1c{margin-left:-32.654526pt;} ._21{margin-left:-30.433485pt;} ._17{margin-left:-28.859641pt;} ._20{margin-left:-27.550554pt;} ._14{margin-left:-26.313310pt;} ._d{margin-left:-24.878733pt;} ._c{margin-left:-22.788346pt;} ._18{margin-left:-21.665282pt;} ._e{margin-left:-19.744605pt;} ._19{margin-left:-18.319536pt;} ._a2{margin-left:-17.184271pt;} ._11{margin-left:-16.091491pt;} ._b{margin-left:-14.833451pt;} ._a{margin-left:-13.070985pt;} ._38{margin-left:-11.986978pt;} ._10{margin-left:-10.534141pt;} ._12{margin-left:-9.299462pt;} ._31{margin-left:-8.080479pt;} ._3{margin-left:-5.848657pt;} ._0{margin-left:-3.851590pt;} ._1{margin-left:-2.002008pt;} ._6{width:1.853316pt;} ._7{width:3.148714pt;} ._15{width:4.194450pt;} ._5{width:5.612347pt;} ._8{width:7.471107pt;} ._f{width:11.405937pt;} ._4{width:12.476882pt;} ._82{width:15.663200pt;} ._81{width:18.527966pt;} ._4c{width:22.075543pt;} ._76{width:24.440649pt;} ._54{width:25.716667pt;} ._5f{width:27.219184pt;} ._58{width:28.891451pt;} ._7c{width:30.138983pt;} ._79{width:33.367958pt;} ._6d{width:35.363370pt;} ._2f{width:36.605340pt;} ._63{width:38.461929pt;} ._3c{width:39.873343pt;} ._72{width:42.454420pt;} ._73{width:43.546214pt;} ._5a{width:45.230311pt;} ._65{width:48.451813pt;} ._80{width:49.891570pt;} ._37{width:51.001511pt;} ._52{width:52.142716pt;} ._7a{width:54.743997pt;} ._35{width:55.848464pt;} ._74{width:57.712039pt;} ._47{width:59.692954pt;} ._34{width:60.767758pt;} ._44{width:62.402700pt;} ._46{width:64.522524pt;} ._45{width:65.583707pt;} ._62{width:67.827714pt;} ._7f{width:68.925974pt;} ._33{width:70.099950pt;} ._9b{width:71.437254pt;} ._36{width:72.957481pt;} ._2b{width:74.259648pt;} ._75{width:76.124795pt;} ._61{width:77.783808pt;} ._3b{width:79.830025pt;} ._27{width:81.276877pt;} ._29{width:82.434358pt;} ._28{width:83.881209pt;} ._2d{width:85.183376pt;} ._2c{width:86.823671pt;} ._25{width:88.438791pt;} ._2e{width:89.560101pt;} ._2a{width:91.332494pt;} ._6f{width:92.732230pt;} ._68{width:93.973989pt;} ._94{width:95.572160pt;} ._26{width:96.685844pt;} ._30{width:98.385894pt;} ._39{width:99.941260pt;} ._56{width:101.124699pt;} ._3a{width:102.992235pt;} ._59{width:104.880471pt;} ._70{width:106.826598pt;} ._78{width:107.986499pt;} ._5b{width:110.512703pt;} ._86{width:111.633016pt;} ._95{width:112.847186pt;} ._89{width:113.896732pt;} ._7b{width:115.658160pt;} ._60{width:117.926850pt;} ._5e{width:119.449371pt;} ._57{width:121.524880pt;} ._4b{width:123.309955pt;} ._90{width:124.560119pt;} ._7d{width:125.973430pt;} ._64{width:127.161639pt;} ._6b{width:131.377190pt;} ._51{width:133.628700pt;} ._53{width:136.491934pt;} ._4d{width:140.042240pt;} ._77{width:141.106399pt;} ._8b{width:144.677817pt;} ._96{width:151.574907pt;} ._8f{width:158.492620pt;} ._88{width:163.293426pt;} ._9f{width:170.596839pt;} ._7e{width:189.149707pt;} ._1f{width:193.893068pt;} ._8a{width:199.379629pt;} ._9c{width:222.227630pt;} ._9d{width:224.859680pt;} ._91{width:230.845018pt;} ._98{width:242.669106pt;} ._99{width:244.594155pt;} ._9e{width:251.118645pt;} ._9a{width:283.420353pt;} ._97{width:284.714150pt;} ._8c{width:323.159703pt;} ._87{width:331.017517pt;} ._8d{width:334.879930pt;} ._8e{width:347.173316pt;} ._93{width:349.602352pt;} ._92{width:359.546548pt;} ._1b{width:401.831002pt;} ._32{width:515.408336pt;} ._1a{width:572.559465pt;} ._a1{width:606.736788pt;} ._4a{width:615.915765pt;} ._48{width:747.304457pt;} ._3d{width:920.648795pt;} ._3e{width:1138.816087pt;} ._a0{width:1674.680139pt;} ._22{width:1797.158479pt;} ._23{width:1808.830023pt;} ._24{width:1813.749317pt;} .fs23{font-size:20.669306pt;} .fs22{font-size:24.803167pt;} .fs19{font-size:28.937028pt;} .fs18{font-size:29.957768pt;} .fs38{font-size:32.088683pt;} .fs4{font-size:33.070889pt;} .fs51{font-size:33.149432pt;} .fs60{font-size:34.497484pt;} .fs26{font-size:35.137819pt;} .fs10{font-size:35.964592pt;} .fs31{font-size:36.171285pt;} .fs27{font-size:36.377978pt;} .fs15{font-size:37.204750pt;} .fs3f{font-size:37.633845pt;} .fs34{font-size:39.271681pt;} .fs33{font-size:40.758630pt;} .fs11{font-size:40.853296pt;} .fs8{font-size:41.338611pt;} .fs2c{font-size:41.855344pt;} .fs65{font-size:41.981840pt;} .fs7{font-size:42.900384pt;} .fs55{font-size:43.671762pt;} .fs32{font-size:44.645700pt;} .fs3e{font-size:45.472472pt;} .fs64{font-size:47.229363pt;} .fs67{font-size:47.362887pt;} .fs5a{font-size:47.539403pt;} .fs35{font-size:47.611745pt;} .fs14{font-size:49.606333pt;} .fs5c{font-size:49.732416pt;} .fs50{font-size:50.033775pt;} .fs2d{font-size:50.226413pt;} .fsd{font-size:50.227653pt;} .fs66{font-size:53.282989pt;} .fs17{font-size:53.740194pt;} .fs42{font-size:55.225904pt;} .fs3a{font-size:56.840590pt;} .fs3{font-size:57.200236pt;} .fs16{font-size:57.874056pt;} .fs2e{font-size:58.226674pt;} .fs3d{font-size:59.527600pt;} .fs29{font-size:60.372975pt;} .fs1a{font-size:62.007917pt;} .fsc{font-size:64.128587pt;} .fs62{font-size:64.770989pt;} .fs43{font-size:67.526621pt;} .fs4c{font-size:70.762608pt;} .fs9{font-size:71.474872pt;} .fs37{font-size:72.222687pt;} .fs6{font-size:74.409500pt;} .fs47{font-size:75.029579pt;} .fs63{font-size:77.509997pt;} .fs12{font-size:81.551158pt;} .fs1f{font-size:82.677222pt;} .fs5f{font-size:83.390313pt;} .fsa{font-size:83.982696pt;} .fse{font-size:86.521713pt;} .fs5b{font-size:86.811083pt;} .fs40{font-size:87.198840pt;} .fs30{font-size:87.844549pt;} .fs61{font-size:90.944944pt;} .fs1e{font-size:92.598489pt;} .fs4d{font-size:95.078806pt;} .fs56{font-size:95.351656pt;} .fs36{font-size:97.713315pt;} .fs1{font-size:99.212667pt;} .fs44{font-size:103.540819pt;} .fs54{font-size:107.194739pt;} .fs53{font-size:107.480389pt;} .fs13{font-size:111.614250pt;} .fs48{font-size:115.045355pt;} .fs25{font-size:115.748111pt;} .fs2f{font-size:118.848507pt;} .fs2{font-size:123.100596pt;} .fs28{font-size:128.149694pt;} .fs1d{font-size:132.283556pt;} .fs41{font-size:133.704777pt;} .fs49{font-size:133.866411pt;} .fs58{font-size:136.417417pt;} .fs24{font-size:142.618208pt;} .fs4b{font-size:144.685139pt;} .fs20{font-size:147.785535pt;} .fs4a{font-size:148.048035pt;} .fs39{font-size:150.679237pt;} .fs1b{font-size:158.740267pt;} .fs21{font-size:160.982060pt;} .fs5e{font-size:165.747161pt;} .fs59{font-size:167.421375pt;} .fs52{font-size:169.936003pt;} .fs3c{font-size:170.521771pt;} .fs2b{font-size:173.002088pt;} .fsf{font-size:186.023750pt;} .fs4e{font-size:193.504385pt;} .fs4f{font-size:195.458875pt;} .fs3b{font-size:198.425333pt;} .fs2a{font-size:200.905650pt;} .fs46{font-size:206.693056pt;} .fs45{font-size:209.161270pt;} .fs5d{font-size:215.595325pt;} .fs57{font-size:224.439308pt;} .fs5{font-size:280.455606pt;} .fsb{font-size:295.386699pt;} .fs1c{font-size:357.165600pt;} .fs0{font-size:373.940808pt;} .yf{bottom:0.000000pt;} .y12{bottom:5.709067pt;} .ye6b{bottom:14.785600pt;} .ye67{bottom:14.785867pt;} .ye69{bottom:14.786133pt;} .yce{bottom:22.574400pt;} .y17f{bottom:22.677200pt;} .ycd{bottom:23.131067pt;} .y180{bottom:23.423733pt;} .ybd4{bottom:23.966267pt;} .y11{bottom:37.794667pt;} .ye{bottom:37.795333pt;} .y3e0{bottom:38.659867pt;} .y5b9{bottom:51.659867pt;} .y42{bottom:52.462000pt;} .ybb5{bottom:56.600172pt;} .ybb2{bottom:56.615101pt;} .ybb3{bottom:56.618800pt;} .y927{bottom:56.700133pt;} .y930{bottom:56.724133pt;} .y939{bottom:56.748133pt;} .ya6c{bottom:58.197467pt;} .ya72{bottom:58.221467pt;} .ya78{bottom:58.245467pt;} .y86f{bottom:58.354400pt;} .y877{bottom:58.378400pt;} .y87f{bottom:58.402400pt;} .y602{bottom:59.042267pt;} .y673{bottom:59.100667pt;} .y47d{bottom:59.101333pt;} .y5df{bottom:59.126267pt;} .y41e{bottom:59.141467pt;} .y404{bottom:59.177467pt;} .y650{bottom:59.181200pt;} .y43b{bottom:59.207200pt;} .y481{bottom:59.212667pt;} .y72c{bottom:59.214933pt;} .y752{bottom:59.217333pt;} .y7fb{bottom:59.224400pt;} .y7dc{bottom:59.247867pt;} .y7bb{bottom:59.265867pt;} .y796{bottom:59.275600pt;} .y6bc{bottom:59.281600pt;} .y6e0{bottom:59.349600pt;} .y4e5{bottom:59.506400pt;} .y8ad{bottom:60.202133pt;} .y8b3{bottom:60.226133pt;} .y350{bottom:62.047200pt;} .yac5{bottom:62.253733pt;} .y5b8{bottom:62.278800pt;} .yac2{bottom:62.286267pt;} .y583{bottom:62.405733pt;} .yd29{bottom:62.570133pt;} .yabd{bottom:64.141600pt;} .yf33{bottom:64.308133pt;} .yb21{bottom:65.731200pt;} .y387{bottom:66.290667pt;} .y10c{bottom:66.519733pt;} .ycc{bottom:66.537733pt;} .y239{bottom:66.563733pt;} .ya4{bottom:66.580933pt;} .y10b{bottom:66.591733pt;} .y975{bottom:66.596267pt;} .y245{bottom:66.611733pt;} .y97e{bottom:66.632267pt;} .y147{bottom:66.634933pt;} .y1ab{bottom:66.635600pt;} .y1f4{bottom:66.635733pt;} .y27c{bottom:66.639733pt;} .y3ab{bottom:66.655733pt;} .y987{bottom:66.668267pt;} .y257{bottom:66.683733pt;} .y7b{bottom:66.717733pt;} .y1c9{bottom:66.755600pt;} .y212{bottom:66.755733pt;} .y29b{bottom:66.759733pt;} .y383{bottom:66.767733pt;} .y1cf{bottom:66.779600pt;} .y2d9{bottom:66.999733pt;} .y41{bottom:67.128667pt;} .y3d3{bottom:67.797067pt;} .y9a3{bottom:67.857867pt;} .y9a9{bottom:67.869867pt;} .yb63{bottom:68.117733pt;} .yd2d{bottom:68.976400pt;} .yb47{bottom:69.398933pt;} .yd{bottom:69.795333pt;} .yb85{bottom:70.771867pt;} .y43a{bottom:71.209867pt;} .y926{bottom:71.364133pt;} .y92f{bottom:71.388133pt;} .y938{bottom:71.412133pt;} .y581{bottom:72.294533pt;} .y696{bottom:73.252667pt;} .y672{bottom:73.415067pt;} .y584{bottom:73.471733pt;} .y64f{bottom:73.495600pt;} .ybb4{bottom:73.506271pt;} .ybb1{bottom:73.521200pt;} .y7ba{bottom:73.579867pt;} .y795{bottom:73.589600pt;} .y6bb{bottom:73.595600pt;} .y6df{bottom:73.663600pt;} .y703{bottom:73.731600pt;} .y601{bottom:73.766267pt;} .y5de{bottom:73.850267pt;} .y72b{bottom:73.940267pt;} .y751{bottom:73.942667pt;} .y773{bottom:73.947333pt;} .y7fa{bottom:73.949733pt;} .y818{bottom:73.956800pt;} .y7db{bottom:73.973200pt;} .y47c{bottom:73.981333pt;} .ya03{bottom:74.006533pt;} .ya09{bottom:74.018533pt;} .y41d{bottom:74.117467pt;} .y403{bottom:74.153467pt;} .y582{bottom:74.184400pt;} .ya6b{bottom:74.193467pt;} .ya71{bottom:74.217467pt;} .ya77{bottom:74.241467pt;} .y86e{bottom:74.350400pt;} .y876{bottom:74.374400pt;} .y87e{bottom:74.398400pt;} .y4e4{bottom:74.446400pt;} .yf42{bottom:74.697600pt;} .yf3b{bottom:74.842667pt;} .yf32{bottom:75.508133pt;} .y3df{bottom:75.993200pt;} .yd66{bottom:76.062102pt;} .y8ab{bottom:76.198133pt;} .y8b2{bottom:76.222133pt;} .y8b9{bottom:76.246133pt;} .ya25{bottom:77.135467pt;} .y8ac{bottom:77.290133pt;} .yc98{bottom:78.766480pt;} .y388{bottom:79.370133pt;} .y3d2{bottom:79.799733pt;} .yd1e{bottom:81.788933pt;} .y8d6{bottom:82.305333pt;} .y9a2{bottom:82.521867pt;} .y9a8{bottom:82.533867pt;} .ycb{bottom:82.534133pt;} .y17e{bottom:82.544133pt;} .y238{bottom:82.559733pt;} .ya3{bottom:82.577333pt;} .y10a{bottom:82.588133pt;} .y974{bottom:82.592267pt;} .y244{bottom:82.607733pt;} .y97d{bottom:82.628267pt;} .y146{bottom:82.631333pt;} .y1aa{bottom:82.631600pt;} .y1f3{bottom:82.631733pt;} .y27b{bottom:82.635733pt;} .y3aa{bottom:82.651733pt;} .y986{bottom:82.664267pt;} .y256{bottom:82.679733pt;} .y7a{bottom:82.714133pt;} .y1c8{bottom:82.751600pt;} .y211{bottom:82.751733pt;} .y29a{bottom:82.755733pt;} .y382{bottom:82.763733pt;} .y1ce{bottom:82.775600pt;} .yb62{bottom:82.781733pt;} .y2d8{bottom:82.995733pt;} .yf0d{bottom:83.110097pt;} .y439{bottom:83.212533pt;} .yb46{bottom:84.062933pt;} .yac1{bottom:84.210667pt;} .yafd{bottom:84.707388pt;} .yaf9{bottom:84.720534pt;} .yc{bottom:85.795333pt;} .y925{bottom:86.028133pt;} .y92e{bottom:86.052133pt;} .yac4{bottom:86.066000pt;} .y937{bottom:86.076133pt;} .y695{bottom:87.567067pt;} .y671{bottom:87.729467pt;} .y64e{bottom:87.810000pt;} .y7b9{bottom:87.893867pt;} .y794{bottom:87.903600pt;} .y6ba{bottom:87.909600pt;} .y6de{bottom:87.977600pt;} .y702{bottom:88.045600pt;} .y623{bottom:88.406267pt;} .y600{bottom:88.490267pt;} .y5dd{bottom:88.574267pt;} .y40{bottom:88.580227pt;} .y72a{bottom:88.668000pt;} .ya02{bottom:88.670533pt;} .y772{bottom:88.672667pt;} .y729{bottom:88.675067pt;} .y817{bottom:88.682133pt;} .ya08{bottom:88.682533pt;} .ya0e{bottom:88.694533pt;} .y7da{bottom:88.698533pt;} .y47b{bottom:88.861333pt;} .y41c{bottom:89.093467pt;} .y402{bottom:89.129467pt;} .y4e3{bottom:89.386400pt;} .ya6a{bottom:90.189467pt;} .ya70{bottom:90.213467pt;} .ya76{bottom:90.237467pt;} .y86d{bottom:90.346400pt;} .y875{bottom:90.370400pt;} .y87d{bottom:90.394400pt;} .ybb9{bottom:90.399224pt;} .ybaf{bottom:90.412370pt;} .ybb0{bottom:90.423600pt;} .yd65{bottom:91.697414pt;} .y3d1{bottom:91.802400pt;} .yf4b{bottom:92.000800pt;} .y8aa{bottom:92.194133pt;} .y8b1{bottom:92.218133pt;} .y8b8{bottom:92.242133pt;} .y1e{bottom:92.395211pt;} .y9a1{bottom:97.185867pt;} .y9a7{bottom:97.197867pt;} .yb61{bottom:97.445733pt;} .yf2a{bottom:97.931067pt;} .yca{bottom:98.530533pt;} .y17d{bottom:98.540533pt;} .y237{bottom:98.555733pt;} .ya2{bottom:98.573733pt;} .y109{bottom:98.584533pt;} .y973{bottom:98.588267pt;} .y243{bottom:98.603733pt;} .y97c{bottom:98.624267pt;} .y1a9{bottom:98.627600pt;} .y145{bottom:98.627733pt;} .y27a{bottom:98.631733pt;} .y3a9{bottom:98.647733pt;} .y985{bottom:98.660267pt;} .y255{bottom:98.675733pt;} .y79{bottom:98.710533pt;} .yb45{bottom:98.726933pt;} .y1c7{bottom:98.747600pt;} .y210{bottom:98.747733pt;} .y299{bottom:98.751733pt;} .y381{bottom:98.759733pt;} .y1cd{bottom:98.771600pt;} .ye68{bottom:98.873467pt;} .y2d7{bottom:98.991733pt;} .ye1f{bottom:99.062267pt;} .y924{bottom:100.692133pt;} .y92d{bottom:100.716133pt;} .y936{bottom:100.740133pt;} .yafc{bottom:101.613487pt;} .yaf8{bottom:101.626633pt;} .yb01{bottom:101.657768pt;} .yb{bottom:101.795333pt;} .y694{bottom:101.881467pt;} .y670{bottom:102.043867pt;} .y64d{bottom:102.124400pt;} .y7b8{bottom:102.207867pt;} .y793{bottom:102.217600pt;} .y6b9{bottom:102.223600pt;} .y6dd{bottom:102.291600pt;} .y701{bottom:102.359600pt;} .y622{bottom:103.130267pt;} .y5ff{bottom:103.214267pt;} .y5dc{bottom:103.298267pt;} .ya01{bottom:103.334533pt;} .ya07{bottom:103.346533pt;} .ya0d{bottom:103.358533pt;} .y750{bottom:103.395733pt;} .y771{bottom:103.398000pt;} .y728{bottom:103.400400pt;} .y816{bottom:103.407467pt;} .y74f{bottom:103.409867pt;} .y7d9{bottom:103.423867pt;} .y47a{bottom:103.741333pt;} .y41b{bottom:104.069467pt;} .y401{bottom:104.105467pt;} .y4e2{bottom:104.326400pt;} .yabc{bottom:104.999667pt;} .yac0{bottom:106.135067pt;} .ya69{bottom:106.185467pt;} .ya6f{bottom:106.209467pt;} .ya75{bottom:106.233467pt;} .y86c{bottom:106.342400pt;} .y874{bottom:106.366400pt;} .y87c{bottom:106.390400pt;} .ybb8{bottom:107.305323pt;} .ybae{bottom:107.318469pt;} .yd64{bottom:107.332726pt;} .yac3{bottom:107.990403pt;} .y8a9{bottom:108.190133pt;} .y8b0{bottom:108.214133pt;} .y8b7{bottom:108.238133pt;} .ybeb{bottom:108.398587pt;} .y9a0{bottom:111.849867pt;} .y9a6{bottom:111.861867pt;} .yb60{bottom:112.109733pt;} .y3de{bottom:113.326533pt;} .yb44{bottom:113.390933pt;} .yc9{bottom:114.526933pt;} .y236{bottom:114.551733pt;} .ya1{bottom:114.570133pt;} .y108{bottom:114.580933pt;} .y972{bottom:114.584267pt;} .y242{bottom:114.599733pt;} .y97b{bottom:114.620267pt;} .y1a8{bottom:114.623600pt;} .y1f2{bottom:114.623733pt;} .y144{bottom:114.624133pt;} .y279{bottom:114.627733pt;} .y3a8{bottom:114.643733pt;} .y984{bottom:114.656267pt;} .y254{bottom:114.671733pt;} .y78{bottom:114.706933pt;} .y1c6{bottom:114.743600pt;} .y20f{bottom:114.743733pt;} .y298{bottom:114.747733pt;} .y380{bottom:114.755733pt;} .y1cc{bottom:114.767600pt;} .y22d{bottom:114.863733pt;} .y2d6{bottom:114.987733pt;} .ye1e{bottom:115.062267pt;} .y923{bottom:115.356133pt;} .y92c{bottom:115.380133pt;} .y935{bottom:115.404133pt;} .y693{bottom:116.195867pt;} .y66f{bottom:116.358267pt;} .y64c{bottom:116.438800pt;} .y7b7{bottom:116.521867pt;} .y792{bottom:116.531600pt;} .y6b8{bottom:116.537600pt;} .y6dc{bottom:116.605600pt;} .y700{bottom:116.673600pt;} .ya{bottom:117.795333pt;} .y621{bottom:117.854267pt;} .y5fe{bottom:117.938267pt;} .ya00{bottom:117.998533pt;} .ya06{bottom:118.010533pt;} .y5db{bottom:118.022267pt;} .ya0c{bottom:118.022533pt;} .y770{bottom:118.123333pt;} .y727{bottom:118.125733pt;} .y815{bottom:118.132800pt;} .y74e{bottom:118.135200pt;} .y7d8{bottom:118.149200pt;} .yafb{bottom:118.519585pt;} .yaf7{bottom:118.532732pt;} .yb00{bottom:118.563867pt;} .y479{bottom:118.621333pt;} .yb84{bottom:118.958400pt;} .y41a{bottom:119.045467pt;} .y400{bottom:119.081467pt;} .y8d5{bottom:119.090133pt;} .y4e1{bottom:119.266400pt;} .ya24{bottom:120.390133pt;} .ye65{bottom:120.952933pt;} .ya68{bottom:122.181467pt;} .ya6e{bottom:122.205467pt;} .ya74{bottom:122.229467pt;} .yebd{bottom:122.322533pt;} .y86b{bottom:122.338400pt;} .y873{bottom:122.362400pt;} .y87b{bottom:122.386400pt;} .ybea{bottom:122.964667pt;} .yd63{bottom:122.968038pt;} .y8a8{bottom:124.186133pt;} .y8af{bottom:124.210133pt;} .ybb7{bottom:124.211421pt;} .ybad{bottom:124.224568pt;} .y8b6{bottom:124.234133pt;} .y8da{bottom:125.559867pt;} .y99f{bottom:126.513867pt;} .y9a5{bottom:126.525867pt;} .y9ab{bottom:126.537867pt;} .yb5f{bottom:126.773733pt;} .yb43{bottom:128.054933pt;} .yf29{bottom:128.320400pt;} .y922{bottom:130.020133pt;} .y92b{bottom:130.044133pt;} .y934{bottom:130.068133pt;} .yf1a{bottom:130.154533pt;} .y692{bottom:130.510267pt;} .yc8{bottom:130.523333pt;} .y17c{bottom:130.544933pt;} .y235{bottom:130.547733pt;} .ya0{bottom:130.566533pt;} .y107{bottom:130.577333pt;} .y971{bottom:130.580267pt;} .y241{bottom:130.595733pt;} .y97a{bottom:130.616267pt;} .y1a7{bottom:130.619600pt;} .y1f1{bottom:130.619733pt;} .y143{bottom:130.620533pt;} .y278{bottom:130.623733pt;} .y3a7{bottom:130.639733pt;} .y983{bottom:130.652267pt;} .y253{bottom:130.667733pt;} .y66e{bottom:130.672667pt;} .y77{bottom:130.703333pt;} .y1c5{bottom:130.739600pt;} .y20e{bottom:130.739733pt;} .y297{bottom:130.743733pt;} .y37f{bottom:130.751733pt;} .y64b{bottom:130.753200pt;} .y1cb{bottom:130.763600pt;} .y7b6{bottom:130.835867pt;} .y791{bottom:130.845600pt;} .y6b7{bottom:130.851600pt;} .y22c{bottom:130.859733pt;} .y6db{bottom:130.919600pt;} .y2d5{bottom:130.983733pt;} .y6ff{bottom:130.987600pt;} .ye1d{bottom:131.062267pt;} .yabe{bottom:132.004000pt;} .yf31{bottom:132.198800pt;} .y3f{bottom:132.393693pt;} .y620{bottom:132.578267pt;} .y5fd{bottom:132.662267pt;} .y9ff{bottom:132.662533pt;} .ye85{bottom:132.671333pt;} .ya05{bottom:132.674533pt;} .ya0b{bottom:132.686533pt;} .y5da{bottom:132.746267pt;} .y726{bottom:132.851067pt;} .y76f{bottom:132.858133pt;} .y74d{bottom:132.860533pt;} .y7d7{bottom:132.874533pt;} .y478{bottom:133.501333pt;} .y9{bottom:133.795333pt;} .yf18{bottom:133.859867pt;} .yabf{bottom:133.863468pt;} .y419{bottom:134.021467pt;} .y3ff{bottom:134.057467pt;} .y4e0{bottom:134.206400pt;} .yabb{bottom:134.324667pt;} .yafe{bottom:135.412538pt;} .yafa{bottom:135.425684pt;} .yaf6{bottom:135.438831pt;} .yaff{bottom:135.466267pt;} .y1c{bottom:136.224607pt;} .ye64{bottom:136.952933pt;} .ybe8{bottom:137.530693pt;} .ybe9{bottom:137.530800pt;} .ye9f{bottom:137.634667pt;} .y1d{bottom:138.106851pt;} .ya67{bottom:138.177467pt;} .ya6d{bottom:138.201467pt;} .ya73{bottom:138.225467pt;} .yebc{bottom:138.322533pt;} .y86a{bottom:138.334400pt;} .y872{bottom:138.358400pt;} .y87a{bottom:138.382400pt;} .yd62{bottom:138.603350pt;} .yf28{bottom:139.520400pt;} .y8a7{bottom:140.182133pt;} .y8ae{bottom:140.206133pt;} .y8b4{bottom:140.230133pt;} .yd92{bottom:140.613732pt;} .ybb6{bottom:141.117520pt;} .ybac{bottom:141.130667pt;} .y99e{bottom:141.177867pt;} .y9a4{bottom:141.189867pt;} .y9aa{bottom:141.201867pt;} .y8b5{bottom:141.322133pt;} .yf19{bottom:141.354533pt;} .yc3f{bottom:141.428400pt;} .yb5e{bottom:141.437733pt;} .yb42{bottom:142.718933pt;} .yf30{bottom:143.398800pt;} .y921{bottom:144.684133pt;} .y92a{bottom:144.708133pt;} .y933{bottom:144.732133pt;} .y691{bottom:144.824667pt;} .y66d{bottom:144.987067pt;} .yf17{bottom:145.059867pt;} .y64a{bottom:145.067600pt;} .y7b5{bottom:145.149867pt;} .y790{bottom:145.159600pt;} .y6b6{bottom:145.165600pt;} .y6da{bottom:145.233600pt;} .y6fe{bottom:145.301600pt;} .yede{bottom:145.415333pt;} .yc7{bottom:146.519733pt;} .y17b{bottom:146.541333pt;} .y234{bottom:146.543733pt;} .y9f{bottom:146.562933pt;} .y106{bottom:146.573733pt;} .y970{bottom:146.576267pt;} .y240{bottom:146.591733pt;} .y979{bottom:146.612267pt;} .y1a6{bottom:146.615600pt;} .y1f0{bottom:146.615733pt;} .y142{bottom:146.616933pt;} .y277{bottom:146.619733pt;} .y3a6{bottom:146.635733pt;} .y982{bottom:146.648267pt;} .y252{bottom:146.663733pt;} .y76{bottom:146.699733pt;} .y1c4{bottom:146.735600pt;} .y20d{bottom:146.735733pt;} .y296{bottom:146.739733pt;} .y37e{bottom:146.747733pt;} .y1ca{bottom:146.759600pt;} .y22b{bottom:146.855733pt;} .y2d4{bottom:146.979733pt;} .ya23{bottom:147.051800pt;} .ye1c{bottom:147.062267pt;} .y61f{bottom:147.302267pt;} .y9fe{bottom:147.326533pt;} .ya04{bottom:147.338533pt;} .ya0a{bottom:147.350533pt;} .y5fc{bottom:147.386267pt;} .y5d9{bottom:147.470267pt;} .y725{bottom:147.578800pt;} .y724{bottom:147.581067pt;} .y76e{bottom:147.583467pt;} .y74c{bottom:147.585867pt;} .y7d6{bottom:147.599867pt;} .y7f9{bottom:147.682000pt;} .y477{bottom:148.381333pt;} .ye84{bottom:148.671333pt;} .y418{bottom:148.997467pt;} .y3fe{bottom:149.033467pt;} .y4df{bottom:149.146400pt;} .yc66{bottom:149.639867pt;} .y8d4{bottom:149.803467pt;} .ybe7{bottom:152.096773pt;} .y8d8{bottom:152.221533pt;} .ye63{bottom:152.952933pt;} .ye9e{bottom:153.634667pt;} .yd61{bottom:154.238662pt;} .yebb{bottom:154.322533pt;} .y869{bottom:154.330400pt;} .y871{bottom:154.354400pt;} .y879{bottom:154.378400pt;} .y8d9{bottom:154.799867pt;} .yb5d{bottom:156.101733pt;} .yf41{bottom:156.653600pt;} .yb41{bottom:157.382933pt;} .yd91{bottom:157.573116pt;} .yf3a{bottom:159.020000pt;} .y690{bottom:159.139067pt;} .y66c{bottom:159.301467pt;} .y920{bottom:159.348133pt;} .y929{bottom:159.372133pt;} .y649{bottom:159.382000pt;} .y932{bottom:159.396133pt;} .y7b4{bottom:159.463867pt;} .y78f{bottom:159.473600pt;} .y6b5{bottom:159.479600pt;} .y6d9{bottom:159.547600pt;} .y6fd{bottom:159.615600pt;} .y61e{bottom:162.026267pt;} .y5fb{bottom:162.110267pt;} .y5d8{bottom:162.194267pt;} .ye16{bottom:162.302267pt;} .y723{bottom:162.306400pt;} .y76d{bottom:162.308800pt;} .y74b{bottom:162.311200pt;} .y7d5{bottom:162.325200pt;} .y7f8{bottom:162.407333pt;} .yc6{bottom:162.519733pt;} .y17a{bottom:162.537733pt;} .y233{bottom:162.539733pt;} .y9e{bottom:162.559333pt;} .y105{bottom:162.570133pt;} .y96f{bottom:162.572267pt;} .y23f{bottom:162.587733pt;} .y978{bottom:162.608267pt;} .y1a5{bottom:162.611600pt;} .y1ef{bottom:162.611733pt;} .y141{bottom:162.613333pt;} .y276{bottom:162.615733pt;} .y3a5{bottom:162.631733pt;} .y981{bottom:162.644267pt;} .y251{bottom:162.659733pt;} .y75{bottom:162.696133pt;} .y1c3{bottom:162.731600pt;} .y20c{bottom:162.731733pt;} .y295{bottom:162.735733pt;} .y37d{bottom:162.743733pt;} .y22a{bottom:162.851733pt;} .y2d3{bottom:162.975733pt;} .ye1b{bottom:163.062267pt;} .y476{bottom:163.261333pt;} .y417{bottom:163.973467pt;} .y3fd{bottom:164.009467pt;} .y4de{bottom:164.086400pt;} .ye83{bottom:164.671333pt;} .y8{bottom:165.795333pt;} .ybe6{bottom:166.662853pt;} .yf40{bottom:167.853600pt;} .ye62{bottom:168.952933pt;} .ye9d{bottom:169.634667pt;} .yd60{bottom:169.873974pt;} .yf39{bottom:170.220000pt;} .yeba{bottom:170.322533pt;} .y868{bottom:170.326400pt;} .ye3e{bottom:170.345200pt;} .y870{bottom:170.350400pt;} .y878{bottom:170.374400pt;} .yb5c{bottom:170.765733pt;} .yb40{bottom:172.046933pt;} .y68f{bottom:173.453467pt;} .y66b{bottom:173.615867pt;} .y647{bottom:173.669600pt;} .y648{bottom:173.692000pt;} .ya22{bottom:173.713467pt;} .y7b3{bottom:173.777867pt;} .y78e{bottom:173.787600pt;} .y6b4{bottom:173.793600pt;} .y6d8{bottom:173.861600pt;} .y6fc{bottom:173.929600pt;} .y91f{bottom:174.012133pt;} .y928{bottom:174.036133pt;} .y931{bottom:174.060133pt;} .y61d{bottom:176.750267pt;} .y5fa{bottom:176.834267pt;} .y5d7{bottom:176.918267pt;} .y722{bottom:177.034133pt;} .y74a{bottom:177.036533pt;} .y7d4{bottom:177.050533pt;} .y721{bottom:177.052933pt;} .y7f7{bottom:177.132667pt;} .yd71{bottom:177.256340pt;} .y8d3{bottom:177.796800pt;} .y475{bottom:178.141333pt;} .ye15{bottom:178.302267pt;} .y179{bottom:178.534133pt;} .y232{bottom:178.535733pt;} .y9d{bottom:178.555733pt;} .y104{bottom:178.566533pt;} .y96e{bottom:178.568267pt;} .y23e{bottom:178.583733pt;} .y977{bottom:178.604267pt;} .yc88{bottom:178.605685pt;} .y1a4{bottom:178.607600pt;} .y1ee{bottom:178.607733pt;} .y140{bottom:178.609733pt;} .y275{bottom:178.611733pt;} .y3a4{bottom:178.627733pt;} .y980{bottom:178.640267pt;} .y250{bottom:178.655733pt;} .y74{bottom:178.692533pt;} .y1c2{bottom:178.727600pt;} .y20b{bottom:178.727733pt;} .y294{bottom:178.731733pt;} .y37c{bottom:178.739733pt;} .y229{bottom:178.847733pt;} .y8d7{bottom:178.883200pt;} .y416{bottom:178.949467pt;} .y2d2{bottom:178.971733pt;} .y3fc{bottom:178.985467pt;} .y4dd{bottom:179.026400pt;} .ye1a{bottom:179.062267pt;} .y2c{bottom:180.158692pt;} .ye82{bottom:180.671333pt;} .ybe5{bottom:181.228933pt;} .yed6{bottom:182.924667pt;} .yab6{bottom:183.836933pt;} .yab0{bottom:183.849600pt;} .yc75{bottom:184.745333pt;} .ye61{bottom:184.952933pt;} .yd5f{bottom:185.509286pt;} .ye9c{bottom:185.634667pt;} .yc4a{bottom:185.690267pt;} .yeb9{bottom:186.322533pt;} .ye3d{bottom:186.345200pt;} .yb3f{bottom:186.710933pt;} .y68e{bottom:187.767867pt;} .y66a{bottom:187.930267pt;} .y646{bottom:187.984000pt;} .y7b2{bottom:188.091867pt;} .y78d{bottom:188.101600pt;} .y6b3{bottom:188.107600pt;} .y6d7{bottom:188.175600pt;} .y6fb{bottom:188.243600pt;} .y61c{bottom:191.474267pt;} .y5f9{bottom:191.558267pt;} .y5d6{bottom:191.642267pt;} .y749{bottom:191.761867pt;} .y76c{bottom:191.766533pt;} .y7d3{bottom:191.775867pt;} .y720{bottom:191.778267pt;} .y7f6{bottom:191.858000pt;} .yc0e{bottom:192.149600pt;} .yc61{bottom:192.670373pt;} .y474{bottom:193.021333pt;} .y415{bottom:193.925467pt;} .y3fb{bottom:193.961467pt;} .y4dc{bottom:193.966400pt;} .ye14{bottom:194.302267pt;} .yc5{bottom:194.523333pt;} .y178{bottom:194.530533pt;} .y231{bottom:194.531733pt;} .y9c{bottom:194.552133pt;} .y103{bottom:194.562933pt;} .y96d{bottom:194.564267pt;} .y23d{bottom:194.579733pt;} .y976{bottom:194.600267pt;} .y1a3{bottom:194.603600pt;} .y1ed{bottom:194.603733pt;} .y13f{bottom:194.606133pt;} .y274{bottom:194.607733pt;} .y3a3{bottom:194.623733pt;} .y97f{bottom:194.636267pt;} .y24f{bottom:194.651733pt;} .y73{bottom:194.688933pt;} .y1c1{bottom:194.723600pt;} .y20a{bottom:194.723733pt;} .y293{bottom:194.727733pt;} .y37b{bottom:194.735733pt;} .y228{bottom:194.843733pt;} .y2d1{bottom:194.967733pt;} .yc48{bottom:194.994267pt;} .ye19{bottom:195.062267pt;} .ye81{bottom:196.671333pt;} .yc57{bottom:197.135467pt;} .y3dd{bottom:197.256800pt;} .y2b{bottom:198.384142pt;} .yab5{bottom:198.504933pt;} .yaaf{bottom:198.517600pt;} .yed5{bottom:198.924667pt;} .ye60{bottom:200.952933pt;} .yd5e{bottom:201.144598pt;} .yb3e{bottom:201.374933pt;} .ye9b{bottom:201.634667pt;} .y68d{bottom:202.082267pt;} .y669{bottom:202.244667pt;} .y645{bottom:202.298400pt;} .yeb8{bottom:202.322533pt;} .ye3c{bottom:202.345200pt;} .y7b1{bottom:202.405867pt;} .y78c{bottom:202.415600pt;} .y6b2{bottom:202.421600pt;} .y6d6{bottom:202.489600pt;} .y6fa{bottom:202.557600pt;} .ya21{bottom:205.177867pt;} .y61b{bottom:206.198267pt;} .yc77{bottom:206.268000pt;} .y5f8{bottom:206.282267pt;} .y5d5{bottom:206.366267pt;} .y748{bottom:206.489467pt;} .y747{bottom:206.491867pt;} .y7d2{bottom:206.501200pt;} .y71f{bottom:206.503600pt;} .y814{bottom:206.517733pt;} .y7f5{bottom:206.583333pt;} .y473{bottom:207.901333pt;} .y414{bottom:208.901467pt;} .y4db{bottom:208.906400pt;} .y3fa{bottom:208.937467pt;} .ye13{bottom:210.302267pt;} .y8d2{bottom:210.347733pt;} .yc4{bottom:210.519733pt;} .y177{bottom:210.526933pt;} .y230{bottom:210.527733pt;} .y9b{bottom:210.548533pt;} .y102{bottom:210.559333pt;} .y23c{bottom:210.575733pt;} .y1a2{bottom:210.599600pt;} .y1ec{bottom:210.599733pt;} .y13e{bottom:210.602533pt;} .y273{bottom:210.603733pt;} .y3a2{bottom:210.619733pt;} .y24e{bottom:210.647733pt;} .y72{bottom:210.685333pt;} .y1c0{bottom:210.719600pt;} .y209{bottom:210.719733pt;} .y292{bottom:210.723733pt;} .y37a{bottom:210.731733pt;} .y227{bottom:210.839733pt;} .y2d0{bottom:210.963733pt;} .ye18{bottom:211.062267pt;} .yfc8{bottom:211.698800pt;} .ye80{bottom:212.671333pt;} .yaba{bottom:213.160267pt;} .yab4{bottom:213.172933pt;} .yaae{bottom:213.185600pt;} .yc60{bottom:214.045413pt;} .ya29{bottom:214.676267pt;} .yed4{bottom:214.924667pt;} .y68c{bottom:216.396667pt;} .y668{bottom:216.559067pt;} .y2a{bottom:216.609592pt;} .y644{bottom:216.612800pt;} .y7b0{bottom:216.719867pt;} .y78b{bottom:216.729600pt;} .y6b1{bottom:216.735600pt;} .yd5d{bottom:216.779910pt;} .y6d5{bottom:216.803600pt;} .y6f9{bottom:216.871600pt;} .ye5f{bottom:216.952933pt;} .ye9a{bottom:217.634667pt;} .yeb7{bottom:218.322533pt;} .ye3b{bottom:218.345200pt;} .yd90{bottom:218.522661pt;} .y61a{bottom:220.922267pt;} .y5f7{bottom:221.006267pt;} .y5d4{bottom:221.090267pt;} .y746{bottom:221.217200pt;} .y7d1{bottom:221.226533pt;} .y71e{bottom:221.228933pt;} .y813{bottom:221.243067pt;} .y7f4{bottom:221.308667pt;} .y472{bottom:222.781333pt;} .y4da{bottom:223.846400pt;} .y413{bottom:223.877467pt;} .y3f9{bottom:223.913467pt;} .ye12{bottom:226.302267pt;} .yfc7{bottom:226.362800pt;} .yc3{bottom:226.519733pt;} .y176{bottom:226.523333pt;} .y22f{bottom:226.523733pt;} .y9a{bottom:226.544933pt;} .y101{bottom:226.555733pt;} .y23b{bottom:226.571733pt;} .y1a1{bottom:226.595600pt;} .y1eb{bottom:226.595733pt;} .y13d{bottom:226.598933pt;} .y272{bottom:226.599733pt;} .y3a1{bottom:226.615733pt;} .y24d{bottom:226.643733pt;} .y71{bottom:226.681733pt;} .yc2{bottom:226.684133pt;} .y1bf{bottom:226.715600pt;} .y208{bottom:226.715733pt;} .y291{bottom:226.719733pt;} .y379{bottom:226.727733pt;} .y226{bottom:226.835733pt;} .y2cf{bottom:226.959733pt;} .ye17{bottom:227.062267pt;} .yc70{bottom:227.483307pt;} .yc2c{bottom:227.631040pt;} .yab9{bottom:227.828267pt;} .yab3{bottom:227.840933pt;} .yaad{bottom:227.853600pt;} .ye7f{bottom:228.671333pt;} .y68b{bottom:230.711067pt;} .y667{bottom:230.873467pt;} .yed3{bottom:230.924667pt;} .y643{bottom:230.927200pt;} .y7af{bottom:231.033867pt;} .y78a{bottom:231.043600pt;} .y6b0{bottom:231.049600pt;} .y6d4{bottom:231.117600pt;} .y6f8{bottom:231.185600pt;} .yf3e{bottom:232.272267pt;} .yd5c{bottom:232.415222pt;} .ye5e{bottom:232.952933pt;} .ye99{bottom:233.634667pt;} .yeb6{bottom:234.322533pt;} .y29{bottom:234.835042pt;} .yc5f{bottom:235.420453pt;} .yd8f{bottom:235.482044pt;} .y619{bottom:235.646267pt;} .y5f6{bottom:235.730267pt;} .y5d3{bottom:235.814267pt;} .y745{bottom:235.944800pt;} .y7d0{bottom:235.951867pt;} .y71d{bottom:235.954267pt;} .y744{bottom:235.961333pt;} .y812{bottom:235.968400pt;} .y76b{bottom:235.980133pt;} .y7f3{bottom:236.034000pt;} .yc52{bottom:236.217787pt;} .yc0d{bottom:237.365013pt;} .y471{bottom:237.661333pt;} .y4d9{bottom:238.786400pt;} .y412{bottom:238.853467pt;} .y3f8{bottom:238.889467pt;} .yfc6{bottom:241.026800pt;} .y534{bottom:241.093733pt;} .yab8{bottom:242.496267pt;} .yab2{bottom:242.508933pt;} .y175{bottom:242.519733pt;} .yaac{bottom:242.521600pt;} .y99{bottom:242.541333pt;} .y100{bottom:242.552133pt;} .y23a{bottom:242.567733pt;} .y1a0{bottom:242.591600pt;} .y1ea{bottom:242.591733pt;} .y13c{bottom:242.595333pt;} .y271{bottom:242.595733pt;} .y3a0{bottom:242.611733pt;} .y5a1{bottom:242.627600pt;} .y24c{bottom:242.639733pt;} .y70{bottom:242.678133pt;} .yc1{bottom:242.680533pt;} .y1be{bottom:242.711600pt;} .y207{bottom:242.711733pt;} .y290{bottom:242.715733pt;} .y378{bottom:242.723733pt;} .y225{bottom:242.831733pt;} .y2ce{bottom:242.955733pt;} .yf3d{bottom:243.472267pt;} .ye7e{bottom:244.671333pt;} .y68a{bottom:245.025467pt;} .y666{bottom:245.187867pt;} .y642{bottom:245.241600pt;} .y7ae{bottom:245.347867pt;} .y789{bottom:245.357600pt;} .y6af{bottom:245.363600pt;} .y6d3{bottom:245.431600pt;} .y6f7{bottom:245.499600pt;} .yed2{bottom:246.924667pt;} .yd5b{bottom:248.050534pt;} .yc6f{bottom:248.858347pt;} .ye5d{bottom:248.952933pt;} .yc2b{bottom:249.006080pt;} .ye98{bottom:249.634667pt;} .yc46{bottom:249.803280pt;} .ycdc{bottom:250.182800pt;} .yeb5{bottom:250.322533pt;} .ye3a{bottom:250.345200pt;} .y618{bottom:250.370267pt;} .y5f5{bottom:250.454267pt;} .y5d1{bottom:250.538267pt;} .y7cf{bottom:250.677200pt;} .y71c{bottom:250.679600pt;} .y743{bottom:250.686667pt;} .y811{bottom:250.693733pt;} .y76a{bottom:250.705467pt;} .y7f2{bottom:250.759333pt;} .yf4a{bottom:251.050133pt;} .y5d2{bottom:251.630267pt;} .yd8e{bottom:252.441428pt;} .y470{bottom:252.541333pt;} .y28{bottom:253.060492pt;} .y411{bottom:253.829467pt;} .y3f7{bottom:253.865467pt;} .yb22{bottom:254.502418pt;} .ydd8{bottom:255.170133pt;} .yfc5{bottom:255.690800pt;} .yc06{bottom:255.917333pt;} .yc5e{bottom:256.795493pt;} .yab7{bottom:257.164267pt;} .yab1{bottom:257.176933pt;} .yaab{bottom:257.189600pt;} .yc51{bottom:257.592827pt;} .ye11{bottom:258.302267pt;} .y174{bottom:258.519733pt;} .y98{bottom:258.537733pt;} .yff{bottom:258.548533pt;} .y19f{bottom:258.587600pt;} .y1e9{bottom:258.587733pt;} .y13b{bottom:258.591733pt;} .y39f{bottom:258.607733pt;} .y5a0{bottom:258.623600pt;} .y24b{bottom:258.635733pt;} .y6f{bottom:258.674533pt;} .yc0{bottom:258.676933pt;} .y3dc{bottom:258.680800pt;} .y1bd{bottom:258.707600pt;} .y206{bottom:258.707733pt;} .y28f{bottom:258.711733pt;} .y377{bottom:258.719733pt;} .yc0c{bottom:258.740053pt;} .y224{bottom:258.827733pt;} .y2cd{bottom:258.951733pt;} .y689{bottom:259.339867pt;} .y665{bottom:259.502267pt;} .y640{bottom:259.547067pt;} .y641{bottom:259.551467pt;} .y7ad{bottom:259.661867pt;} .y788{bottom:259.671600pt;} .y6ae{bottom:259.677600pt;} .y6d2{bottom:259.745600pt;} .y6f6{bottom:259.813600pt;} .ye7d{bottom:260.671333pt;} .yd5a{bottom:263.685846pt;} .ye5c{bottom:264.952933pt;} .y617{bottom:265.094267pt;} .y5f4{bottom:265.178267pt;} .y5d0{bottom:265.262267pt;} .y7ce{bottom:265.402533pt;} .y71b{bottom:265.404933pt;} .y742{bottom:265.412000pt;} .y810{bottom:265.419067pt;} .yf15{bottom:265.422533pt;} .y769{bottom:265.430800pt;} .y7f1{bottom:265.484667pt;} .ye97{bottom:265.634667pt;} .yeb4{bottom:266.322533pt;} .ye39{bottom:266.345200pt;} .y46f{bottom:267.421333pt;} .y4d8{bottom:268.678400pt;} .y410{bottom:268.805467pt;} .y3f6{bottom:268.841467pt;} .yd8d{bottom:269.400811pt;} .yc6e{bottom:270.233387pt;} .yfc4{bottom:270.354800pt;} .yc2a{bottom:270.381120pt;} .yc45{bottom:271.178320pt;} .yc22{bottom:271.190267pt;} .y688{bottom:273.654267pt;} .y664{bottom:273.816667pt;} .y3e{bottom:273.852587pt;} .y63f{bottom:273.861467pt;} .y7ac{bottom:273.975867pt;} .y787{bottom:273.985600pt;} .y6ad{bottom:273.991600pt;} .yd24{bottom:274.042543pt;} .y6d1{bottom:274.059600pt;} .y6f5{bottom:274.127600pt;} .ye10{bottom:274.302267pt;} .y97{bottom:274.534133pt;} .yfe{bottom:274.544933pt;} .y19e{bottom:274.583600pt;} .y1e8{bottom:274.583733pt;} .y13a{bottom:274.588133pt;} .y39e{bottom:274.603733pt;} .y59f{bottom:274.619600pt;} .y24a{bottom:274.631733pt;} .y6e{bottom:274.670933pt;} .ybf{bottom:274.673333pt;} .y1bc{bottom:274.703600pt;} .y205{bottom:274.703733pt;} .y376{bottom:274.715733pt;} .y223{bottom:274.823733pt;} .y2cc{bottom:274.947733pt;} .y25b{bottom:275.206667pt;} .yf14{bottom:276.622533pt;} .yf16{bottom:276.837200pt;} .y1b{bottom:277.682483pt;} .yc5d{bottom:278.170533pt;} .yed1{bottom:278.924667pt;} .yc50{bottom:278.967867pt;} .yd59{bottom:279.321158pt;} .y616{bottom:279.818267pt;} .y34b{bottom:279.834000pt;} .y5f3{bottom:279.902267pt;} .y5cf{bottom:279.986267pt;} .ycde{bottom:280.026400pt;} .yc0b{bottom:280.115093pt;} .y7cd{bottom:280.127867pt;} .y71a{bottom:280.130267pt;} .y741{bottom:280.137333pt;} .y80f{bottom:280.144400pt;} .y768{bottom:280.156133pt;} .y7f0{bottom:280.210000pt;} .ydd7{bottom:281.836800pt;} .y46e{bottom:282.301333pt;} .y4d7{bottom:283.618400pt;} .y40f{bottom:283.781467pt;} .y3f5{bottom:283.817467pt;} .yfc3{bottom:285.018800pt;} .yd8c{bottom:286.360195pt;} .yd23{bottom:287.375467pt;} .y687{bottom:287.968667pt;} .y663{bottom:288.131067pt;} .y63d{bottom:288.148933pt;} .y63e{bottom:288.171333pt;} .yec6{bottom:288.289067pt;} .y7ab{bottom:288.289867pt;} .y786{bottom:288.299600pt;} .y6ac{bottom:288.305600pt;} .y6d0{bottom:288.373600pt;} .y6f4{bottom:288.441600pt;} .ye72{bottom:288.856000pt;} .y96{bottom:290.530533pt;} .yfd{bottom:290.541333pt;} .y19d{bottom:290.579600pt;} .y1e7{bottom:290.579733pt;} .y139{bottom:290.584533pt;} .y39d{bottom:290.599733pt;} .y59e{bottom:290.615600pt;} .y249{bottom:290.627733pt;} .y6d{bottom:290.667333pt;} .ybe{bottom:290.669733pt;} .y1bb{bottom:290.699600pt;} .y204{bottom:290.699733pt;} .y375{bottom:290.711733pt;} .y222{bottom:290.819733pt;} .yb86{bottom:290.933467pt;} .y2cb{bottom:290.943733pt;} .yc6d{bottom:291.608427pt;} .yf2f{bottom:291.733467pt;} .yc29{bottom:291.756160pt;} .yc44{bottom:292.553360pt;} .ye8c{bottom:293.481600pt;} .ya35{bottom:293.567259pt;} .ye30{bottom:294.190000pt;} .y615{bottom:294.542267pt;} .y5f2{bottom:294.626267pt;} .y5ce{bottom:294.710267pt;} .y719{bottom:294.855600pt;} .y740{bottom:294.862667pt;} .y80e{bottom:294.869733pt;} .y767{bottom:294.881467pt;} .y7cc{bottom:294.898000pt;} .yed0{bottom:294.924667pt;} .y7ef{bottom:294.935333pt;} .yd58{bottom:294.956470pt;} .ye48{bottom:295.171333pt;} .y25a{bottom:295.209333pt;} .y46d{bottom:297.181333pt;} .yf27{bottom:297.216400pt;} .y8cc{bottom:298.488400pt;} .y4d6{bottom:298.558400pt;} .y40e{bottom:298.757467pt;} .y3f4{bottom:298.793467pt;} .y9b1{bottom:299.019312pt;} .yf77{bottom:299.478800pt;} .yc5c{bottom:299.545573pt;} .yf96{bottom:299.562800pt;} .yfc2{bottom:299.682800pt;} .yc4f{bottom:300.342907pt;} .yc02{bottom:301.490133pt;} .y686{bottom:302.283067pt;} .ydd5{bottom:302.414133pt;} .y662{bottom:302.445467pt;} .y63c{bottom:302.463333pt;} .y7aa{bottom:302.603867pt;} .y785{bottom:302.613600pt;} .y6ab{bottom:302.619600pt;} .y6cf{bottom:302.687600pt;} .y6f3{bottom:302.755600pt;} .yf2e{bottom:302.933467pt;} .yd8b{bottom:303.319578pt;} .y9d2{bottom:304.800674pt;} .y95{bottom:306.526933pt;} .yfc{bottom:306.537733pt;} .y19c{bottom:306.575600pt;} .y1e6{bottom:306.575733pt;} .y138{bottom:306.580933pt;} .y39c{bottom:306.595733pt;} .y59d{bottom:306.611600pt;} .y248{bottom:306.623733pt;} .ybd3{bottom:306.633333pt;} .y6c{bottom:306.663733pt;} .ybd{bottom:306.666133pt;} .y1ba{bottom:306.695600pt;} .y203{bottom:306.695733pt;} .y374{bottom:306.707733pt;} .y221{bottom:306.815733pt;} .y2ca{bottom:306.939733pt;} .yf26{bottom:308.416400pt;} .y614{bottom:309.266267pt;} .y5f1{bottom:309.350267pt;} .y5cd{bottom:309.434267pt;} .y718{bottom:309.583333pt;} .y73f{bottom:309.588000pt;} .y80d{bottom:309.595067pt;} .y766{bottom:309.606800pt;} .y717{bottom:309.618667pt;} .y7cb{bottom:309.623333pt;} .y2dd{bottom:309.652133pt;} .y7ee{bottom:309.660667pt;} .y46c{bottom:312.061333pt;} .yf38{bottom:312.320000pt;} .yc6c{bottom:312.983467pt;} .yc28{bottom:313.131200pt;} .y4d5{bottom:313.498400pt;} .y40d{bottom:313.733467pt;} .y3f3{bottom:313.769467pt;} .ydd6{bottom:313.834133pt;} .yc1d{bottom:313.928400pt;} .yf76{bottom:314.142800pt;} .yf95{bottom:314.226800pt;} .yfc1{bottom:314.346800pt;} .yec5{bottom:314.955733pt;} .y259{bottom:315.212000pt;} .ye71{bottom:315.522667pt;} .ya34{bottom:316.235202pt;} .yd34{bottom:316.491777pt;} .y685{bottom:316.597467pt;} .y661{bottom:316.759867pt;} .y63b{bottom:316.777733pt;} .y7a9{bottom:316.917867pt;} .y784{bottom:316.927600pt;} .y6aa{bottom:316.933600pt;} .y6ce{bottom:317.001600pt;} .ya2a{bottom:317.002667pt;} .y6f2{bottom:317.069600pt;} .yedc{bottom:319.053200pt;} .ye8b{bottom:320.148267pt;} .yd8a{bottom:320.278962pt;} .ye2f{bottom:320.856667pt;} .yc5b{bottom:320.920613pt;} .y9b0{bottom:321.687255pt;} .yc4e{bottom:321.717947pt;} .ye47{bottom:321.838000pt;} .y94{bottom:322.523333pt;} .yfb{bottom:322.534133pt;} .y3d{bottom:322.549720pt;} .y19b{bottom:322.571600pt;} .y1e5{bottom:322.571733pt;} .y137{bottom:322.577333pt;} .y39b{bottom:322.591733pt;} .y59c{bottom:322.607600pt;} .y247{bottom:322.619733pt;} .y6b{bottom:322.660133pt;} .ybc{bottom:322.662533pt;} .y304{bottom:322.667733pt;} .y1b9{bottom:322.691600pt;} .y202{bottom:322.691733pt;} .y373{bottom:322.703733pt;} .y220{bottom:322.811733pt;} .yc01{bottom:322.865173pt;} .y2c9{bottom:322.935733pt;} .ycdd{bottom:323.290667pt;} .y613{bottom:323.990267pt;} .y5f0{bottom:324.074267pt;} .y5cc{bottom:324.158267pt;} .y73e{bottom:324.313333pt;} .y80c{bottom:324.320400pt;} .y765{bottom:324.332133pt;} .y716{bottom:324.344000pt;} .y7ca{bottom:324.348667pt;} .y7ed{bottom:324.386000pt;} .y1a{bottom:326.372619pt;} .y46b{bottom:326.941333pt;} .y4d4{bottom:328.438400pt;} .yf0b{bottom:328.482933pt;} .yd28{bottom:328.693609pt;} .y3f2{bottom:328.745467pt;} .y9d1{bottom:328.802025pt;} .yf75{bottom:328.806800pt;} .yf94{bottom:328.890800pt;} .yfc0{bottom:329.010800pt;} .ydd4{bottom:329.080800pt;} .y8d0{bottom:329.462800pt;} .y533{bottom:330.025733pt;} .y684{bottom:330.911867pt;} .y660{bottom:331.074267pt;} .y63a{bottom:331.092133pt;} .y7a8{bottom:331.231867pt;} .y783{bottom:331.241600pt;} .y6a9{bottom:331.247600pt;} .y6cd{bottom:331.315600pt;} .y6f1{bottom:331.383600pt;} .y2dc{bottom:332.098267pt;} .yce3{bottom:333.867467pt;} .yc6b{bottom:334.358507pt;} .yc27{bottom:334.506240pt;} .y8f1{bottom:334.762920pt;} .yf0a{bottom:334.920667pt;} .y258{bottom:335.214667pt;} .yc1c{bottom:335.303440pt;} .y830{bottom:335.494325pt;} .yf3f{bottom:337.094933pt;} .yd89{bottom:337.238345pt;} .yda1{bottom:337.755200pt;} .yb4b{bottom:337.763968pt;} .y93{bottom:338.519733pt;} .yfa{bottom:338.530533pt;} .y19a{bottom:338.567600pt;} .y1e4{bottom:338.567733pt;} .y136{bottom:338.573733pt;} .y39a{bottom:338.587733pt;} .y59b{bottom:338.603600pt;} .y246{bottom:338.615733pt;} .y6a{bottom:338.656533pt;} .ybb{bottom:338.658933pt;} .y303{bottom:338.663733pt;} .y1b8{bottom:338.687600pt;} .y201{bottom:338.687733pt;} .y372{bottom:338.699733pt;} .yda0{bottom:338.700133pt;} .y612{bottom:338.714267pt;} .y5ef{bottom:338.798267pt;} .y21f{bottom:338.807733pt;} .y5cb{bottom:338.882267pt;} .y2c8{bottom:338.931733pt;} .y73d{bottom:339.038667pt;} .y80b{bottom:339.045733pt;} .y764{bottom:339.057467pt;} .y715{bottom:339.069333pt;} .y7c9{bottom:339.074000pt;} .y7ec{bottom:339.111333pt;} .y50e{bottom:339.943867pt;} .y52d{bottom:339.991867pt;} .y4fa{bottom:340.051867pt;} .yf25{bottom:340.205733pt;} .y46a{bottom:341.821333pt;} .y532{bottom:342.025733pt;} .yd27{bottom:342.026533pt;} .yc5a{bottom:342.295653pt;} .y42f{bottom:342.737467pt;} .yc4d{bottom:343.092987pt;} .y4d3{bottom:343.378400pt;} .yf74{bottom:343.470800pt;} .yf93{bottom:343.554800pt;} .yfbf{bottom:343.674800pt;} .y40c{bottom:343.685467pt;} .y3f1{bottom:343.721467pt;} .y885{bottom:344.173294pt;} .yc00{bottom:344.240213pt;} .y683{bottom:345.226267pt;} .y65f{bottom:345.388667pt;} .y639{bottom:345.406533pt;} .y7a7{bottom:345.545867pt;} .y782{bottom:345.555600pt;} .y6a8{bottom:345.561600pt;} .y6cc{bottom:345.629600pt;} .y6f0{bottom:345.697600pt;} .yedb{bottom:345.719867pt;} .y5ba{bottom:346.570667pt;} .yec4{bottom:346.963200pt;} .ye70{bottom:347.529200pt;} .yad7{bottom:350.084277pt;} .yb2b{bottom:350.094800pt;} .yc97{bottom:350.478863pt;} .y2db{bottom:350.764933pt;} .yf24{bottom:351.405733pt;} .yf09{bottom:352.036667pt;} .y940{bottom:352.039733pt;} .ye8a{bottom:352.153467pt;} .yda2{bottom:352.616800pt;} .ye2e{bottom:352.857467pt;} .y611{bottom:353.438267pt;} .y5ee{bottom:353.522267pt;} .y5ca{bottom:353.606267pt;} .y73c{bottom:353.766400pt;} .y73b{bottom:353.768667pt;} .y80a{bottom:353.771067pt;} .y763{bottom:353.782800pt;} .y714{bottom:353.794667pt;} .y7c8{bottom:353.799333pt;} .y7eb{bottom:353.836667pt;} .ye46{bottom:353.842667pt;} .yb8e{bottom:353.958400pt;} .y92{bottom:354.519733pt;} .yf9{bottom:354.526933pt;} .y173{bottom:354.530533pt;} .y199{bottom:354.563600pt;} .y1e3{bottom:354.563733pt;} .y135{bottom:354.570133pt;} .y399{bottom:354.583733pt;} .y59a{bottom:354.599600pt;} .y69{bottom:354.652933pt;} .yba{bottom:354.655333pt;} .y302{bottom:354.659733pt;} .y1b7{bottom:354.683600pt;} .y200{bottom:354.683733pt;} .y52c{bottom:354.691867pt;} .y371{bottom:354.695733pt;} .ybd2{bottom:354.728600pt;} .y21e{bottom:354.803733pt;} .y2c7{bottom:354.927733pt;} .y349{bottom:354.983733pt;} .y50d{bottom:355.351867pt;} .y4f9{bottom:355.459867pt;} .yc6a{bottom:355.733547pt;} .yc26{bottom:355.881280pt;} .yc1b{bottom:356.678480pt;} .y469{bottom:356.701333pt;} .y42e{bottom:357.401467pt;} .yf73{bottom:358.134800pt;} .yf92{bottom:358.218800pt;} .y4d2{bottom:358.318400pt;} .yfbe{bottom:358.338800pt;} .y40b{bottom:358.661467pt;} .y3f0{bottom:358.697467pt;} .y8f0{bottom:358.764271pt;} .y82f{bottom:359.495676pt;} .y682{bottom:359.540667pt;} .y65e{bottom:359.703067pt;} .y638{bottom:359.720933pt;} .y7a6{bottom:359.859867pt;} .y781{bottom:359.869600pt;} .y6a7{bottom:359.875600pt;} .y6cb{bottom:359.943600pt;} .y6ef{bottom:360.011600pt;} .yce7{bottom:360.591209pt;} .yd70{bottom:360.743389pt;} .ydd3{bottom:361.078667pt;} .yd57{bottom:362.357342pt;} .yc87{bottom:362.769467pt;} .yc59{bottom:363.670693pt;} .yf2d{bottom:364.393467pt;} .yc4c{bottom:364.468027pt;} .yc89{bottom:364.621970pt;} .yc0a{bottom:365.615253pt;} .y3c{bottom:367.451547pt;} .y610{bottom:368.162267pt;} .y5ed{bottom:368.246267pt;} .y5c9{bottom:368.330267pt;} .y73a{bottom:368.494000pt;} .y809{bottom:368.496400pt;} .y762{bottom:368.508133pt;} .y713{bottom:368.520000pt;} .y7c7{bottom:368.524667pt;} .y7ea{bottom:368.562000pt;} .y3db{bottom:368.901467pt;} .yf08{bottom:369.152667pt;} .y52b{bottom:369.403867pt;} .y2da{bottom:369.431600pt;} .y884{bottom:369.508054pt;} .ycc7{bottom:369.538533pt;} .yf8{bottom:370.523333pt;} .y172{bottom:370.526933pt;} .y198{bottom:370.559600pt;} .y1e2{bottom:370.559733pt;} .y134{bottom:370.566533pt;} .y398{bottom:370.579733pt;} .y599{bottom:370.595600pt;} .y68{bottom:370.649333pt;} .yb9{bottom:370.651733pt;} .y301{bottom:370.655733pt;} .y1b6{bottom:370.679600pt;} .y1ff{bottom:370.679733pt;} .y370{bottom:370.691733pt;} .y50c{bottom:370.759867pt;} .y21d{bottom:370.799733pt;} .y4f8{bottom:370.867867pt;} .y2c6{bottom:370.923733pt;} .y348{bottom:370.979733pt;} .y18{bottom:371.298267pt;} .yce2{bottom:371.536800pt;} .y468{bottom:371.581333pt;} .yb83{bottom:371.606400pt;} .y42d{bottom:372.065467pt;} .yf72{bottom:372.798800pt;} .yf91{bottom:372.882800pt;} .yfbd{bottom:373.002800pt;} .y19{bottom:373.180511pt;} .y4d1{bottom:373.258400pt;} .y40a{bottom:373.637467pt;} .y3ef{bottom:373.673467pt;} .y681{bottom:373.855067pt;} .y65d{bottom:374.017467pt;} .y637{bottom:374.030800pt;} .y7a5{bottom:374.173867pt;} .y780{bottom:374.183600pt;} .y6a6{bottom:374.189600pt;} .y6ca{bottom:374.257600pt;} .y6ee{bottom:374.325600pt;} .yf2c{bottom:375.593467pt;} .y93f{bottom:376.039733pt;} .y93e{bottom:376.047332pt;} .yb2a{bottom:376.270533pt;} .yb29{bottom:376.275831pt;} .ydac{bottom:376.808933pt;} .yc69{bottom:377.108587pt;} .yc25{bottom:377.256320pt;} .yeda{bottom:377.728133pt;} .yd56{bottom:377.992654pt;} .yc43{bottom:378.053520pt;} .yda3{bottom:378.246133pt;} .yb8d{bottom:380.134133pt;} .yb8c{bottom:380.140729pt;} .ya83{bottom:382.562533pt;} .y60f{bottom:382.886267pt;} .y5ec{bottom:382.970267pt;} .y5c8{bottom:383.054267pt;} .y739{bottom:383.221733pt;} .y761{bottom:383.233467pt;} .y712{bottom:383.245333pt;} .y738{bottom:383.247600pt;} .y7c6{bottom:383.250000pt;} .y7e9{bottom:383.287333pt;} .yd2b{bottom:383.622133pt;} .ybd1{bottom:384.053600pt;} .y52a{bottom:384.103867pt;} .yce6{bottom:384.693071pt;} .yc58{bottom:385.045733pt;} .y25c{bottom:385.407067pt;} .yc4b{bottom:385.843067pt;} .y50b{bottom:386.167867pt;} .yf13{bottom:386.186533pt;} .yf07{bottom:386.268667pt;} .y4f7{bottom:386.275867pt;} .y467{bottom:386.461333pt;} .y91{bottom:386.519733pt;} .y171{bottom:386.523333pt;} .y197{bottom:386.555600pt;} .y1e1{bottom:386.555733pt;} .y133{bottom:386.562933pt;} .y397{bottom:386.575733pt;} .y598{bottom:386.591600pt;} .y54f{bottom:386.623733pt;} .y67{bottom:386.645733pt;} .yb8{bottom:386.648133pt;} .y300{bottom:386.651733pt;} .y1b5{bottom:386.675600pt;} .y1fe{bottom:386.675733pt;} .y36f{bottom:386.687733pt;} .y3ba{bottom:386.707733pt;} .y42c{bottom:386.729467pt;} .y56a{bottom:386.731733pt;} .y57a{bottom:386.791733pt;} .y21c{bottom:386.795733pt;} .y2c5{bottom:386.919733pt;} .y347{bottom:386.975733pt;} .ybff{bottom:386.990293pt;} .yf71{bottom:387.462800pt;} .yf90{bottom:387.546800pt;} .yfbc{bottom:387.666800pt;} .yb5b{bottom:387.773733pt;} .yf37{bottom:388.004000pt;} .y680{bottom:388.169467pt;} .y4d0{bottom:388.198400pt;} .y65c{bottom:388.331867pt;} .y635{bottom:388.336267pt;} .y636{bottom:388.340800pt;} .y7a4{bottom:388.487867pt;} .y77f{bottom:388.497600pt;} .y6a5{bottom:388.503600pt;} .y6c9{bottom:388.571600pt;} .y409{bottom:388.613467pt;} .y6ed{bottom:388.639600pt;} .y3ee{bottom:388.649467pt;} .ya56{bottom:388.773467pt;} .ya5f{bottom:388.809467pt;} .yccf{bottom:391.294933pt;} .yf11{bottom:392.626533pt;} .yd55{bottom:393.627966pt;} .yf12{bottom:397.386533pt;} .y60e{bottom:397.610267pt;} .y5eb{bottom:397.694267pt;} .y5c7{bottom:397.778267pt;} .y808{bottom:397.949467pt;} .y807{bottom:397.956533pt;} .y760{bottom:397.958800pt;} .y711{bottom:397.970667pt;} .y737{bottom:397.972933pt;} .y7c5{bottom:397.975333pt;} .y7e8{bottom:398.012667pt;} .ydf7{bottom:398.468667pt;} .yc68{bottom:398.483627pt;} .y853{bottom:398.544667pt;} .y85e{bottom:398.568667pt;} .yc24{bottom:398.631360pt;} .yce4{bottom:398.749733pt;} .y529{bottom:398.803867pt;} .yf36{bottom:399.204000pt;} .yc1a{bottom:399.428560pt;} .ydb5{bottom:400.822933pt;} .y466{bottom:401.341333pt;} .y42b{bottom:401.393467pt;} .y50a{bottom:401.575867pt;} .y4f6{bottom:401.683867pt;} .yd88{bottom:401.765700pt;} .yf70{bottom:402.126800pt;} .yf8f{bottom:402.210800pt;} .yfbb{bottom:402.330800pt;} .y98f{bottom:402.412533pt;} .y997{bottom:402.417867pt;} .yb5a{bottom:402.437733pt;} .y67f{bottom:402.483867pt;} .y90{bottom:402.519733pt;} .y196{bottom:402.551600pt;} .y1e0{bottom:402.551733pt;} .y132{bottom:402.559333pt;} .y396{bottom:402.571733pt;} .y8f{bottom:402.580933pt;} .y597{bottom:402.587600pt;} .y54e{bottom:402.619733pt;} .y66{bottom:402.642133pt;} .yb7{bottom:402.644533pt;} .y65b{bottom:402.646267pt;} .y2ff{bottom:402.647733pt;} .y634{bottom:402.650667pt;} .yf7{bottom:402.663733pt;} .y1b4{bottom:402.671600pt;} .y1fd{bottom:402.671733pt;} .y36e{bottom:402.683733pt;} .y3b9{bottom:402.703733pt;} .y569{bottom:402.727733pt;} .y579{bottom:402.787733pt;} .y21b{bottom:402.791733pt;} .y7a3{bottom:402.801867pt;} .y77e{bottom:402.811600pt;} .y6a4{bottom:402.817600pt;} .y6c8{bottom:402.885600pt;} .y2c4{bottom:402.915733pt;} .y6ec{bottom:402.953600pt;} .y346{bottom:402.971733pt;} .y49a{bottom:403.114400pt;} .y4b5{bottom:403.126400pt;} .y4cf{bottom:403.138400pt;} .yccb{bottom:403.179467pt;} .yf06{bottom:403.384667pt;} .y408{bottom:403.589467pt;} .y3ed{bottom:403.625467pt;} .yf49{bottom:403.790133pt;} .yf10{bottom:403.826533pt;} .ya55{bottom:404.769467pt;} .ya5e{bottom:404.805467pt;} .ya81{bottom:405.220131pt;} .ya82{bottom:405.229200pt;} .y910{bottom:408.000133pt;} .y918{bottom:408.024133pt;} .ybfe{bottom:408.365333pt;} .yce5{bottom:408.794933pt;} .yd54{bottom:409.263278pt;} .yb23{bottom:411.220099pt;} .y60d{bottom:412.334267pt;} .y3b{bottom:412.353373pt;} .y5ea{bottom:412.418267pt;} .y5c6{bottom:412.502267pt;} .y806{bottom:412.681867pt;} .y75f{bottom:412.684133pt;} .y710{bottom:412.696000pt;} .y736{bottom:412.698267pt;} .y7c4{bottom:412.700667pt;} .y7e7{bottom:412.738000pt;} .ydf6{bottom:413.132667pt;} .y852{bottom:413.208667pt;} .y85d{bottom:413.232667pt;} .y528{bottom:413.515867pt;} .yf48{bottom:414.990133pt;} .yba1{bottom:415.027200pt;} .yba6{bottom:415.039200pt;} .ybab{bottom:415.051200pt;} .yf3c{bottom:415.504267pt;} .y899{bottom:415.906133pt;} .y8a0{bottom:415.930133pt;} .y42a{bottom:416.057467pt;} .y465{bottom:416.221333pt;} .y17{bottom:416.223915pt;} .yf6f{bottom:416.790800pt;} .y67e{bottom:416.798267pt;} .ydb4{bottom:416.818933pt;} .yf8e{bottom:416.874800pt;} .y632{bottom:416.956133pt;} .y633{bottom:416.960667pt;} .y509{bottom:416.983867pt;} .yfba{bottom:416.994800pt;} .y98e{bottom:417.079200pt;} .y996{bottom:417.081867pt;} .y4f5{bottom:417.091867pt;} .y98d{bottom:417.092533pt;} .y99d{bottom:417.093867pt;} .yb59{bottom:417.101733pt;} .y7a2{bottom:417.115867pt;} .y77d{bottom:417.125600pt;} .y6a3{bottom:417.131600pt;} .yaf1{bottom:417.189618pt;} .y6c7{bottom:417.199600pt;} .yaec{bottom:417.202764pt;} .y6eb{bottom:417.267600pt;} .y499{bottom:418.054400pt;} .y4b4{bottom:418.066400pt;} .y4ce{bottom:418.078400pt;} .y170{bottom:418.519733pt;} .y195{bottom:418.547600pt;} .y1df{bottom:418.547733pt;} .y131{bottom:418.555733pt;} .y16f{bottom:418.562933pt;} .y407{bottom:418.565467pt;} .y395{bottom:418.567733pt;} .y8e{bottom:418.577333pt;} .y596{bottom:418.583600pt;} .y270{bottom:418.587733pt;} .y3ec{bottom:418.601467pt;} .y54d{bottom:418.615733pt;} .y65{bottom:418.638533pt;} .yb6{bottom:418.640933pt;} .y2fe{bottom:418.643733pt;} .yf6{bottom:418.660133pt;} .y1b3{bottom:418.667600pt;} .y1fc{bottom:418.667733pt;} .y36d{bottom:418.679733pt;} .y3b8{bottom:418.699733pt;} .y28e{bottom:418.707733pt;} .y568{bottom:418.723733pt;} .y578{bottom:418.783733pt;} .y21a{bottom:418.787733pt;} .y3d0{bottom:418.795733pt;} .y2c3{bottom:418.911733pt;} .y345{bottom:418.967733pt;} .ybf1{bottom:419.370533pt;} .yc67{bottom:419.858667pt;} .yc23{bottom:420.006400pt;} .y9ef{bottom:420.374533pt;} .y9f6{bottom:420.386533pt;} .y9fd{bottom:420.398533pt;} .yf05{bottom:420.494267pt;} .ya54{bottom:420.765467pt;} .yd87{bottom:420.767534pt;} .ya5d{bottom:420.801467pt;} .yc19{bottom:420.803600pt;} .ya66{bottom:420.837467pt;} .y95f{bottom:422.264267pt;} .y966{bottom:422.276267pt;} .ycd6{bottom:422.574933pt;} .y90f{bottom:422.664133pt;} .y917{bottom:422.688133pt;} .yc64{bottom:423.377200pt;} .y480{bottom:423.456000pt;} .yc55{bottom:424.174533pt;} .yda9{bottom:424.352267pt;} .yd53{bottom:424.898590pt;} .y60c{bottom:427.058267pt;} .y5e9{bottom:427.142267pt;} .y5c5{bottom:427.226267pt;} .y805{bottom:427.407200pt;} .y75e{bottom:427.409467pt;} .y70f{bottom:427.421333pt;} .y735{bottom:427.423600pt;} .y7c3{bottom:427.426000pt;} .y7e6{bottom:427.463333pt;} .y851{bottom:427.872667pt;} .ya80{bottom:427.888074pt;} .y85c{bottom:427.896667pt;} .y867{bottom:427.920667pt;} .y527{bottom:428.215867pt;} .yba0{bottom:429.691200pt;} .yba5{bottom:429.703200pt;} .ybaa{bottom:429.715200pt;} .y429{bottom:430.721467pt;} .y464{bottom:431.101333pt;} .y67d{bottom:431.112667pt;} .y65a{bottom:431.234667pt;} .y631{bottom:431.270533pt;} .y7a1{bottom:431.429867pt;} .y77c{bottom:431.439600pt;} .y6a2{bottom:431.445600pt;} .yf6e{bottom:431.454800pt;} .y6c6{bottom:431.513600pt;} .yf8d{bottom:431.538800pt;} .y6ea{bottom:431.581600pt;} .yfb9{bottom:431.658800pt;} .y995{bottom:431.745867pt;} .y98c{bottom:431.756533pt;} .y99c{bottom:431.757867pt;} .yb58{bottom:431.765733pt;} .y898{bottom:431.902133pt;} .y89f{bottom:431.926133pt;} .y8a6{bottom:431.950133pt;} .ye0f{bottom:432.088933pt;} .y508{bottom:432.391867pt;} .y4f4{bottom:432.499867pt;} .ydb3{bottom:432.814933pt;} .y498{bottom:432.994400pt;} .y4b3{bottom:433.006400pt;} .y4cd{bottom:433.018400pt;} .y406{bottom:433.541467pt;} .y3eb{bottom:433.577467pt;} .yaf5{bottom:434.082571pt;} .yaf0{bottom:434.095717pt;} .yaeb{bottom:434.108863pt;} .y194{bottom:434.543600pt;} .y1de{bottom:434.543733pt;} .y130{bottom:434.552133pt;} .y16e{bottom:434.559333pt;} .y394{bottom:434.563733pt;} .y8d{bottom:434.573733pt;} .y595{bottom:434.579600pt;} .y26f{bottom:434.583733pt;} .y54c{bottom:434.611733pt;} .y64{bottom:434.634933pt;} .yb5{bottom:434.637333pt;} .y2fd{bottom:434.639733pt;} .yf5{bottom:434.656533pt;} .y1b2{bottom:434.663600pt;} .y1fb{bottom:434.663733pt;} .y36c{bottom:434.675733pt;} .y3b7{bottom:434.695733pt;} .y28d{bottom:434.703733pt;} .y567{bottom:434.719733pt;} .y577{bottom:434.779733pt;} .y219{bottom:434.783733pt;} .ydfb{bottom:434.789733pt;} .y3cf{bottom:434.791733pt;} .y2c2{bottom:434.907733pt;} .y344{bottom:434.963733pt;} .y9ee{bottom:435.038533pt;} .y9f5{bottom:435.050533pt;} .y9fc{bottom:435.062533pt;} .ya53{bottom:436.761467pt;} .ya5c{bottom:436.797467pt;} .ya65{bottom:436.833467pt;} .y95e{bottom:436.928267pt;} .y965{bottom:436.940267pt;} .y96c{bottom:436.952267pt;} .yd26{bottom:437.186809pt;} .y90e{bottom:437.328133pt;} .y916{bottom:437.352133pt;} .y91e{bottom:437.376133pt;} .yd6f{bottom:439.123856pt;} .yd52{bottom:440.533902pt;} .y60b{bottom:441.782267pt;} .y5e8{bottom:441.866267pt;} .y5c4{bottom:441.950267pt;} .y804{bottom:442.132533pt;} .y75d{bottom:442.134800pt;} .y70e{bottom:442.146667pt;} .y734{bottom:442.148933pt;} .y7c2{bottom:442.151333pt;} .y7e5{bottom:442.188667pt;} .y850{bottom:442.536667pt;} .y85b{bottom:442.560667pt;} .y866{bottom:442.584667pt;} .y526{bottom:442.915867pt;} .y386{bottom:442.929733pt;} .yb9f{bottom:444.355200pt;} .yba4{bottom:444.367200pt;} .yba9{bottom:444.379200pt;} .ycc1{bottom:445.006000pt;} .y428{bottom:445.385467pt;} .y67c{bottom:445.427067pt;} .y659{bottom:445.549067pt;} .y630{bottom:445.580533pt;} .y7a0{bottom:445.743867pt;} .y77b{bottom:445.753600pt;} .y6a1{bottom:445.759600pt;} .y6c5{bottom:445.827600pt;} .y6e9{bottom:445.895600pt;} .y463{bottom:445.981333pt;} .yf6d{bottom:446.118800pt;} .yf8c{bottom:446.202800pt;} .yfb8{bottom:446.322800pt;} .ycc9{bottom:446.407600pt;} .y994{bottom:446.412533pt;} .y993{bottom:446.416533pt;} .y98b{bottom:446.420533pt;} .y99b{bottom:446.421867pt;} .yb57{bottom:446.429733pt;} .yc05{bottom:446.696800pt;} .y507{bottom:447.799867pt;} .y897{bottom:447.898133pt;} .y4f3{bottom:447.907867pt;} .y89e{bottom:447.922133pt;} .y8a5{bottom:447.946133pt;} .y4b2{bottom:447.946400pt;} .y4cc{bottom:447.958400pt;} .ye0e{bottom:448.088933pt;} .y405{bottom:448.517467pt;} .y3ea{bottom:448.553467pt;} .ydb1{bottom:448.810933pt;} .y9ed{bottom:449.702533pt;} .y9f4{bottom:449.714533pt;} .y9fb{bottom:449.726533pt;} .ydb2{bottom:449.902933pt;} .yd25{bottom:450.519733pt;} .y193{bottom:450.539600pt;} .y1dd{bottom:450.539733pt;} .y12f{bottom:450.548533pt;} .y16d{bottom:450.555733pt;} .y393{bottom:450.559733pt;} .y8c{bottom:450.570133pt;} .y594{bottom:450.575600pt;} .y26e{bottom:450.579733pt;} .y54b{bottom:450.607733pt;} .y63{bottom:450.631333pt;} .yb4{bottom:450.633733pt;} .y2fc{bottom:450.635733pt;} .yf4{bottom:450.652933pt;} .y1b1{bottom:450.659600pt;} .y1fa{bottom:450.659733pt;} .y36b{bottom:450.671733pt;} .y3b6{bottom:450.691733pt;} .y28c{bottom:450.699733pt;} .y566{bottom:450.715733pt;} .ye66{bottom:450.734667pt;} .y576{bottom:450.775733pt;} .y218{bottom:450.779733pt;} .y3ce{bottom:450.787733pt;} .y2c1{bottom:450.903733pt;} .y343{bottom:450.959733pt;} .yaf4{bottom:450.988669pt;} .yaef{bottom:451.001816pt;} .yaea{bottom:451.014962pt;} .y95d{bottom:451.592267pt;} .y964{bottom:451.604267pt;} .y96b{bottom:451.616267pt;} .y90d{bottom:451.992133pt;} .y915{bottom:452.016133pt;} .y91d{bottom:452.040133pt;} .y27{bottom:452.519817pt;} .ya52{bottom:452.757467pt;} .ya5b{bottom:452.793467pt;} .ya64{bottom:452.829467pt;} .ya2c{bottom:453.298667pt;} .yf04{bottom:454.712869pt;} .ycfa{bottom:455.655067pt;} .yd51{bottom:456.169214pt;} .y60a{bottom:456.506267pt;} .y5e7{bottom:456.590267pt;} .y5c3{bottom:456.674267pt;} .y75c{bottom:456.860133pt;} .y70d{bottom:456.872000pt;} .y733{bottom:456.874267pt;} .y7c1{bottom:456.876667pt;} .y803{bottom:456.890533pt;} .y7e4{bottom:456.914000pt;} .yeb3{bottom:456.935867pt;} .y84f{bottom:457.200667pt;} .y85a{bottom:457.224667pt;} .y865{bottom:457.248667pt;} .y525{bottom:457.627867pt;} .yc73{bottom:458.190267pt;} .yc2f{bottom:458.337867pt;} .yb9e{bottom:459.019200pt;} .yba3{bottom:459.031200pt;} .yba8{bottom:459.043200pt;} .yc20{bottom:459.135067pt;} .y67b{bottom:459.741467pt;} .y62e{bottom:459.859067pt;} .y658{bottom:459.863467pt;} .ycf4{bottom:459.875867pt;} .y62f{bottom:459.890400pt;} .y427{bottom:460.049467pt;} .y79f{bottom:460.059733pt;} .y77a{bottom:460.067600pt;} .y6a0{bottom:460.073600pt;} .y79e{bottom:460.135600pt;} .y6c4{bottom:460.141600pt;} .y6e8{bottom:460.209600pt;} .yf6c{bottom:460.782800pt;} .y462{bottom:460.861333pt;} .yf8b{bottom:460.866800pt;} .yc63{bottom:460.877200pt;} .yfb7{bottom:460.986800pt;} .y992{bottom:461.080533pt;} .y98a{bottom:461.084533pt;} .y99a{bottom:461.085867pt;} .yb56{bottom:461.093733pt;} .yc54{bottom:461.674533pt;} .y497{bottom:462.874400pt;} .y4b1{bottom:462.886400pt;} .y4cb{bottom:462.898400pt;} .y506{bottom:463.207867pt;} .y4f2{bottom:463.315867pt;} .y896{bottom:463.894133pt;} .y89d{bottom:463.918133pt;} .y8a4{bottom:463.942133pt;} .ye0d{bottom:464.088933pt;} .y9ec{bottom:464.366533pt;} .y9f3{bottom:464.378533pt;} .y9fa{bottom:464.390533pt;} .ydaf{bottom:464.806933pt;} .ybf0{bottom:465.064267pt;} .ydb0{bottom:465.898933pt;} .y95c{bottom:466.256267pt;} .y963{bottom:466.268267pt;} .y96a{bottom:466.280267pt;} .y192{bottom:466.535600pt;} .y1dc{bottom:466.535733pt;} .y12e{bottom:466.544933pt;} .y16c{bottom:466.552133pt;} .y392{bottom:466.555733pt;} .y8b{bottom:466.566533pt;} .y593{bottom:466.571600pt;} .y26d{bottom:466.575733pt;} .y54a{bottom:466.603733pt;} .y62{bottom:466.627733pt;} .yb3{bottom:466.630133pt;} .y2fb{bottom:466.631733pt;} .yf3{bottom:466.649333pt;} .y1b0{bottom:466.655600pt;} .y1f9{bottom:466.655733pt;} .y90c{bottom:466.656133pt;} .y36a{bottom:466.667733pt;} .y914{bottom:466.680133pt;} .y3b5{bottom:466.687733pt;} .y28b{bottom:466.695733pt;} .y91c{bottom:466.704133pt;} .y565{bottom:466.711733pt;} .y575{bottom:466.771733pt;} .y217{bottom:466.775733pt;} .y3cd{bottom:466.783733pt;} .y2c0{bottom:466.899733pt;} .y342{bottom:466.955733pt;} .ye5b{bottom:467.872933pt;} .yaf3{bottom:467.894768pt;} .yaee{bottom:467.907915pt;} .yae9{bottom:467.921061pt;} .ycd4{bottom:468.218267pt;} .ya51{bottom:468.753467pt;} .ya5a{bottom:468.789467pt;} .ya63{bottom:468.825467pt;} .yf03{bottom:469.878565pt;} .ycf9{bottom:470.323067pt;} .y26{bottom:470.745267pt;} .y609{bottom:471.230267pt;} .y5e6{bottom:471.314267pt;} .y5c2{bottom:471.398267pt;} .y75b{bottom:471.587867pt;} .y75a{bottom:471.592533pt;} .y70c{bottom:471.597333pt;} .y732{bottom:471.599600pt;} .y7c0{bottom:471.602000pt;} .y802{bottom:471.615867pt;} .y7e3{bottom:471.639333pt;} .ybd0{bottom:471.740667pt;} .yd50{bottom:471.804526pt;} .y84e{bottom:471.864667pt;} .y859{bottom:471.888667pt;} .y864{bottom:471.912667pt;} .y524{bottom:472.327867pt;} .yeb2{bottom:472.935867pt;} .y438{bottom:473.185600pt;} .ya28{bottom:473.285867pt;} .yb9d{bottom:473.683200pt;} .yba2{bottom:473.695200pt;} .yba7{bottom:473.707200pt;} .yb81{bottom:473.797867pt;} .y67a{bottom:474.055867pt;} .yaaa{bottom:474.074925pt;} .yaa3{bottom:474.101217pt;} .ya9c{bottom:474.127510pt;} .y62d{bottom:474.173467pt;} .y657{bottom:474.177867pt;} .y779{bottom:474.381600pt;} .y69f{bottom:474.387600pt;} .y79d{bottom:474.449600pt;} .y6c3{bottom:474.455600pt;} .y6e7{bottom:474.523600pt;} .ycf3{bottom:474.543867pt;} .y426{bottom:474.713467pt;} .ydf5{bottom:474.896667pt;} .yf6b{bottom:475.446800pt;} .yf8a{bottom:475.530800pt;} .yfb6{bottom:475.650800pt;} .y461{bottom:475.741333pt;} .y991{bottom:475.744533pt;} .y989{bottom:475.748533pt;} .y999{bottom:475.749867pt;} .yb55{bottom:475.757733pt;} .ye38{bottom:476.931867pt;} .y496{bottom:477.814400pt;} .y4b0{bottom:477.826400pt;} .y4ca{bottom:477.838400pt;} .y505{bottom:478.615867pt;} .y4f1{bottom:478.723867pt;} .y9eb{bottom:479.030533pt;} .y9f2{bottom:479.042533pt;} .y9f9{bottom:479.054533pt;} .ycc5{bottom:479.576933pt;} .y895{bottom:479.890133pt;} .y89c{bottom:479.914133pt;} .y8a3{bottom:479.938133pt;} .ye0c{bottom:480.088933pt;} .yd86{bottom:480.266235pt;} .ydad{bottom:480.802933pt;} .y95b{bottom:480.920267pt;} .y962{bottom:480.932267pt;} .y969{bottom:480.944267pt;} .y90b{bottom:481.320133pt;} .y913{bottom:481.344133pt;} .y91b{bottom:481.368133pt;} .ydae{bottom:481.894933pt;} .y191{bottom:482.531600pt;} .y1db{bottom:482.531733pt;} .y12d{bottom:482.541333pt;} .y16b{bottom:482.548533pt;} .y8a{bottom:482.562933pt;} .y592{bottom:482.567600pt;} .y26c{bottom:482.571733pt;} .y549{bottom:482.599733pt;} .y61{bottom:482.624133pt;} .yb2{bottom:482.626533pt;} .y2fa{bottom:482.627733pt;} .yf2{bottom:482.645733pt;} .y1af{bottom:482.651600pt;} .y1f8{bottom:482.651733pt;} .y369{bottom:482.663733pt;} .y28a{bottom:482.691733pt;} .y564{bottom:482.707733pt;} .y574{bottom:482.767733pt;} .y216{bottom:482.771733pt;} .y3cc{bottom:482.779733pt;} .y2bf{bottom:482.895733pt;} .y341{bottom:482.951733pt;} .yb3d{bottom:483.794933pt;} .ye5a{bottom:483.872933pt;} .yc04{bottom:484.196800pt;} .ya50{bottom:484.749467pt;} .ya59{bottom:484.785467pt;} .yaf2{bottom:484.800867pt;} .yaed{bottom:484.814014pt;} .ya62{bottom:484.821467pt;} .yae8{bottom:484.827160pt;} .ycf8{bottom:484.991067pt;} .yf02{bottom:485.044261pt;} .yd94{bottom:485.833067pt;} .y608{bottom:485.954267pt;} .y5e5{bottom:486.038267pt;} .y5c1{bottom:486.122267pt;} .y759{bottom:486.317867pt;} .y70b{bottom:486.322667pt;} .y731{bottom:486.324933pt;} .y7bf{bottom:486.327333pt;} .y801{bottom:486.341200pt;} .y7e2{bottom:486.364667pt;} .ye7c{bottom:486.444667pt;} .y84d{bottom:486.528667pt;} .y858{bottom:486.552667pt;} .y863{bottom:486.576667pt;} .y523{bottom:487.039867pt;} .yd4f{bottom:487.439838pt;} .yb09{bottom:487.893467pt;} .y679{bottom:488.370267pt;} .y62c{bottom:488.487867pt;} .y656{bottom:488.492267pt;} .y778{bottom:488.695600pt;} .y69e{bottom:488.701600pt;} .y79c{bottom:488.763600pt;} .y6c2{bottom:488.769600pt;} .y6e6{bottom:488.837600pt;} .yeb1{bottom:488.935867pt;} .y25{bottom:488.970717pt;} .ycf2{bottom:489.211867pt;} .y425{bottom:489.377467pt;} .ydf4{bottom:489.476667pt;} .yf6a{bottom:490.110800pt;} .yf89{bottom:490.194800pt;} .yfb5{bottom:490.314800pt;} .y990{bottom:490.408533pt;} .y988{bottom:490.412533pt;} .y998{bottom:490.413867pt;} .yb54{bottom:490.421733pt;} .yd22{bottom:490.538133pt;} .y460{bottom:490.621333pt;} .yaa9{bottom:490.981024pt;} .yaa2{bottom:491.007316pt;} .ya9b{bottom:491.033609pt;} .yb80{bottom:492.464533pt;} .y495{bottom:492.754400pt;} .y4af{bottom:492.766400pt;} .y4c9{bottom:492.778400pt;} .ye37{bottom:492.931867pt;} .y437{bottom:493.188267pt;} .y9ea{bottom:493.694533pt;} .y9f1{bottom:493.706533pt;} .y9f8{bottom:493.718533pt;} .y504{bottom:494.023867pt;} .y4f0{bottom:494.131867pt;} .yc9f{bottom:495.294400pt;} .y95a{bottom:495.584267pt;} .y961{bottom:495.596267pt;} .y968{bottom:495.608267pt;} .yc72{bottom:495.690267pt;} .yc2e{bottom:495.837867pt;} .y894{bottom:495.886133pt;} .y89b{bottom:495.910133pt;} .y8a2{bottom:495.934133pt;} .y90a{bottom:495.984133pt;} .y912{bottom:496.008133pt;} .y91a{bottom:496.032133pt;} .ye0b{bottom:496.088933pt;} .yc1f{bottom:496.635067pt;} .ycb5{bottom:497.083067pt;} .ye96{bottom:497.168000pt;} .yd85{bottom:497.225619pt;} .yca4{bottom:497.933333pt;} .yb3c{bottom:498.458933pt;} .y190{bottom:498.527600pt;} .y1da{bottom:498.527733pt;} .y12c{bottom:498.537733pt;} .y16a{bottom:498.544933pt;} .y89{bottom:498.559333pt;} .y591{bottom:498.563600pt;} .y26b{bottom:498.567733pt;} .y548{bottom:498.595733pt;} .y60{bottom:498.620533pt;} .yb1{bottom:498.622933pt;} .y2f9{bottom:498.623733pt;} .yf1{bottom:498.642133pt;} .y1ae{bottom:498.647600pt;} .y1f7{bottom:498.647733pt;} .y368{bottom:498.659733pt;} .y289{bottom:498.687733pt;} .y563{bottom:498.703733pt;} .y573{bottom:498.763733pt;} .y215{bottom:498.767733pt;} .y3cb{bottom:498.775733pt;} .y2be{bottom:498.891733pt;} .y340{bottom:498.947733pt;} .ybce{bottom:499.269067pt;} .ye59{bottom:499.872933pt;} .yf01{bottom:500.209957pt;} .ya2b{bottom:500.631467pt;} .y607{bottom:500.678267pt;} .ya4f{bottom:500.745467pt;} .y5e4{bottom:500.762267pt;} .ya58{bottom:500.781467pt;} .ya61{bottom:500.817467pt;} .y5c0{bottom:500.846267pt;} .y758{bottom:501.043200pt;} .y70a{bottom:501.048000pt;} .y730{bottom:501.050267pt;} .y7be{bottom:501.052667pt;} .y800{bottom:501.066533pt;} .y7e1{bottom:501.090000pt;} .y84c{bottom:501.192667pt;} .y857{bottom:501.216667pt;} .y862{bottom:501.240667pt;} .y522{bottom:501.739867pt;} .ye7b{bottom:502.444667pt;} .y678{bottom:502.684667pt;} .y62b{bottom:502.802267pt;} .y655{bottom:502.806667pt;} .y777{bottom:503.009600pt;} .y69d{bottom:503.015600pt;} .yd4e{bottom:503.075150pt;} .y79b{bottom:503.077600pt;} .y6c1{bottom:503.083600pt;} .y6e5{bottom:503.151600pt;} .yca8{bottom:503.498800pt;} .yecf{bottom:503.724667pt;} .ycf1{bottom:503.879867pt;} .y424{bottom:504.041467pt;} .ydf3{bottom:504.056667pt;} .ydb6{bottom:504.642933pt;} .yf69{bottom:504.774800pt;} .yf88{bottom:504.858800pt;} .yeb0{bottom:504.935867pt;} .yfb4{bottom:504.978800pt;} .y45f{bottom:505.501333pt;} .ycf7{bottom:505.731067pt;} .yc62{bottom:505.877200pt;} .yc53{bottom:506.674533pt;} .y3d8{bottom:506.784133pt;} .y24{bottom:507.196167pt;} .y494{bottom:507.694400pt;} .y4ae{bottom:507.706400pt;} .y4c8{bottom:507.718400pt;} .yaa8{bottom:507.887123pt;} .yb08{bottom:507.890133pt;} .yaa1{bottom:507.913415pt;} .ya9a{bottom:507.939708pt;} .y9e9{bottom:508.358533pt;} .y9f0{bottom:508.370533pt;} .y9f7{bottom:508.382533pt;} .ydaa{bottom:508.874533pt;} .ye36{bottom:508.931867pt;} .y503{bottom:509.431867pt;} .y4ef{bottom:509.539867pt;} .yf23{bottom:509.577733pt;} .y959{bottom:510.248267pt;} .y960{bottom:510.260267pt;} .y967{bottom:510.272267pt;} .y909{bottom:510.648133pt;} .y911{bottom:510.672133pt;} .y919{bottom:510.696133pt;} .yd1d{bottom:510.789333pt;} .ycfb{bottom:510.946000pt;} .yb7f{bottom:511.131200pt;} .y893{bottom:511.882133pt;} .y89a{bottom:511.906133pt;} .y8a1{bottom:511.930133pt;} .ye0a{bottom:512.088933pt;} .ycac{bottom:512.550933pt;} .yb3b{bottom:513.122933pt;} .ye95{bottom:513.168000pt;} .y436{bottom:513.190933pt;} .yd84{bottom:514.185002pt;} .y18f{bottom:514.523600pt;} .y1d9{bottom:514.523733pt;} .y12b{bottom:514.534133pt;} .y169{bottom:514.541333pt;} .y88{bottom:514.555733pt;} .y590{bottom:514.559600pt;} .y26a{bottom:514.563733pt;} .y547{bottom:514.591733pt;} .y5f{bottom:514.616933pt;} .yb0{bottom:514.619333pt;} .y2f8{bottom:514.619733pt;} .yf0{bottom:514.638533pt;} .y1ad{bottom:514.643600pt;} .y1f6{bottom:514.643733pt;} .y367{bottom:514.655733pt;} .y288{bottom:514.683733pt;} .y562{bottom:514.699733pt;} .y572{bottom:514.759733pt;} .y214{bottom:514.763733pt;} .y3ca{bottom:514.771733pt;} .y2bd{bottom:514.887733pt;} .y33f{bottom:514.943733pt;} .yf00{bottom:515.375653pt;} .y606{bottom:515.402267pt;} .y5e3{bottom:515.486267pt;} .y5bf{bottom:515.570267pt;} .y757{bottom:515.770933pt;} .y709{bottom:515.773333pt;} .y72f{bottom:515.775600pt;} .y7bd{bottom:515.778000pt;} .y756{bottom:515.784800pt;} .y7ff{bottom:515.791867pt;} .y7e0{bottom:515.815333pt;} .y84b{bottom:515.856667pt;} .ye58{bottom:515.872933pt;} .y856{bottom:515.880667pt;} .y861{bottom:515.904667pt;} .y521{bottom:516.439867pt;} .ya4e{bottom:516.741467pt;} .ya57{bottom:516.777467pt;} .ya60{bottom:516.813467pt;} .y677{bottom:516.999067pt;} .ycd3{bottom:517.031600pt;} .y62a{bottom:517.116667pt;} .y654{bottom:517.121067pt;} .y776{bottom:517.323600pt;} .y69c{bottom:517.329600pt;} .y79a{bottom:517.391600pt;} .y6c0{bottom:517.397600pt;} .y6e4{bottom:517.465600pt;} .ye7a{bottom:518.444667pt;} .y423{bottom:518.705467pt;} .yf68{bottom:519.438800pt;} .yf87{bottom:519.522800pt;} .yfb3{bottom:519.642800pt;} .yece{bottom:519.724667pt;} .y45e{bottom:520.381333pt;} .yf22{bottom:520.777733pt;} .yeaf{bottom:520.935867pt;} .ydfa{bottom:521.336400pt;} .y493{bottom:522.634400pt;} .y4ad{bottom:522.646400pt;} .y4c7{bottom:522.658400pt;} .ycc3{bottom:524.188133pt;} .ycec{bottom:524.622400pt;} .yced{bottom:524.628800pt;} .yaa7{bottom:524.793222pt;} .yaa0{bottom:524.819514pt;} .y502{bottom:524.839867pt;} .ya99{bottom:524.845807pt;} .ye35{bottom:524.931867pt;} .y4ee{bottom:524.947867pt;} .yc9e{bottom:525.168933pt;} .y23{bottom:525.421617pt;} .ycb3{bottom:525.862800pt;} .ybcd{bottom:525.930733pt;} .yd33{bottom:526.670366pt;} .yc99{bottom:526.805131pt;} .yb3a{bottom:527.786933pt;} .yca2{bottom:527.816133pt;} .yca1{bottom:527.826513pt;} .yb07{bottom:527.886800pt;} .ye09{bottom:528.088933pt;} .yd1c{bottom:528.125333pt;} .ybcf{bottom:528.509067pt;} .ye94{bottom:529.168000pt;} .yc03{bottom:529.196800pt;} .y3d7{bottom:529.226400pt;} .yb7e{bottom:529.797867pt;} .y605{bottom:530.126267pt;} .ycf6{bottom:530.190267pt;} .y5e2{bottom:530.210267pt;} .y5be{bottom:530.294267pt;} .ybef{bottom:530.299067pt;} .y708{bottom:530.498667pt;} .y72e{bottom:530.500933pt;} .y7bc{bottom:530.503333pt;} .y755{bottom:530.510133pt;} .y7fe{bottom:530.517200pt;} .y18e{bottom:530.519600pt;} .y1d8{bottom:530.519733pt;} .y84a{bottom:530.520667pt;} .y12a{bottom:530.530533pt;} .y168{bottom:530.537733pt;} .y7df{bottom:530.540667pt;} .yeff{bottom:530.541349pt;} .y855{bottom:530.544667pt;} .y87{bottom:530.552133pt;} .y58f{bottom:530.555600pt;} .y269{bottom:530.559733pt;} .y860{bottom:530.568667pt;} .y546{bottom:530.587733pt;} .y5e{bottom:530.613333pt;} .yaf{bottom:530.615733pt;} .yef{bottom:530.634933pt;} .y1ac{bottom:530.639600pt;} .y1f5{bottom:530.639733pt;} .y366{bottom:530.651733pt;} .y287{bottom:530.679733pt;} .y561{bottom:530.695733pt;} .y571{bottom:530.755733pt;} .y213{bottom:530.759733pt;} .y3c9{bottom:530.767733pt;} .y2bc{bottom:530.883733pt;} .y33e{bottom:530.939733pt;} .yd83{bottom:531.144386pt;} .y520{bottom:531.151867pt;} .y676{bottom:531.313467pt;} .y629{bottom:531.431067pt;} .y653{bottom:531.435467pt;} .y775{bottom:531.639600pt;} .y69b{bottom:531.643600pt;} .y799{bottom:531.705600pt;} .y6bf{bottom:531.711600pt;} .y6e3{bottom:531.779600pt;} .ye57{bottom:531.872933pt;} .y435{bottom:533.193600pt;} .y422{bottom:533.369467pt;} .yca7{bottom:533.511733pt;} .yf67{bottom:534.102800pt;} .yf86{bottom:534.186800pt;} .yfb2{bottom:534.306800pt;} .ye79{bottom:534.444667pt;} .y45d{bottom:535.261333pt;} .yecd{bottom:535.724667pt;} .yeae{bottom:536.935867pt;} .y492{bottom:537.574400pt;} .y4ac{bottom:537.586400pt;} .y4c6{bottom:537.598400pt;} .ycd7{bottom:539.252133pt;} .y501{bottom:540.247867pt;} .y4ed{bottom:540.355867pt;} .yc71{bottom:540.690267pt;} .yc2d{bottom:540.837867pt;} .ye34{bottom:540.931867pt;} .ydc0{bottom:541.247333pt;} .yc1e{bottom:541.635067pt;} .yaa6{bottom:541.699321pt;} .ya9f{bottom:541.725613pt;} .ya98{bottom:541.751906pt;} .yca9{bottom:542.203347pt;} .ycaa{bottom:542.212800pt;} .yb39{bottom:542.450933pt;} .y22{bottom:543.647067pt;} .ye08{bottom:544.088933pt;} .y604{bottom:544.850267pt;} .y5e1{bottom:544.934267pt;} .y5bd{bottom:545.018267pt;} .ye93{bottom:545.168000pt;} .y849{bottom:545.184667pt;} .y854{bottom:545.208667pt;} .y707{bottom:545.226267pt;} .y706{bottom:545.228667pt;} .y85f{bottom:545.232667pt;} .y754{bottom:545.235467pt;} .y7fd{bottom:545.242533pt;} .y7de{bottom:545.266000pt;} .yd1b{bottom:545.461333pt;} .y675{bottom:545.627867pt;} .yefe{bottom:545.707045pt;} .y628{bottom:545.745467pt;} .y652{bottom:545.749867pt;} .y51f{bottom:545.851867pt;} .y69a{bottom:545.957600pt;} .y798{bottom:546.019600pt;} .y6be{bottom:546.025600pt;} .y6e2{bottom:546.093600pt;} .y129{bottom:546.526933pt;} .y167{bottom:546.534133pt;} .y86{bottom:546.548533pt;} .y58e{bottom:546.551600pt;} .y268{bottom:546.555733pt;} .y545{bottom:546.583733pt;} .y5d{bottom:546.609733pt;} .y2f7{bottom:546.611733pt;} .yae{bottom:546.612133pt;} .yee{bottom:546.631333pt;} .y365{bottom:546.647733pt;} .y286{bottom:546.675733pt;} .y560{bottom:546.691733pt;} .y570{bottom:546.751733pt;} .y31c{bottom:546.755733pt;} .y3c8{bottom:546.763733pt;} .y2bb{bottom:546.879733pt;} .y33d{bottom:546.935733pt;} .yf2b{bottom:547.243867pt;} .ye56{bottom:547.872933pt;} .yb06{bottom:547.883467pt;} .y3d6{bottom:547.894400pt;} .y421{bottom:548.033467pt;} .yb7d{bottom:548.464533pt;} .yf66{bottom:548.766800pt;} .yf85{bottom:548.850800pt;} .yfb1{bottom:548.970800pt;} .ybee{bottom:549.499067pt;} .yf21{bottom:550.140400pt;} .y45c{bottom:550.141333pt;} .ye78{bottom:550.444667pt;} .yecc{bottom:551.724667pt;} .yd6e{bottom:551.905983pt;} .y491{bottom:552.514400pt;} .y4ab{bottom:552.526400pt;} .y4c5{bottom:552.538400pt;} .ybcc{bottom:552.592400pt;} .yead{bottom:552.935867pt;} .y434{bottom:553.196267pt;} .ydbf{bottom:554.599493pt;} .yf0f{bottom:554.856667pt;} .y500{bottom:555.655867pt;} .y4ec{bottom:555.763867pt;} .ye33{bottom:556.931867pt;} .yb38{bottom:557.114933pt;} .ycb2{bottom:558.129467pt;} .yaa5{bottom:558.605419pt;} .ya9e{bottom:558.631712pt;} .ya97{bottom:558.658005pt;} .y603{bottom:559.574267pt;} .y5e0{bottom:559.658267pt;} .y5bc{bottom:559.742267pt;} .y674{bottom:559.942267pt;} .y705{bottom:559.954000pt;} .y72d{bottom:559.958400pt;} .y753{bottom:559.960800pt;} .y7fc{bottom:559.967867pt;} .y7dd{bottom:559.991333pt;} .y651{bottom:560.022800pt;} .y627{bottom:560.059867pt;} .ye07{bottom:560.088933pt;} .y699{bottom:560.271600pt;} .y797{bottom:560.333600pt;} .y6bd{bottom:560.339600pt;} .y6e1{bottom:560.407600pt;} .y51e{bottom:560.551867pt;} .yefd{bottom:560.872741pt;} .ye92{bottom:561.168000pt;} .yf20{bottom:561.340400pt;} .ydf2{bottom:561.524667pt;} .y18c{bottom:562.188267pt;} .y128{bottom:562.523333pt;} .y166{bottom:562.530533pt;} .y85{bottom:562.544933pt;} .y58d{bottom:562.547600pt;} .y267{bottom:562.551733pt;} .y544{bottom:562.579733pt;} .y5c{bottom:562.606133pt;} .y2f6{bottom:562.607733pt;} .yad{bottom:562.608533pt;} .yed{bottom:562.627733pt;} .y364{bottom:562.643733pt;} .y285{bottom:562.671733pt;} .y55f{bottom:562.687733pt;} .y420{bottom:562.697467pt;} .y56f{bottom:562.747733pt;} .y31b{bottom:562.751733pt;} .y3c7{bottom:562.759733pt;} .yd1a{bottom:562.797333pt;} .y2ba{bottom:562.875733pt;} .y33c{bottom:562.931733pt;} .ycd8{bottom:563.220267pt;} .yf65{bottom:563.430800pt;} .yf84{bottom:563.514800pt;} .yfb0{bottom:563.634800pt;} .ye55{bottom:563.872933pt;} .y1d6{bottom:564.076267pt;} .y3a{bottom:564.500520pt;} .y45b{bottom:565.021333pt;} .ye77{bottom:566.444667pt;} .y3d5{bottom:566.562400pt;} .y16{bottom:567.093011pt;} .yb7c{bottom:567.131200pt;} .y490{bottom:567.454400pt;} .y4aa{bottom:567.466400pt;} .y4c4{bottom:567.478400pt;} .yecb{bottom:567.724667pt;} .yb04{bottom:567.880133pt;} .ydbe{bottom:567.951653pt;} .yd4d{bottom:568.194112pt;} .ybed{bottom:568.699067pt;} .yeac{bottom:568.935867pt;} .yb05{bottom:568.941800pt;} .yd9f{bottom:570.584533pt;} .y4ff{bottom:571.063867pt;} .y4eb{bottom:571.171867pt;} .ye32{bottom:572.931867pt;} .y433{bottom:573.198933pt;} .y51d{bottom:575.263867pt;} .yaa4{bottom:575.511518pt;} .ya9d{bottom:575.537811pt;} .ya96{bottom:575.564103pt;} .ydca{bottom:575.605120pt;} .yefc{bottom:576.038437pt;} .ye06{bottom:576.088933pt;} .ydf1{bottom:576.104667pt;} .ye91{bottom:577.168000pt;} .y41f{bottom:577.361467pt;} .yf64{bottom:578.094800pt;} .yfaf{bottom:578.298800pt;} .y127{bottom:578.519733pt;} .y165{bottom:578.526933pt;} .y84{bottom:578.541333pt;} .y58c{bottom:578.543600pt;} .y266{bottom:578.547733pt;} .y543{bottom:578.575733pt;} .y5b{bottom:578.602533pt;} .y2f5{bottom:578.603733pt;} .yac{bottom:578.604933pt;} .yec{bottom:578.624133pt;} .y363{bottom:578.639733pt;} .y284{bottom:578.667733pt;} .y55e{bottom:578.683733pt;} .y56e{bottom:578.743733pt;} .y31a{bottom:578.747733pt;} .y3c6{bottom:578.755733pt;} .y2b9{bottom:578.871733pt;} .y33b{bottom:578.927733pt;} .ye54{bottom:579.872933pt;} .yd19{bottom:580.133333pt;} .ydbd{bottom:581.303813pt;} .y18b{bottom:581.388267pt;} .y8d1{bottom:582.047200pt;} .y48f{bottom:582.394400pt;} .y4a9{bottom:582.406400pt;} .y4c3{bottom:582.418400pt;} .ye76{bottom:582.444667pt;} .yd9e{bottom:582.584533pt;} .y1d5{bottom:583.276267pt;} .yeca{bottom:583.724667pt;} .yd4c{bottom:583.829424pt;} .ybcb{bottom:584.056800pt;} .yeab{bottom:584.935867pt;} .y3d4{bottom:585.230400pt;} .yb7b{bottom:585.797867pt;} .y4fe{bottom:586.471867pt;} .y4ea{bottom:586.579867pt;} .yb02{bottom:587.876800pt;} .ybec{bottom:587.899067pt;} .ye31{bottom:588.931867pt;} .yb03{bottom:588.938467pt;} .ydc9{bottom:588.957280pt;} .ydba{bottom:589.917867pt;} .y51c{bottom:589.963867pt;} .ydf0{bottom:590.684667pt;} .yefb{bottom:591.204133pt;} .ye05{bottom:592.088933pt;} .yf63{bottom:592.758800pt;} .yfae{bottom:592.962800pt;} .ye90{bottom:593.168000pt;} .yd82{bottom:593.291229pt;} .y126{bottom:594.519733pt;} .y164{bottom:594.523333pt;} .y83{bottom:594.537733pt;} .y58b{bottom:594.539600pt;} .y265{bottom:594.543733pt;} .y542{bottom:594.571733pt;} .yd9d{bottom:594.584533pt;} .y125{bottom:594.595333pt;} .y5a{bottom:594.598933pt;} .y2f4{bottom:594.599733pt;} .yab{bottom:594.601333pt;} .yeb{bottom:594.620533pt;} .y362{bottom:594.635733pt;} .ydbc{bottom:594.655973pt;} .y283{bottom:594.663733pt;} .y55d{bottom:594.679733pt;} .y56d{bottom:594.739733pt;} .y319{bottom:594.743733pt;} .y3c5{bottom:594.751733pt;} .y45a{bottom:594.781333pt;} .y2b8{bottom:594.867733pt;} .y33a{bottom:594.923733pt;} .ye53{bottom:595.872933pt;} .ycb1{bottom:596.847000pt;} .y48e{bottom:597.334400pt;} .y4a8{bottom:597.346400pt;} .y4c2{bottom:597.358400pt;} .yd18{bottom:597.469333pt;} .y35{bottom:598.145212pt;} .ye75{bottom:598.444667pt;} .yd4b{bottom:599.464736pt;} .yec9{bottom:599.724667pt;} .y18a{bottom:600.588267pt;} .yeaa{bottom:600.935867pt;} .y4fd{bottom:601.879867pt;} .y4e9{bottom:601.987867pt;} .ydc8{bottom:602.309440pt;} .y1d4{bottom:602.476267pt;} .yb7a{bottom:604.464533pt;} .y51b{bottom:604.663867pt;} .ydef{bottom:605.264667pt;} .yd9c{bottom:606.584533pt;} .yf62{bottom:607.422800pt;} .yfad{bottom:607.626800pt;} .ydbb{bottom:608.008133pt;} .ye8f{bottom:609.168000pt;} .yda7{bottom:609.263600pt;} .y459{bottom:609.661333pt;} .y163{bottom:610.519733pt;} .y82{bottom:610.534133pt;} .y58a{bottom:610.535600pt;} .y264{bottom:610.539733pt;} .y541{bottom:610.567733pt;} .y124{bottom:610.591733pt;} .y59{bottom:610.595333pt;} .y2f3{bottom:610.595733pt;} .yaa{bottom:610.597733pt;} .yea{bottom:610.616933pt;} .y361{bottom:610.631733pt;} .y282{bottom:610.659733pt;} .y55c{bottom:610.675733pt;} .y56c{bottom:610.735733pt;} .y318{bottom:610.739733pt;} .y3c4{bottom:610.747733pt;} .y2b7{bottom:610.863733pt;} .y339{bottom:610.919733pt;} .ye52{bottom:611.872933pt;} .y48d{bottom:612.274400pt;} .y4a7{bottom:612.286400pt;} .yd81{bottom:612.293063pt;} .y4c1{bottom:612.298400pt;} .ye74{bottom:614.444667pt;} .yd17{bottom:614.805333pt;} .yd4a{bottom:615.100048pt;} .ydc6{bottom:615.661600pt;} .yec8{bottom:615.724667pt;} .y34{bottom:616.370662pt;} .ydc7{bottom:616.674139pt;} .ye2d{bottom:616.777467pt;} .yea9{bottom:616.935867pt;} .y4fc{bottom:617.287867pt;} .y4e8{bottom:617.395867pt;} .yd9b{bottom:618.584533pt;} .y51a{bottom:619.375867pt;} .y189{bottom:619.788267pt;} .ydee{bottom:619.844667pt;} .ydd2{bottom:620.198667pt;} .y432{bottom:621.600933pt;} .y1d3{bottom:621.676267pt;} .yf61{bottom:622.086800pt;} .yfac{bottom:622.290800pt;} .yb79{bottom:623.131200pt;} .y8ce{bottom:623.525200pt;} .y458{bottom:624.541333pt;} .y531{bottom:624.715867pt;} .ye8e{bottom:625.168000pt;} .yc65{bottom:625.608133pt;} .y162{bottom:626.519733pt;} .y161{bottom:626.526933pt;} .y81{bottom:626.530533pt;} .y589{bottom:626.531600pt;} .y263{bottom:626.535733pt;} .y391{bottom:626.551733pt;} .y540{bottom:626.563733pt;} .y123{bottom:626.588133pt;} .y58{bottom:626.591733pt;} .ya9{bottom:626.594133pt;} .ye9{bottom:626.613333pt;} .y360{bottom:626.627733pt;} .y281{bottom:626.655733pt;} .y55b{bottom:626.671733pt;} .y3b4{bottom:626.683733pt;} .y56b{bottom:626.731733pt;} .y317{bottom:626.735733pt;} .y3c3{bottom:626.743733pt;} .y2b6{bottom:626.859733pt;} .y338{bottom:626.915733pt;} .y48c{bottom:627.214400pt;} .y4a6{bottom:627.226400pt;} .y4c0{bottom:627.238400pt;} .ydb8{bottom:628.028667pt;} .ydc1{bottom:628.275200pt;} .y9af{bottom:628.427528pt;} .yd9a{bottom:630.584533pt;} .yd49{bottom:630.735360pt;} .yc3e{bottom:631.085333pt;} .yd80{bottom:631.294898pt;} .yec7{bottom:631.724667pt;} .yd16{bottom:632.141333pt;} .yda5{bottom:632.239600pt;} .y4fb{bottom:632.695867pt;} .y4e7{bottom:632.803867pt;} .yea8{bottom:632.935867pt;} .yda6{bottom:633.695600pt;} .y519{bottom:634.075867pt;} .yded{bottom:634.424667pt;} .y33{bottom:634.596112pt;} .yd95{bottom:635.096533pt;} .yc76{bottom:635.793600pt;} .yefa{bottom:636.700661pt;} .yf60{bottom:636.750800pt;} .yfab{bottom:636.954800pt;} .ydc5{bottom:637.343333pt;} .yb20{bottom:637.781000pt;} .y188{bottom:638.988267pt;} .y457{bottom:639.421333pt;} .ye45{bottom:639.722667pt;} .ybe4{bottom:639.811600pt;} .yc95{bottom:640.522533pt;} .y1d2{bottom:640.876267pt;} .yb78{bottom:641.797867pt;} .y48b{bottom:642.154400pt;} .y4a5{bottom:642.166400pt;} .y4bf{bottom:642.178400pt;} .ye6f{bottom:642.289200pt;} .y160{bottom:642.523333pt;} .y80{bottom:642.526933pt;} .y588{bottom:642.527600pt;} .y262{bottom:642.531733pt;} .y390{bottom:642.547733pt;} .y53f{bottom:642.559733pt;} .y122{bottom:642.584533pt;} .y2f2{bottom:642.587733pt;} .y57{bottom:642.588133pt;} .ya8{bottom:642.590533pt;} .ye8{bottom:642.609733pt;} .y35f{bottom:642.623733pt;} .y280{bottom:642.651733pt;} .y55a{bottom:642.667733pt;} .y3b3{bottom:642.679733pt;} .y316{bottom:642.731733pt;} .y3c2{bottom:642.739733pt;} .y2b5{bottom:642.855733pt;} .y337{bottom:642.911733pt;} .ye2c{bottom:643.444133pt;} .yd48{bottom:646.370672pt;} .ydd1{bottom:646.865333pt;} .y518{bottom:648.787867pt;} .ydec{bottom:649.004667pt;} .ycbc{bottom:649.096133pt;} .yd15{bottom:649.477333pt;} .yd7f{bottom:650.296732pt;} .y9ae{bottom:651.095471pt;} .yf5f{bottom:651.414800pt;} .yfaa{bottom:651.618800pt;} .yef9{bottom:651.866357pt;} .y32{bottom:652.821562pt;} .ye89{bottom:653.013467pt;} .y456{bottom:654.301333pt;} .yd99{bottom:654.584533pt;} .yec3{bottom:654.903200pt;} .yed9{bottom:655.848133pt;} .y48a{bottom:657.094400pt;} .y4a4{bottom:657.106400pt;} .y4be{bottom:657.118400pt;} .y187{bottom:658.188267pt;} .y15f{bottom:658.519733pt;} .y7f{bottom:658.523333pt;} .y587{bottom:658.523600pt;} .y261{bottom:658.527733pt;} .y38f{bottom:658.543733pt;} .y53e{bottom:658.555733pt;} .y121{bottom:658.580933pt;} .y2f1{bottom:658.583733pt;} .y56{bottom:658.584533pt;} .ya7{bottom:658.586933pt;} .ye7{bottom:658.606133pt;} .y35e{bottom:658.619733pt;} .y27f{bottom:658.647733pt;} .y559{bottom:658.663733pt;} .y3b2{bottom:658.675733pt;} .y315{bottom:658.727733pt;} .y3c1{bottom:658.735733pt;} .y2b4{bottom:658.851733pt;} .y336{bottom:658.907733pt;} .yc84{bottom:659.519867pt;} .y1d1{bottom:660.076267pt;} .y52e{bottom:660.432400pt;} .yb77{bottom:660.464533pt;} .ya20{bottom:661.466067pt;} .ybca{bottom:661.763282pt;} .ybc1{bottom:661.789574pt;} .ybc2{bottom:661.815600pt;} .yd47{bottom:662.005984pt;} .y517{bottom:663.487867pt;} .ydeb{bottom:663.584667pt;} .yda4{bottom:664.033467pt;} .yc07{bottom:665.190000pt;} .ybe3{bottom:665.457867pt;} .yf5e{bottom:666.078800pt;} .yfa9{bottom:666.282800pt;} .ye44{bottom:666.389333pt;} .yd14{bottom:666.813333pt;} .yef8{bottom:667.032053pt;} .yb1f{bottom:667.106000pt;} .y8ef{bottom:667.176000pt;} .ya33{bottom:667.954533pt;} .ye6e{bottom:668.955867pt;} .yc47{bottom:668.979467pt;} .y455{bottom:669.181333pt;} .yd7e{bottom:669.298566pt;} .yc49{bottom:669.825467pt;} .y31{bottom:671.047012pt;} .y489{bottom:672.034400pt;} .y4a3{bottom:672.046400pt;} .y4bd{bottom:672.058400pt;} .y9d0{bottom:672.164078pt;} .y93d{bottom:673.115699pt;} .y586{bottom:674.519600pt;} .y7e{bottom:674.519733pt;} .y260{bottom:674.523733pt;} .y38e{bottom:674.539733pt;} .y53d{bottom:674.551733pt;} .y120{bottom:674.577333pt;} .y2f0{bottom:674.579733pt;} .y55{bottom:674.580933pt;} .ya6{bottom:674.583333pt;} .ye6{bottom:674.602533pt;} .y35d{bottom:674.615733pt;} .y27e{bottom:674.643733pt;} .y558{bottom:674.659733pt;} .y3b1{bottom:674.671733pt;} .yd98{bottom:674.717333pt;} .y314{bottom:674.723733pt;} .y3c0{bottom:674.731733pt;} .y2b3{bottom:674.847733pt;} .y335{bottom:674.903733pt;} .ye2b{bottom:675.444133pt;} .y186{bottom:677.388267pt;} .y8e9{bottom:677.531467pt;} .yd46{bottom:677.641296pt;} .ycbe{bottom:677.724800pt;} .ydea{bottom:678.164667pt;} .y516{bottom:678.187867pt;} .ybc9{bottom:678.669381pt;} .ybc0{bottom:678.695673pt;} .ydd0{bottom:678.872667pt;} .yc3a{bottom:678.905067pt;} .yc74{bottom:678.917067pt;} .yb76{bottom:679.131200pt;} .y1d0{bottom:679.276267pt;} .ye88{bottom:679.680133pt;} .ya1f{bottom:679.794400pt;} .y8cb{bottom:679.855067pt;} .yf5d{bottom:680.742800pt;} .yfa8{bottom:680.946800pt;} .yb8b{bottom:681.453467pt;} .yec2{bottom:681.569867pt;} .yef7{bottom:682.197749pt;} .yed8{bottom:682.514800pt;} .ybe2{bottom:683.057867pt;} .ydc3{bottom:683.238133pt;} .y82e{bottom:683.964647pt;} .y454{bottom:684.061333pt;} .yd13{bottom:684.149333pt;} .yb4a{bottom:684.957223pt;} .ybfd{bottom:685.399600pt;} .y488{bottom:686.974400pt;} .y4a2{bottom:686.986400pt;} .y4bc{bottom:686.998400pt;} .yd7c{bottom:688.245392pt;} .yd7d{bottom:688.300400pt;} .yb82{bottom:688.432533pt;} .yad6{bottom:688.657328pt;} .y30{bottom:689.272462pt;} .y3e6{bottom:689.435200pt;} .y8ee{bottom:689.842667pt;} .y8ed{bottom:689.846389pt;} .y7d{bottom:690.519733pt;} .y38d{bottom:690.535733pt;} .y53c{bottom:690.547733pt;} .y11f{bottom:690.573733pt;} .y2ef{bottom:690.575733pt;} .y54{bottom:690.577333pt;} .ya5{bottom:690.579733pt;} .ye5{bottom:690.598933pt;} .ya31{bottom:690.611558pt;} .y35c{bottom:690.611733pt;} .ya32{bottom:690.621200pt;} .y27d{bottom:690.639733pt;} .y557{bottom:690.655733pt;} .y3b0{bottom:690.667733pt;} .y7c{bottom:690.716533pt;} .y313{bottom:690.719733pt;} .y3bf{bottom:690.727733pt;} .y2b2{bottom:690.843733pt;} .y334{bottom:690.899733pt;} .y47f{bottom:692.598533pt;} .yde9{bottom:692.744667pt;} .y515{bottom:692.899867pt;} .yd45{bottom:693.276608pt;} .yf5c{bottom:695.406800pt;} .ybc8{bottom:695.575479pt;} .yc56{bottom:695.578267pt;} .ybbf{bottom:695.601772pt;} .yfa7{bottom:695.610800pt;} .y93c{bottom:695.783642pt;} .y185{bottom:696.588267pt;} .yef6{bottom:697.363445pt;} .yb75{bottom:697.797867pt;} .ya1e{bottom:698.122733pt;} .ye43{bottom:698.386933pt;} .y453{bottom:698.941333pt;} .ya2d{bottom:699.106667pt;} .y8ca{bottom:699.851733pt;} .yc39{bottom:700.280107pt;} .ye6d{bottom:700.958933pt;} .yd12{bottom:701.485333pt;} .y487{bottom:701.914400pt;} .y4a1{bottom:701.926400pt;} .y4bb{bottom:701.938400pt;} .yc80{bottom:702.257867pt;} .yc91{bottom:704.137040pt;} .ydb9{bottom:704.180400pt;} .y47e{bottom:704.598533pt;} .ycbd{bottom:705.732800pt;} .y15e{bottom:706.519733pt;} .y38c{bottom:706.531733pt;} .y53b{bottom:706.543733pt;} .y11e{bottom:706.570133pt;} .y2ee{bottom:706.571733pt;} .y53{bottom:706.573733pt;} .ye4{bottom:706.595333pt;} .y35b{bottom:706.607733pt;} .y556{bottom:706.651733pt;} .y3af{bottom:706.663733pt;} .y5b7{bottom:706.715600pt;} .y312{bottom:706.715733pt;} .y3be{bottom:706.723733pt;} .y2b1{bottom:706.839733pt;} .y333{bottom:706.895733pt;} .yd7b{bottom:707.247226pt;} .yde8{bottom:707.324667pt;} .y514{bottom:707.599867pt;} .yb8a{bottom:707.629200pt;} .yb89{bottom:707.630744pt;} .yd44{bottom:708.911920pt;} .y82d{bottom:709.374528pt;} .y39{bottom:709.503560pt;} .yf5b{bottom:710.070800pt;} .yfa6{bottom:710.274800pt;} .yad4{bottom:710.561067pt;} .ye87{bottom:711.680133pt;} .y21{bottom:712.232639pt;} .yc09{bottom:712.295147pt;} .ybc7{bottom:712.481578pt;} .ybbe{bottom:712.507871pt;} .yef5{bottom:712.529141pt;} .y883{bottom:712.776205pt;} .yec1{bottom:713.578533pt;} .y452{bottom:713.821333pt;} .yb28{bottom:714.022544pt;} .y1d7{bottom:714.236267pt;} .yed7{bottom:714.518533pt;} .y5bb{bottom:715.104000pt;} .ya1d{bottom:716.451067pt;} .yb73{bottom:716.464533pt;} .y486{bottom:716.854400pt;} .y4a0{bottom:716.866400pt;} .y4ba{bottom:716.878400pt;} .yb74{bottom:717.526200pt;} .ybe1{bottom:718.257867pt;} .yd2c{bottom:718.550267pt;} .yd11{bottom:718.821333pt;} .y3e5{bottom:719.435200pt;} .y8c9{bottom:719.848400pt;} .yc42{bottom:720.211440pt;} .y8e8{bottom:720.837600pt;} .ya7f{bottom:721.162800pt;} .yc38{bottom:721.655147pt;} .yde7{bottom:721.904667pt;} .y513{bottom:722.299867pt;} .y82a{bottom:722.389067pt;} .y15d{bottom:722.519733pt;} .y38b{bottom:722.527733pt;} .y53a{bottom:722.539733pt;} .y11d{bottom:722.566533pt;} .y2ed{bottom:722.567733pt;} .y52{bottom:722.570133pt;} .ye3{bottom:722.591733pt;} .y35a{bottom:722.603733pt;} .y555{bottom:722.647733pt;} .y3ae{bottom:722.659733pt;} .y15c{bottom:722.707733pt;} .y5b6{bottom:722.711600pt;} .y311{bottom:722.711733pt;} .y3bd{bottom:722.719733pt;} .y2b0{bottom:722.835733pt;} .y332{bottom:722.891733pt;} .yc21{bottom:723.068000pt;} .y2df{bottom:723.582000pt;} .yc7f{bottom:723.632907pt;} .yd43{bottom:724.547232pt;} .yf5a{bottom:724.734800pt;} .yfa5{bottom:724.938800pt;} .yc90{bottom:725.512080pt;} .yd7a{bottom:726.249060pt;} .yf1f{bottom:727.072400pt;} .yef4{bottom:727.694837pt;} .y451{bottom:728.701333pt;} .y18d{bottom:728.828267pt;} .ybc6{bottom:729.387677pt;} .ybbd{bottom:729.413970pt;} .y9da{bottom:730.640800pt;} .y9e2{bottom:730.664800pt;} .y9c5{bottom:730.734000pt;} .y9ba{bottom:730.752667pt;} .y485{bottom:731.794400pt;} .y49e{bottom:731.806400pt;} .y4b9{bottom:731.818400pt;} .y49f{bottom:732.898400pt;} .ybfc{bottom:733.670187pt;} .yb11{bottom:734.185867pt;} .yb18{bottom:734.197867pt;} .ya1c{bottom:734.779400pt;} .yb71{bottom:735.131200pt;} .y2de{bottom:735.582000pt;} .ybe0{bottom:735.857867pt;} .yd10{bottom:736.157333pt;} .yb72{bottom:736.192867pt;} .yde6{bottom:736.484667pt;} .yb27{bottom:736.690487pt;} .y882{bottom:736.777556pt;} .y8f9{bottom:737.004133pt;} .y512{bottom:737.011867pt;} .y901{bottom:737.028133pt;} .y8e7{bottom:737.037600pt;} .y38a{bottom:738.523733pt;} .y539{bottom:738.535733pt;} .y11c{bottom:738.562933pt;} .y51{bottom:738.566533pt;} .ye2{bottom:738.588133pt;} .y359{bottom:738.599733pt;} .y554{bottom:738.643733pt;} .y3ad{bottom:738.655733pt;} .y15b{bottom:738.704133pt;} .y5b5{bottom:738.707600pt;} .y3bc{bottom:738.715733pt;} .y2af{bottom:738.831733pt;} .y331{bottom:738.887733pt;} .yd2a{bottom:739.376133pt;} .yf59{bottom:739.398800pt;} .yfa4{bottom:739.602800pt;} .y8c8{bottom:739.845067pt;} .yd42{bottom:740.182544pt;} .yb93{bottom:740.983200pt;} .yb98{bottom:740.995200pt;} .ya2f{bottom:741.244667pt;} .yc41{bottom:741.586480pt;} .y948{bottom:741.979467pt;} .y950{bottom:742.003467pt;} .y958{bottom:742.027467pt;} .yef3{bottom:742.860533pt;} .yc37{bottom:743.030187pt;} .y450{bottom:743.581333pt;} .ya7d{bottom:743.826501pt;} .ya7e{bottom:743.829467pt;} .yd79{bottom:745.250894pt;} .y9d9{bottom:745.304800pt;} .y9e1{bottom:745.328800pt;} .y9c4{bottom:745.398000pt;} .y9b9{bottom:745.416667pt;} .y9cd{bottom:745.422000pt;} .y3e4{bottom:746.031200pt;} .ybc5{bottom:746.293776pt;} .ybbc{bottom:746.320069pt;} .y484{bottom:746.734400pt;} .y49d{bottom:746.746400pt;} .y4b8{bottom:746.758400pt;} .yb53{bottom:747.917733pt;} .yb10{bottom:748.849867pt;} .yb17{bottom:748.861867pt;} .yb1e{bottom:748.873867pt;} .y2e0{bottom:749.291467pt;} .yde5{bottom:751.064667pt;} .y8f8{bottom:751.668133pt;} .y900{bottom:751.692133pt;} .y511{bottom:751.711867pt;} .y908{bottom:751.716133pt;} .y385{bottom:752.448133pt;} .y838{bottom:752.868667pt;} .y841{bottom:752.892667pt;} .ya1b{bottom:753.107733pt;} .y8e6{bottom:753.237600pt;} .ybdf{bottom:753.457867pt;} .yd0f{bottom:753.493333pt;} .yf58{bottom:754.062800pt;} .yfa3{bottom:754.266800pt;} .y389{bottom:754.519733pt;} .y538{bottom:754.531733pt;} .y11b{bottom:754.559333pt;} .y50{bottom:754.562933pt;} .ye1{bottom:754.584533pt;} .y358{bottom:754.595733pt;} .y553{bottom:754.639733pt;} .y3ac{bottom:754.651733pt;} .y15a{bottom:754.700533pt;} .y5b4{bottom:754.703600pt;} .y3bb{bottom:754.711733pt;} .y2ae{bottom:754.827733pt;} .yad1{bottom:754.871867pt;} .y330{bottom:754.883733pt;} .ybfb{bottom:755.045227pt;} .yb92{bottom:755.647200pt;} .yb97{bottom:755.659200pt;} .yb9c{bottom:755.671200pt;} .yd41{bottom:755.817856pt;} .y947{bottom:756.643467pt;} .y94f{bottom:756.667467pt;} .y2f{bottom:756.682327pt;} .y957{bottom:756.691467pt;} .y3e9{bottom:757.079600pt;} .yb24{bottom:757.765867pt;} .yef2{bottom:758.026133pt;} .y44f{bottom:758.461333pt;} .yae1{bottom:758.675258pt;} .yadc{bottom:758.688404pt;} .yae7{bottom:758.703333pt;} .ya3d{bottom:759.285467pt;} .ya45{bottom:759.309467pt;} .ya4d{bottom:759.333467pt;} .y8c7{bottom:759.841733pt;} .y9d8{bottom:759.968800pt;} .y9e0{bottom:759.992800pt;} .y9e8{bottom:760.016800pt;} .y9c3{bottom:760.064667pt;} .y9c2{bottom:760.067333pt;} .y9b8{bottom:760.080667pt;} .y9cc{bottom:760.086000pt;} .yf1e{bottom:760.728400pt;} .y483{bottom:761.674400pt;} .y49c{bottom:761.686400pt;} .y4b7{bottom:761.698400pt;} .yb52{bottom:762.581733pt;} .yc15{bottom:762.961520pt;} .ybc4{bottom:763.199875pt;} .ybbb{bottom:763.226168pt;} .yb0f{bottom:763.513867pt;} .yb16{bottom:763.525867pt;} .yb1d{bottom:763.537867pt;} .yd78{bottom:764.252729pt;} .yc36{bottom:764.405227pt;} .y384{bottom:764.448133pt;} .ye6a{bottom:765.069333pt;} .ya27{bottom:765.260267pt;} .yde4{bottom:765.644667pt;} .yc96{bottom:766.330267pt;} .y8f7{bottom:766.332133pt;} .yc86{bottom:766.334481pt;} .y8ff{bottom:766.356133pt;} .y907{bottom:766.380133pt;} .yc7e{bottom:766.382987pt;} .y510{bottom:766.411867pt;} .yc8f{bottom:768.262160pt;} .yf57{bottom:768.726800pt;} .yb87{bottom:768.742533pt;} .yf83{bottom:768.846800pt;} .y837{bottom:768.864667pt;} .y840{bottom:768.888667pt;} .y848{bottom:768.912667pt;} .yfa2{bottom:768.930800pt;} .y8e5{bottom:769.437600pt;} .y34f{bottom:770.280533pt;} .yb91{bottom:770.311200pt;} .yb96{bottom:770.323200pt;} .yb9b{bottom:770.335200pt;} .y537{bottom:770.527733pt;} .y11a{bottom:770.555733pt;} .y4f{bottom:770.559333pt;} .ye0{bottom:770.580933pt;} .y357{bottom:770.591733pt;} .y552{bottom:770.635733pt;} .y159{bottom:770.696933pt;} .y5b3{bottom:770.699600pt;} .y2ad{bottom:770.823733pt;} .yd0e{bottom:770.829333pt;} .y32f{bottom:770.879733pt;} .yad0{bottom:771.071867pt;} .y946{bottom:771.307467pt;} .y94e{bottom:771.331467pt;} .y956{bottom:771.355467pt;} .ya1a{bottom:771.436067pt;} .yd40{bottom:771.453168pt;} .yf1d{bottom:771.928400pt;} .y829{bottom:771.972133pt;} .y44e{bottom:773.341333pt;} .y9d7{bottom:774.632800pt;} .y9df{bottom:774.656800pt;} .y9e7{bottom:774.680800pt;} .y9c1{bottom:774.731333pt;} .y9b7{bottom:774.744667pt;} .y9cb{bottom:774.750000pt;} .ya3c{bottom:775.281467pt;} .ya44{bottom:775.305467pt;} .ya4c{bottom:775.329467pt;} .yae0{bottom:775.581357pt;} .yadb{bottom:775.594503pt;} .yae6{bottom:775.605733pt;} .ybfa{bottom:776.420267pt;} .y482{bottom:776.614400pt;} .y49b{bottom:776.626400pt;} .y4b6{bottom:776.638400pt;} .yb51{bottom:777.245733pt;} .y38{bottom:777.735360pt;} .yb0e{bottom:778.177867pt;} .yb15{bottom:778.189867pt;} .yb1c{bottom:778.201867pt;} .y3e3{bottom:779.364533pt;} .y88a{bottom:779.494133pt;} .y88f{bottom:779.506133pt;} .y3da{bottom:779.527600pt;} .y8c6{bottom:779.838400pt;} .ybc3{bottom:780.105974pt;} .ybba{bottom:780.132267pt;} .yde3{bottom:780.224667pt;} .y20{bottom:780.469155pt;} .y8f6{bottom:780.996133pt;} .y8fe{bottom:781.020133pt;} .y906{bottom:781.044133pt;} .y50f{bottom:781.123867pt;} .ya89{bottom:782.024572pt;} .ya90{bottom:782.039368pt;} .yd77{bottom:783.254563pt;} .yf56{bottom:783.390800pt;} .yf82{bottom:783.510800pt;} .yfa1{bottom:783.594800pt;} .yc14{bottom:784.336560pt;} .y836{bottom:784.860667pt;} .y83f{bottom:784.884667pt;} .y847{bottom:784.908667pt;} .yb90{bottom:784.975200pt;} .yb95{bottom:784.987200pt;} .yb9a{bottom:784.999200pt;} .y8e4{bottom:785.637600pt;} .yc35{bottom:785.780267pt;} .y945{bottom:785.971467pt;} .y94d{bottom:785.995467pt;} .y955{bottom:786.019467pt;} .y536{bottom:786.523733pt;} .y119{bottom:786.552133pt;} .y4e{bottom:786.555733pt;} .ydf{bottom:786.577333pt;} .y356{bottom:786.587733pt;} .y551{bottom:786.631733pt;} .y158{bottom:786.693333pt;} .y5b2{bottom:786.695600pt;} .yb31{bottom:786.758933pt;} .yb37{bottom:786.770933pt;} .y2ac{bottom:786.819733pt;} .y32e{bottom:786.875733pt;} .yd3f{bottom:787.088480pt;} .yacf{bottom:787.271867pt;} .yc7d{bottom:787.758027pt;} .yd0d{bottom:788.165333pt;} .y828{bottom:788.172133pt;} .y44d{bottom:788.221333pt;} .ybde{bottom:788.657867pt;} .y9d6{bottom:789.296800pt;} .y9de{bottom:789.320800pt;} .y9e6{bottom:789.344800pt;} .y9c0{bottom:789.398000pt;} .y9b6{bottom:789.408667pt;} .y9ca{bottom:789.414000pt;} .y9bf{bottom:789.432667pt;} .yc8e{bottom:789.637200pt;} .ya19{bottom:789.764400pt;} .y3e8{bottom:790.412933pt;} .ya3b{bottom:791.277467pt;} .ya43{bottom:791.301467pt;} .ya4b{bottom:791.325467pt;} .yb50{bottom:791.909733pt;} .yedd{bottom:791.939600pt;} .yadf{bottom:792.487456pt;} .yada{bottom:792.500602pt;} .yae5{bottom:792.508000pt;} .y34e{bottom:792.740000pt;} .yb0d{bottom:792.841867pt;} .yb14{bottom:792.853867pt;} .yb1b{bottom:792.865867pt;} .y889{bottom:794.158133pt;} .y88e{bottom:794.170133pt;} .yb70{bottom:794.413667pt;} .yde2{bottom:794.804667pt;} .y8f5{bottom:795.660133pt;} .y8fd{bottom:795.684133pt;} .y905{bottom:795.708133pt;} .ybf9{bottom:797.795307pt;} .yf55{bottom:798.054800pt;} .yf81{bottom:798.174800pt;} .yfa0{bottom:798.258800pt;} .ya88{bottom:798.930671pt;} .ya95{bottom:798.932320pt;} .ya8f{bottom:798.945467pt;} .yb8f{bottom:799.639200pt;} .yb94{bottom:799.651200pt;} .yb99{bottom:799.663200pt;} .y8c5{bottom:799.835067pt;} .y944{bottom:800.635467pt;} .y94c{bottom:800.659467pt;} .y954{bottom:800.683467pt;} .y835{bottom:800.856667pt;} .y83d{bottom:800.880667pt;} .y846{bottom:800.904667pt;} .yb30{bottom:801.422933pt;} .yb36{bottom:801.434933pt;} .y8e3{bottom:801.837600pt;} .y83e{bottom:801.972667pt;} .yd76{bottom:802.256397pt;} .y535{bottom:802.519733pt;} .y118{bottom:802.548533pt;} .y4d{bottom:802.552133pt;} .yde{bottom:802.573733pt;} .y355{bottom:802.583733pt;} .y550{bottom:802.627733pt;} .y157{bottom:802.689733pt;} .y5b1{bottom:802.691600pt;} .yd3e{bottom:802.723792pt;} .y2ab{bottom:802.815733pt;} .y32d{bottom:802.871733pt;} .y4e6{bottom:802.897600pt;} .y44c{bottom:803.101333pt;} .yace{bottom:803.471867pt;} .yef1{bottom:803.522197pt;} .y9d5{bottom:803.960800pt;} .y9dd{bottom:803.984800pt;} .y9e5{bottom:804.008800pt;} .y9b5{bottom:804.072667pt;} .y9c9{bottom:804.078000pt;} .y9be{bottom:804.096667pt;} .y827{bottom:804.372133pt;} .y8cf{bottom:804.475600pt;} .ye04{bottom:804.888933pt;} .yd0c{bottom:805.501333pt;} .yc13{bottom:805.711600pt;} .ybdd{bottom:806.257867pt;} .yb4f{bottom:806.573733pt;} .yc34{bottom:807.155307pt;} .ya3a{bottom:807.273467pt;} .ya42{bottom:807.297467pt;} .ya4a{bottom:807.321467pt;} .yb0c{bottom:807.505867pt;} .yb13{bottom:807.517867pt;} .yb1a{bottom:807.529867pt;} .ye86{bottom:807.939600pt;} .ya18{bottom:808.092733pt;} .y888{bottom:808.822133pt;} .y88d{bottom:808.834133pt;} .y892{bottom:808.846133pt;} .yc7c{bottom:809.133067pt;} .yd21{bottom:809.234667pt;} .yae3{bottom:809.380409pt;} .yde1{bottom:809.384667pt;} .yade{bottom:809.393555pt;} .yad9{bottom:809.406701pt;} .yae4{bottom:809.410400pt;} .y8f4{bottom:810.324133pt;} .y8fc{bottom:810.348133pt;} .y904{bottom:810.372133pt;} .yc8d{bottom:811.012240pt;} .yd1f{bottom:811.123679pt;} .yd20{bottom:811.124400pt;} .y3e2{bottom:812.697867pt;} .yf54{bottom:812.718800pt;} .yf80{bottom:812.838800pt;} .yf9f{bottom:812.922800pt;} .y943{bottom:815.299467pt;} .y94b{bottom:815.323467pt;} .y953{bottom:815.347467pt;} .y34d{bottom:815.400000pt;} .ya8d{bottom:815.823624pt;} .ya87{bottom:815.836770pt;} .ya94{bottom:815.838419pt;} .ya8e{bottom:815.847867pt;} .yb2f{bottom:816.086933pt;} .yb35{bottom:816.098933pt;} .y834{bottom:816.852667pt;} .y83c{bottom:816.876667pt;} .y845{bottom:816.900667pt;} .y44b{bottom:817.981333pt;} .y8e2{bottom:818.037600pt;} .yd3d{bottom:818.359104pt;} .y117{bottom:818.544933pt;} .y4c{bottom:818.548533pt;} .ydd{bottom:818.570133pt;} .y354{bottom:818.579733pt;} .y9d4{bottom:818.624800pt;} .y9dc{bottom:818.648800pt;} .y9e4{bottom:818.672800pt;} .y156{bottom:818.686133pt;} .y5b0{bottom:818.687600pt;} .yef0{bottom:818.687893pt;} .y9b4{bottom:818.736667pt;} .y9c8{bottom:818.742000pt;} .y9bd{bottom:818.760667pt;} .y2aa{bottom:818.811733pt;} .y32c{bottom:818.867733pt;} .ybf8{bottom:819.170347pt;} .ydab{bottom:819.212533pt;} .yacd{bottom:819.671867pt;} .y8c4{bottom:819.831733pt;} .y826{bottom:820.572133pt;} .ye03{bottom:820.888933pt;} .yb4e{bottom:821.237733pt;} .yd75{bottom:821.258231pt;} .y530{bottom:821.812000pt;} .yb0b{bottom:822.169867pt;} .yb12{bottom:822.181867pt;} .yb19{bottom:822.193867pt;} .yd0b{bottom:822.837333pt;} .ya39{bottom:823.269467pt;} .ya41{bottom:823.293467pt;} .ya49{bottom:823.317467pt;} .y887{bottom:823.486133pt;} .y88c{bottom:823.498133pt;} .y891{bottom:823.510133pt;} .ye73{bottom:823.671333pt;} .yb6f{bottom:823.738667pt;} .y3e7{bottom:823.746267pt;} .ybdc{bottom:823.857867pt;} .ye51{bottom:823.939600pt;} .yde0{bottom:823.964667pt;} .y2e{bottom:824.318997pt;} .y8f3{bottom:824.988133pt;} .y8fb{bottom:825.012133pt;} .y903{bottom:825.036133pt;} .yae2{bottom:826.286507pt;} .yadd{bottom:826.299654pt;} .yad8{bottom:826.312800pt;} .ya17{bottom:826.421067pt;} .yc12{bottom:827.086640pt;} .yf53{bottom:827.382800pt;} .yf7f{bottom:827.502800pt;} .yf9e{bottom:827.586800pt;} .yc33{bottom:828.530347pt;} .y942{bottom:829.963467pt;} .y94a{bottom:829.987467pt;} .y952{bottom:830.011467pt;} .yc7b{bottom:830.508107pt;} .yb2e{bottom:830.750933pt;} .yb34{bottom:830.762933pt;} .yc8c{bottom:832.387280pt;} .ya8c{bottom:832.729723pt;} .ya86{bottom:832.742869pt;} .ya93{bottom:832.744518pt;} .y833{bottom:832.848667pt;} .y44a{bottom:832.861333pt;} .y83b{bottom:832.872667pt;} .y844{bottom:832.896667pt;} .y9d3{bottom:833.288800pt;} .y9db{bottom:833.312800pt;} .y9e3{bottom:833.336800pt;} .y9b3{bottom:833.400667pt;} .y9c7{bottom:833.406000pt;} .y9bc{bottom:833.424667pt;} .y580{bottom:833.750667pt;} .y52f{bottom:833.814667pt;} .yeef{bottom:833.853589pt;} .yd3c{bottom:833.994416pt;} .ya2e{bottom:834.237600pt;} .y116{bottom:834.541333pt;} .y4b{bottom:834.544933pt;} .ydc{bottom:834.566533pt;} .y353{bottom:834.575733pt;} .y155{bottom:834.682533pt;} .y5af{bottom:834.683600pt;} .y2a9{bottom:834.807733pt;} .y32b{bottom:834.863733pt;} .yacc{bottom:835.871867pt;} .yb4d{bottom:835.901733pt;} .y825{bottom:836.772133pt;} .ye02{bottom:836.888933pt;} .y34c{bottom:838.060000pt;} .y886{bottom:838.150133pt;} .y88b{bottom:838.162133pt;} .y890{bottom:838.174133pt;} .yddf{bottom:838.544667pt;} .ya38{bottom:839.265467pt;} .ya40{bottom:839.289467pt;} .ya48{bottom:839.313467pt;} .y8f2{bottom:839.652133pt;} .ye2a{bottom:839.671333pt;} .y8fa{bottom:839.676133pt;} .y902{bottom:839.700133pt;} .y8c3{bottom:839.828400pt;} .ye50{bottom:839.939600pt;} .yd0a{bottom:840.173333pt;} .yd74{bottom:840.260065pt;} .yc08{bottom:840.545387pt;} .yc85{bottom:841.164933pt;} .yea7{bottom:841.829200pt;} .yf52{bottom:842.046800pt;} .yf7e{bottom:842.166800pt;} .yf9d{bottom:842.250800pt;} .y2d{bottom:842.544447pt;} .y941{bottom:844.627467pt;} .y949{bottom:844.651467pt;} .y951{bottom:844.675467pt;} .ya16{bottom:844.749400pt;} .yb2d{bottom:845.414933pt;} .yb33{bottom:845.426933pt;} .y3e1{bottom:846.031200pt;} .y449{bottom:847.741333pt;} .y9b2{bottom:848.064667pt;} .y9c6{bottom:848.070000pt;} .y9bb{bottom:848.088667pt;} .yc11{bottom:848.461680pt;} .y832{bottom:848.844667pt;} .y83a{bottom:848.868667pt;} .y843{bottom:848.892667pt;} .yeee{bottom:849.019285pt;} .yd3b{bottom:849.629728pt;} .ya8b{bottom:849.635821pt;} .ya85{bottom:849.648968pt;} .ya92{bottom:849.650617pt;} .yc32{bottom:849.905387pt;} .y8e1{bottom:850.437600pt;} .y115{bottom:850.537733pt;} .y4a{bottom:850.541333pt;} .ydb{bottom:850.562933pt;} .yb4c{bottom:850.565733pt;} .y352{bottom:850.571733pt;} .y154{bottom:850.678933pt;} .y5ae{bottom:850.679600pt;} .y2a8{bottom:850.803733pt;} .y32a{bottom:850.859733pt;} .yc7a{bottom:851.883147pt;} .yacb{bottom:852.071867pt;} .ye01{bottom:852.888933pt;} .y824{bottom:852.972133pt;} .ydde{bottom:853.124667pt;} .y57f{bottom:854.550667pt;} .ya37{bottom:855.261467pt;} .ya3f{bottom:855.285467pt;} .ya47{bottom:855.309467pt;} .ye29{bottom:855.671333pt;} .ye4f{bottom:855.939600pt;} .yf51{bottom:856.710800pt;} .yf7d{bottom:856.830800pt;} .yf9c{bottom:856.914800pt;} .yd09{bottom:857.509333pt;} .yea6{bottom:857.829200pt;} .ybdb{bottom:859.057867pt;} .yd73{bottom:859.261899pt;} .y8c2{bottom:859.825067pt;} .yb2c{bottom:860.078933pt;} .yb32{bottom:860.090933pt;} .ybf7{bottom:861.920427pt;} .y448{bottom:862.621333pt;} .y37{bottom:862.766973pt;} .ya15{bottom:863.077733pt;} .yeed{bottom:864.184981pt;} .y831{bottom:864.840667pt;} .y839{bottom:864.864667pt;} .y842{bottom:864.888667pt;} .y1f{bottom:865.501079pt;} .y114{bottom:866.534133pt;} .y49{bottom:866.537733pt;} .ya8a{bottom:866.541920pt;} .ya84{bottom:866.555067pt;} .ya91{bottom:866.556716pt;} .yda{bottom:866.559333pt;} .y351{bottom:866.567733pt;} .y8e0{bottom:866.637600pt;} .y153{bottom:866.675333pt;} .y5ad{bottom:866.675600pt;} .y2a7{bottom:866.799733pt;} .y329{bottom:866.855733pt;} .yddd{bottom:867.704667pt;} .ye00{bottom:868.888933pt;} .y823{bottom:869.172133pt;} .yc40{bottom:869.836720pt;} .ya36{bottom:871.257467pt;} .yc31{bottom:871.280427pt;} .ya3e{bottom:871.281467pt;} .ya46{bottom:871.305467pt;} .yf50{bottom:871.374800pt;} .yf7c{bottom:871.494800pt;} .yf9b{bottom:871.578800pt;} .ye28{bottom:871.671333pt;} .ye4e{bottom:871.939600pt;} .yd31{bottom:872.173677pt;} .yea5{bottom:873.829200pt;} .y183{bottom:873.859067pt;} .y182{bottom:873.861043pt;} .yd08{bottom:874.845333pt;} .yc8b{bottom:875.137360pt;} .yd32{bottom:875.319960pt;} .y57e{bottom:875.350667pt;} .ybda{bottom:876.657867pt;} .y447{bottom:877.501333pt;} .yd72{bottom:878.263733pt;} .yeec{bottom:879.350677pt;} .y8c1{bottom:879.821733pt;} .ya14{bottom:881.406067pt;} .yddc{bottom:882.284667pt;} .y113{bottom:882.530533pt;} .y48{bottom:882.534133pt;} .yd9{bottom:882.555733pt;} .y2ec{bottom:882.563733pt;} .y5ac{bottom:882.671600pt;} .y152{bottom:882.671733pt;} .y310{bottom:882.707733pt;} .y2a6{bottom:882.795733pt;} .y8df{bottom:882.837600pt;} .y328{bottom:882.851733pt;} .ybf6{bottom:883.295467pt;} .yaca{bottom:884.471867pt;} .ydff{bottom:884.888933pt;} .y822{bottom:885.372133pt;} .yf4f{bottom:886.038800pt;} .yf7b{bottom:886.158800pt;} .yf9a{bottom:886.242800pt;} .ye27{bottom:887.671333pt;} .ye4d{bottom:887.939600pt;} .y184{bottom:889.450800pt;} .yea4{bottom:889.829200pt;} .yc10{bottom:891.211760pt;} .yd07{bottom:892.181333pt;} .y446{bottom:892.381333pt;} .yc30{bottom:892.655467pt;} .yeeb{bottom:894.516373pt;} .yc79{bottom:894.633227pt;} .y57d{bottom:896.150667pt;} .yc8a{bottom:896.512400pt;} .ycbb{bottom:897.107467pt;} .y112{bottom:898.526933pt;} .y47{bottom:898.530533pt;} .yd8{bottom:898.552133pt;} .y2eb{bottom:898.559733pt;} .y5ab{bottom:898.667600pt;} .y151{bottom:898.668133pt;} .y30f{bottom:898.703733pt;} .y2a5{bottom:898.791733pt;} .y327{bottom:898.847733pt;} .yd6d{bottom:898.896000pt;} .y8de{bottom:899.037600pt;} .ya13{bottom:899.734400pt;} .y8c0{bottom:899.818400pt;} .yac9{bottom:900.671867pt;} .yf4e{bottom:900.702800pt;} .yf7a{bottom:900.822800pt;} .ydfe{bottom:900.888933pt;} .yf99{bottom:900.906800pt;} .yb6d{bottom:900.988133pt;} .y821{bottom:901.572133pt;} .yb6e{bottom:902.432000pt;} .ydf9{bottom:903.367467pt;} .ye26{bottom:903.671333pt;} .ye4c{bottom:903.939600pt;} .yea3{bottom:905.829200pt;} .y445{bottom:907.261333pt;} .yd06{bottom:909.517333pt;} .yeea{bottom:909.682069pt;} .yd3a{bottom:911.044107pt;} .y36{bottom:911.296667pt;} .ybd9{bottom:911.857867pt;} .yc0f{bottom:912.586800pt;} .y15{bottom:913.219067pt;} .y111{bottom:914.523333pt;} .y46{bottom:914.526933pt;} .yd7{bottom:914.548533pt;} .y8cd{bottom:914.549200pt;} .y2ea{bottom:914.555733pt;} .y5aa{bottom:914.663600pt;} .y150{bottom:914.664533pt;} .y30e{bottom:914.699733pt;} .y2a4{bottom:914.787733pt;} .y326{bottom:914.843733pt;} .y8dd{bottom:915.237600pt;} .yf4d{bottom:915.366800pt;} .yf79{bottom:915.486800pt;} .yf98{bottom:915.570800pt;} .ydc4{bottom:915.968400pt;} .yc78{bottom:916.008267pt;} .yac8{bottom:916.871867pt;} .ydfd{bottom:916.888933pt;} .y57c{bottom:916.950667pt;} .y820{bottom:917.772133pt;} .ya11{bottom:918.062733pt;} .ya12{bottom:919.124400pt;} .ye25{bottom:919.671333pt;} .y8be{bottom:919.815067pt;} .ye4b{bottom:919.939600pt;} .y6{bottom:920.216667pt;} .y8bf{bottom:920.876733pt;} .ybf4{bottom:921.627067pt;} .yea2{bottom:921.829200pt;} .y444{bottom:922.141333pt;} .yee9{bottom:924.847765pt;} .yd39{bottom:926.679419pt;} .yd05{bottom:926.853333pt;} .y181{bottom:927.914667pt;} .yb68{bottom:928.516533pt;} .ycb4{bottom:929.252133pt;} .ybd8{bottom:929.457867pt;} .yb6c{bottom:929.961533pt;} .yf4c{bottom:930.030800pt;} .yf78{bottom:930.150800pt;} .yf97{bottom:930.234800pt;} .y110{bottom:930.519733pt;} .y45{bottom:930.523333pt;} .yd6{bottom:930.544933pt;} .y2e9{bottom:930.551733pt;} .y5a9{bottom:930.659600pt;} .y14f{bottom:930.660933pt;} .y30d{bottom:930.695733pt;} .y2a3{bottom:930.783733pt;} .y325{bottom:930.839733pt;} .yc3d{bottom:930.986933pt;} .y8dc{bottom:931.437600pt;} .ydfc{bottom:932.888933pt;} .yac7{bottom:933.071867pt;} .ycce{bottom:933.878933pt;} .y81f{bottom:933.972133pt;} .ycba{bottom:934.593733pt;} .yf34{bottom:935.611200pt;} .ye24{bottom:935.671333pt;} .yc94{bottom:935.832000pt;} .ye4a{bottom:935.939600pt;} .ya0f{bottom:936.391067pt;} .ycc0{bottom:936.984667pt;} .y443{bottom:937.021333pt;} .ya10{bottom:937.452733pt;} .yea1{bottom:937.829200pt;} .yd6c{bottom:937.899716pt;} .ycc6{bottom:938.199867pt;} .ycdf{bottom:939.553467pt;} .y8bc{bottom:939.811733pt;} .yee8{bottom:940.013461pt;} .y8bd{bottom:940.873400pt;} .ycd9{bottom:941.034533pt;} .yd38{bottom:942.314731pt;} .yddb{bottom:943.568667pt;} .yd04{bottom:944.189333pt;} .ya26{bottom:945.721067pt;} .y44{bottom:946.519733pt;} .yd5{bottom:946.541333pt;} .y2e8{bottom:946.547733pt;} .y5a8{bottom:946.655600pt;} .y14e{bottom:946.657333pt;} .y30c{bottom:946.691733pt;} .y2a2{bottom:946.779733pt;} .y324{bottom:946.835733pt;} .yc18{bottom:950.918400pt;} .ye23{bottom:951.671333pt;} .y442{bottom:951.901333pt;} .ye49{bottom:951.939600pt;} .yea0{bottom:953.829200pt;} .yc83{bottom:954.339867pt;} .y2{bottom:954.801067pt;} .yd6b{bottom:954.859100pt;} .yb67{bottom:955.178200pt;} .yee7{bottom:955.179157pt;} .ydc2{bottom:956.129200pt;} .yb6a{bottom:956.623200pt;} .yd37{bottom:957.950043pt;} .ydda{bottom:958.232667pt;} .ybf3{bottom:959.127067pt;} .yb6b{bottom:959.201533pt;} .ydcf{bottom:960.992667pt;} .y14{bottom:961.456000pt;} .ycb0{bottom:961.516800pt;} .yd03{bottom:961.525333pt;} .y81c{bottom:961.770933pt;} .y8ea{bottom:962.114533pt;} .y10f{bottom:962.519733pt;} .yd4{bottom:962.537733pt;} .y2e7{bottom:962.543733pt;} .y5a7{bottom:962.651600pt;} .y14d{bottom:962.653733pt;} .y30b{bottom:962.687733pt;} .y2a1{bottom:962.775733pt;} .y323{bottom:962.831733pt;} .yad2{bottom:963.748800pt;} .yfc9{bottom:964.038800pt;} .ycf0{bottom:964.946533pt;} .ycd5{bottom:965.166933pt;} .yc9c{bottom:965.495067pt;} .yf35{bottom:965.892533pt;} .y441{bottom:966.781333pt;} .ycca{bottom:968.043467pt;} .yc3c{bottom:968.486933pt;} .yc9d{bottom:968.937067pt;} .y430{bottom:969.715467pt;} .yee6{bottom:970.344853pt;} .ycdb{bottom:970.878133pt;} .yd6a{bottom:971.818483pt;} .ycc4{bottom:972.504933pt;} .ydd9{bottom:972.896667pt;} .yce1{bottom:972.968133pt;} .yc93{bottom:973.332000pt;} .yd36{bottom:973.585355pt;} .ybd7{bottom:974.570667pt;} .yec0{bottom:975.798533pt;} .y7{bottom:975.943333pt;} .yf47{bottom:976.673867pt;} .y585{bottom:977.738133pt;} .yd3{bottom:978.534133pt;} .y2e6{bottom:978.539733pt;} .y5a6{bottom:978.647600pt;} .y14c{bottom:978.650133pt;} .y30a{bottom:978.683733pt;} .y322{bottom:978.827733pt;} .yd02{bottom:978.861333pt;} .ycef{bottom:979.614533pt;} .ybd6{bottom:980.365600pt;} .ycb9{bottom:980.670800pt;} .y440{bottom:981.661333pt;} .yb66{bottom:981.839867pt;} .yb69{bottom:983.284867pt;} .ye22{bottom:984.398933pt;} .ye42{bottom:984.666933pt;} .yee5{bottom:985.510549pt;} .ydce{bottom:987.659333pt;} .yc17{bottom:988.418400pt;} .yd69{bottom:988.777867pt;} .y0{bottom:988.966267pt;} .yd35{bottom:989.220667pt;} .ya7c{bottom:989.474133pt;} .y8bb{bottom:990.949133pt;} .ycab{bottom:991.570800pt;} .yca3{bottom:991.609067pt;} .yca6{bottom:991.661333pt;} .yc82{bottom:991.839867pt;} .ycaf{bottom:993.783467pt;} .ycee{bottom:994.282533pt;} .y10e{bottom:994.519733pt;} .yd2{bottom:994.530533pt;} .y2e5{bottom:994.535733pt;} .y5a5{bottom:994.643600pt;} .y14b{bottom:994.646533pt;} .y309{bottom:994.679733pt;} .y2a0{bottom:994.779733pt;} .y321{bottom:994.823733pt;} .ydf8{bottom:995.241333pt;} .y8db{bottom:995.998400pt;} .yf44{bottom:996.032533pt;} .yd01{bottom:996.197333pt;} .y43f{bottom:996.541333pt;} .yf1c{bottom:996.858800pt;} .yf1b{bottom:996.858933pt;} .yf0e{bottom:996.912000pt;} .yf45{bottom:997.219867pt;} .yc9a{bottom:997.610667pt;} .yac6{bottom:997.632533pt;} .yb25{bottom:999.041467pt;} .y81d{bottom:999.746533pt;} .y81e{bottom:999.746667pt;} .yee4{bottom:1000.676245pt;} .y8ec{bottom:1000.943715pt;} .y9cf{bottom:1001.215467pt;} .yad3{bottom:1001.380800pt;} .y5{bottom:1001.567200pt;} .yf43{bottom:1001.636267pt;} .yebf{bottom:1002.465200pt;} .y9ad{bottom:1002.833582pt;} .yf46{bottom:1004.057600pt;} .ybf2{bottom:1004.127067pt;} .y81b{bottom:1005.831733pt;} .yd67{bottom:1006.277200pt;} .yb49{bottom:1006.289867pt;} .yd96{bottom:1006.830267pt;} .yf0c{bottom:1008.312338pt;} .yd68{bottom:1008.465200pt;} .y698{bottom:1009.158933pt;} .y625{bottom:1009.170800pt;} .yd30{bottom:1009.400000pt;} .ycd2{bottom:1010.064933pt;} .yb88{bottom:1010.107867pt;} .y774{bottom:1010.372267pt;} .y10d{bottom:1010.519733pt;} .y626{bottom:1010.523333pt;} .yd1{bottom:1010.526933pt;} .y2e4{bottom:1010.531733pt;} .y5a4{bottom:1010.639600pt;} .y14a{bottom:1010.642933pt;} .y308{bottom:1010.675733pt;} .y29f{bottom:1010.775733pt;} .ybd5{bottom:1010.819200pt;} .y320{bottom:1010.819733pt;} .y57b{bottom:1010.911067pt;} .ye21{bottom:1011.065600pt;} .ycc8{bottom:1011.307600pt;} .ye41{bottom:1011.333600pt;} .y43e{bottom:1011.421333pt;} .ya7a{bottom:1012.139524pt;} .ya7b{bottom:1012.140800pt;} .y82c{bottom:1012.283600pt;} .y93b{bottom:1012.552649pt;} .y431{bottom:1012.863867pt;} .yb64{bottom:1013.304400pt;} .y43{bottom:1013.391067pt;} .yc3b{bottom:1013.486933pt;} .yd00{bottom:1013.533333pt;} .ya30{bottom:1013.615657pt;} .ycda{bottom:1014.142267pt;} .yb65{bottom:1014.761067pt;} .yceb{bottom:1015.022400pt;} .yda8{bottom:1015.127067pt;} .yee3{bottom:1015.841941pt;} .yce0{bottom:1016.142933pt;} .ycc2{bottom:1016.194800pt;} .yc92{bottom:1018.332000pt;} .ydcd{bottom:1019.659333pt;} .y8ba{bottom:1020.274133pt;} .ycf5{bottom:1020.821067pt;} .yca5{bottom:1021.232667pt;} .yc9b{bottom:1022.024667pt;} .yca0{bottom:1022.428533pt;} .y881{bottom:1024.080115pt;} .y8eb{bottom:1024.945067pt;} .y9ce{bottom:1025.215467pt;} .yb26{bottom:1025.889867pt;} .y43d{bottom:1026.301333pt;} .yd0{bottom:1026.523333pt;} .y2e3{bottom:1026.527733pt;} .y5a3{bottom:1026.635600pt;} .y149{bottom:1026.639333pt;} .y307{bottom:1026.671733pt;} .y29e{bottom:1026.771733pt;} .y31f{bottom:1026.815733pt;} .y9ac{bottom:1026.834933pt;} .yb0a{bottom:1028.193333pt;} .y81a{bottom:1028.325067pt;} .y624{bottom:1028.784133pt;} .yb48{bottom:1028.956533pt;} .yad5{bottom:1029.765733pt;} .yee2{bottom:1031.007637pt;} .y697{bottom:1031.785600pt;} .yd97{bottom:1032.459600pt;} .ycae{bottom:1032.503467pt;} .yc16{bottom:1033.418400pt;} .ydb7{bottom:1033.998533pt;} .yebe{bottom:1034.465200pt;} .ya79{bottom:1034.807467pt;} .y82b{bottom:1036.283600pt;} .y93a{bottom:1036.554000pt;} .yc81{bottom:1036.839867pt;} .y25f{bottom:1038.499733pt;} .y43c{bottom:1041.181333pt;} .ycf{bottom:1042.519733pt;} .y2e2{bottom:1042.523733pt;} .y5a2{bottom:1042.631600pt;} .y148{bottom:1042.635733pt;} .y306{bottom:1042.667733pt;} .y29d{bottom:1042.767733pt;} .y31e{bottom:1042.811733pt;} .ye20{bottom:1043.065600pt;} .ye40{bottom:1043.333600pt;} .ye8d{bottom:1043.341600pt;} .y13{bottom:1044.316800pt;} .yee0{bottom:1046.173333pt;} .y3d9{bottom:1046.749467pt;} .yee1{bottom:1047.559567pt;} .y880{bottom:1048.081467pt;} .ycad{bottom:1048.382667pt;} .y819{bottom:1049.738400pt;} .y1{bottom:1050.366400pt;} .ycff{bottom:1051.264267pt;} .y25e{bottom:1053.030800pt;} .ybf5{bottom:1055.983200pt;} .y2e1{bottom:1058.519733pt;} .y305{bottom:1058.663733pt;} .y29c{bottom:1058.763733pt;} .y31d{bottom:1058.807733pt;} .yd93{bottom:1058.819467pt;} .ycfe{bottom:1059.349733pt;} .ydcb{bottom:1059.364267pt;} .ycb6{bottom:1059.537733pt;} .yce8{bottom:1060.239333pt;} .yd2e{bottom:1062.939200pt;} .ycb7{bottom:1064.997733pt;} .y25d{bottom:1065.030800pt;} .ycfd{bottom:1066.395200pt;} .ycea{bottom:1066.576800pt;} .ycb8{bottom:1067.351200pt;} .yd2f{bottom:1067.594533pt;} .ydcc{bottom:1069.420933pt;} .yedf{bottom:1075.896933pt;} .yccc{bottom:1080.781600pt;} .ycd0{bottom:1081.726533pt;} .ycfc{bottom:1082.391200pt;} .yccd{bottom:1082.480267pt;} .yce9{bottom:1082.572800pt;} .ycd1{bottom:1083.425200pt;} .y704{bottom:1086.904400pt;} .y34a{bottom:1086.911333pt;} .y22e{bottom:1087.856400pt;} .ye6c{bottom:1087.856800pt;} .ye3f{bottom:1087.863333pt;} .ycbf{bottom:1089.555067pt;} .y4{bottom:1103.116533pt;} .y3{bottom:1113.783200pt;} .y10{bottom:1115.729067pt;} .h4{height:22.041877pt;} .h9{height:23.054667pt;} .h6f{height:23.777596pt;} .h1d{height:26.323087pt;} .h68{height:26.704581pt;} .h1c{height:27.251622pt;} .h79{height:27.386830pt;} .h20{height:27.933840pt;} .h14{height:29.303463pt;} .h40{height:29.777728pt;} .h50{height:29.879215pt;} .h2d{height:30.083528pt;} .h47{height:30.537522pt;} .h82{height:31.381257pt;} .h32{height:31.963749pt;} .h13{height:32.435283pt;} .h11{height:32.715837pt;} .h33{height:33.091881pt;} .h3b{height:33.716805pt;} .h19{height:33.843969pt;} .h2e{height:34.031689pt;} .h7{height:34.060559pt;} .h3f{height:34.422770pt;} .h51{height:35.502240pt;} .h43{height:35.589961pt;} .h1e{height:35.914937pt;} .h4f{height:36.102656pt;} .h42{height:36.937509pt;} .h8{height:37.463116pt;} .h8b{height:37.497532pt;} .h38{height:37.931405pt;} .h8d{height:38.046042pt;} .h7a{height:38.153439pt;} .h53{height:38.972944pt;} .h30{height:39.340309pt;} .h7b{height:39.384716pt;} .h73{height:39.577535pt;} .h6e{height:39.724081pt;} .h12{height:39.905485pt;} .h41{height:40.460166pt;} .h18{height:40.595808pt;} .h6d{height:41.209428pt;} .h77{height:41.512201pt;} .h8c{height:42.801610pt;} .h28{height:42.850458pt;} .h8e{height:42.922616pt;} .h2c{height:43.768869pt;} .h7c{height:43.896034pt;} .h4b{height:45.128320pt;} .h44{height:45.310201pt;} .h3{height:45.413859pt;} .h39{height:45.517686pt;} .he{height:45.518810pt;} .h78{height:45.891308pt;} .h1a{height:45.948835pt;} .h3a{height:46.228795pt;} .h4e{height:47.261659pt;} .h17{height:47.886583pt;} .h7e{height:48.008294pt;} .h83{height:49.230895pt;} .h58{height:50.048476pt;} .h67{height:50.791520pt;} .hd{height:50.914591pt;} .ha{height:51.176008pt;} .h1b{height:51.877131pt;} .h63{height:52.448363pt;} .h64{height:53.409163pt;} .h35{height:54.713008pt;} .h3c{height:54.928679pt;} .h89{height:55.596770pt;} .h1f{height:55.867680pt;} .h6a{height:56.194674pt;} .h46{height:57.340864pt;} .h6{height:58.459417pt;} .h85{height:58.495750pt;} .h54{height:59.077074pt;} .h81{height:59.814634pt;} .h21{height:59.858228pt;} .h5c{height:61.196001pt;} .h7d{height:62.268301pt;} .h52{height:64.954907pt;} .hb{height:66.677667pt;} .h5e{height:67.995556pt;} .hf{height:68.693509pt;} .h55{height:69.231110pt;} .h3e{height:69.743768pt;} .h66{height:71.212217pt;} .h27{height:72.084203pt;} .h87{height:72.205312pt;} .h74{height:73.420775pt;} .h69{height:75.487372pt;} .h25{height:76.140554pt;} .h45{height:77.579029pt;} .h86{height:77.994333pt;} .h15{height:78.723945pt;} .h62{height:78.769432pt;} .h26{height:80.093559pt;} .h84{height:81.894049pt;} .h2a{height:82.160490pt;} .h5a{height:82.205748pt;} .h57{height:82.259843pt;} .h4a{height:82.868978pt;} .h72{height:85.106761pt;} .h71{height:85.333551pt;} .h6b{height:89.693483pt;} .h5f{height:91.339720pt;} .h3d{height:94.359215pt;} .h2{height:97.735142pt;} .h65{height:103.851149pt;} .h56{height:106.154281pt;} .h61{height:106.264947pt;} .h60{height:106.282609pt;} .h16{height:107.744811pt;} .h31{height:111.735359pt;} .h24{height:112.195574pt;} .h8a{height:113.174533pt;} .h88{height:113.174667pt;} .h48{height:119.631074pt;} .h34{height:123.707005pt;} .h59{height:126.131655pt;} .h2b{height:127.810952pt;} .h80{height:131.594182pt;} .h76{height:132.923416pt;} .h22{height:134.634689pt;} .h70{height:134.919893pt;} .h4d{height:135.967799pt;} .h37{height:137.354196pt;} .h2f{height:137.673925pt;} .h29{height:142.662110pt;} .h10{height:147.692684pt;} .h6c{height:155.183657pt;} .h4c{height:158.217075pt;} .h36{height:159.508099pt;} .h5d{height:164.102983pt;} .h7f{height:171.170898pt;} .h75{height:178.192536pt;} .h5b{height:180.213350pt;} .h49{height:189.526228pt;} .h5{height:222.666414pt;} .hc{height:234.520885pt;} .h23{height:293.684995pt;} .h1{height:296.888552pt;} .h0{height:1122.520000pt;} .w2{width:159.182667pt;} .w4{width:307.625333pt;} .w1{width:463.416000pt;} .w3{width:793.700000pt;} .w0{width:793.701333pt;} .x7{left:-793.700800pt;} .xe1{left:-230.551200pt;} .x3{left:-0.000133pt;} .x9{left:6.848533pt;} .xb{left:10.240400pt;} .x53{left:30.236267pt;} .x26{left:32.292000pt;} .x9f{left:33.544533pt;} .x3a{left:34.589067pt;} .x17{left:35.905467pt;} .x0{left:37.795200pt;} .x6{left:39.685067pt;} .x66{left:41.097600pt;} .xcb{left:42.217600pt;} .x2{left:43.464533pt;} .x69{left:44.932800pt;} .x50{left:46.022800pt;} .x22{left:48.000000pt;} .x7c{left:49.528400pt;} .x4{left:51.121467pt;} .x54{left:52.168933pt;} .x25{left:54.173200pt;} .x5{left:55.373467pt;} .x42{left:57.643200pt;} .x52{left:59.783733pt;} .x64{left:60.917600pt;} .x6b{left:62.714133pt;} .xa6{left:64.074267pt;} .x1c{left:65.763733pt;} .x38{left:68.419867pt;} .x90{left:69.933600pt;} .xbb{left:74.656933pt;} .x97{left:77.480267pt;} .xb0{left:78.806000pt;} .x9b{left:80.126000pt;} .x21{left:83.073067pt;} .x37{left:86.499867pt;} .xe4{left:87.685067pt;} .x71{left:97.537333pt;} .x98{left:102.047200pt;} .xb9{left:104.357733pt;} .xa5{left:120.991467pt;} .xc2{left:122.730800pt;} .xa4{left:124.961733pt;} .xc7{left:126.540667pt;} .xc4{left:128.384933pt;} .x6f{left:131.276533pt;} .x9d{left:133.543333pt;} .xc3{left:137.250400pt;} .xc8{left:141.060267pt;} .xc5{left:142.904533pt;} .x2f{left:150.748400pt;} .x30{left:155.596933pt;} .x31{left:162.094133pt;} .xa7{left:163.195333pt;} .xe3{left:173.281333pt;} .xd6{left:180.569174pt;} .x5d{left:182.915867pt;} .xa8{left:184.555333pt;} .xd7{left:185.898912pt;} .x7d{left:188.534400pt;} .x9e{left:191.540942pt;} .x7e{left:194.122733pt;} .x81{left:200.102400pt;} .x56{left:202.651200pt;} .xc0{left:203.926533pt;} .x57{left:206.935200pt;} .xae{left:213.770133pt;} .xd3{left:220.075333pt;} .x8a{left:224.239400pt;} .x85{left:225.511867pt;} .x76{left:227.129467pt;} .x8b{left:229.827733pt;} .xc1{left:234.790800pt;} .x6a{left:236.528667pt;} .x7f{left:238.771067pt;} .x8f{left:241.264800pt;} .x80{left:244.359400pt;} .xd1{left:253.579333pt;} .x6c{left:256.462467pt;} .xbd{left:257.952800pt;} .xd2{left:259.327333pt;} .x6d{left:262.050800pt;} .x46{left:264.566933pt;} .x1e{left:267.086667pt;} .x8c{left:273.566067pt;} .x68{left:274.617600pt;} .x75{left:276.970000pt;} .x18{left:282.207200pt;} .x29{left:283.459333pt;} .x67{left:285.501600pt;} .xcc{left:286.558933pt;} .x59{left:287.783067pt;} .x5a{left:293.371400pt;} .x73{left:296.602933pt;} .xe8{left:298.646667pt;} .x79{left:301.823467pt;} .x65{left:302.921467pt;} .x5b{left:305.901400pt;} .x78{left:309.807067pt;} .x5c{left:311.489733pt;} .xd4{left:316.411333pt;} .x96{left:318.630000pt;} .x77{left:319.947600pt;} .xd0{left:326.140533pt;} .x8{left:330.285333pt;} .x32{left:333.546667pt;} .xb5{left:336.377867pt;} .xda{left:340.769333pt;} .xdc{left:357.997333pt;} .x33{left:367.493333pt;} .x2d{left:370.098800pt;} .xba{left:373.555333pt;} .xd{left:375.046800pt;} .xa1{left:377.952980pt;} .xc{left:385.133467pt;} .x16{left:387.000613pt;} .x15{left:388.144787pt;} .x13{left:390.293600pt;} .x14{left:391.577307pt;} .xdb{left:392.721333pt;} .x3e{left:397.574800pt;} .x3c{left:398.995200pt;} .xce{left:401.889733pt;} .x3d{left:404.875200pt;} .x61{left:406.929067pt;} .xd8{left:410.393733pt;} .xb7{left:413.376133pt;} .x34{left:414.560000pt;} .xb6{left:417.005467pt;} .xe9{left:418.658800pt;} .x7b{left:422.892400pt;} .x63{left:426.852800pt;} .x99{left:432.756000pt;} .x6e{left:434.641333pt;} .xbf{left:446.316800pt;} .x55{left:450.787333pt;} .xe2{left:453.288800pt;} .x23{left:454.803200pt;} .xe5{left:455.922400pt;} .xe{left:457.498000pt;} .x83{left:459.336533pt;} .x82{left:461.508982pt;} .xe6{left:469.112000pt;} .x91{left:470.591200pt;} .x94{left:474.228267pt;} .x5e{left:476.416667pt;} .xe7{left:483.776400pt;} .xb2{left:489.417867pt;} .x3f{left:493.207867pt;} .x87{left:496.515600pt;} .x86{left:498.271867pt;} .xf{left:500.313880pt;} .xa3{left:502.442267pt;} .x84{left:504.493867pt;} .x10{left:507.698068pt;} .x27{left:509.446400pt;} .x19{left:511.496000pt;} .x93{left:513.402933pt;} .x36{left:516.685067pt;} .xb8{left:518.662133pt;} .x5f{left:520.048667pt;} .x1a{left:526.616667pt;} .x39{left:529.123200pt;} .xcd{left:530.900267pt;} .x89{left:539.854533pt;} .x7a{left:541.663271pt;} .xbe{left:544.992667pt;} .x35{left:547.069067pt;} .x11{left:553.616548pt;} .x12{left:562.324512pt;} .x44{left:564.910667pt;} .xa0{left:571.361467pt;} .x92{left:577.693333pt;} .x4f{left:578.909333pt;} .xb3{left:585.457867pt;} .x4d{left:586.492933pt;} .xa2{left:587.944935pt;} .x8d{left:589.061867pt;} .xa9{left:590.895067pt;} .x4b{left:599.073733pt;} .xac{left:600.869600pt;} .xa{left:604.281333pt;} .xcf{left:606.174000pt;} .x43{left:607.324000pt;} .xbc{left:610.780933pt;} .x8e{left:612.289067pt;} .x24{left:615.427200pt;} .xab{left:616.901600pt;} .x74{left:618.702133pt;} .x48{left:621.581333pt;} .x62{left:624.982400pt;} .x58{left:626.035200pt;} .xaf{left:634.583600pt;} .xb4{left:635.670267pt;} .x88{left:638.348667pt;} .x4c{left:645.226267pt;} .x4e{left:646.469333pt;} .x70{left:648.567733pt;} .x4a{left:651.193733pt;} .xde{left:652.798133pt;} .x49{left:654.803067pt;} .xc9{left:660.314400pt;} .x2c{left:662.059200pt;} .x45{left:664.317067pt;} .x47{left:665.568000pt;} .xd9{left:668.655333pt;} .x1f{left:672.000000pt;} .x60{left:674.848667pt;} .x51{left:678.713200pt;} .x1{left:681.173867pt;} .xd5{left:683.149600pt;} .xe0{left:685.246994pt;} .x72{left:686.295733pt;} .x95{left:691.370133pt;} .xc6{left:693.382133pt;} .x2e{left:700.135867pt;} .x9c{left:702.933733pt;} .x1d{left:704.871200pt;} .x9a{left:709.311867pt;} .xaa{left:713.282267pt;} .xb1{left:715.009733pt;} .x40{left:717.406933pt;} .xad{left:718.526533pt;} .xca{left:723.085333pt;} .xdf{left:741.725067pt;} .xdd{left:743.346400pt;} .x41{left:745.398800pt;} .x3b{left:746.988000pt;} .x2b{left:748.815333pt;} .x20{left:750.533200pt;} .x1b{left:755.905467pt;} .x28{left:768.354933pt;} .x2a{left:769.400267pt;} }- 983668.jpg
- 983669.jpg
- 983670.jpg
- 983671.jpg
- 983672.jpg
- 983673.jpg
- 983674.jpg
- 983675.jpg
- 983676.jpg
- 983677.jpg
- 983678.jpg
- 983679.jpg
- 983680.jpg
- 983681.jpg
- 983682.jpg
- 983683.jpg
- 983684.jpg
- 983685.jpg
- 983687.jpg
- 983688.jpg
- 983689.jpg
- 983691.jpg
- 983692.jpg
- 983696.jpg
- 983700.jpg
- 983701.jpg
- 983702.jpg
- 983703.jpg
- 983704.jpg
- 983705.jpg
- 983706.jpg
- 983707.jpg
- 983708.jpg
- 983709.jpg
- 983710.jpg
- 983711.jpg
- 983712.png
- 983713.png
- 983714.png
- 983715.png
- 983716.png
- 983717.png
- 983718.png
- 983719.png
- 983720.png
- 983721.png
- 983722.png
- 983723.png
- 983724.png
- 983725.png
- 983726.png
- 983727.png
- 983728.png
- 983729.png
- 983730.png
- 983731.png
- 983732.png
- 983733.png
- 983734.png
- 983735.png
- 983736.png
- 983737.png
- 983738.png
- 983739.png
- 983740.png
- 983741.png
- 983742.png
- 983743.png
- 983744.png
- 983745.png
- 983746.png
- 983747.png
- 983748.png
- 983749.png
- 986687.pdf
-
Issue title
Issue title
Issue date
Issue description
Search results
Item title
Item description
Item product details
Rok 2021
Rok 2020
Rok 2019
Rok 2018
Rok 2017
Rok 2016
Rok 2015
Rok 2014
Rok 2013
Rok 2012
Rok 2011
Rok 2010
Rok 2022
Pracovní manuály
Work manual
Year 2022
Year 2021
Year 2020
Year 2019
Year 2018
Year 2017
Year 2016
Year 2015
Year 2014
Year 2012
Year 2013
Year 2011
Year 2010
Úvodník
Dobrý den, vážení přátelé, po únorové premiéře a březnovém pokračování P-40E Warhawk je v dubnu čas na patrně nejvýznamnější protivníky Warhawků, japonská Zera. Poslední premiéru příslušníka rodiny Zer, plovákového Rufe, jsme měli přesně přede dvěma lety, v dubnu 2023. Dva roky nabízejí dostatek času si od Zer trochu odpočinout a dostat chuť na nové přírůstky.
Editorial
Good day, Dear Friends After the February premiere and the March sequel of the P-40E, it's time for what was probably the most significant foe of the Warhawks, the Japanese Zero. The last new release of a member of the Zero family, the Rufe float version, was exactly two years ago, in April 2023.
KAMIKAZE TOKKŌTAI
One of the most well-known words from the field of aviation, recognized even by those with no interest in the subject, is kamikaze. It is associated with the predominantly aerial campaign that began in October 1944 and lasted until the end of the war in the Pacific. During this period, hundreds of airmen sacrificed their lives in service of the Japanese Empire.
KAMIKAZE TOKKŌTAI
Jedním ze slov, která zná z oboru letectví doslova každý, aniž by se o něj alespoň okrajově zajímal, je výraz „kamikaze“. Je spojen s převážně leteckou kampaní, která začala v říjnu 1944 a trvala v podstatě až do konce války v Pacifiku. Stovky letců během ní obětovali své životy ve jménu japonského císařství.
Dekelia Greek Air Force Museum
The Hellenic Air Force Museum is a relatively young institution, having existed in its current form since 1986. However, it certainly has a lot to build on, as its aviation collections were previously part of the Hellenic War Museum. The museum is organisationally under the Hellenic Air Force (HAF) administration and its mission is not only historical research, collection, preservation and access to exhibits, but also the retrieval, conservation and restoration of artefacts related to Greek aviation history.
Muzeum řeckých vzdušných sil Dekelia
Muzeum řeckých vzdušných sil (The Hellenic Air Force Museum) je poměrně mladá instituce, v současné podobě existuje od roku 1986. Rozhodně však má na co navazovat, protože letecké sbírky byly předtím součástí řeckého Válečného muzea. Muzeum organizačně spadá pod velení vojenského letectva (Hellenic Air Force – HAF) a jeho úkolem je nejen historický výzkum, shromažďování, uchování a zpřístupňování exponátů, ale také vyhledávání, vyzvedávání, konzervace a restaurace artefaktů souvisejících s řeckou leteckou historií.
Aerial War in Ukraine - The First Mirage 2000s Have Arrived
The full-scale Russian invasion of Ukraine began three years ago, on February 24, 2022. This continuation of the series does not only cover the most recent period from February 1, 2025, to February 28, 2025, but also recaps events from the past year. However, we will start with the most significant updates—developments on the global political scene.
Letecká vojna na Ukrajine - Prišli prvé Mirage 2000
Plná ruská invázia na Ukrajinu sa začala pred tromi rokmi, 24. februára 2022. Toto pokračovanie seriálu sa tak nezaoberá len posledným obdobím od 1. 2. 2025 do 28. 2. 2025, ale rekapituluje aj udalosti za posledný rok. Začneme ale najväčšími aktualitami – a tými je dianie na svetovej politickej scéne.
Červencové Stirlingy
Když byla v létě 1941 denní letecká ofenzíva RAF nad okupovaným evropským pobřežím na svém vrcholu, britské velení již vědělo, že tato strategie přináší vlastní vysoké ztráty, které jsou výrazně vyšší, než ztráty Luftwaffe. RAF se pokoušelo své protivníky zapojit do boje především v rámci operací Sweep a Circus. Zatímco v prvním případě šlo o nasazení pouze stíhacích perutí, v případě Circusu se jednalo o rozsáhlý stíhací doprovod pro malou skupinu Blenheimů. V doletu těchto formací však bylo velmi málo cílů se strategickou hodnotou pro německé okupanty.
Like a Painting on Canvas
Market Garden was the largest Allied airborne operation of World War II, launched on 17 September 1944 in the Netherlands. Its objective was to use paratroopers (the "Market" component) and the rapid advance of ground forces (the "Garden" component) to seize key bridges over rivers and canals, thereby creating a corridor for an attack into Germany. However, the operation ultimately failed due to strong German resistance, poor coordination, and delays in the Allied advance, particularly at Arnhem, where British paratroopers were unable to hold a crucial bridge.
Tail End Charlie - Almost an April problem
It's not entirely my fault that I’m writing my Tail End Charlie text at the last-minute again. I scheduled my work quite responsibly yesterday, Sunday, two days before the current issue was due out. However, somehow I didn't keep up at the end of the day. Understandably, I could blame my slow work, my tendency to run away from responsibilities, orstimuli that release the right hormones into my brain for the wrong mood, and a thousand other things rooted solely in my nature, irresponsibility, and laziness. But this time it's different my friends.
Tail End Charlie - Téměř aprílový problém
Za to, že opět píši svůj příspěvek do Tail End Charlie na poslední chvíli, nemůžu až tak moc já. Práci jsem si včera, tedy v neděli, ještě dva dny před vydáním aktuálního čísla, rozdělil vcelku zodpovědně. Ovšem nějak jsem na konci dne nestíhal. Pochopitelně, mohl bych to přičítat své pomalé práci, tendenci utíkat od povinností k věcem, které mi do mozku propouštějí ty správnější hormony pro správnější nálady a tisíci dalších věcí, tkvících jen a pouze v mé povaze, nezodpovědnosti a lenosti. Je to ale jinak, přátelé. Sebrali mi z toho včerejšího dne hodinu.
Flying Knights in Australia
Flying Knights v Austrálii
P-40E Warhawk
The Curtiss P-40 line of fighter aircraft stood out among American fighter types for having remained in front-line operations from the summer of 1941, before the U.S. entered World War II, through the end of the conflict four years later. Only Grumman’s versatile F4F Wildcat naval fighter could match that record.
Ace in a Single Dogfight
During World War II, legendary Spitfire fighter planes were flown by pilots of many nationalities. Many of them fought and achieved victories, some became flying aces during the war, a few even earned this status in a single day. However, only one pilot flying a Spitfire managed to shoot down five aircraft in a single dogfight. That pilot was Canadian F/Lt Richard Joseph "Dick" Audet.
Esem během jediného souboje
S legendárními stíhacími letouny Spitfire v průběhu 2. světové války bojovali a vítězili letci mnoha národností. Řada z nich se během válečných let stala leteckými esy, někteří z nich tohoto statusu docílilo během jednoho dne. Avšak na letounech Spitfire jen jeden pilot dokázal sestřelit pět letadel během jednoho souboje. Byl jím kanadský pilot F/Lt Richard Joseph „Dick“ Audet.
04/2025
INFO Eduard je modelářsko-historický měsíčník, který od roku 2010 v českém a anglickém jazyce publikuje společnost Eduard Model Accessories. Magazín je dostupný zdarma na platformě Triobo a je možné jej stáhnout také v PDF verzi. Společnost Eduard je výrobcem plastikových modelů a doplňků s více než 30letou tradicí. Během svého působení v oboru plastikového modelářství se společnost Eduard zařadila mezi jeho světové lídry. Další podrobnosti o společnosti a jejím sortimentu najdete na www.eduard.com. Zde se můžete mimo jiné zdarma přihlásit k odebírání magazínu INFO a produktových informací: https://www.eduard.com/cs/info-eduard/
04/2025
INFO Eduard is a monthly scale model-historical magazine published in Czech and English by Eduard Model Accessories since 2010. The magazine is available for free on the Triobo platform and can be downloaded in PDF format. Eduard is a manufacturer of plastic models and accessories with over 30 years of tradition. Throughout its history in the plastic modeling industry, Eduard has become one of the world's leaders. Further details about the company and its product range can be found at www.eduard.com. You can subscribe to the INFO magazine and receive product information for free at: https://www.eduard.com/cs/info-eduard/
03/2025
INFO Eduard je modelářsko-historický měsíčník, který od roku 2010 v českém a anglickém jazyce publikuje společnost Eduard Model Accessories. Magazín je dostupný zdarma na platformě Triobo a je možné jej stáhnout také v PDF verzi. Společnost Eduard je výrobcem plastikových modelů a doplňků s více než 30letou tradicí. Během svého působení v oboru plastikového modelářství se společnost Eduard zařadila mezi jeho světové lídry. Další podrobnosti o společnosti a jejím sortimentu najdete na www.eduard.com. Zde se můžete mimo jiné zdarma přihlásit k odebírání magazínu INFO a produktových informací: https://www.eduard.com/cs/info-eduard/
03/2025
INFO Eduard is a monthly scale model-historical magazine published in Czech and English by Eduard Model Accessories since 2010. The magazine is available for free on the Triobo platform and can be downloaded in PDF format. Eduard is a manufacturer of plastic models and accessories with over 30 years of tradition. Throughout its history in the plastic modeling industry, Eduard has become one of the world's leaders. Further details about the company and its product range can be found at www.eduard.com. You can subscribe to the INFO magazine and receive product information for free at: https://www.eduard.com/cs/info-eduard/
02/2025
INFO Eduard je modelářsko-historický měsíčník, který od roku 2010 v českém a anglickém jazyce publikuje společnost Eduard Model Accessories. Magazín je dostupný zdarma na platformě Triobo a je možné jej stáhnout také v PDF verzi. Společnost Eduard je výrobcem plastikových modelů a doplňků s více než 30letou tradicí. Během svého působení v oboru plastikového modelářství se společnost Eduard zařadila mezi jeho světové lídry. Další podrobnosti o společnosti a jejím sortimentu najdete na www.eduard.com. Zde se můžete mimo jiné zdarma přihlásit k odebírání magazínu INFO a produktových informací: https://www.eduard.com/cs/info-eduard/
02/2025
INFO Eduard is a monthly scale model-historical magazine published in Czech and English by Eduard Model Accessories since 2010. The magazine is available for free on the Triobo platform and can be downloaded in PDF format. Eduard is a manufacturer of plastic models and accessories with over 30 years of tradition. Throughout its history in the plastic modeling industry, Eduard has become one of the world's leaders. Further details about the company and its product range can be found at www.eduard.com. You can subscribe to the INFO magazine and receive product information for free at: https://www.eduard.com/cs/info-eduard/
01/2025
INFO Eduard je modelářsko-historický měsíčník, který od roku 2010 v českém a anglickém jazyce publikuje společnost Eduard Model Accessories. Magazín je dostupný zdarma na platformě Triobo a je možné jej stáhnout také v PDF verzi. Společnost Eduard je výrobcem plastikových modelů a doplňků s více než 30letou tradicí. Během svého působení v oboru plastikového modelářství se společnost Eduard zařadila mezi jeho světové lídry. Další podrobnosti o společnosti a jejím sortimentu najdete na www.eduard.com. Zde se můžete mimo jiné zdarma přihlásit k odebírání magazínu INFO a produktových informací: https://www.eduard.com/cs/info-eduard/
01/2025
INFO Eduard is a monthly scale model-historical magazine published in Czech and English by Eduard Model Accessories since 2010. The magazine is available for free on the Triobo platform and can be downloaded in PDF format. Eduard is a manufacturer of plastic models and accessories with over 30 years of tradition. Throughout its history in the plastic modeling industry, Eduard has become one of the world's leaders. Further details about the company and its product range can be found at www.eduard.com. You can subscribe to the INFO magazine and receive product information for free at: https://www.eduard.com/cs/info-eduard/
12/2024
INFO Eduard je modelářsko-historický měsíčník, který od roku 2010 v českém a anglickém jazyce publikuje společnost Eduard Model Accessories. Magazín je dostupný zdarma na platformě Triobo a je možné jej stáhnout také v PDF verzi. Společnost Eduard je výrobcem plastikových modelů a doplňků s více než 30letou tradicí. Během svého působení v oboru plastikového modelářství se společnost Eduard zařadila mezi jeho světové lídry. Další podrobnosti o společnosti a jejím sortimentu najdete na www.eduard.com. Zde se můžete mimo jiné zdarma přihlásit k odebírání magazínu INFO a produktových informací: https://www.eduard.com/cs/info-eduard/
12/2024
INFO Eduard is a monthly scale model-historical magazine published in Czech and English by Eduard Model Accessories since 2010. The magazine is available for free on the Triobo platform and can be downloaded in PDF format. Eduard is a manufacturer of plastic models and accessories with over 30 years of tradition. Throughout its history in the plastic modeling industry, Eduard has become one of the world's leaders. Further details about the company and its product range can be found at www.eduard.com. You can subscribe to the INFO magazine and receive product information for free at: https://www.eduard.com/cs/info-eduard/
11/2024
INFO Eduard je modelářsko-historický měsíčník, který od roku 2010 v českém a anglickém jazyce publikuje společnost Eduard Model Accessories. Magazín je dostupný zdarma na platformě Triobo a je možné jej stáhnout také v PDF verzi. Společnost Eduard je výrobcem plastikových modelů a doplňků s více než 30letou tradicí. Během svého působení v oboru plastikového modelářství se společnost Eduard zařadila mezi jeho světové lídry. Další podrobnosti o společnosti a jejím sortimentu najdete na www.eduard.com. Zde se můžete mimo jiné zdarma přihlásit k odebírání magazínu INFO a produktových informací: https://www.eduard.com/cs/info-eduard/
11/2024
INFO Eduard is a monthly scale model-historical magazine published in Czech and English by Eduard Model Accessories since 2010. The magazine is available for free on the Triobo platform and can be downloaded in PDF format. Eduard is a manufacturer of plastic models and accessories with over 30 years of tradition. Throughout its history in the plastic modeling industry, Eduard has become one of the world's leaders. Further details about the company and its product range can be found at www.eduard.com. You can subscribe to the INFO magazine and receive product information for free at: https://www.eduard.com/cs/info-eduard/
10/2024
10/2024
10/2024
INFO Eduard je modelářsko-historický měsíčník, který od roku 2010 v českém a anglickém jazyce publikuje společnost Eduard Model Accessories. Magazín je dostupný zdarma na platformě Triobo a je možné jej stáhnout také v PDF verzi. Společnost Eduard je výrobcem plastikových modelů a doplňků s více než 30letou tradicí. Během svého působení v oboru plastikového modelářství se společnost Eduard zařadila mezi jeho světové lídry. Další podrobnosti o společnosti a jejím sortimentu najdete na www.eduard.com. Zde se můžete mimo jiné zdarma přihlásit k odebírání magazínu INFO a produktových informací: https://www.eduard.com/cs/info-eduard/
10/2024
INFO Eduard is a monthly scale model-historical magazine published in Czech and English by Eduard Model Accessories since 2010. The magazine is available for free on the Triobo platform and can be downloaded in PDF format. Eduard is a manufacturer of plastic models and accessories with over 30 years of tradition. Throughout its history in the plastic modeling industry, Eduard has become one of the world's leaders. Further details about the company and its product range can be found at www.eduard.com. You can subscribe to the INFO magazine and receive product information for free at: https://www.eduard.com/cs/info-eduard/
09_Special E-Day/2024
Vážení přátelé, modeláři, hosté a návštěvníci E-daye, V dnešním krátkém mimořádném vydání Infa vás seznámíme s plánovaným programem letošního E-daye, který se koná v sobotu 28. září 2024 v hale muzea na Tankodromu Milovice. Výstava je jednodenní, ale jako obvykle bude výstavní hala otevřena, nejen pro vystavující modeláře, již v pátek od 17:00. Na pátek máme připravený malý program pro všechny časné příchozí. Tento podvečerní program má dva body. Prvním bude představení novinek Eduardu na rok 2025, které se bude opakovat i v sobotu. Druhým bodem bude beseda s Jiřím Šilhánkem, zakladatelem a majitelem firmy Special Hobby. Jiří je velká osobnost našeho oboru, který své podnikání rozjížděl dávno před všemi ostatními českými firmami, hluboko v osmdesátých letech. Jeho historky z dějin plastikového modelářství jsou neuvěřitelné a všem doporučuji si je poslechnout. Věřte mi, že to stojí za páteční cestu do Milovic!
09/2024
INFO Eduard je modelářsko-historický měsíčník, který od roku 2010 v českém a anglickém jazyce publikuje společnost Eduard Model Accessories. Magazín je dostupný zdarma na platformě Triobo a je možné jej stáhnout také v PDF verzi. Společnost Eduard je výrobcem plastikových modelů a doplňků s více než 30letou tradicí. Během svého působení v oboru plastikového modelářství se společnost Eduard zařadila mezi jeho světové lídry. Další podrobnosti o společnosti a jejím sortimentu najdete na www.eduard.com. Zde se můžete mimo jiné zdarma přihlásit k odebírání magazínu INFO a produktových informací: https://www.eduard.com/cs/info-eduard/
09/2024
INFO Eduard is a monthly scale model-historical magazine published in Czech and English by Eduard Model Accessories since 2010. The magazine is available for free on the Triobo platform and can be downloaded in PDF format. Eduard is a manufacturer of plastic models and accessories with over 30 years of tradition. Throughout its history in the plastic modeling industry, Eduard has become one of the world's leaders. Further details about the company and its product range can be found at www.eduard.com. You can subscribe to the INFO magazine and receive product information for free at: https://www.eduard.com/cs/info-eduard/
08/2024
INFO Eduard je modelářsko-historický měsíčník, který od roku 2010 v českém a anglickém jazyce publikuje společnost Eduard Model Accessories. Magazín je dostupný zdarma na platformě Triobo a je možné jej stáhnout také v PDF verzi. Společnost Eduard je výrobcem plastikových modelů a doplňků s více než 30letou tradicí. Během svého působení v oboru plastikového modelářství se společnost Eduard zařadila mezi jeho světové lídry. Další podrobnosti o společnosti a jejím sortimentu najdete na www.eduard.com. Zde se můžete mimo jiné zdarma přihlásit k odebírání magazínu INFO a produktových informací: https://www.eduard.com/cs/info-eduard/
08/2024
INFO Eduard is a monthly scale model-historical magazine published in Czech and English by Eduard Model Accessories since 2010. The magazine is available for free on the Triobo platform and can be downloaded in PDF format. Eduard is a manufacturer of plastic models and accessories with over 30 years of tradition. Throughout its history in the plastic modeling industry, Eduard has become one of the world's leaders. Further details about the company and its product range can be found at www.eduard.com. You can subscribe to the INFO magazine and receive product information for free at: https://www.eduard.com/cs/info-eduard/
07/2024
INFO Eduard je modelářsko-historický měsíčník, který od roku 2010 v českém a anglickém jazyce publikuje společnost Eduard Model Accessories. Magazín je dostupný zdarma na platformě Triobo a je možné jej stáhnout také v PDF verzi. Společnost Eduard je výrobcem plastikových modelů a doplňků s více než 30letou tradicí. Během svého působení v oboru plastikového modelářství se společnost Eduard zařadila mezi jeho světové lídry. Další podrobnosti o společnosti a jejím sortimentu najdete na www.eduard.com. Zde se můžete mimo jiné zdarma přihlásit k odebírání magazínu INFO a produktových informací: https://www.eduard.com/cs/info-eduard/
07/2024
INFO Eduard is a monthly scale model-historical magazine published in Czech and English by Eduard Model Accessories since 2010. The magazine is available for free on the Triobo platform and can be downloaded in PDF format. Eduard is a manufacturer of plastic models and accessories with over 30 years of tradition. Throughout its history in the plastic modeling industry, Eduard has become one of the world's leaders. Further details about the company and its product range can be found at www.eduard.com. You can subscribe to the INFO magazine and receive product information for free at: https://www.eduard.com/cs/info-eduard/
06/2024 - Special
Vážení přátelé, dnešní mimořádné číslo Infa je věnováno mimořádné stavebnici, The Bloody Hundredth 1943/ B-17F 1:48. Tato stavebnice vydávaná v řadě LIMITED patří mezi položky, jejichž základem jsou výlisky nakoupené u spolupracujících firem. V tomto případě jde o výlisky firmy Hong Kong Models, HKM. Tentokrát jde ovšem spolupráce mezi našimi firmami dál, než je v podobných případech dodávek výlisků zvykem. Speciálně k této stavebnici jsme zkonstruovali konverzní rámeček s čirými díly, obsahující další verze přídí B-17F, než které obsahuje původní sestava dílů stavebnice HKM. Tento rámeček jsme zkonstruovali v Eduardu, pochopitelně s využitím konstrukce HKM, na kterou nové díly navazují. Forma na něj byla vyrobena firmou HKM v jejich čínské nástrojárně, výlisky byly vyrobeny tamtéž.
06/2024 Special EN
Dear Friends, Today's special issue of the newsletter is dedicated to an extraordinary kit, ‘The Bloody Hundredth 1943 / B-17F’ in 1:48th scale. This kit, released in the LIMITED edition line, falls under the group of items based on moldings purchased from partner companies. In this case, the plastic is supplied by Hong Kong Models, HKM. This time, however, the cooperation between our companies goes further than is customary in similar endeavors. Specifically for this kit, we have designed an additional set of clear parts that cover variations used on the B-17F nose that were not a part of the original HKM release. We designed the new parts to fit the HKM kit specifically. The mold for it was cut at HKM in their Chinese tool shop, and the parts are produced by them.
06/2024
INFO Eduard je modelářsko-historický měsíčník, který od roku 2010 v českém a anglickém jazyce publikuje společnost Eduard Model Accessories. Magazín je dostupný zdarma na platformě Triobo a je možné jej stáhnout také v PDF verzi. Společnost Eduard je výrobcem plastikových modelů a doplňků s více než 30letou tradicí. Během svého působení v oboru plastikového modelářství se společnost Eduard zařadila mezi jeho světové lídry. Další podrobnosti o společnosti a jejím sortimentu najdete na www.eduard.com. Zde se můžete mimo jiné zdarma přihlásit k odebírání magazínu INFO a produktových informací: https://www.eduard.com/cs/info-eduard/
06/2024
INFO Eduard is a monthly scale model-historical magazine published in Czech and English by Eduard Model Accessories since 2010. The magazine is available for free on the Triobo platform and can be downloaded in PDF format. Eduard is a manufacturer of plastic models and accessories with over 30 years of tradition. Throughout its history in the plastic modeling industry, Eduard has become one of the world's leaders. Further details about the company and its product range can be found at www.eduard.com. You can subscribe to the INFO magazine and receive product information for free at: https://www.eduard.com/cs/info-eduard/
05/2024
INFO Eduard je modelářsko-historický měsíčník, který od roku 2010 v českém a anglickém jazyce publikuje společnost Eduard Model Accessories. Magazín je dostupný zdarma na platformě Triobo a je možné jej stáhnout také v PDF verzi. Společnost Eduard je výrobcem plastikových modelů a doplňků s více než 30letou tradicí. Během svého působení v oboru plastikového modelářství se společnost Eduard zařadila mezi jeho světové lídry. Další podrobnosti o společnosti a jejím sortimentu najdete na www.eduard.com. Zde se můžete mimo jiné zdarma přihlásit k odebírání magazínu INFO a produktových informací: https://www.eduard.com/cs/info-eduard/
05/2024
INFO Eduard is a monthly scale model-historical magazine published in Czech and English by Eduard Model Accessories since 2010. The magazine is available for free on the Triobo platform and can be downloaded in PDF format. Eduard is a manufacturer of plastic models and accessories with over 30 years of tradition. Throughout its history in the plastic modeling industry, Eduard has become one of the world's leaders. Further details about the company and its product range can be found at www.eduard.com. You can subscribe to the INFO magazine and receive product information for free at: https://www.eduard.com/cs/info-eduard/
04/2024
Dobrý večer, vážení přátelé! Máme za sebou hektický březen. Chápu, že vám to asi tak nepřijde, ale ona každá hospoda vypadá jinak z jídelny a jinak z kuchyně. Aby byl pohled z jídelny, tedy od vás zákazníků, pozitivní, nezbývá personálu v kuchyni, tedy nám, aby se pořádně oháněl.
04/2024
Good evening, dear Friends, We've had a hectic March. I understand that it might not seem that way to you, but every bar looks different from the dining room than it does from the kitchen. In order for the view from the dining room, in other words, from you, the customers, to be positive, the staff in the kitchen (us), has little choice but to be very busy. So, hectic is good.
03/2024
Určitě nejsem sám, komu se pravidelně stává, že se jeho předpoklady a představy o průběhu nějaké události nenaplní a výsledek je zcela opačný, než jaká byla očekávání s onou událostí spojená. Mě se to naposledy stalo před měsícem v Norimberku. Co jsem od veletrhu čekal, si jistě pamatujete z minulého úvodníku. Z mé skeptické předpovědi nevyšlo prakticky nic. Ne že by se už veletrh vrátil tam, kde byl za starých časů před covidovými lockdowny, ale byl výrazně živější, zajímavější a ve svém výsledku zábavnější a užitečnější, než bych si troufl očekávat. Troufnu si dokonce tipnout, že podobný názor má víc vystavovatelů. Mimo jiné se opakovala situace z loňska, že rozhovory a setkání byla daleko vřelejší, přátelštější a otevřenější, než kdykoli v minulosti. Možná je to jen můj pocit, ale přijde mi, že jsme se navzájem zase rádi viděli, v mnoha případech i po několika letech. V takových případech si uvědomíte, jak vám ti lidé, které jste vídal tak nějak samozřejmě a nepřišlo vám na tom nic zvláštního, přirostli k srdci a jak vám chyběli. Pak se tak hovory víc otevřou, a to je fajn.
03/2024
I know I’m not alone, when a concept and its associated assumptions turn out exactly opposite to what the expected outcome was. The last time it happened to me was a month ago in Nuremberg.
Jak na plasty II
Mnoho méně zkušených modelářů má velkou fobii z řezání do plastů nebo z většího ztenčování plastových dílů pro zástavbu doplňkových sad. V tomto díle bych chtěl čtenářům představit, že tyto pokročilejší modelářské činnosti nejsou nic těžkého a s využitím vhodných nástrojů a pomůcek se dá snadno dobrat k potřebným úpravám. Prakticky všechny větší brassinové sady po modeláři vyžadují, aby podobné úpravy při jejich zástavbách provedl. Pokud se někteří modeláři obávají doplňkové sady kupovat právě kvůli zmíněným úpravám, chtěl bych jim ukázat, že to s trochou praxe zvládnou i oni. V článku demonstruji přípravu křídla P-51B/C 1/48 pro zástavbu brassinové sady zbraňových šachet. Představím dvě metody – za pomocí pouze základních modelářských nástrojů a poté s pomocí jemné vrtačky a frézky od firmy Proxxon.
How work with Plastic II
Many less experienced modelers often feel apprehensive about cutting into plastic or thinning parts to accommodate additional detailing or conversion sets. In this section, I want to reassure readers that these more advanced modeling techniques are not difficult and that, with the right tools, achieving the necessary modifications is quite manageable. Most larger Brassin sets require modelers to make similar adjustments to their builds. For those hesitant to purchase aftermarket sets due to this process, I aim to show that, with a bit of practice, anyone can master it. In this article, I will demonstrate how to prepare a 1/48 P-51B/C wing for the Brassin gun bay set. I will present two methods: one using only basic modeling tools, and the other employing a motorized Proxxon tool.
Jak na plasty
V tomto článku o pracovních postupech bych se chtěl věnovat těm nejzákladnějším modelářským postupům a technikám a demonstrovat nářadí, které mi pomáhá při rutinních činnostech, které by měl každý modelář zvládat. K této demonstraci jsem si vybral nový model P-51B/C 1/48, který má spoustu vychytávek pro jednoduché lepení modelu, například spodní vtoky u dílů, což především začátečníkům velmi usnadní práci. Pro zkušené modeláře se bude na první pohled nejspíš jednat o zbytečnou spotřebu digitálního papíru, ovšem přečtení doporučuji i jim. Opakování je totiž matka moudrosti!
How to Work with Plastic?
In this workflow article, I will cover the most basic modeling procedures and techniques, presenting the tools that help with usual activities every modeler should master. For this demonstration, I've chosen the new P-51B/C 1/48 scale kit, which includes several features for easy assembly, such as the parts being connected to the sprues from the bottom, making it especially beginner-friendly.
Step by Step P-51B 1/48
Stavební postup k P-51B 1/48.
Step by Step P-51B 1/48
Step by Step for P-51B 1/48.
Jak na 3D tisky
Poslední roky se v modelářství stále více rozmáhá využití 3D tisku, a to převážně pro výrobu doplňků. I v Eduardu jsme se před několika lety rozhodli pustit do této technologie, která z velké části vytlačila klasickou výrobu Brassinů, tedy metodu odlévání. Dnes přímým tiskem vyrábíme již okolo 80 % produkce Brassinů.
How to Work with 3D Prints in Modeling
In recent years, 3D printing has gained widespread popularity in the modeling industry, particularly for accessory production. A few years ago Eduard, too, embraced this technology, gradually replacing traditional casting methods with direct printing, constituting approximately 80% of our Brassin production.
Jak na obtisky Eduard
How to apply Eduard decals
Jak na Space ?
Exploring Space
Nové masky od Eduard
New masks by Eduard
Práce s Eddie the Riveter
Work with Eddie the Riveter
Práce s fotolepty část I
How to Work with PE-Set part I
Práce s fotolepty část II
How to Work with PE-Set part II
Jak sestavit tištěné klapy
How to build printed landing flaps
Step by Step Kurfürst
Step by Step Kurfürst
Step by Step motor F4F-4
Step by Step engine F4F-4
02/2024
Dobrý den, vážení přátelé! Dnešní úvodník píši zase po roce v Norimberku. Letošní Spielenwarenmesse začal v úterý, dnes jsme přesně v polovině, veletrh končí v sobotu. Pořadatelé se s německou houževnatostí drží pěti dnů trvání akce, čímž jdou většině účastníků pěkně na nervy. Je to sice lepší než šest dnů, které na nás zkoušeli dříve, ale stále je to nejméně o den víc, než tu chceme a potřebujeme být. Z hlediska účasti firem je veletrh letos určitě lepší než loni, ale pokud jde o návštěvníky, obchodníky a žurnalisty, tak je situace víceméně stále bídná. Panuje tu klid. Klid je někdy fajn, ale na veletrhu je klid asi tak to poslední, co na něm chce vystavovatel zažít. Možná se to zítra a pozítří změní a veletrh ožije, ale žádné indicie k tomu nemáme. Tak začínáme uvažovat o odboji. Jak to dopadlo vám napíšu v příštím úvodníku.
02/2024
Good day, Dear Friends After a year, I am writing today's editorial once again from Nuremberg. This year's Spielenwarenmesse started on Tuesday, and today, we are exactly at the halfway point, as the fair ends on Saturday. With German tenacity, the organizers are sticking with the five-day duration of the event, which gets on the nerves of most participants.
01/2024
Vítejte v novém roce, vážení přátelé, vítejte u tříkrálového Infa! Lednové novinky jsou již bezmála tři týdny v prodeji, předpokládám tedy, že jste s nimi již zevrubně seznámeni a mnozí je již máte doma. Přesto musím zmínit, že z mého pohledu začínáme letošní rok pěkně zostra. Při prvním pohledu na čtvrtkového Albatrosa D.III to tak možná nevypadá, ale i on byl svého času vrcholovým predátorem válečného nebe a stavebnice přináší vrcholný mix příběhů a osudů jeho pilotů i jejich soupeřů tak, jak je u nás dobrým zvykem. Měli jsme také více než dobrý důvod si toto téma oživit, jak se za chvíli dočtete.
01/2024
Welcome to the New Year! January’s new releases have been on sale for almost three weeks now, so I assume that you are already thoroughly familiar with them and many of you already have them in your posession. Nevertheless, I have to mention that, from my point of view, we are starting this year off with a bit of a bang. A first glance at the 48th scale Albatros D.III may not indicate this, but it too was once the top predator in a sky dominated by war clouds, and this kit offers a superb mix of stories and fates of its pilots and their opponents, as is our custom to uncover over the course of a kit’s development. We also had more than good reason to revive this topic, as you are about to find out.
12/2023
Dobrý den, vážení přátelé! Po tříleté přestávce jsme se letos opět vypravili do Telfordu, a je dobře, že jsme se odhodlali tam jet. Přeci jen je Británie kolébkou našeho byznysu, výstava v Telfordu je největší výstavou v našem oboru a chybět na ní by byla chyba. V příštím roce budeme na výstavy vyrážet dál. Na přelomu ledna a února začneme tradičně v Norimberku. Pevně doufám, že tam letos potkáme víc kolegů z jiných firem i víc obchodníků a novinářů než loni. Přiznám se, že jsem trochu napjatý. Podle účasti firem v Norimberku můžeme posuzovat nakolik se svět vrací do normálu a všichni bychom byli určitě rádi za zjištění, že tomu tak je a svět se do normálu opravdu vrací.
12/2023
Good day, Dear Friends, After a three-year break, we made a return to Telford, and it was a triumphant return at that! After all, Britain is the cradle of our business, and the Telford event is the biggest exhibition in our field and it would be a mistake to miss it. Our plan is to continue attending such events, beginning with Nuremberg in January/February.
11/2023
Dobrý den, vážení přátelé! S listopadovými novinkami jsme na tom stejně jako s říjnovými, také už jsou druhý týden v prodeji, a tak už je přinejmenším velká část čtenářů Infa zná, pokud už je rovnou nemá doma. Někteří už je dokonce lepí, a ano, jsou i tací, kteří už je mají dokonce postavené. To ovšem není v případě Bf 109 G-2 nebo G-4, obsahu té nej nej nej dvaasedmdesátinové novinky, nic složitého.
11/2023
Good Day, Dear Friends We find ourselves in the same situation with November’s new releases as we did with the October ones, in that they also have been available for purchase a couple of weeks ahead of the newsletter announcement, meaning that they will already be known to a large percentage of readers and perhaps even in their possession.
10/2023
Dobrý den, vážení přátelé, vítám vás u zvláštního vydání Infa, věnovaného 21. ročníku E-Daye, konanému 23. září letošního roku na Tankodromu Milovice. Po necelém měsíci ji vy, kdo jste v Milovicích byli, máte ještě v živé paměti, ale věříme, že si ji díky dnešnímu Speciálu Infa znovu rádi připomenete. A ti, kdo tam s námi nebyli, se mohou inspirovat k návštěvě E-Daye příští rok. Bude se konat opět v Milovicích 28. září 2024.
10/2023
Good day, Dear Friends Welcome to our special edition of the newsletter dedicated to the 21st installment of E-Day, held on September 23rd of this year at the Milovice Tankodrom museum. After less than a month, those of you who were in Milovice still remember it vividly, but I believe that thanks to today's newsletter special, you won’t mind being reminded. And those who were not there with us can be inspired to visit E-day next year. It will be held again in Milovice on September 28, 2024.
10/2023
Jak se vám líbilo na E-dayi? Nebojte se, nehodlám dnes důkladně popisovat tamní dění, tomu se bude věnovat Speciál Infa, připravovaný na druhý týden v říjnu. V dnešním čísle ovšem najdete alespoň základní fotogalerii. Letošní druhý ročník E-Daye v Milovicích potvrdil potenciál areálu Tankodromu pro akci tohoto typu. Můžeme tedy ladit a vymýšlet další body programu, hodící se do našeho konceptu modelářské výstavy.
10/2023
How did you like E-Day? Don’t worry, I’m not going to take up precious real estate thoroughly describing the event today, since that will be covered in a Special Edition of our newsletter, slated to come out the second week of October. However, in today’s issue you will find a basic photo gallery of what was there. This year, the second to be held in Milovice, confirmed the potential of the Tankodrom for an event of this type. With that, we can continue to evolve and develop the program to satisfy the concept that goes hand in hand with the venue.
09/2023
Informace o výstavě E-Day 2023 a soutěži Czech Model Masters – program, instrukce pro dopravu, seznam prodejců a mnoho dalšího
09/2023
Vážení přátelé, Jsme zpět z Texasu, v pilné práci na dalších projektech. Jak jsem zmiňoval v minulém úvodníku, jedním z účelů naší cesty, kromě obvyklé reprezentace na dnes již opět pravidelné IPMS USA National Convention, byl i průzkum a dokumentace zachovalých exemplářů P-40 Warhawk.
09/2023
Dear Friends, We’re back from Texas, hard at work on upcoming projects. As I mentioned in the last editorial, one of the purposes of our trip, in addition to our usual participation at the IPMS USA National convention, was to have a good, close up look at several P-40 examples.
08/2023
Vážení přátelé, vítám vás u srpnového Infa a zdravím z texaského Corpus Christi, kudy s kolegy projíždíme na cestě do San Marcos na tradiční letní IPMS USA Nats. Budeme v Texasu dva týdny, po Nats se přesuneme na sever do Dallasu, kde je naším hlavním plánem studium tří exemplářů P-40 Warhawk. Chceme si ověřit nějaké detaily a průběhy křivek a případně si nějaké pasáže naskenovat.
08/2023
Dear Friends Welcome to the August edition of our newsletter and greetings from Corpus Christi, Texas, where my colleagues and I are passing through on our way to San Marcos for the traditional summer IPMS USA Nats. We will be in Texas for two weeks, after the Nats we will move north to Dallas where our main goal is to study three P-40 Warhawks.
07/2023
Dobrý den, vážení přátelé! Ještě před koncem první poloviny letošního roku jsme stihli přestěhovat do nového areálu v Sedleci balení modelů. To nám významně zjednodušilo logistiku, protože dosud jsme výlisky vozili z Obrnic do Mostu, kde jsme stavebnice zabalili a odvezli je do skladu obchodního oddělení v Sedleci. Ta místa od sebe nejsou daleko, je to v řádu jednotek kilometrů, ale i tak jsme se dost najezdili. Teď dělí balení modelů a sklad obchodního oddělení jedna stěna a dvoje dveře, sklad výlisků je přes dvůr.
07/2023
Hello, dear friends! Even before the end of the first half of this year, we managed to move our model packaging operation to our new facility in Sedlec. This significantly simplifies our logistics, because until now, we would typically move the plastic pressings from Obrnice to Most, where they would be packed into kits, and then transported them to our warehouse and sales department in Sedlec.
06/2023
Dobrý den, vážení přátelé, mezi 84 novinkami připravenými pro červen vyčnívá dvaasedmdesátinová limitka s názvem Wunderschöne neue Maschinen. Těmi báječnými novými stroji jsou Messerschmitty Bf 109 F, které při svém zavedení do výzbroje německé Luftwaffe na začátku roku 1941 přinesly nárůst výkonů a kvality německého stíhacího letectva.
06/2023
Good day, Dear Friends Among the 84 new items being released for June, the 72nd Limited Edition kit dubbed “Wunderschöne neue Maschinen” stands out. This “Wonderful New Machines” kit centres around the Messerschmitt Bf 109F, which, when introduced into the arsenal of the Luftwaffe at the beginning of 1941, brought an increase in the performance and quality of German fighters committed to aerial combat.
05/2023
Dobrý den, vážení přátelé! Na začátku května se soutěžní sezóna pěkně rozjíždí. Máme za sebou tradiční Mošoň, v sobotu se koná Kit show v Kopřivnici, a tak je čas říci si také něco o letošním E-dayi. E-day 2023 se koná v sobotu 23. září na Tankodromu v Milovicích. Pojedeme podle stejného schématu jako vloni, tedy se začátkem pro vystavující modeláře v pátek odpoledne, a to včetně podvečerního programu.
05/2023
Good Day, Dear Friends We are at the beginning of May, and so the competition season is revving up nicely. We have just had the traditional Moson event and the Kit Show takes place in Kopřivnice on Saturday, so it´s a good time to talk about this year´s E-day. E-day 2023 takes place on Saturday, September 23 at the Tankodrom in Milovice and we will be following the same scheme as last year, meaning that exhibiting modelers begin on Friday afternoon and will include the early evening program.
04/2023
Dobrý večer, vážení přátelé! Máme přestěhované obchodní oddělení. K včerejšímu dni jsme tak definitivně ukončili naši činnost v areálu Rico, kde obchodní oddělení a také oddělení kompletace stavebnic sídlilo od června roku 2019. A kde také v prosinci 2020 vyhořel sklad výlisků pro stavebnice. Přiznám se, že jsem po požáru doufal v rychlejší přestěhování do nějakých nových prostor. Hned na jaře a v létě 2020 jsme začali připravovat stavbu nové haly, ale turbulentní situace na stavebním trhu v roce 2021 nám tento záměr zhatila. Na podzim 2021 jsme začali jednat o koupi staršího areálu v Sedleci, sousední vesnici vzdálené asi pět kilometrů od Obrnic.
04/2023
Good evening, Dear Friends We have completed our retail department move. As of yesterday, we have vacated the facility in Most that since June, 2019, has served as our main retail headquarters as well as the facility that served as final kit packaging. It’s also the facility in which we lost a lot of the plastic for our kits when a fire broke out in December 2020. I admit to having hoped for an earlier move to a new facility after that fire. Immediately in the spring and summer of 2020, we prepared for a new-build facility, but that was ultimately quelled by the turbulent supply issues in the construction industry.
03/2023
Dobrý den, dámy a pánové! Máme zavřeno. Dnes představované březnové novinky si sice můžete prohlédnout a prostudovat jak na následujících stránkách, tak na našem e-shopu, ale nekoupíte je tam. Chápu, zní to šíleně. Nejde ale o žádný rafinovaný marketingový tah, prostě se stěhujeme. Přesně řečeno, stěhujeme obchodní oddělení. To je také důvod, proč v následujících sedmi dnech nebude možné objednávat na e-shopu. Jak jste ale jistě zaznamenali, bylo na druhou stranu možné tyto novinky nakoupit již od minulého pátku, rovněž tak jsou již k dispozici u našich obchodních partnerů.
03/2023
Good day, Ladies and Gentlemen, We’re closed. Although you are certainly able to view and study our March release listing within these pages or at our e-shop, any purchases will have to be postponed. I understand that this sounds a little nuts, but it is not the result of some underhanded marketing ploy. It is a function of the fact that we are moving our entire retail department. It is also the reason why no sales will be going through our e-shop for the next seven days. As you will have probably already noted, the new items were available for early purchase from last Friday, and they will be available from our retail partners as well.
02/2023
Vážení přátelé, vítejte u únorového Infa! Dnes začíná Norimberský veletrh hraček (Nuremberg Toy Fair). Po dvouleté přestávce se vracíme do Norimberku a, nebudete tomu věřit, vůbec netušíme, co nás tam čeká.
02/2023
Dear Friends, Welcome to the February Newsletter! The Nuremberg Toy Fair started yesterday. After a two year hiatus, we are coming back to Nuremberg, and as hard as it may be to believe, we have no idea of what to expect
01/2023
Vážení přátelé, milí modeláři, vítejte u prvního Infa roku 2023. V lednovém čísle vás tradičně seznamuji s projekty připravenými na aktuální rok. Ani letos tomu nebude jinak, takže se do toho seznamování pustíme rovnou bez zbytečných řečí kolem. Začneme lednem, jehož novinky jsou v prodeji na našem e-shopu již od minulého týdne.
01/2023
Dear Friends and Fellow Modellers, Welcome to the first newsletter of 2023. The January issue traditionally introduces our planned projects for the year. This year will be no different, so we’ll waste no time and get right down to the nitty gritty. We’ll start off with January, new releases for which are already available from our e-shop and have been since last week.
12/2022
Easy reading
12/2022
Easy reading
11/2022
11/2022
10/2022
10/2022
09/2022
09/2022
08/2022
08/2022
07/2022
07/2022
06/2022
06/2022
05/2022
05/2022
04/2022
04/2022
03/2022
03/2022
02/2022
02/2022
01/2022
01/2022
12/2021
12/2021
11/2021
11/2021
10/2021
10/2021
09/2021
09/2021
08/2021
08/2021
07/2021
07/2021
06/2021
06/2021
05/2021
05/2021
04/2021
04/2021
03/2021
03/2021
02/2021
02/2021
01/2021
01/2021
12/2020
12/2020
11/2020
11/2020
10/2020
10/2020
09/2020
09/2020
08/2020
08/2020
07/2020
07/2020
06/2020
06/2020
05/2020
05/2020
04/2020
04/2020
03/2020
03/2020
02/2020
02/2020
01/2020
01/2020
12/2019
12/2019
11/2019
11/2019
10/2019
10/2019
09/2019
09/2019
08/2019
08/2019
07/2019
07/2019
06/2019
06/2019
05/2019
05/2019
04/2019
04/2019
03/2019
03/2019
02/2019
02/2019
01/2019
01/2019
12/2018
12/2018
11/2018
11/2018
10/2018
10/2018
09/2018
09/2018
08/2018
08/2018
07/2018
07/2018
06/2018
06/2018
05/2018
05/2018
04/2018
04/2018
03/2018
03/2018
02/2018
02/2018
01/2018
01/2018
12/2017
12/2017
11/2017
11/2017
10/2017
10/2017
09/2017
09/2017
08/2017
08/2017
07/2017
07/2017
06/2017
06/2017
05/2017
05/2017
04/2017
04/2017
03/2017
03/2017
02/2017
02/2017
01/2017
01/2017
12/2016
12/2016
11/2016
11/2016
10/2016
10/2016
09/2016
09/2016
08/2016
08/2016
07/2016
07/2016
06/2016
06/2016
05/2016
05/2016
04/2016
04/2016
03/2016
03/2016
02/2016
02/2016
01/2016
01/2016
12/2015
12/2015
11/2015
11/2015
10/2015
10/2015
09/2015
09/2015
08/2015
08/2015
07/2015
07/2015
06/2015
06/2015
05/2015
05/2015
04/2015
04/2015
03/2015
03/2015
02/2015
02/2015
01/2015
01/2015
12/2014
12/2014
11/2014
11/2014
10/2014
10/2014
09/2014
09/2014
08/2014
08/2014
07/2014
07/2014
06/2014
06/2014
05/2014
05/2014
04/2014
04/2014
03/2014
03/2014
02/2014
02/2014
01/2014
01/2014
12/2013
12/2013
11/2013
11/2013
10/2013
10/2013
09/2013
09/2013
08/2013
08/2013
07/2013
07/2013
06/2013
06/2013
05/2013
05/2013
04/2013
04/2013
03/2013
03/2013
02/2013
02/2013
01/2013
01/2013
12/2012
12/2012
11/2012
11/2012
10/2012
10/2012
09/2012
09/2012
08/2012
08/2012
07/2012
07/2012
06/2012
06/2012
05/2012
05/2012
04/2012
04/2012
03/2012
03/2012
02/2012
02/2012
01/2012
01/2012
12/2011
12/2011
11/2011
11/2011
10/2011
10/2011
09/2011
09/2011
08/2011
08/2011
07/2011
07/2011
06/2011
06/2011
05/2011
05/2011
04/2011
04/2011
03/2011
03/2011
02/2011
02/2011
01/2011
01/2011
12/2010
12/2010
12/2010
11/2010
11/2010
10/2010
10/2010
09/2010
09/2010
08/2010
08/2010
01.07/2010
06/2010
06/2010
Tail End Charlie
The Golden Era Printed
Can you recall the first accessory set you bought for a kit? Frankly, I don’t. It has been quite some time… I only know I noticed the existence of photo-etched sets sometime in 1992, I would say, and also noted the nice, camouflaged small boxes stuffed with resin parts – detail sets by Verlinden, on the market. As far as I can recall, this producer was really “in” at that time. Amazed by the detail, the supplies of these sets, as well as of the typical flat packages with Eduard photoetch sets, kept growing in my private collection. I never kept any summary of what I spent my money on, leading to some funny moments when, on opening a kit box on which I planned to use my newly acquired accessories, I was met with the exact same pieces already staring back at me from within! Once I even managed to triple one accessory! By the way: who wants some nice Eduard Brassin wheels for the HK Models´ Meteor in 32nd at a very good price?
The wheels are a good example of the “no-problemo” resin accessory, because if one doesn't make any fundamental mistake during the mastering and molding, than all should be OK. In this case, even typical resin shrinkage presents no serious problems. But it is a very different story when it comes to the parts which must be precisely combined with the plastic parts. I think everyone who has ever built a kit with resin accessories knows that: thinning, scribing, placing and, sometimes, shouting … Many of us also experienced a disappointment after opening the box only to find out there are just original plastic parts re-molded with several “easy-to-do-myself” details added. It is even worse when the price of such an “accessory” reaches the price of the kit and the installation of these resin parts requires more effort than to do the detailing using the original kit parts.
And then, after years spent with cast resin sets, 3D printing emerged and the continual progress of this technology led the first enthusiasts to start trying to produce their own home-made parts (the more skilled and daring even made entire models of desired types). Manufacturers, well aware of what was happening, waited for the technology to mature enough to allow for sensible serial production and jumped at the opportunity when it did. Eduard did not stay aloof of this trend, of course, despite its well-established resin casting department. I remember the first attempts about two years ago, when colleagues were testing different materials for printing in search for the right one to use, the one giving the best possible results and was stable enough. And even then, I was impressed with the finesse of the printed parts. Today we have a herd of printers humming merrily along, running at full speed. And the small beauties produced by them make me want to start some super-detailed projects again, after quite a long time. For example, the Wildcat, where the wheel bay, engine and wing folding mechanism sets are really encouraging me to do it!
Anyone who knows something about resin casting knows that a rubber mold does not survive forever and the last part to come out of it will not be exactly the same as the first one quality-wise. And also he knows, there are a number of factors that can affect the result, whether it’s the quality of the air bubble removal in the vacuum chamber, the mix of the material used, the temperature at which it is cast, and so on and so forth ... 3D production is quite a different world! Yes, even the printer can make a mistake occasionally, but it’s visible and the part is discarded during quality control. Otherwise, they’re just like each other, first and last. And since these parts do not shrink, one can also rely on their accuracy. In fact, some of the printed parts seem to fit better than the original plastic parts! And I think it’s a terrible shame that this manufacturing process isn’t fast and cost-effective enough to produce complete kits. It would eliminate the many constraints that limit the detail and sometimes also shape accuracy of parts produced using molds and injection molding machines.
By the way, nowadays even metal parts can be printed with great precision, and perhaps the time is not so far away for printing molds. Such a technology might eliminate at least the milling, maybe even electrode discharging of the molds. Since it is possible to print, for example, H13 tool steel, it may only be a matter of time. Even in this case, 3D printing technology would bring a number of advantages apart from those mentioned.
In any case, 3D printing is a revolution for our hobby, and in combination with other technologies, such as Mimaki printers in our case, it opens up a whole new world of possibilities for the production of perfect accessories. Many modelers keep saying we are in the golden age of modelling thanks to the constant flurry of new kits. But I think the real golden era is coming with the rise of 3D technology.
Richard Plos

Good day, Ladies and Gentlemen, We’re closed. Although you are certainly able to view and study our March release listing within these pages or at our e-shop, any purchases will have to be postponed. I understand that this sounds a little nuts, but it is not the result of some underhanded marketing ploy. It is a function of the fact that we are moving our entire retail department. It is also the reason why no sales will be going through our e-shop for the next seven days. As you will have probably already noted, the new items were available for early purchase from last Friday, and they will be available from our retail partners as well.
3/1/2023
Don't miss out
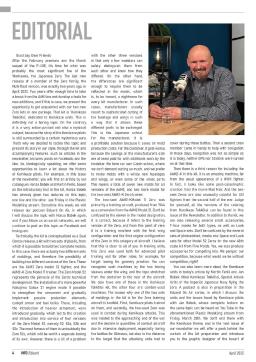
Editorial
Good day, Dear Friends After the February premiere and the March sequel of the P-40E, it's time for what was probably the most significant foe of the Warhawks, the Japanese Zero. The last new release of a member of the Zero family, the Rufe float version, was exactly two years ago, in April 2023.
04/2025
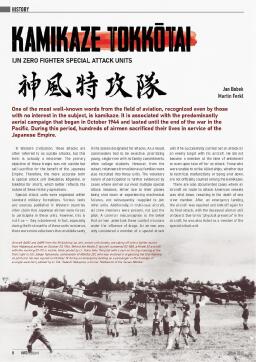
KAMIKAZE TOKKŌTAI
One of the most well-known words from the field of aviation, recognized even by those with no interest in the subject, is kamikaze. It is associated with the predominantly aerial campaign that began in October 1944 and lasted until the end of the war in the Pacific. During this period, hundreds of airmen sacrificed their lives in service of the Japanese Empire.
04/2025
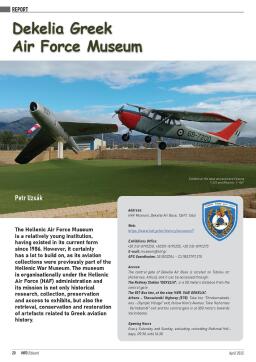
Dekelia Greek Air Force Museum
The Hellenic Air Force Museum is a relatively young institution, having existed in its current form since 1986. However, it certainly has a lot to build on, as its aviation collections were previously part of the Hellenic War Museum. The museum is organisationally under the Hellenic Air Force (HAF) administration and its mission is not only historical research, collection, preservation and access to exhibits, but also the retrieval, conservation and restoration of artefacts related to Greek aviation history.
04/2025
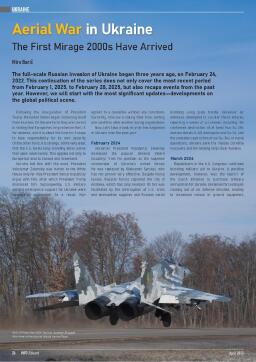
Aerial War in Ukraine - The First Mirage 2000s Have Arrived
The full-scale Russian invasion of Ukraine began three years ago, on February 24, 2022. This continuation of the series does not only cover the most recent period from February 1, 2025, to February 28, 2025, but also recaps events from the past year. However, we will start with the most significant updates—developments on the global political scene.
04/2025
Like a Painting on Canvas
Market Garden was the largest Allied airborne operation of World War II, launched on 17 September 1944 in the Netherlands. Its objective was to use paratroopers (the "Market" component) and the rapid advance of ground forces (the "Garden" component) to seize key bridges over rivers and canals, thereby creating a corridor for an attack into Germany. However, the operation ultimately failed due to strong German resistance, poor coordination, and delays in the Allied advance, particularly at Arnhem, where British paratroopers were unable to hold a crucial bridge.
04/2025
Tail End Charlie - Almost an April problem
It's not entirely my fault that I’m writing my Tail End Charlie text at the last-minute again. I scheduled my work quite responsibly yesterday, Sunday, two days before the current issue was due out. However, somehow I didn't keep up at the end of the day. Understandably, I could blame my slow work, my tendency to run away from responsibilities, orstimuli that release the right hormones into my brain for the wrong mood, and a thousand other things rooted solely in my nature, irresponsibility, and laziness. But this time it's different my friends.
04/2025
Flying Knights in Australia
03/2025
P-40E Warhawk
The Curtiss P-40 line of fighter aircraft stood out among American fighter types for having remained in front-line operations from the summer of 1941, before the U.S. entered World War II, through the end of the conflict four years later. Only Grumman’s versatile F4F Wildcat naval fighter could match that record.
02/2025